Draeger UK CLEAN AGENT SYSTEMS (3)
Browse CLEAN AGENT SYSTEMS
- Manual Release Device?
- Yes
- Make
- Draeger UK
Clean Agent System products updated recently
Clean Agent Systems - Expert Commentary
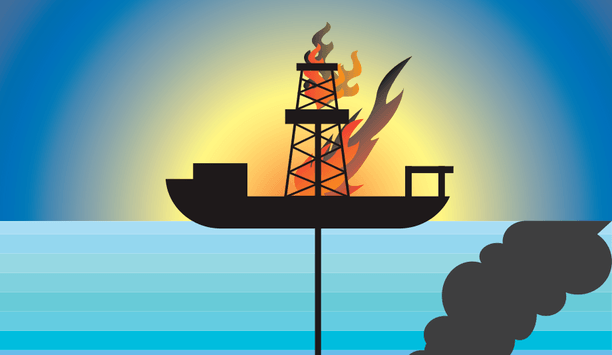
The original fire suppression agent has always been, of course, water. In the age of sail, it was ideal. Not so with the advent of the combustion engine, however. When applied to b...
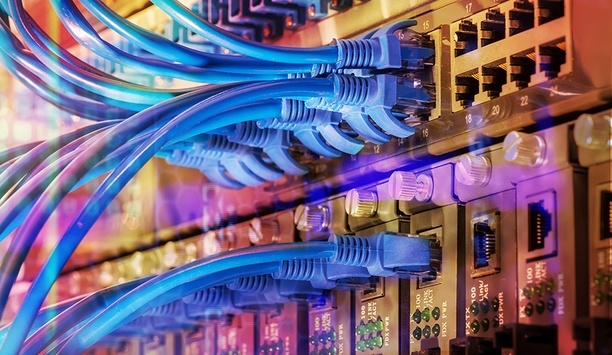
While whole room protection – sprinklers or gas systems – is a common choice, there is an argument for thinking smaller; taking fire detection and suppression down to t...
Latest Draeger Safety UK Limited news
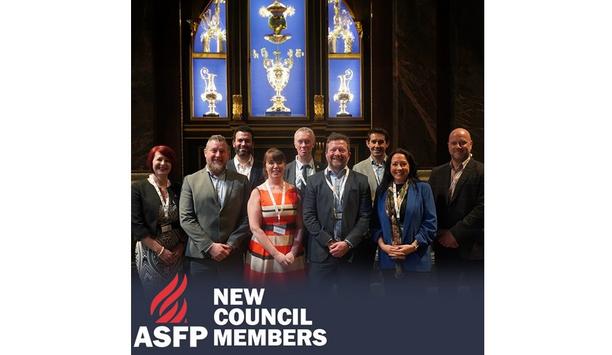
The Association for Specialist Fire Protection (ASFP) appointed its new Council at its 2024 Annual General Meeting (AGM) at Drapers’ Hall, in London, UK, on 11 April, 2024.&n...
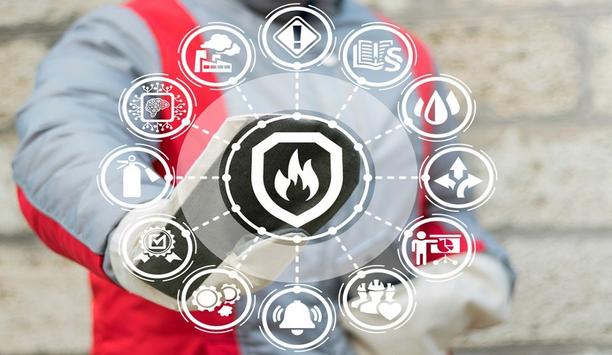
Fostering fire safety is a basic principle, but one that suggests many different approaches and technologies. Best practices and greater innovation can play a role to ensure variou...
