Industrial Fire Safety
AGF Manufacturing is pleased to announce the addition of George Stewart to its growing engineering team. George brings with him a wealth of engineering experience across a diverse range of industries and a strong track record of developing specialized equipment and systems. George began his career at Gamajet/Alfa Laval, where he worked his way up through the engineering department. There, he focused on designing advanced tank cleaning machines and systems used in a wide range of industrial appl...
Fire and Rescue NSW will be undertaking a hazard reduction burn on North Head located near Manly on Sydney’s Northern Beaches. Smoke from the planned hazard reduction burn may settle in and around the Manly area and will be visible from a long distance away. Planned hazard reduction This is an important prescribed burn which will reduce the risk to people and properties from future bush fires. If users have asthma or a lung condition, reduce outdoor activities if smoke levels are high a...
Bosch Building Technologies has launched the AVENAR IO (input/output) module 4000 series, a new range of interface modules designed to elevate the efficiency and adaptability of fire safety systems. The launch debuts with the FLM-430-I2M1, a smart interface module engineered to enhance connectivity and control across multiple applications. It is fully compatible with the AVENAR fire detector 4000 series. Role of Interface Modules Interface modules are important parts that connect fire a...
Fire and Rescue NSW’s (FRNSW) Merrylands Fire Station has marked its 100th birthday. The Minister for Emergency Services, Jihad Dib, Member for Granville, Julia Finn MP and Mayor of Cumberland, Councillor Ola Hamed, joined FRNSW Commissioner Jeremy Fewtrell at the Station in Sydney’s west to celebrate the milestone. Firefighters were first stationed at Merrylands in February 1925, with the original eight-member crew equipped only with a hose-reel. Several months later, approval was...
Matrix, a provider of enterprise-grade Security and Telecom solutions, is proud to participate as a Gold Sponsor at the prestigious Project Heads, Architects, Consultants, and Conclave (PACC) 2025, hosted by the Fire & Security Association of India (FSAI). The event, set to take place from February 6th to 9th at ITC Grand Chola, is a critical platform for industry pioneers shaping the future of infrastructure, smart buildings, and security ecosystems. PACC 2025 PACC 2025 is a c...
The Kidde Fire Protection Natura™ Inert Gas System by Kidde Australia has transformed the way installers think about deploying inert gas fire suppression systems, delivering savings in time, and installation costs and bringing peace of mind to mission-critical operations. two advantages The essence of this innovation comes from the Kidde pressure-regulated valve which offers two distinct advantages. Firstly the 90-degree hoses installed on the top exit port of the valve allow easier ac...
News
The Automatic Fire Extinguisher (AMFE) not only releases the extinguishing gas but also signals that it has. In installations where accessibility is limited, the AMFE can be connected to a monitoring system by two connectors for reading a signal. Permanently controlling if the AMFE has been initiated (e.g., line control through a PLC or monitoring device) allows for precise knowledge about the status of whether and where a fire might have started in an otherwise hard-to-reach installation. Fire Suppression For Electrical Enclosures & Control Cabinets The S-AMFE is rated for typical PLC signals of 24 V/48 V and 1000 mA. The connectors are standardized (6.3 mm blade terminals), but customizations are possible. In control cabinets, fire can quickly lead to a disaster. The AMFE extinguishes reliably and precisely. Suitable For Various Applications: Domestic & Industrial Fire Safety The application spectrum of the AMFE is diverse: It ranges from technical household appliances, exhibits and collections to solutions in a vast variety of applications, both at home or in the industry. AMFE Form & Function The glass bulb bursts into small fragments and triggers a mechanism that releases the gas from the cylinder Due to rising heat in a fire scenario, the pressure inside the glass bulb increases. After the predetermined operating temperature of the heat-sensitive glass bulb is reached, the glass bulb bursts into small fragments and triggers a mechanism that releases the gas from the cylinder. The extinguishing medium is released through the holes in the outlet body and extinguishes the fire when the fire is still in an early stage. The quick operation and the effective extinguishing of the fire prevents further expansion of the fire and helps keeping damage to a minimum. AMFE Advantages At A Glance Easy to use Easy to install (can be retrofitted) Variety of customer-specific operating & releasing temperatures are available No water being used (gas) Scalable Robust and shock-tolerant NOVEC or CO2 as an extinguishing agent Usable in various applications (home, industry, automotive, etc.) Mechanical release; no electric power supply required Release mechanism: qualified in the automotive and sprinkler industry
VIKING Life’s factories and their global service stations are the heart of VIKING. Over the last decade, they have invested heavily in optimizing their production facilities within technology, innovation, safety and low energy consumption. In 2023, they have worked on a large number of local and global initiatives throughout their production facilities with the aim of promoting sustainable production methods. These initiatives include improved waste air treatment, further installation of solar panels on factories, introduction of environmentally friendly equipment such as electric forklifts, battery recycling, and more. Selected results from their 2023 local energy optimization initiatives: The installation of LED lights has resulted in electricity savings of 11.6% throughout their Danish facilities. The solar panels installed in their production facilities in Thailand now cover around 40% of the total electricity consumption, resulting in reduced CO2 emissions of approximately 844 tons per year. The facility also runs on 100% LED lights. The installation of LED light in their Chinese factory has resulted in a 44.8% reduction of electricity used for lighting. Paper consumption has dropped 17.5% from 2022 to 2023 as a result of targeted efforts to promote the paperless office. Reducing water and electricity consumption At VIKING, they are committed to reducing their water and electricity consumption At VIKING, they are committed to reducing their water and electricity consumption on an annual basis. To achieve this goal, they have established yearly targets for their service and manufacturing sites. These targets are set to reduce both electricity and water consumption. They are pleased to report that their manufacturing sites have successfully met the electricity target. However, their service stations have exceeded their targets, likely due to an increase in activity over the past year. Rise in need of water to produce products Conversely, for their water target, they can see the opposite scenario. Their manufacturing sites did not meet the target, while their service stations significantly reduced their consumption compared to 2022. Nonetheless, these results were expected as the increase in activity also implies an increased need of water to produce their products.
VIKING Norsafe totally enclosed and partially enclosed lifeboats keep crew and passengers safe and protected. Their enclosed lifeboats are used on commercial vessels worldwide, and they are designed and manufactured exclusively at VIKING’s production facilities to guarantee product quality. VIKING Norsafe lifeboats VIKING Norsafe lifeboats offer outstanding safety and performance in demanding conditions. Even if damaged or fully flooded, the lifeboats are self-righting and virtually unsinkable. Safely launch and retrieve the totally enclosed lifeboats with VIKING Norsafe conventional davits. VIKING Norsafe conventional davits VIKING Norsafe conventional davits are available in a wide range of safe working loads VIKING Norsafe conventional davits are available in a wide range of safe working loads, lowering heights and weights. VIKING Norsafe davits are produced in house and manufactured in accordance with SOLAS and national authority requirements, ensuring high quality products and safe operation for your crew. Key features of VIKING Norsafe enclosed lifeboats: Positive stability up to 180 degrees Smaller boats (under 8.5 m) are suitable as both lifeboat and rescue boat The largest boats have a maximum capacity of 150 persons in SOLAS configuration (430 mm, 82.5 kg per person) with alternative seating arrangements to accommodate ‘big persons’ in lifeboats Constructed in fire-retardant, glass-fiber reinforced polyester (GRP) Enclosed lifeboats can be delivered either with the VIKING Nadiro Drop-in-Ball system or the VIKING Norsafe Tor MK-2 offload release hook Models available for compliance with NORSOK R-002 and NOROG requirements Possibility for site and host-specific analysis of lifeboat occupant safety through DavitSim analysis Enclosed lifeboats can be launched via a cantilevered platform davit, single pivot gravity davit, or hydraulically pivoting davit Key features of VIKING Norsafe lifeboat davits: Approved according to SOLAS LSA and MODU Code regulations Designed for safe maintenance and operation Special solutions available for extremely high or low temperatures Alternatives for ATEX or IEC EX specifications for operation in hazardous zones Project specific solutions for retrofit Designed and manufactured at VIKING Norsafe facilities
Hochiki Europe, a globally renowned provider of innovative fire detection and life safety solutions, is proud to announce that it has been named Fire Detection Company of the Year by Building and Facilities News. This prestigious award recognizes Hochiki Europe's commitment to excellence, innovation, and reliability in the fire safety industry. fire safety standards Building and Facilities News highlighted Hochiki Europe's extensive product portfolio Building and Facilities News highlighted Hochiki Europe's extensive product portfolio, dedication to customer service, and continuous investment in research and development as key factors in their decision. The award also acknowledged the company's contributions to advancing fire safety standards and its strong reputation within the building and facilities management sector. innovation and excellence "We are incredibly honored to receive this award from Building and Facilities News," said Shinsuke Kubo, Managing Director at Hochiki Europe. Shinsuke Kubo adds, "This recognition is a testament to the hard work and dedication of our entire team. We are committed to providing our customers with the highest quality fire detection solutions that protect lives and property. This award inspires us to continue pushing the boundaries of innovation and excellence in the fire safety industry." fire detection solutions Hochiki Europe provides comprehensive fire safety solutions to a diverse range of industries, including commercial property, healthcare, education, industrial, transportation, and spaces of cultural and historical importance. This award further solidifies Hochiki Europe's position as a global pioneer in the fire detection industry, demonstrating its ongoing commitment to providing cutting-edge solutions and exceptional service to its customers.
