Rosenbauer FIRE PUMPS (10)
Browse FIRE PUMPS
- Type
- Portable
- PTO
- Hydraulic
- Transmission
- Mounting
- Front Mount
- Rear Mount
- Midship
- Make
- Rosenbauer
- Other Rosenbauer products
- Rosenbauer Vehicles
- Rosenbauer Boots
- Rosenbauer Helmets
- Rosenbauer Nozzles
- Rosenbauer Turnout/Bunker Gear
Pump products updated recently
Pumps - Expert Commentary
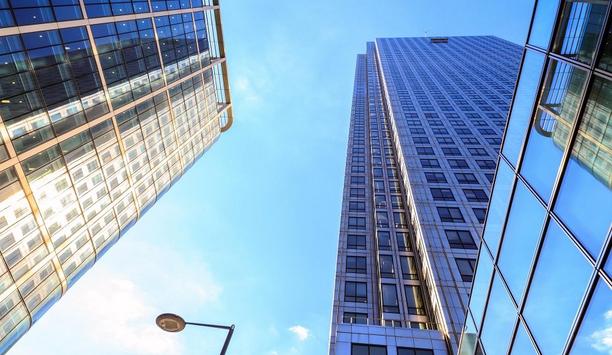
The importance of understanding the revised Code of Practice for Category 3 Control fire performance cables which reduce harmful smoke, toxic gases, and flame spread in the event o...
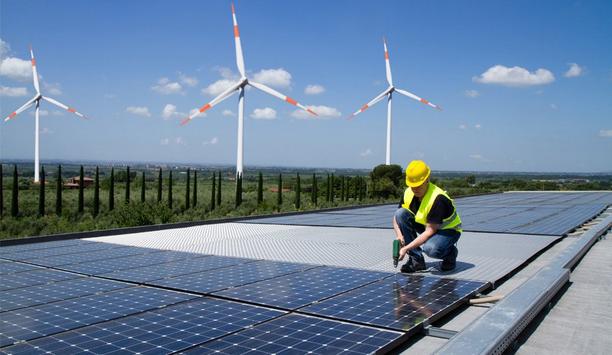
Following the UK Chancellor of the Exchequer Rishi Sunak’s Spring Statement on 23 March, several imminent and future changes were laid out by the UK government. This include...
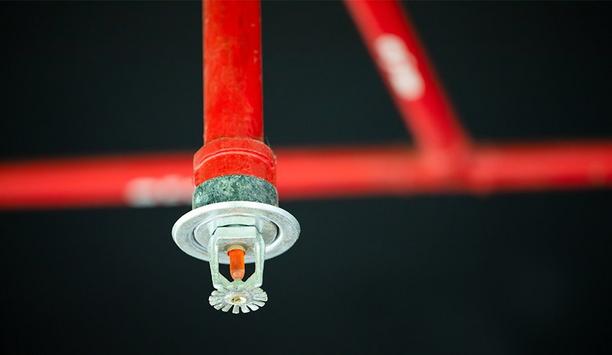
The fire sprinkler system in your building is a critical safety measure and, when needed, it can save lives. Still, even the best systems can malfunction, and sprinklers do occasio...
Latest Rosenbauer International AG news
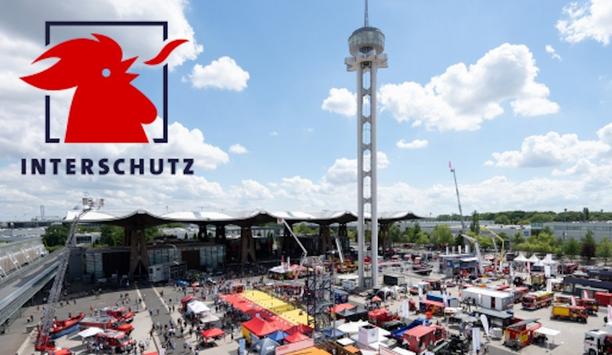
One and a half years before INTERSCHUTZ 2026, many well-known companies have already confirmed their participation in the world's renowned trade fair for firefighting, rescue, and...