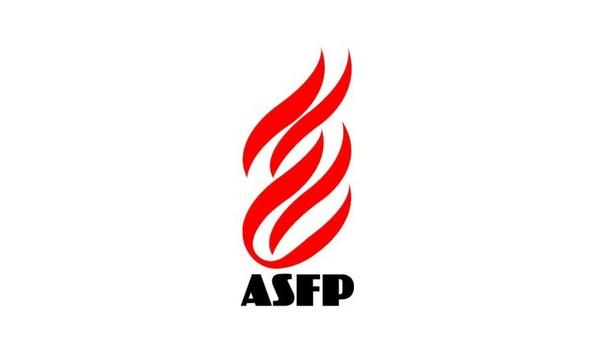
The Association for Specialist Fire Protection (ASFP) will once again be hosting the ASFP Pavilion on stand FI1224 at Firex International at London Excel from 17-19 May....
Trending topic articles
Dräger, an international pioneer in the fields of medical and safety technology, will showcase a range of systems designed to protect fire and rescue and police personnel during a wide variety of...
State Farm® and the National Volunteer Fire Council (NVFC) have teamed up for the second year to support local volunteer fire departments with funding to secure needed equipment to help keep their...
With wildfires overwhelming Los Angeles and dominating headlines across the country, dramatically changing the landscape that people live and work in the wildland-urban interface, there...
Darley, a globally renowned provider of defense, fire, and emergency services equipment, is proud to announce the launch of a new section on its website, darley.com/uncrewed-systems, dedicated exclusi...
Growing fire safety industry organization - Fire Aware aims to change the culture of the built environment sector, by introducing a moral code of conduct via a series of charters designed to influence...
Dräger, the international pioneer in medical and safety technology, has launched a browser-based software solution to optimize daily operations in fire service workshops. Resource and Asse...
Pierce Manufacturing Inc., an Oshkosh Corporation business, is pleased to announce Pierce's authorized dealer, Atlantic Emergency Solutions, has completed a significant expansion of its Charlotte, Nor...
Fire and Rescue NSW (FRNSW) investigators have determined a tobacco pipe sparked a fire at Seven Hills, in Sydney's north-west, which injured two people last night. The blaze broke out at the back of...
Fire and Rescue NSW (FRNSW) investigators will examine the scene of a major gas fire at a service station last night at Fairfield, in Sydney's south-west. Around 50 firefighters responded to numerous...
Fire and Rescue NSW (FRNSW) crews have extinguished a major factory fire in Sydney's south-west. Just before 4 am this morning, a Triple Zero (000) emergency call alerted firefighters to a plastic pi...
His younger colleagues lovingly call him “the dinosaur,” and after five decades of serving the public, Fire and Rescue NSW (FRNSW) Station Officer Fred Parkhouse, has called ‘time&rs...
Fire and Rescue NSW (FRNSW) crews are at the scene of a helicopter crash in Sydney's south-west. Two people were aboard the single-engine aircraft when it plummeted to the ground at the Bankstown Aer...
Fire and Rescue NSW (FRNSW) crews are working to clear a major spill of combustible liquid at Mascot, in Sydney's inner south. The operation began around 4:30 am when two semi-trailers collided at th...
Fire and Rescue NSW (FRNSW) investigators are working to determine the cause of a fire which has engulfed a factory at Jamisontown, in Sydney's west. More than 40 firefighters and 14 fire trucks were...
Fire and Rescue NSW (FRNSW) crews are battling a large warehouse fire at Five Dock, in Sydney's inner west. Shortly after 3 pm, FRNSW received multiple Triple-Zero (000) calls reporting large volumes...
The New Future For Fire Agencies
DownloadThe Eight Key Trends in Fire Detection in 2023
DownloadA Digital Platform to Improve Fire Safety Compliance and Inspections
DownloadOvercoming the Challenges of Fire Safety in the Paper Industry
DownloadCarbon Monoxide: Creeping Killer Caught In The Act
Download