Chubbsafes, one of the world’s most trusted security brands, proudly marks its 190th anniversary in 2025. Since its first safe patented in 1835, Chubbsafes has become synonymous with strength, dependability, and innovation, protecting valuables for generations. Reliability and craftsmanship For nearly two centuries, Chubbsafes has stood as a symbol of reliability and craftsmanship. Its rich history includes landmark innovations like the first patented resistant safe and pioneering materials such as Torch and drill-resistant (TDR) barriers. These achievements underscore the brand’s commitment to protecting valuables in an ever-evolving world. excellence and innovation “This year-long campaign is more than just a celebration. It’s a tribute to Chubbsafes’ legacy of reliability and excellence,” said Chanisa Wallace, Head of Marketing and Communication at Gunnebo Safe Storage. “For nearly 200 years, we’ve been trusted by customers worldwide. This milestone is an opportunity to honor our craftsmanship and innovation while looking ahead to the future we’re shaping together with our teams, partners, and customers.” limited-edition collector’s safe Combining robust protection with exquisite craftsmanship, only 190 units have been produced A highlight of the anniversary celebrations is the launch of the Chubbsafes™ 1835, a limited-edition 190th-anniversary collector’s safe. Combining robust protection with exquisite craftsmanship, only 190 individually numbered units have been produced, making it a true piece of history. Mark Brookes, Global Product & Standards Director at Gunnebo Safe Storage, added, “As we celebrate 190 years, we do so with the same core values that have guided us from the beginning: To Care, Be Fair, and Dare." Hard work and resilience "Chubbsafes is more than a brand; it’s a legacy of trust that has been earned through decades of hard work, innovation, and resilience." "The Chubbsafes™ 1835 encapsulates everything we stand for - a product that represents the culmination of almost two centuries of refinement and commitment to excellence. It is not just a safe but a piece of history, built to last and symbolizing the standards we uphold for the future.” modern security In 1889, the brand opened a state-of-the-art factory in Wolverhampton, England, cementing its reputation for quality Chubbsafes’ journey has been defined by transformative milestones. In 1889, the brand opened a state-of-the-art factory in Wolverhampton, England, cementing its reputation for quality and trust. Significant advancements followed to remain one step ahead of criminals and tools used to attempt to break into safes and vaults. This included Anti-Arc materials in 1959, TDR barriers in 1962, and lightweight Dualite materials in 2004. By 2019, Chubbsafes achieved T2 burglary certification, reaffirming its leadership in modern security. Protecting assets Chanisa concluded, “From pioneering advanced safe technologies to protecting assets around the globe, Chubbsafes has remained synonymous with safeguarding what truly matters." "And while we celebrate its storied past, the brand remains forward-thinking, continuously adapting to meet modern security challenges. Its commitment to innovation ensures it remains a trusted partner for safeguarding assets worldwide.” Visit the Chubbsafes 190 Years Celebration page to learn more about this historic milestone and explore the exciting initiatives planned for 2025.
Fire and Rescue NSW (FRNSW) is reminding the public not to charge Lithium-ion-powered devices, such as e-bikes, near emergency exits, following a second-storey unit fire yesterday at Merrylands West in Sydney. FRNSW releases dramatic footage from a camera worn by the Incident Commander in charge of the fire scene in Arcadia Street. Lithium-ion-powered devices The footage shows the first senior officer on scene, Station Officer Darryn Moalem from Wentworthville Fire Station, assigning firefighters crucial tasks and managing the rescue of three people and a dog from the burning building just after 11.15 am. Firefighters used ladders and an aerial appliance to rescue a woman from her unit Firefighters used ladders and an aerial appliance to rescue a woman from her unit, where an e-bike caught fire, blocking the front door and preventing her initial escape. Fortunately, a working smoke alarm activated. When the woman opened her door to investigate, she saw the e-bike that had been charging in a loungeroom, near the front door, on fire. Working smoke alarm Unable to reach the exit, she retreated to her bedroom where she was spotted by firefighters. The aerial appliance raised the first responders to the second floor window, where they guided the resident and her dog to safety. The firefighters also plucked a man and a woman from the balcony of another fire-affected unit above, on the top floor of the three-storey building. The incident has prompted FRNSW to remind the public not to leave e-bikes and other Lithium-Ion battery-powered devices on charge near emergency exits. Explosive gas expelled FRNSW Commissioner, Jeremy Fewtrell, said, "Time after time, we see situations where occupants find themselves trapped by fire, caused by faulty Lithium-Ion battery fires. Residents can’t escape, leaving them exposed to toxic and explosive gas expelled by the batteries and the intense fires that generally follow." He adds, "These types of blazes are often more intense than regular fires due to the energy stored in the batteries and they burn faster. That means more danger to anyone trapped by the blaze which can take hold before fire crews can get there." Jeremy Fewtrell continues, "Please charge e-bikes and other devices away from escape points and try to keep an eye on them in case of trouble. Don’t charge them while you’re sleeping or away from home, and ensure you have a working smoke alarm. That’s what’s saved the day in this case." Highly flammable materials FRNSW also recommends: Never charge in exits or anywhere that would prevent users from escaping in the event of a fire Install active smoke alarms in the home/garage Always buy reputable lithium-ion battery brands and never ‘mix and match’ components Don’t leave devices charging in bedrooms or on beds, sofas or around highly flammable materials Try to charge devices outside if possible Beware of cheap, substandard lithium-ion battery-powered devices Avoid dropping, crushing or piercing battery cells If lithium-ion batteries are damaged or compromised, dispose of them properly Don’t throw them out in the rubbish, they can start garbage truck or rubbish tip fires when compacted Contact the local, approved recycling centre for disposal advice Store batteries and devices in a cool, dry area, away from combustible materials Ensure users have a home evacuation plan in the event of fire
The Automatic Fire Extinguisher (AMFE) not only releases the extinguishing gas but also signals that it has. In installations where accessibility is limited, the AMFE can be connected to a monitoring system by two connectors for reading a signal. Permanently controlling if the AMFE has been initiated (e.g., line control through a PLC or monitoring device) allows for precise knowledge about the status of whether and where a fire might have started in an otherwise hard-to-reach installation. Fire Suppression For Electrical Enclosures & Control Cabinets The S-AMFE is rated for typical PLC signals of 24 V/48 V and 1000 mA. The connectors are standardized (6.3 mm blade terminals), but customizations are possible. In control cabinets, fire can quickly lead to a disaster. The AMFE extinguishes reliably and precisely. Suitable For Various Applications: Domestic & Industrial Fire Safety The application spectrum of the AMFE is diverse: It ranges from technical household appliances, exhibits and collections to solutions in a vast variety of applications, both at home or in the industry. AMFE Form & Function The glass bulb bursts into small fragments and triggers a mechanism that releases the gas from the cylinder Due to rising heat in a fire scenario, the pressure inside the glass bulb increases. After the predetermined operating temperature of the heat-sensitive glass bulb is reached, the glass bulb bursts into small fragments and triggers a mechanism that releases the gas from the cylinder. The extinguishing medium is released through the holes in the outlet body and extinguishes the fire when the fire is still in an early stage. The quick operation and the effective extinguishing of the fire prevents further expansion of the fire and helps keeping damage to a minimum. AMFE Advantages At A Glance Easy to use Easy to install (can be retrofitted) Variety of customer-specific operating & releasing temperatures are available No water being used (gas) Scalable Robust and shock-tolerant NOVEC or CO2 as an extinguishing agent Usable in various applications (home, industry, automotive, etc.) Mechanical release; no electric power supply required Release mechanism: qualified in the automotive and sprinkler industry
VIKING Life’s factories and their global service stations are the heart of VIKING. Over the last decade, they have invested heavily in optimizing their production facilities within technology, innovation, safety and low energy consumption. In 2023, they have worked on a large number of local and global initiatives throughout their production facilities with the aim of promoting sustainable production methods. These initiatives include improved waste air treatment, further installation of solar panels on factories, introduction of environmentally friendly equipment such as electric forklifts, battery recycling, and more. Selected results from their 2023 local energy optimization initiatives: The installation of LED lights has resulted in electricity savings of 11.6% throughout their Danish facilities. The solar panels installed in their production facilities in Thailand now cover around 40% of the total electricity consumption, resulting in reduced CO2 emissions of approximately 844 tons per year. The facility also runs on 100% LED lights. The installation of LED light in their Chinese factory has resulted in a 44.8% reduction of electricity used for lighting. Paper consumption has dropped 17.5% from 2022 to 2023 as a result of targeted efforts to promote the paperless office. Reducing water and electricity consumption At VIKING, they are committed to reducing their water and electricity consumption At VIKING, they are committed to reducing their water and electricity consumption on an annual basis. To achieve this goal, they have established yearly targets for their service and manufacturing sites. These targets are set to reduce both electricity and water consumption. They are pleased to report that their manufacturing sites have successfully met the electricity target. However, their service stations have exceeded their targets, likely due to an increase in activity over the past year. Rise in need of water to produce products Conversely, for their water target, they can see the opposite scenario. Their manufacturing sites did not meet the target, while their service stations significantly reduced their consumption compared to 2022. Nonetheless, these results were expected as the increase in activity also implies an increased need of water to produce their products.