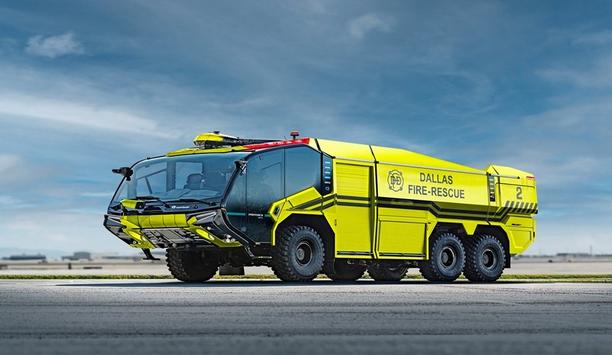
Rosenbauer America and the Dallas Fire Rescue Department have entered into an innovative partnership aimed at the joint further development of the PANTHER 6x6 electric through to s...
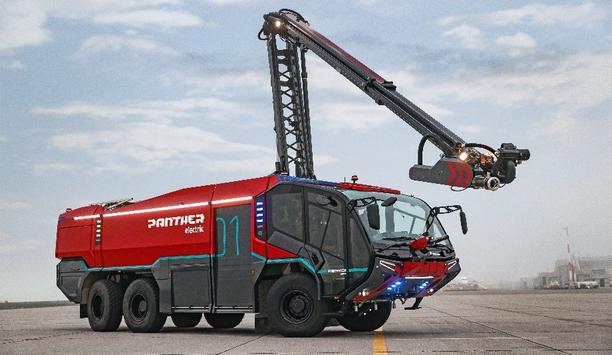
Interested emergency organizations can now order the new PANTHER 6x6 electric. The fully electric twin of the legendary PANTHER unleashes its full power in pure electric mode and a...
Trending topic articles
Perimeter Solutions, a renowned global manufacturer of high-quality fire retardant and firefighting foam concentrates, marked the grand opening of its new PHOS-CHEK facility at McClellan Park in Sacra...
The Engineered Solutions division of Dräger, an international pioneer in the fields of medical and safety technology, has designed a breathing air panel for Staffordshire Fire and Rescue to prote...
INTERSCHUTZ 2026, taking place from 1 to 6 June in Hanover, will be shaped by what many are calling a “turning point”. With eleven months to go before the event starts, strong exhibitor i...
FeuerTrutz 2025 has once again proven itself as the central platform for preventive fire protection. With new formats, a strong congress program and intensive expert discussions, the trade fair p...
Oshkosh Airport Products, an Oshkosh Corporation business, is proud to announce the delivery of three advanced Striker Aircraft Rescue and Fire Fighting (ARFF) vehicles to the Metropolitan Washington...
An upgrade to the Johnson Controls flagship building automation system (BAS), Metasys 14.1 offers a suite of new and enhanced features that answers the need for more comprehensive energy management....
Pierce Manufacturing Inc., an Oshkosh Corporation business, is proud to announce the continued momentum of the 2025 Pierce Road Rally as it nears its midpoint, visiting locations across the United Sta...
Andy Spence, Joint Managing Director of Britannia Fire, the pioneering manufacturer of fire extinguishers in the UK, has addressed the Environmental Audit Committee in the House of Commons. He highli...
Darley, a globally renowned provider of defense, fire, and emergency services equipment, is pleased to announce the appointment of Jim Johnson to its Fire Advisory Board. Jim Johnson brings a wealth o...
QuickFitting highlighted its comprehensive flame-free fitting portfolio, addressing industry data from construction research firm FMI showing construction rework now consumes 12-15% of total North Ame...
Oshkosh Airport Products, an Oshkosh Corporation business, announced the delivery of three new Striker® 8x8 Aircraft Rescue and Firefighting (ARFF) vehicles to serve Minneapolis–St. Paul Int...
