Rosenbauer Thermal Imaging for Fire Fighters (2)
Browse Thermal Imaging for Fire Fighters
- Display
- Standard Resolution
- High Resolution
- Vehicle Charger?
- Yes
- Make
- Rosenbauer
- Other Rosenbauer products
- Rosenbauer Vehicles
- Rosenbauer Boots
- Rosenbauer Pumps
- Rosenbauer Helmets
- Rosenbauer Nozzles
Thermal Imager products updated recently
Thermal Imagers - Expert Commentary
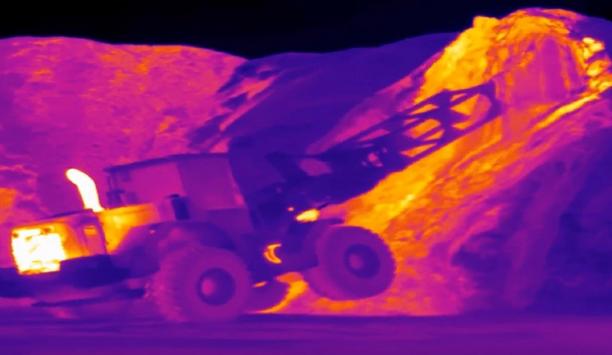
Waste management sites are particularly vulnerable to fires, with hundreds reported every year, just in the UK. The materials stored in a waste heap make them particularly risky e...
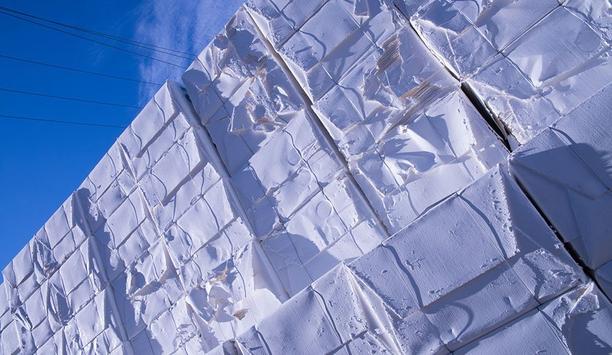
There is a sense in some markets that the paper and pulp industry will decline owing to the digital technologies with which people interact every day. While this might be considere...
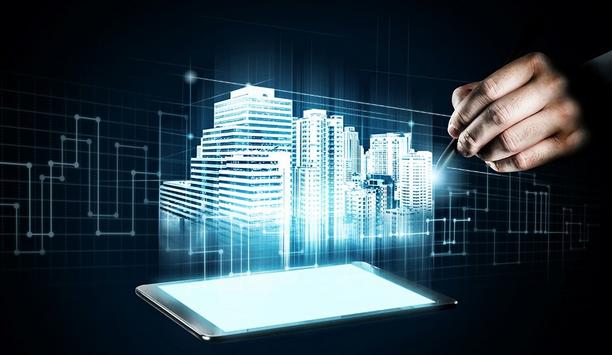
As Grenfell remains a chilling reminder of the importance of fire safety in construction, new digital methods are now being adopted to guarantee the safety of end users. But how is...
Latest Rosenbauer International AG news
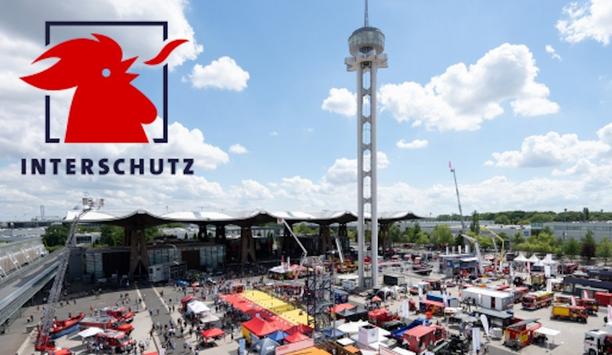
One and a half years before INTERSCHUTZ 2026, many well-known companies have already confirmed their participation in the world's renowned trade fair for firefighting, rescue, and...