VIKING Norsafe totally enclosed and partially enclosed lifeboats keep crew and passengers safe and protected. Their enclosed lifeboats are used on commercial vessels worldwide, and they are designed and manufactured exclusively at VIKING’s production facilities to guarantee product quality. VIKING Norsafe lifeboats VIKING Norsafe lifeboats offer outstanding safety and performance in demanding conditions. Even if damaged or fully flooded, the lifeboats are self-righting and virtually unsinkable. Safely launch and retrieve the totally enclosed lifeboats with VIKING Norsafe conventional davits. VIKING Norsafe conventional davits VIKING Norsafe conventional davits are available in a wide range of safe working loads VIKING Norsafe conventional davits are available in a wide range of safe working loads, lowering heights and weights. VIKING Norsafe davits are produced in house and manufactured in accordance with SOLAS and national authority requirements, ensuring high quality products and safe operation for your crew. Key features of VIKING Norsafe enclosed lifeboats: Positive stability up to 180 degrees Smaller boats (under 8.5 m) are suitable as both lifeboat and rescue boat The largest boats have a maximum capacity of 150 persons in SOLAS configuration (430 mm, 82.5 kg per person) with alternative seating arrangements to accommodate ‘big persons’ in lifeboats Constructed in fire-retardant, glass-fiber reinforced polyester (GRP) Enclosed lifeboats can be delivered either with the VIKING Nadiro Drop-in-Ball system or the VIKING Norsafe Tor MK-2 offload release hook Models available for compliance with NORSOK R-002 and NOROG requirements Possibility for site and host-specific analysis of lifeboat occupant safety through DavitSim analysis Enclosed lifeboats can be launched via a cantilevered platform davit, single pivot gravity davit, or hydraulically pivoting davit Key features of VIKING Norsafe lifeboat davits: Approved according to SOLAS LSA and MODU Code regulations Designed for safe maintenance and operation Special solutions available for extremely high or low temperatures Alternatives for ATEX or IEC EX specifications for operation in hazardous zones Project specific solutions for retrofit Designed and manufactured at VIKING Norsafe facilities
Hochiki Europe, a globally renowned provider of innovative fire detection and life safety solutions, is proud to announce that it has been named Fire Detection Company of the Year by Building and Facilities News. This prestigious award recognizes Hochiki Europe's commitment to excellence, innovation, and reliability in the fire safety industry. fire safety standards Building and Facilities News highlighted Hochiki Europe's extensive product portfolio Building and Facilities News highlighted Hochiki Europe's extensive product portfolio, dedication to customer service, and continuous investment in research and development as key factors in their decision. The award also acknowledged the company's contributions to advancing fire safety standards and its strong reputation within the building and facilities management sector. innovation and excellence "We are incredibly honored to receive this award from Building and Facilities News," said Shinsuke Kubo, Managing Director at Hochiki Europe. Shinsuke Kubo adds, "This recognition is a testament to the hard work and dedication of our entire team. We are committed to providing our customers with the highest quality fire detection solutions that protect lives and property. This award inspires us to continue pushing the boundaries of innovation and excellence in the fire safety industry." fire detection solutions Hochiki Europe provides comprehensive fire safety solutions to a diverse range of industries, including commercial property, healthcare, education, industrial, transportation, and spaces of cultural and historical importance. This award further solidifies Hochiki Europe's position as a global pioneer in the fire detection industry, demonstrating its ongoing commitment to providing cutting-edge solutions and exceptional service to its customers.
Chubbsafes, one of the world’s most trusted security brands, proudly marks its 190th anniversary in 2025. Since its first safe patented in 1835, Chubbsafes has become synonymous with strength, dependability, and innovation, protecting valuables for generations. Reliability and craftsmanship For nearly two centuries, Chubbsafes has stood as a symbol of reliability and craftsmanship. Its rich history includes landmark innovations like the first patented resistant safe and pioneering materials such as Torch and drill-resistant (TDR) barriers. These achievements underscore the brand’s commitment to protecting valuables in an ever-evolving world. excellence and innovation “This year-long campaign is more than just a celebration. It’s a tribute to Chubbsafes’ legacy of reliability and excellence,” said Chanisa Wallace, Head of Marketing and Communication at Gunnebo Safe Storage. “For nearly 200 years, we’ve been trusted by customers worldwide. This milestone is an opportunity to honor our craftsmanship and innovation while looking ahead to the future we’re shaping together with our teams, partners, and customers.” limited-edition collector’s safe Combining robust protection with exquisite craftsmanship, only 190 units have been produced A highlight of the anniversary celebrations is the launch of the Chubbsafes™ 1835, a limited-edition 190th-anniversary collector’s safe. Combining robust protection with exquisite craftsmanship, only 190 individually numbered units have been produced, making it a true piece of history. Mark Brookes, Global Product & Standards Director at Gunnebo Safe Storage, added, “As we celebrate 190 years, we do so with the same core values that have guided us from the beginning: To Care, Be Fair, and Dare." Hard work and resilience "Chubbsafes is more than a brand; it’s a legacy of trust that has been earned through decades of hard work, innovation, and resilience." "The Chubbsafes™ 1835 encapsulates everything we stand for - a product that represents the culmination of almost two centuries of refinement and commitment to excellence. It is not just a safe but a piece of history, built to last and symbolizing the standards we uphold for the future.” modern security In 1889, the brand opened a state-of-the-art factory in Wolverhampton, England, cementing its reputation for quality Chubbsafes’ journey has been defined by transformative milestones. In 1889, the brand opened a state-of-the-art factory in Wolverhampton, England, cementing its reputation for quality and trust. Significant advancements followed to remain one step ahead of criminals and tools used to attempt to break into safes and vaults. This included Anti-Arc materials in 1959, TDR barriers in 1962, and lightweight Dualite materials in 2004. By 2019, Chubbsafes achieved T2 burglary certification, reaffirming its leadership in modern security. Protecting assets Chanisa concluded, “From pioneering advanced safe technologies to protecting assets around the globe, Chubbsafes has remained synonymous with safeguarding what truly matters." "And while we celebrate its storied past, the brand remains forward-thinking, continuously adapting to meet modern security challenges. Its commitment to innovation ensures it remains a trusted partner for safeguarding assets worldwide.” Visit the Chubbsafes 190 Years Celebration page to learn more about this historic milestone and explore the exciting initiatives planned for 2025.
