Draeger UK FIRE SUPPRESSION SYSTEM ACCESSORIES (3)
Browse FIRE SUPPRESSION SYSTEM ACCESSORIES
- Make
- Draeger UK
- Other Draeger UK products
- Draeger UK Helmets
- Draeger UK Detectors
- Draeger UK Turnout/Bunker Gear
- Draeger UK Thermal Imagers
Fire Suppression System Accessories products updated recently
Fire Suppression System Accessories - Expert Commentary
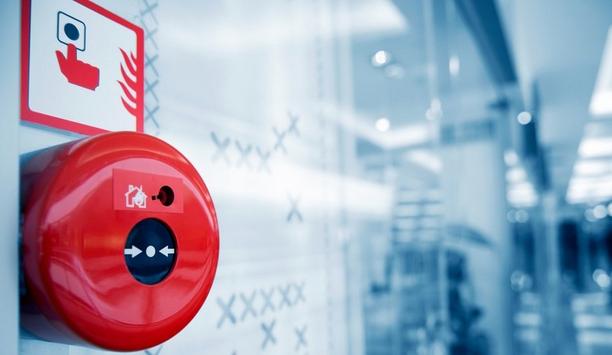
The National Fire Protection Association (NFPA) has developed over 300 codes and standards to support the rapidly changing needs of the fire and life safety industry. NFPA 72, Na...
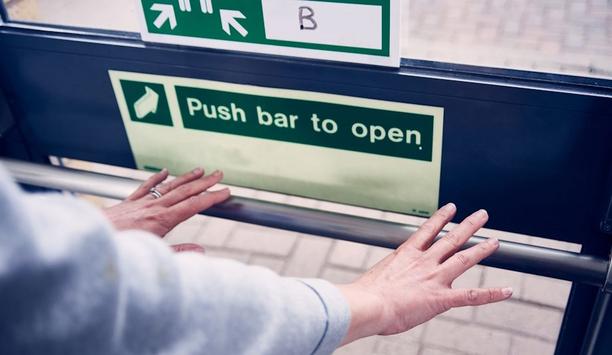
Healthcare environments are synonymous with caution, wellness and safety. Though, where National Health Service professionals work determinedly to meet the needs of their patients,...
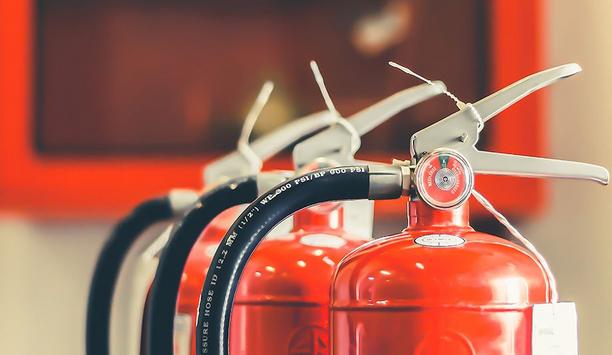
Nearly a decade has passed since the devastating Grenfell Fire, and still the UK construction industry finds itself grappling with the imperative of ensuring fire safety standards...
Latest Draeger Safety UK Limited news
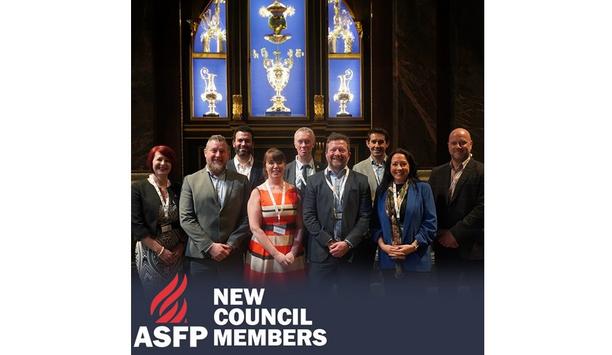
The Association for Specialist Fire Protection (ASFP) appointed its new Council at its 2024 Annual General Meeting (AGM) at Drapers’ Hall, in London, UK, on 11 April, 2024.&n...