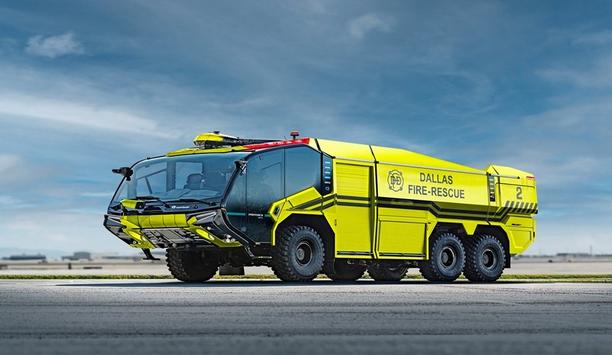
Rosenbauer America and the Dallas Fire Rescue Department have entered into an innovative partnership aimed at the joint further development of the PANTHER 6x6 electric through to s...
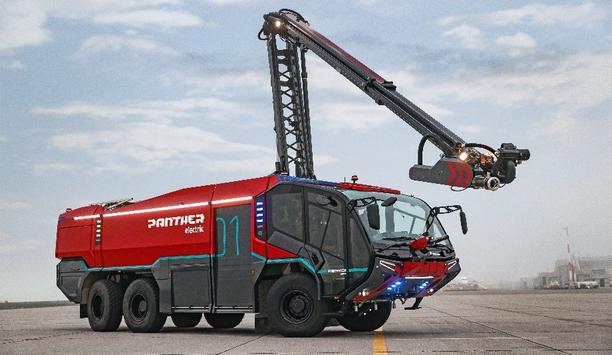
Interested emergency organizations can now order the new PANTHER 6x6 electric. The fully electric twin of the legendary PANTHER unleashes its full power in pure electric mode and a...
Trending topic articles
Fire and Rescue NSW (FRNSW) crews are battling a large warehouse fire at Five Dock, in Sydney's inner west. Shortly after 3 pm, FRNSW received multiple Triple-Zero (000) calls reporting large volumes...
Fire and Rescue NSW (FRNSW) has determined there was a 12 percent increase in house fires during winter this year, sparking calls for more working smoke alarms in NSW homes. The latest statistics gat...
Fire and Rescue NSW (FRNSW) crews have saved a home from a large Lithium-Ion battery fire at Warrawee, on Sydney’s upper north shore. A resident was charging the battery used to power a leaf bl...
Darley, a major provider of defense, fire, and emergency services equipment, is proud to announce it has been named one of Crain’s 2025 Fast 50 by Crain’s Chicago Business. This honor re...
Fire and Rescue NSW (FRNSW) crews have successfully completed a strategic hazard reduction burn to protect the headland at North Mona Vale, on Sydney's northern beaches. FRNSW deployed firefighters f...
Johnson Controls marks the one-year anniversary of Autocall as it introduces the brand of proven fire detection systems to the Canadian market. By bringing Autocall to Canada, Johnson Controls is pr...
The latest updates to UL 268, Standard for Safety of Smoke Detectors for Fire Alarm Systems, call for significant improvements to smoke detection technology. Set to take effect in June 2021, the new...
While building fire and life safety codes are typically viewed as set in stone, the reality is not quite as concrete. As facilities add unique design elements to achieve aesthetic or functional goals,...
Fire and Rescue NSW (FRNSW) investigators have determined a tobacco pipe sparked a fire at Seven Hills, in Sydney's north-west, which injured two people last night. The blaze broke out at the back of...
Fire and Rescue NSW (FRNSW) investigators will examine the scene of a major gas fire at a service station last night at Fairfield, in Sydney's south-west. Around 50 firefighters responded to numerous...
Fire and Rescue NSW (FRNSW) crews have extinguished a major factory fire in Sydney's south-west. Just before 4 am this morning, a Triple Zero (000) emergency call alerted firefighters to a plastic pi...
His younger colleagues lovingly call him “the dinosaur,” and after five decades of serving the public, Fire and Rescue NSW (FRNSW) Station Officer Fred Parkhouse, has called ‘time&rs...