Fire and Rescue NSW (FRNSW) is reminding the public not to charge Lithium-ion-powered devices, such as e-bikes, near emergency exits, following a second-storey unit fire yesterday at Merrylands West in Sydney. FRNSW releases dramatic footage from a camera worn by the Incident Commander in charge of the fire scene in Arcadia Street. Lithium-ion-powered devices The footage shows the first senior officer on scene, Station Officer Darryn Moalem from Wentworthville Fire Station, assigning firefighters crucial tasks and managing the rescue of three people and a dog from the burning building just after 11.15 am. Firefighters used ladders and an aerial appliance to rescue a woman from her unit Firefighters used ladders and an aerial appliance to rescue a woman from her unit, where an e-bike caught fire, blocking the front door and preventing her initial escape. Fortunately, a working smoke alarm activated. When the woman opened her door to investigate, she saw the e-bike that had been charging in a loungeroom, near the front door, on fire. Working smoke alarm Unable to reach the exit, she retreated to her bedroom where she was spotted by firefighters. The aerial appliance raised the first responders to the second floor window, where they guided the resident and her dog to safety. The firefighters also plucked a man and a woman from the balcony of another fire-affected unit above, on the top floor of the three-storey building. The incident has prompted FRNSW to remind the public not to leave e-bikes and other Lithium-Ion battery-powered devices on charge near emergency exits. Explosive gas expelled FRNSW Commissioner, Jeremy Fewtrell, said, "Time after time, we see situations where occupants find themselves trapped by fire, caused by faulty Lithium-Ion battery fires. Residents can’t escape, leaving them exposed to toxic and explosive gas expelled by the batteries and the intense fires that generally follow." He adds, "These types of blazes are often more intense than regular fires due to the energy stored in the batteries and they burn faster. That means more danger to anyone trapped by the blaze which can take hold before fire crews can get there." Jeremy Fewtrell continues, "Please charge e-bikes and other devices away from escape points and try to keep an eye on them in case of trouble. Don’t charge them while you’re sleeping or away from home, and ensure you have a working smoke alarm. That’s what’s saved the day in this case." Highly flammable materials FRNSW also recommends: Never charge in exits or anywhere that would prevent users from escaping in the event of a fire Install active smoke alarms in the home/garage Always buy reputable lithium-ion battery brands and never ‘mix and match’ components Don’t leave devices charging in bedrooms or on beds, sofas or around highly flammable materials Try to charge devices outside if possible Beware of cheap, substandard lithium-ion battery-powered devices Avoid dropping, crushing or piercing battery cells If lithium-ion batteries are damaged or compromised, dispose of them properly Don’t throw them out in the rubbish, they can start garbage truck or rubbish tip fires when compacted Contact the local, approved recycling centre for disposal advice Store batteries and devices in a cool, dry area, away from combustible materials Ensure users have a home evacuation plan in the event of fire


Expert Commentary
The 2022 Building Safety Act, instituted in direct response to the Grenfell Tower tragedy in London, UK, has outlined a raft of new responsibilities that building owners and managers must adhere to, in line with many of the deficiencies identified post-2017. With the UK’s building stock notoriously aging, many of us live and work in buildings that were built under outdated regulations and have not been updated for decades in some cases. As such there is an enormous amount of remedial safety work to be done that covers essential fire protection features such as fire doors, alarms, sprinklers, and cladding materials. High-rise buildings Despite £5bn being allocated by the government to replace dangerous cladding, progress is slow, and it has been estimated that the amount needed to fully address the issue is closer to £50bn. In London, more than £1bn has been spent, and 700 buildings over 18m in height have applied for government support. However, almost half of those buildings currently in that process have not seen any remedial work begin. This means in the capital alone there are more than a thousand high-rise buildings that are currently in need of urgent work. The need for retrofitting is particularly notable in high-rise buildings where fire spread can be rapid, and evacuation can be challenging. Across the country, there are over 11,000 high-risk buildings over 18 meters tall. In total, there could be two decades worth of remediation work. Building regulations Perfectly illustrates the delays people are facing when making their home or place of work safe from fire We had a stark, while thankfully non-tragic, reminder in August, that showed the danger of leaving these buildings in their current state when an apartment block in Dagenham caught fire. In this particular case, an external wall survey, commissioned four years before the fire, found that the block did not fully meet building regulations at the time of construction. Despite permission being granted in May 2023 and work being scheduled for June 2023, it was still ongoing almost 9 months after the target end date of December 2023. This perfectly illustrates the delays people are facing when making their home or place of work safe from fire. Traditional fire stopping The option that is often left to building owners is to completely remove the façade and install traditional fire stopping and, in many cases, requires residents to be relocated, requires large amounts of time, is severely disruptive, and carries a large price tag. This is why I have been vocal in my support of remedial work that doesn’t carry the enormous burden and cost of completely removing a facade to complete the work. By inserting a protective sock filled with an acrylic-based fire-resistant sealant, the fire can be contained within a small section of the cavity for longer, significantly reducing the speed at which fire and smoke can spread, and I’m a huge proponent of it. Fire-resistant performance The system is devised to reinstate the fire-resistant routine of rigid and flexible wall and floor structures The system is designed to reinstate the fire-resistant performance of rigid and flexible wall and floor constructions where a retrospective cavity barrier is required. I think it’s the best solution for a huge number of cases where remedial work is required. It can be installed in residential, commercial, industrial and public buildings and the work can be carried out in-situ. Without the need to remove the whole building façade, projects can take weeks rather than months and cut out significant costs. When we look at why delays are happening, and the number of buildings where action is yet to be taken, it’s obvious that these are key stumbling blocks. Recent fire in Dagenham We’ve gained experience up and down the country, from London to Manchester, working in fire safety and have identified a number of areas which we hope that we can further improve on. Early reports from the recent fire in Dagenham suggest that the fire alarms sounded too late or were not activated at all. The cause of this has not been formerly identified, however, I envisage, and we are actively developing an ‘early warning system’, that could be installed within any wall, floor or ceiling cavity. The system could then be linked to a current fire alarm system, and/or App on your mobile phone. Expertise in sensor technology Fire can spread quickly before penetrating rooms where it would activate conventional fire alarms The benefit of this system, which would leverage our existing expertise in sensor technology, would be the ability to detect fire and smoke where conventional systems wouldn’t be able to. Where a fire is outside of the core of the building, our system would sit within cavities where fire can spread quickly before penetrating rooms where it would activate conventional fire alarms. In the event of a fire, response time is crucial. This would enable occupants to be able to leave the building or call Fire Brigade at an earlier opportunity, giving vital and potentially lifesaving time. Fire safety retrofitting The failure to address these issues could lead to further loss of life, economic costs, and legal liabilities. Fire safety retrofitting is not just about compliance but ensuring the long-term safety of residents and building occupants, particularly in densely populated areas where the risk of fire can have devastating consequences. We can make this happen far more quickly and ensure far more effective action is taken if we begin to think more imaginatively about the, giving people crucial time to act when disaster hits.