Fire detection and life safety specialist, Hispec, has partnered with Vericon Systems, a pioneering manufacturer of remote technologies for essential building services, to enable social housing provid...
Pierce Manufacturing Inc., an Oshkosh Corporation business, is proud to announce Canadian Pierce dealer, Commercial Emergency Equipment Co., has secured an apparatus contract and initial order with th...
With building safety facing more scrutiny than ever before, renowned multi-disciplinary contractor - Miller Knight has secured a place on Fusion21’s £800 million Building Safety and Compli...
Ballyclare, a major designer and manufacturer of firefighter personal protective equipment (PPE), announces a raft of strategic appointments as it focuses on further expansion in the UK market. The f...
Perimeter Solutions, a renowned global manufacturer of high-quality fire retardant and firefighting foam concentrates, marked the grand opening of its new PHOS-CHEK facility at McClellan Park in Sacra...
The Engineered Solutions division of Dräger, an international pioneer in the fields of medical and safety technology, has designed a breathing air panel for Staffordshire Fire and Rescue to prote...
INTERSCHUTZ 2026, taking place from 1 to 6 June in Hanover, will be shaped by what many are calling a “turning point”. With eleven months to go before the event starts, strong exhibitor i...
FeuerTrutz 2025 has once again proven itself as the central platform for preventive fire protection. With new formats, a strong congress program and intensive expert discussions, the trade fair p...
Oshkosh Airport Products, an Oshkosh Corporation business, is proud to announce the delivery of three advanced Striker Aircraft Rescue and Fire Fighting (ARFF) vehicles to the Metropolitan Washington...
An upgrade to the Johnson Controls flagship building automation system (BAS), Metasys 14.1 offers a suite of new and enhanced features that answers the need for more comprehensive energy management....
Pierce Manufacturing Inc., an Oshkosh Corporation business, is proud to announce the continued momentum of the 2025 Pierce Road Rally as it nears its midpoint, visiting locations across the United Sta...
Andy Spence, Joint Managing Director of Britannia Fire, the pioneering manufacturer of fire extinguishers in the UK, has addressed the Environmental Audit Committee in the House of Commons. He highli...
Darley, a globally renowned provider of defense, fire, and emergency services equipment, is pleased to announce the appointment of Jim Johnson to its Fire Advisory Board. Jim Johnson brings a wealth o...
QuickFitting highlighted its comprehensive flame-free fitting portfolio, addressing industry data from construction research firm FMI showing construction rework now consumes 12-15% of total North Ame...
Oshkosh Airport Products, an Oshkosh Corporation business, announced the delivery of three new Striker® 8x8 Aircraft Rescue and Firefighting (ARFF) vehicles to serve Minneapolis–St. Paul Int...
Fire detection and life safety specialist, Hispec, has partnered with Vericon Systems, a pioneering manufacturer of remote technologies for essential building services, to enable social housing provid...
Pierce Manufacturing Inc., an Oshkosh Corporation business, is proud to announce Canadian Pierce dealer, Commercial Emergency Equipment Co., has secured an apparatus contract and initial order with th...
With building safety facing more scrutiny than ever before, renowned multi-disciplinary contractor - Miller Knight has secured a place on Fusion21’s £800 million Building Safety and Compli...
Ballyclare, a major designer and manufacturer of firefighter personal protective equipment (PPE), announces a raft of strategic appointments as it focuses on further expansion in the UK market. The f...
Perimeter Solutions, a renowned global manufacturer of high-quality fire retardant and firefighting foam concentrates, marked the grand opening of its new PHOS-CHEK facility at McClellan Park in Sacra...
The New Future For Fire Agencies
DownloadThe Eight Key Trends in Fire Detection in 2023
DownloadA Digital Platform to Improve Fire Safety Compliance and Inspections
DownloadOvercoming the Challenges of Fire Safety in the Paper Industry
DownloadCarbon Monoxide: Creeping Killer Caught In The Act
Download