Fire and Rescue NSW (FRNSW) crews are at the scene of a helicopter crash in Sydney's south-west. Two people were aboard the single-engine aircraft when it plummeted to the ground at the Bankstown Aer...
Fire and Rescue NSW (FRNSW) crews are working to clear a major spill of combustible liquid at Mascot, in Sydney's inner south. The operation began around 4:30 am when two semi-trailers collided at th...
Fire and Rescue NSW (FRNSW) investigators are working to determine the cause of a fire which has engulfed a factory at Jamisontown, in Sydney's west. More than 40 firefighters and 14 fire trucks were...
Fire and Rescue NSW (FRNSW) crews are battling a large warehouse fire at Five Dock, in Sydney's inner west. Shortly after 3 pm, FRNSW received multiple Triple-Zero (000) calls reporting large volumes...
Fire and Rescue NSW (FRNSW) has determined there was a 12 percent increase in house fires during winter this year, sparking calls for more working smoke alarms in NSW homes. The latest statistics gat...
Fire and Rescue NSW (FRNSW) crews have saved a home from a large Lithium-Ion battery fire at Warrawee, on Sydney’s upper north shore. A resident was charging the battery used to power a leaf bl...
Darley, a major provider of defense, fire, and emergency services equipment, is proud to announce it has been named one of Crain’s 2025 Fast 50 by Crain’s Chicago Business. This honor re...
Fire and Rescue NSW (FRNSW) crews have successfully completed a strategic hazard reduction burn to protect the headland at North Mona Vale, on Sydney's northern beaches. FRNSW deployed firefighters f...
Johnson Controls marks the one-year anniversary of Autocall as it introduces the brand of proven fire detection systems to the Canadian market. By bringing Autocall to Canada, Johnson Controls is pr...
The latest updates to UL 268, Standard for Safety of Smoke Detectors for Fire Alarm Systems, call for significant improvements to smoke detection technology. Set to take effect in June 2021, the new...
While building fire and life safety codes are typically viewed as set in stone, the reality is not quite as concrete. As facilities add unique design elements to achieve aesthetic or functional goals,...
Fire and Rescue NSW (FRNSW) investigators have determined a tobacco pipe sparked a fire at Seven Hills, in Sydney's north-west, which injured two people last night. The blaze broke out at the back of...
Fire and Rescue NSW (FRNSW) investigators will examine the scene of a major gas fire at a service station last night at Fairfield, in Sydney's south-west. Around 50 firefighters responded to numerous...
Fire and Rescue NSW (FRNSW) crews have extinguished a major factory fire in Sydney's south-west. Just before 4 am this morning, a Triple Zero (000) emergency call alerted firefighters to a plastic pi...
His younger colleagues lovingly call him “the dinosaur,” and after five decades of serving the public, Fire and Rescue NSW (FRNSW) Station Officer Fred Parkhouse, has called ‘time&rs...
Fire and Rescue NSW (FRNSW) crews are at the scene of a helicopter crash in Sydney's south-west. Two people were aboard the single-engine aircraft when it plummeted to the ground at the Bankstown Aer...
Fire and Rescue NSW (FRNSW) crews are working to clear a major spill of combustible liquid at Mascot, in Sydney's inner south. The operation began around 4:30 am when two semi-trailers collided at th...
Fire and Rescue NSW (FRNSW) investigators are working to determine the cause of a fire which has engulfed a factory at Jamisontown, in Sydney's west. More than 40 firefighters and 14 fire trucks were...
Fire and Rescue NSW (FRNSW) crews are battling a large warehouse fire at Five Dock, in Sydney's inner west. Shortly after 3 pm, FRNSW received multiple Triple-Zero (000) calls reporting large volumes...
The New Future For Fire Agencies
DownloadThe Eight Key Trends in Fire Detection in 2023
DownloadA Digital Platform to Improve Fire Safety Compliance and Inspections
DownloadOvercoming the Challenges of Fire Safety in the Paper Industry
DownloadCarbon Monoxide: Creeping Killer Caught In The Act
Download