While the technology sector was once considered the most desirable in terms of salary and job security, recent layoffs have exposed its vulnerability. Job security has always been a sought-after job benefit, and one career path that’s often overlooked is skilled trades. The skilled trades industry stands out as a resilient sector, offering the next generation of workers a promising path for growth and professional development through on-the-job experience and education. Significant talent gap With the retirement of Baby Boomers leading to a significant talent gap, current trade professionals are now more determined than ever to attract younger workers to the industry. Regrettably, many students in high school fail to see the value of pursuing a career in skilled trades. In a 2022 survey, only 16% of students noted they were likely to consider a career in the skilled trades. However, as other industries face a high level of uncertainty, the skilled trades offer stability and constant demand for services such as new construction, renovations, and climate change-resilient building improvements. The Benefit of Trade Education One of the major benefits of skilled trades education is its flexibility and room for career advancement The skilled trades industry presents young professionals with unique opportunities for hands-on learning and digital skill development. And as the next generation begins to explore higher education alternatives to gain valuable life skills, hands-on training in skilled trades becomes increasingly appealing. In trade education, learning happens directly from experiences in the field, complemented by classroom training, on-demand video sessions, and even virtual reality (VR) simulations. This approach ensures that graduates are well-prepared to start their careers immediately, avoiding the burden of college debt. One of the major benefits of skilled trades education is its flexibility and room for career advancement. Unlike traditional four-year college programs, trade school education typically lasts around two years, making it accessible to individuals at different stages of their careers. Moreover, the skilled trades industry provides workers with continuous opportunities for education and specialization. Formal certifications or licensing requirements define career paths in the skilled trades, and workers can pursue additional certifications to open new avenues for advancement. Beyond Traditional Training Techniques To maintain its resilience, the skilled trades industry is embracing technology To maintain its resilience, the skilled trades industry is embracing technology, integrating tech-focused learning methods and digital platforms to streamline processes and increase efficiency. Gen Z is inherently tech-savvy, and incorporating new technologies in training and in the field will attract these younger generations to the industry. This can include implementing tech-focused learning methods, embracing gamification, or transitioning from physical code books to digital platforms to streamline processes, make work more efficient, and increase engagement on new tools coming onto the jobsite. While the skilled trades industry offers numerous opportunities for growth and professional development, it is essential to acknowledge that these professions are not without their risks. Enhancing safety training Skilled trade workers, particularly those in fields like construction, electrical work, and fire safety, are often exposed to serious fire, electrical, and related hazards on the job. Ensuring the safety of these workers is of paramount importance. One powerful solution to enhance safety training is the integration of digital learning technology One powerful solution to enhance safety training is the integration of digital learning technology, which is uniquely suited to provide deep immersion simulations. By incorporating virtual reality (VR) and augmented reality (AR) training modules, skilled workers can experience lifelike scenarios that simulate potential hazards in a controlled environment. This kind of training allows them to develop critical skills, practice emergency response procedures, and make informed decisions without facing real-life risks. By leveraging digital learning technology, the skilled trades industry can better equip its workers with the knowledge and experience needed to enhance job safety and minimize workplace accidents. The Bottom Line The skilled trades industry presents a promising future for the next generation of talent. It offers resilience in the face of economic fluctuations and provides abundant opportunities for growth and professional development through hands-on training. To attract a new generation to this industry, organizations must be willing to not only emphasize value, in terms of resiliency salary, to candidates, but also show that the industry is moving towards innovation just like any other profession. As the industry continues to embrace technology, such as digital learning, it will remain relevant and appealing to young, technologically adept individuals seeking rewarding and stable careers. And by showcasing the value and potential of skilled trades, we as skilled trades professionals can inspire more individuals to consider this path and take the first step toward a successful and fulfilling career.
It’s been three years since the National Fire Protection Association (NFPA) published the most recent edition of the wide-ranging standard that spans “the application, installation, location, performance, inspection, testing and maintenance of fire alarm systems, fire warning equipment, and emergency warning equipment and their components.” 2022 update A 2022 edition was officially published in September 2021, after thousands of hours of collaboration, review, and debate among a technical committee. The 2022 update is a significant one; there are hundreds of changes in the document, ranging from minor edits of terminology to major items like Cybersecurity. Whether you’re an architect, engineer, contractor, or building owner/manager, NFPA 72 matters. It will have an impact on how you design, test, install and maintain life safety systems in the future. So even if your jurisdiction will not immediately adopt the 2022 edition of NFPA 72, it’s important to know what’s in the pipeline. Understanding the new edition will enable you to plan for the future and gain insight into how technologies like remote access are changing life safety and building systems. Here are five things you need to know about the 2022 edition of NFPA 72: 1) Secondary power supply requirements for batteries have changed Fire alarm control units typically rely on their local power grid as a primary power supply Batteries play a significant role in ensuring fire alarm system reliability but are one of the most overlooked items. Fire alarm control units typically rely on their local power grid as a primary power supply, and when that grid is operational, all is fine. However, should that power failure due to weather interference or technical failure and brownout conditions occur, the secondary power supply comes into play? Capacity NFPA 72 states that the secondary power supply (typically batteries) for the protected premises system shall have sufficient capacity to operate the system under quiescent load (system operating in a nonalarm condition) for a minimum of 24 hours. At the end of the 24-hour, the secondary power supply must be capable of operating all alarm notification appliances used for evacuation or to direct aid to the location of an emergency for five minutes. If the system incorporates in-building fire emergency voice/alarm communications, then the system needs to operate for 15 minutes. Charging system Batteries need to be able to take a charge from the charging system within the fire alarm control unit. Batteries have a life expectancy and also need to be load tested at least annually. But not all batteries are created equal. So much so that NFPA 72 has decided to raise the bar and impose a new requirement for the batteries used in fire alarm control units. Listing standards Examples of listing standards are UL 1989, Standby Batteries, and UL 2054, Household and Commercial Batteries NFPA 72 states that effective January 1, 2024, rechargeable batteries for the secondary power supply used in control units, devices, and accessories shall be listed or component-recognized by a nationally recognized testing laboratory. The action was taken because of the acknowledged new dangers posed by today’s battery technologies, primarily due to increased energy densities. Examples of listing standards are UL 1989, Standby Batteries, and UL 2054, Household and Commercial Batteries. 2) Fire alarm control units powered by the Internet of Things require new cybersecurity measures Should you be concerned about cybersecurity in a fire alarm control unit? It depends on how it was installed and connected. Many fire alarm systems do not require cybersecurity as they typically use their wiring and infrastructure and do not connect to “outside” equipment. For example, smoke detectors connected to the fire alarm control unit with wires only used for the fire alarm system, meaning there are no attack vectors that could be exploited. However, this is rapidly changing. Cybersecurity standards With fire alarm systems able to connect to the internet, allowing a user to see the status of their system on an app and even perform remote service diagnostics, these cloud-based integrations require new cybersecurity measures. Underwaters Laboratories, UL, has created a suite of cybersecurity standards. For example, The UL 2900 series of documents covering cybersecurity encompass healthcare, industrial and life safety signaling systems. Now manufacturers can produce fire alarm control units listed to these standards and “build-in” cybersecurity measures. Patches Bad actors are constantly on the prowl for vulnerabilities and patches need to be sent periodically But cybersecurity protection doesn’t stop once a piece of equipment leaves the factory. Bad actors are constantly on the prowl for vulnerabilities and patches need to be sent periodically to fix any such avenues for attack. Just like our computers, mobile devices, etc. all routinely receive updates to help to prevent unwanted attacks, fire alarm systems are no different. How these patches will get delivered and tested is different. Fire alarms Fire alarms need to function all of the time, they cannot go down unless service personnel or Firewatch people are on site. When patches are implemented, we need to ensure the system still functions properly, has come back online properly, and has not been compromised. Fire alarms, unlike our computers, cannot be rebooted over and over trying to fix them when a patch does not function properly. Nor do we have the luxury to replace a fire alarm CPU as quickly as a laptop. Guidelines for cybersecurity To address all of this, NFPA 72 has created a new chapter for 2022, Chapter 11 entitled “Cybersecurity.” The chapter is a placeholder for the technical committees to work on for the 2025 edition. But it does offer a glimpse into things to come and provides some guidance for today. Along with the chapter addition, there is a new Annex J entitled “Guidelines for Cybersecurity.” There is a wealth of information on how cybersecurity measures can be improved for fire alarm and signaling solutions within the new annex. 3) Remote access for fire alarm control units requires new capabilities We do not want to allow bad actors to possibly use the fire alarm system to access larger digital infrastructure Now that systems are being connected for users to see the status of their systems and remote diagnostics have become the norm, NFPA and UL have had to make changes to the allowance and proper usage of these features. UL 864 the Standard for Control Units and Accessories for Fire Alarm Systems has recently added testing protocols for remote access for fire alarm systems. NFPA 72 has also added guidance for how to properly implement remote access. Like cybersecurity, we do not want to allow bad actors to possibly use the fire alarm system to access larger digital infrastructure and do harm. Benefits The benefit of having properly listed equipment and processes for remote access is the door is now open even wider for remote testing, programming, and other applications. Some of the additions to NFPA 72 are that remote access shall not affect the operation or response of the fire alarm or signaling systems. Remote access can now allow for the first time the ability to test and perform maintenance activities, including the resetting, silencing, or operation of emergency control functions. Remote access There are additional requirements such as the system needing a means to manually terminate the remote access connection at the remote device and the fire alarm or signaling system control unit at any time. Further, remote access needs to automatically terminate within a maximum of one hour of inactivity in the remote access mode. Also, the resetting, silencing, or operation of emergency control functions shall be limited to a portion(s) of the system taken out of service and must be enabled by a qualified person onsite by password or limited access. 4) Fire alarm systems must meet new MNS standards The 2007 edition of the NFPA 72 added annex materials to guide allowing a fire alarm system to be used The role of communication in fire systems has been evolving for years, and NFPA 72 has been evolving with it. The 2007 edition of the NFPA 72 added annex materials to guide allowing a fire alarm system to be used or connected to a Mass Notification System (MNS). In the 2010 edition, this was taken a step further with the creation of Chapter 24, Emergency Communications Systems (ECS). UL 2572 Standard At that time there were no listing standards for MNS or ECS, but that was about to change. UL created a new Standard in 2016, UL 2572 Standard for Mass Notification Systems. This new Standard allows for equipment to become certified to be used for MNS or ECS applications. Since the Standard has been released many manufacturers have been able to obtain this certification for their respective systems. Starting with the 2022 edition of NFPA 72, control units installed as part of an MNS must be listed by applicable standards such as UL 2572, and Mass Notification Systems. 5) You are key to the process The NFPA has made the process of updating NFPA 72 rigorous, open and inclusive, and the organization values your opinion. Don’t sit on the sidelines. Your knowledge, input, and feedback will help ensure that life safety standards continue to improve in a way that makes sense for everyone. If you believe there are key changes that should be addressed or new technologies that should be added, go to the NFPA website to make your voice heard.