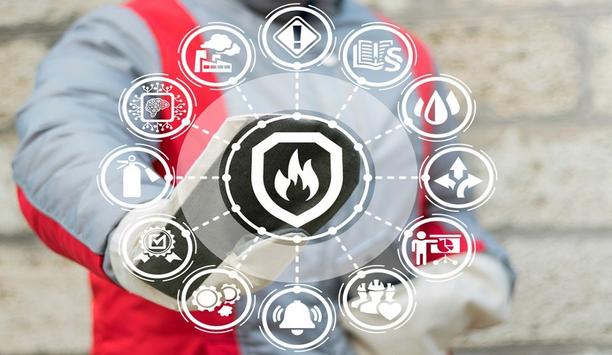
Fostering fire safety is a basic principle, but one that suggests many different approaches and technologies. Best practices and greater innovation can play a role to ensure variou...
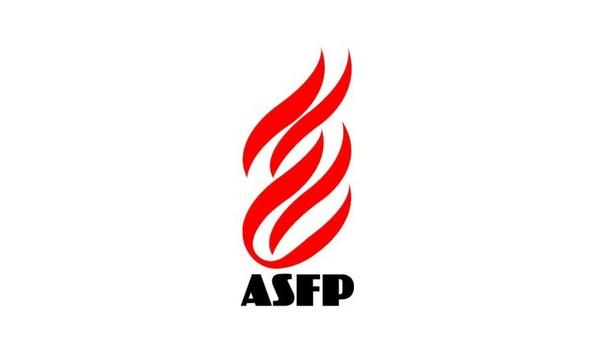
The Association for Specialist Fire Protection (ASFP) will once again be hosting the ASFP Pavilion on stand FI1224 at Firex International at London Excel from 17-19 May....
Trending topic articles
Hampshire and Isle of Wight Fire and Rescue Service (HIWFRS) is changing the way it responds to Automatic Fire Alarms in certain types of buildings as of 01 August 2025. Following a public consultati...
SMARTSHOOTER, a world pioneer in fire control systems, will showcase its handheld and remotely controlled SMASH solutions at the DEFEA 2025 defense exhibition in Athens, Greece. The company will pre...
Global safety equipment manufacturer MSA Safety, Inc. announced it has secured a $10 million contract to provide respiratory protective equipment to the Orange County Fire Authorit...
Skills for Security welcomes EFT Group as a new sponsor, further strengthening its mission to develop the next generation of skilled professionals in the fire and security industry. As one of the UK&...
Johnson Controls, the pioneer for smart, healthy, and sustainable buildings, launches the new Simplex 4017ES Fire Alarm Control Unit to help customers meet evolving life safety voice regulations. ...
Hochiki Europe, a manufacturer of innovative life safety solutions, is partnering with Jendee Trading, a global provider with nearly 50 years of experience exporting British electrical and fire safety...
Fire doors are designed to save lives. When closed, they form a crucial barrier against smoke and fire and provide vital time for occupants to escape in an emergency situation. An open fire door on th...
Sabrina Cohen-Hatton has been appointed as the new Chief Fire Officer to lead Hampshire and Isle of Wight Fire and Rescue Service, becoming the organization’s first female chief. Set to s...
Godiva, a global pioneer in fire pump innovation, proudly announces the launch of The SAMFlows Experience—a dynamic, interactive digital journey that redefines how users engage with and understa...
Darley is proud to announce it has been selected as a 2025 US Best Managed Company. Sponsored by Deloitte Private and The Wall Street Journal, the program recognizes outstanding U.S. private companies...
Blackline Safety Corp., a pioneer in connected safety technology, has announced that its new EXO 8 area monitor — the world’s only direct-to-cloud portable area monitor capable of detectin...