Editor's Dispatch
Information systems drive greater situational awareness when emergency responders are rushing to the scene, including access to live-911 audio feeds, video of the unfolding emergency, and/or geographic information showing the locations of fire hydrants and the best travel route to ensure the most rapid response. Information tools to manage emergency response include the locations of teams, vehicles, and personnel available in three dimensions, including locations in a multi-story building. Panasonic’s technology “First responders are thinking about getting to the scene and planning their disaster response,” says Aidan Clifford, Panasonic’s National Sales Manager. Vital information on the scene of an emergency includes video feeds, coordination with other services in the city or county, and communication with various responding agencies. Providing hardware to manage information during emergency response, Panasonic works to understand “the voice of the customer.” The company’s TOUGHBOOK ruggedized laptop computers serve the needs of fire and emergency response entities. A new Fire Advisory Council, currently being assembled, will help to guide Panasonic’s technology direction, and increase their understanding of the practical information needs of firefighters and other emergency responders. Panasonic survey Panasonic survey, 55% of respondents said access to real-time data is a top priority for their agency “The goal is to provide more information to end users more quickly,” says Marcus Claycomb, Panasonic’s Business Development Manager for the Public Sector. “Better information can save response time and enable first responders to adjust the type of response in real-time.” For example, streaming video can provide details of an unfolding emergency to firefighters as they are driving to the call. In a Panasonic survey, 55% of respondents said access to real-time information is a top priority for their agency. Useful information includes who is on the scene and where they are in real-time. Smart devices can track locations and vitals. Information goes in two directions. The ongoing deployment of 5G communications and devices will ensure information moves even faster and is more actionable. Live-911 capability Also in the Panasonic survey, 62% of respondents said computer-aided dispatch (CAD) and geographic information system (GIS) data are mission-critical. GIS data can include “layers” of information imposed on a map to show the fastest route to an incident and the locations of fire hydrants and/or accessible video cameras. Some 85% in the survey said the most important pieces of information are the location of teams, vehicles, hydrants, and/or personnel. Location and communication with drone assets are also a requirement. Live-911 capability can enable first responders to hear the dispatcher speaking with a caller in real-time. “A dispatcher can push the 911 call through the TOUGHBOOK laptop to responders on route to a call,” says Clifford. “It is an emerging technology that integrates with computer-aided dispatch (CAD) systems.” privacy of HIPAA data Device encryption and multi-factor authentication to secure the information, even ensuring the privacy of HIPAA data during an emergency medical call. Panasonic understands that fire and emergency departments need real-time information Broadly speaking, Panasonic understands that fire and emergency departments need real-time information provided by rugged devices that can withstand the daily rigors of firefighting. In the survey, 85% of respondents said rugged computer devices are important, as opposed to using consumer devices in the harsh environment of firefighters and EMS personnel. (Conducted in April 2023, the Panasonic Connect survey generated 117 responses from individuals in the fire rescue industry.) Total cost of ownership While first responders understand the importance of using ruggedized devices, purchasing decisions are not always made by those on the front lines. Sometimes it is someone else at the city or county level who decides to buy consumer-grade hardware, especially tablets, in lieu of a ruggedized laptop. Multiple problems can result, such as “battery swelling” and fire hazards if a battery overheats because of the high internal temperatures in a vehicle. Consumer devices are not designed to operate in temperatures above 100°F. Cost is the main reason to opt for less expensive consumer-grade equipment, but the lower cost is an illusion. The math is very different if one considers the total cost of ownership (TCO), including any downtime resulting from a battery charge not lasting the entire shift, for example. Panasonic's TOUGHBOOK laptops First responders should work to ensure their voices are heard as purchasing decisions are made Ruggedized equipment is more resistant to being dropped. Panasonic's TOUGHBOOK laptops meet the MIL-STD-810H specification and ingress protection (IP) standards, IP65 and IP66, which test for ruggedness and resistance to solids and liquids. Additional features include enhanced connectivity and embedded antenna, non-breakable components, and all-day batteries. First responders should work to ensure their voices are heard as purchasing decisions are made. They should have a conversation with command-level employees and throughout the fire service to ensure equipment purchasing reflects the real needs on the front lines, says Claycomb. What's Ahead? What’s ahead for information technology on the front lines of firefighting? “There is an incredible opportunity ahead to integrate the TOUGHBOOK with fire vehicles,” says Marcus. He adds, “And the potential of using 5G will be limited only by our own creativity. Looking ahead, we can expect more artificial intelligence (AI), augmented reality (AR), and an incredible amount of data.”
In Ann Arbor, Michigan, USA, in May 2022, a helmet camera recorded firefighters extinguishing a truck fire along I-94, catching every detail as sparks flew and firefighters hosed down the truck to suppress the blaze. Firefighters also hosed down the grass on the side of the freeway to put out hot spots and prevent a grass fire, MLive.com reported. The helmet-cam was part of a voluntary program that involves Ann Arbor firefighters wearing cameras when responding to active structure fires to capture video that can be used as a training tool, in order to better understand what went right and what went wrong. Video can also be released to the public to showcase how tax dollars are being spent. A focus on structure fires precludes any concerns about privacy. Helmet-cams used by firefighters Helmet-cams used by firefighters can provide a valuable tool for training and post-incident analysis Helmet-cams used by firefighters can provide a valuable tool for training and post-incident analysis. On the other hand, they could impact how a firefighter does his or her job or even violate privacy concerns and/or the public trust. While debate around the use of body-cams by law enforcement officers has mostly been settled, opinions still vary about the use of helmet-cams by firefighters. In one sense, the rules and regulations have not caught up with the technology, including smaller (and inexpensive) video cameras that can easily (and even discreetly) be mounted on a firefighter’s helmet. Some departments have banned use of helmet-cams, while others have sought to restrict and control their use. Still others haven’t given it much thought. Multiple perspectives for post-incident analysis An advantage of helmet-cams is to record video of the actions of officers and firefighters at an incident and to provide multiple perspectives for post-incident analysis. Critiquing performance is a learning tool to encourage continuous improvement. In case of an injury or line-of-duty death (LODD), helmet-cam footage provides an unblinking record of exactly what occurred. If a time element is being assessed, a helmet-cam video can display each activity along with a time display, thus eliminating the need for a stopwatch. Clear and time-marked audio recording In addition to video, helmet-cams can provide a clear and time-marked audio recording, not limited by radio-frequency interference. (Audio recordings are subject to additional privacy concerns in some jurisdictions.) A possible downside of using helmet-cams is to distract a firefighter from his or her duties or to narrow their focus to the detriment of a broad awareness of their surroundings. It is important that a firefighter not miss something that is happening at the periphery of his or her line-of-sight. Helmet-Cams can distract a firefighter’s attention Conscious of how they appear in a video recording, a firefighter might be more guarded in their actions or words; at the other extreme, they might be tempted to “show off” for the camera by taking greater risks to provide more dramatic footage. A firefighter with a helmet-cam might also become preoccupied with operating the camera to optimize video to the detriment of other concerns. Becoming fixated on the technology can distract a firefighter’s attention from the real job at hand. Creating a policy that addresses issues are helmet-cams use Departments should consider carefully the issues surrounding helmet-cams and create a policy Departments should consider carefully the issues surrounding helmet-cams and create a policy that addresses those issues. Fire service leaders may benefit from collaborating with local police leaders who have worked with body-cam video and know the possible evidentiary value of video that can be captured on the devices. Fire departments should be aware that any captured footage may have evidentiary value, if it relates to a crime or police internal affairs investigation. Unlike body-cams used by police, which download video to the department at the end of a shift and are covered by department policy, helmet-cams are less restricted and less well-managed. Firefighters may even own their cameras. Privacy concerns surrounding the use of helmet-cams Some fire departments, such as Houston, San Antonio, and San Francisco, have banned helmet-cams because of privacy concerns and worries about how a video might embarrass a department. Privacy concerns include the use of helmet-cams in medical calls, which make up most a firefighter’s daily responses. There should be rules that ensure that videos do not eventually make their way to Internet sites such as YouTube. In New Jersey, for example, Cathy’s Law (passed in 2012) restricts images and recordings at emergency scenes, such as motor vehicle accidents.
Among the ways, garments protect firefighters is by reducing the heat stress and discomfort created by the need to carry heavy gear. Making the garments more comfortable to wear means less physical stress. Garments also help to protect firefighters from the toxic elements in the fire environment. The extent to which plastic materials can generate toxic smoke when they burn has previously been ignored but is now better understood. Concerted effort to understand end user As a manufacturer of fibers used in firefighting garments, DuPont makes a concerted effort to understand the end user of their products; that is, the firefighter. They seek to keep the firefighter safer and to extend the time available to do his or her job safely. DuPont works with fabric and garment manufacturers to focus on minimizing the impact of the toxic environment. Firefighter’s awareness Multiple initiatives seek to make firefighters more aware of potential dangers and best practices Awareness by firefighters of the negative impact of toxic materials has increased substantially. Multiple initiatives seek to make firefighters more aware of potential dangers and best practices to avoid exposure to contamination. Organizations promoting greater awareness include firefighters’ unions, the International Association of Fire Chiefs (IAFC), and the National Fallen Firefighters Association. Toxic smoke For example, testing confirms that toxic smoke often affects firefighters in the neck and jaw area, where sweat promotes absorption of smoke particles. A woven hood or baklava avoids the absorption, reflected in the NFPA Standard 1971, which makes particulate protection hoods mandatory. The Nomex Nano Flex hood increases the comfort of the gear. Avoiding toxic materials also includes no inclusion of per-and poly-fluoroalkyl substances (PFAs) in garment materials themselves. Standards and Specifications Testing is an area of focus for DuPont, which has the capabilities to test the layered structures firefighters are wearing. One tool is the Thermo-Man, a fully instrumented mannequin that tests the likely burn injuries of flash-over fires. DuPont works with the NFPA, ISO, EN, and other standards committees to develop testing and certified standards to ensure the performance of firefighter garments. Fire gear is specified in each region according to a standard (minimum) performance. In many cases, garments out-perform the requirements. Other variables Other variables of firefighting garments include the fitting and weight Other variables of firefighting garments include the fitting and weight. A less expensive approach might yield a garment that sacrifices comfort. Geographic and climate differences matter, too. A firefighter in the North would prefer a different garment than in the South. Garments should be comfortable, lighter, and warmer in cold environments. On the topic of gender, garment makers offer female designs that are cut and shaped differently. Garment makers evaluate the weight of the assembly, how well it protects against the heat, and the comfort. DuPont works with garment makers to test various materials and how they perform in fire garments. The company works with firefighter consultants in the U.S. and Europe who help them understand the language of firefighters. Addressing Dangers of Toxic Materials Cleaning fire gear of toxic materials is a challenge related to garments. Toxic materials on fire gear returned to the fire station can also expose the station environment to danger. Changing logistics and processes are driving how gear is handled in the fire station environments. Some stations are designating black zones, gray zones, and white zones, depending on the level of contamination of the gear in those areas. Washing and drying More frequent washing of bulky, heavy gear helps to circumvent the impact of toxic materials, but repeated washing and drying can cause mechanical stress and resulting damage to a garment. DuPont collaborates with weaving mills and garment makers to develop fabrics and garments that stand up well to frequent washing.Toxic smoke particles and mandatory use of hoods on firefighters is translating into more washing. As time goes on, the washing and decontamination process will likely become more professionalized with laundry companies stepping in to wash and handle the garments. Fire stations are not well suited to cleaning these garments. Nomex Nano fiber Nomex Nano Flex is a non-woven material that retains toxic and cancer-causing particles Developed to address the growing problem of heat stress, DuPont’s Nomex Nano fiber is engineered to be thinner than other advanced flame-resistant materials. Nomex Nano Flex was developed to help make products like firefighter hoods more protective against particles without compromising comfort. Nomex Nano Flex is a non-woven material that retains toxic and cancer-causing particles, and creates a particulate barrier. It also protects the firefighter from outside heat while cooling the firefighter by evacuating body heat. Higher evaporation rate Nomex Nano Flex has a higher evaporation rate. For the same thermal protection performance (TPP), it also has higher total heat loss (THL). Combining protection, thermal performance and toughness, Nomex Xtreme Performance is the highest performance category of solutions for flame-resistant personal protective apparel. Feedback from Firefighters “If we have a new innovation, or want to share our developments, we go proactively to fire departments to ask: Will this help you or not?” says Alfons N. Held, Global Market Leader, Emergency Response, DuPont Personal Protection. There is a difference between lab testing and what firefighters experience in the real world. Alfons N. Held adds, “We seek to understand what they need, and approach ‘lighthouse’ fire departments for guidance.” In any country or jurisdiction, there are fire departments – ‘lighthouse’ departments – that set the trends and work to evaluate the gear. If someone in Florida is using certain gear, it might also work in Texas or Arizona. The protection level Areas of continuing research in terms of firefighter garments include making them more wash-durable The question is: What protection level do we need? Given that level, departments seek to balance comfort with performance. Ironically, of the firefighters who die every year, some two-thirds of the deaths are attributable to overexertion, while less than 10% is linked to the fire/heat. Areas of continuing research in terms of firefighter garments include making them more wash-durable, more comfortable (with higher evaporation) and more lightweight. Complex systems Garments can be complex systems; heavy turnout gear is a five-layer garment with each layer contributing to performance – the outer shell, the inner liner, a moisture membrane, and one or two thermal liners. Sometimes attention is more focused on the outer layer of the gear with less awareness of the other layers and how the entire system works together. Importance of station wear In fact, protection of the firefighter starts at the skin, so station wear is important. “In our view, looking at all the layers on the skin and outwards is important,” says Alfons N. Held, adding “Firefighters wear various materials that are not always optimal.” For example, a cotton undergarment might get wet from sweat, stay wet and not evaporate. Environmental impact is another concern among garment-makers. Can the materials be reused or recycled? Some countries in Europe ask that manufacturers take back garments after they are used. New Garments, New Needs A special need is development of new garments that can perform at the wildland urban interface (WUI), where catastrophic wildland fires encroach on residential areas. Design of gear for wildland firefighting has been lighter and does not include breathing systems. When fires reach residential areas, gear needs change. Wildland firefighters are not equipped to enter a structure fire and do not have adequate protection against carcinogens. New gear designs are needed that address both environments.