The surge in demand seen by the cables industry for Category 3 Control fire performance cables can be met with the supply chains working together, says pioneering cable supplier - AEI Cables. The inc...
Hochiki Europe has brought the thrill of live football to the heart of the Gillingham community, awarding 35 coveted tickets to a Gillingham FC home game to the deserving Medway Soccer Academy. The a...
Oshkosh Airport Products, an Oshkosh Corporation business, announced the delivery of two Oshkosh Airport Products Striker® 6x6 ARFF vehicles to MET – Montreal Metropolitan Airport ...
Fire protection solutions manufacturer, Advanced, has supplied an intelligent fire panel with wireless detection to iconic Scottish knitwear brand Eribé. An Advanced MxPro 5 analog addressable...
Hampshire and Isle of Wight Fire and Rescue Service (HIWFRS) is changing the way it responds to Automatic Fire Alarms in certain types of buildings as of 01 August 2025. Following a public consultati...
SMARTSHOOTER, a world pioneer in fire control systems, will showcase its handheld and remotely controlled SMASH solutions at the DEFEA 2025 defense exhibition in Athens, Greece. The company will pre...
Global safety equipment manufacturer MSA Safety, Inc. announced it has secured a $10 million contract to provide respiratory protective equipment to the Orange County Fire Authorit...
Skills for Security welcomes EFT Group as a new sponsor, further strengthening its mission to develop the next generation of skilled professionals in the fire and security industry. As one of the UK&...
Johnson Controls, the pioneer for smart, healthy, and sustainable buildings, launches the new Simplex 4017ES Fire Alarm Control Unit to help customers meet evolving life safety voice regulations. ...
Hochiki Europe, a manufacturer of innovative life safety solutions, is partnering with Jendee Trading, a global provider with nearly 50 years of experience exporting British electrical and fire safety...
Fire doors are designed to save lives. When closed, they form a crucial barrier against smoke and fire and provide vital time for occupants to escape in an emergency situation. An open fire door on th...
Sabrina Cohen-Hatton has been appointed as the new Chief Fire Officer to lead Hampshire and Isle of Wight Fire and Rescue Service, becoming the organization’s first female chief. Set to s...
Godiva, a global pioneer in fire pump innovation, proudly announces the launch of The SAMFlows Experience—a dynamic, interactive digital journey that redefines how users engage with and understa...
Darley is proud to announce it has been selected as a 2025 US Best Managed Company. Sponsored by Deloitte Private and The Wall Street Journal, the program recognizes outstanding U.S. private companies...
Blackline Safety Corp., a pioneer in connected safety technology, has announced that its new EXO 8 area monitor — the world’s only direct-to-cloud portable area monitor capable of detectin...
The surge in demand seen by the cables industry for Category 3 Control fire performance cables can be met with the supply chains working together, says pioneering cable supplier - AEI Cables. The inc...
Hochiki Europe has brought the thrill of live football to the heart of the Gillingham community, awarding 35 coveted tickets to a Gillingham FC home game to the deserving Medway Soccer Academy. The a...
Oshkosh Airport Products, an Oshkosh Corporation business, announced the delivery of two Oshkosh Airport Products Striker® 6x6 ARFF vehicles to MET – Montreal Metropolitan Airport ...
Fire protection solutions manufacturer, Advanced, has supplied an intelligent fire panel with wireless detection to iconic Scottish knitwear brand Eribé. An Advanced MxPro 5 analog addressable...
Hampshire and Isle of Wight Fire and Rescue Service (HIWFRS) is changing the way it responds to Automatic Fire Alarms in certain types of buildings as of 01 August 2025. Following a public consultati...
The New Future For Fire Agencies
DownloadThe Eight Key Trends in Fire Detection in 2023
DownloadA Digital Platform to Improve Fire Safety Compliance and Inspections
DownloadOvercoming the Challenges of Fire Safety in the Paper Industry
DownloadCarbon Monoxide: Creeping Killer Caught In The Act
Download