Case studies
Reel Cinemas in Bahrain’s popular Marassi Mall has enhanced its fire safety infrastructure by installing a state-of-the-art Axis AX fire alarm system from Advanced. Axis AX fire system The installation was designed to protect both cinema-goers and staff across a wide range of areas, including seven cinema screens, an IMAX theatre, VIP lounges, the kitchen, a waiting lobby, and common areas. This project was spearheaded by Alpha Fire & Safety and used the powerful Axis AX fire system, known for its flexibility, reliability, and compliance with UL 864 10th Edition standards. scalability and advanced configuration With the installation covering such a dynamic environment, including high-ceiling auditoriums and specialized spaces like the IMAX screen, the project posed significant logistical challenges. However, the scalability and advanced configuration options of the Axis AX system allowed the team to overcome these hurdles seamlessly. 4-loop Axis AX panel An audio booster panel was also installed to ensure that emergency communications would be transmitted Alpha Fire & Safety chose a 4-loop Axis AX panel, along with a comprehensive range of devices including smoke detectors, heat detectors, sounders, manual call points, and duct detectors. In addition, a voice evacuation system was integrated into the installation, ensuring clear and effective emergency communications across all areas of the cinema. An audio booster panel was also installed to ensure that emergency communications would be transmitted throughout the expansive complex. comprehensive control and safety The system's versatility was further demonstrated through its integration with third-party systems critical to Reel Cinemas' operations. Access control, fan control units, kitchen hoods, motorized smoke dampers, and FM200 gas control systems were all seamlessly connected to the Axis AX platform, ensuring comprehensive control and safety management from a central point. reliability and ease of programming "The Axis AX installation at Reel Cinemas was smooth and efficient, despite the complexities of working in a large-scale entertainment venue. The system’s flexibility and advanced configuration options allowed us to tailor it to the project’s specific fire safety needs, seamlessly integrating with the cinema’s existing infrastructure," said Adithya Karne, Draughtsman & Estimator at Alpha Fire & Safety. He adds, "The Axis AX’s reliability and ease of programming enabled us to meet the challenges of this dynamic environment, while ensuring top-level safety for cinema-goers and staff." powerful fire protection Sargunan Sellamuthu, Advanced’s Business Development Manager for the Middle East, said, "We’re proud to see the Axis AX system installed at such a prestigious location as Reel Cinemas in Bahrain." Sargunan Sellamuthu adds, "This project highlights the system’s ability to manage complex environments, easily integrating with other critical building systems, while offering the flexibility to meet the unique demands of an entertainment venue. It’s a great example of how our technology delivers scalable, powerful fire protection for even the most challenging applications." advanced fire detection and control The reliability of the Axis AX system ensures that safety remains a priority without compromising the cinema’s design Reel Cinemas equipped with the Axis AX system, is well prepared to protect its visitors, providing peace of mind through advanced fire detection and control technology. As a venue with thousands of patrons passing through its doors daily, the reliability of the Axis AX system ensures that safety remains a priority without compromising the cinema’s sleek, modern design. fire protection solutions This installation is a testament to Advanced’s ongoing commitment to providing robust and scalable fire protection solutions for entertainment complexes and beyond. With its ability to support intelligent devices and integrate with building management systems, the Axis AX continues to be the preferred choice for major installations in the Middle East and around the world. UL 864-approved devices The versatile system is suited to a wide range of settings, from mass transportation and industrial complexes Axis AX is their complete solution for customers demanding a versatile fire alarm system of high-performance fire panels, audio systems, command centers, and devices that are fully UL 864-approved. The versatile system is suited to a wide range of settings, from mass transportation and industrial complexes to landmark developments, and historic and public buildings. Advanced portfolio As a world pioneer in the development and manufacture of intelligent fire systems, Advanced products are specified in locations around the world, from single-panel installations to large, multi-site networks. The Advanced portfolio includes complete fire detection systems, multiprotocol fire panels, extinguishing control, false alarm management, and reduction systems as well as emergency lighting. Advanced is owned by FTSE 100 company Halma PLC – a global group of life-saving technology companies with a clear purpose to grow a safer, cleaner, healthier future for everyone, every day.
A blend of historic charm and modern functionality, the Printworks Belfast has undergone a significant renovation to meet the demands of contemporary office spaces, while preserving its Victorian heritage. Central to this transformation is a robust fire safety system powered by Hochiki devices, ensuring the protection of occupants and the building's architectural integrity. Printworks Belfast The Printworks Belfast, a historic Victorian warehouse dating back to 1890, is located in the heart of Belfast's vibrant business district. Originally built for R Carswell & Son, a renowned printing and stationery firm, the building has undergone meticulous restoration. Angus Properties acquired the property in 2019 and has transformed it into a modern, open-plan office space, while preserving its industrial character. comprehensive modernization Key features include a new atrium, a cobbled courtyard, and additional floors with panoramic city views Key features include a new atrium, a cobbled courtyard, and additional floors with panoramic city views. The Printworks is a sought-after location, offering flexible office spaces and potential retail or hospitality opportunities on the ground floor. The comprehensive modernization of the Printworks Belfast across its five floors necessitated the installation of a robust life safety system that would safeguard future occupants, while integrating sympathetically with the building's historical features. user-friendly fire safety systems 365 Fire Security, a premier provider of life safety solutions, was entrusted with installing the fire safety systems at Printworks Belfast. This marked the company's inaugural use of Hochiki equipment, renowned for its dependability, quality, and user-friendly installation. The decision was influenced by a recommendation from James Morrison, National Key Accounts Manager for Hochiki, who highlighted the advantages of Hochiki's cutting-edge technology and streamlined installation process. heat and smoke detectors The heat and smoke sensors are engineered to deliver swift and precise fire detection The installation at Printworks Belfast encompassed a variety of standard heat and smoke detectors from Hochiki, interconnected to a central fire alarm control panel equipped with a selection of other Hochiki field devices. The heat and smoke sensors are engineered to deliver swift and precise fire detection, ensuring optimal safety for the building's occupants. ease of installation Wesley Allan, Managing Director at 365 Fire Security explained how the Hochiki equipment proved to be an asset in the Printworks Belfast restoration project. He said, "Its ease of installation was a significant advantage, given the complex nature of the building and the need to minimize disruptions during the upgrade works." Wesley Allan adds, "Even though we installed over 500 devices, the process was remarkably smooth thanks to Hochiki's consistent base design. This standardization significantly simplified the installation process and reduced the overall project timeline." reliable and early detection The detectors provide comprehensive fire protection across all five floors, offering reliable and early detection of potential hazards. Moreover, the devices seamlessly integrate with the building's architectural elements, preserving its historic charm, while ensuring state-of-the-art fire safety. The successful installation of Hochiki's fire detection system by 365 Fire Security has fortified Printworks Belfast with a robust and reliable life safety infrastructure. quality and reliability This project exemplifies the effectiveness of Hochiki's technology in a complex, mixed-use building This project exemplifies the effectiveness of Hochiki's technology in a complex, mixed-use building, balancing historical preservation and modern safety standards. Wesley Allan continues, "Despite having no prior experience with Hochiki devices, the Printworks Belfast project has convinced us of their exceptional quality and reliability. Unless specified otherwise, we'll now make Hochiki our first choice for fire detection systems and devices." dependability and effectiveness Consequently, Printworks Belfast is primed for its modern office space role, equipped with a fire safety system that safeguards both the building's heritage and its occupants. The triumph of this installation marks a promising commencement for 365 Fire Security's utilization of Hochiki equipment, underscoring the systems' user-friendliness, dependability, and effectiveness in intricate and demanding environments.
Masterfire Project Managed a Site-Wide Fire Detection & Alarm & Emergency Lighting Upgrade at University Hospital Waterford. Masterfire successfully completed a large-scale upgrade of both the Fire Alarm & Emergency Lighting systems at University Hospital Waterford in early 2021. University Hospital Waterford is a large acute hospital facility with a capacity for 431 inpatients and a further 85-day procedure beds. Fire Alarm System Upgrade The Fire Alarm System upgrade involved the installation of 75 new fire alarm control panel networks and graphic packages, 6050 new fire detection points, and 65 km of fire-rated cable. The Emergency Lighting System upgrade involved the installation of 50 new emergency light control panels, 5200 new emergency luminaires and 47 km of fire rated cable. Masterfire managed this project from design to installation, commission, system handover and continued maintenance. During the project, they consistently met the needs of the live healthcare environment, from complying with infection control measures to protecting patient privacy & dignity and assigning fall back areas.
Fire and Rescue NSW Hazardous Materials crews remain at the scene of yesterday's major fire and chemical emergency in Sydney's west. More than 100 firefighters and 20 fire trucks were confronted by 60-metre-high fireballs at the waste recycling plant in Christies Street, St Marys. Industrial Fire Fallout FRNSW is working with site management, the NSW Environment Protection Agency and Comcare Burning gas bottles and chemicals caused numerous explosions at the height of the blaze, forcing authorities to evacuate workers nearby. Once the fire was contained early last night, firefighters worked through the evening to extinguish persistent hot spots. FRNSW is working with site management, the NSW Environment Protection Agency and Comcare to execute a Hazardous Materials management plan, including monitoring runoff from firefighting efforts. Aerial Threat Assessment FRNSW's Aviation Unit is using Remotely Piloted Aircraft Systems or drones, to provide valuable threat and damage assessments at the scene. FRNSW fire investigators are also at the site to determine the origin and cause of the fire.
Fire safety is one of the most critical paths of industrial operations especially in manufacturing plants. Factories handle a lot of combustible materials, flammable liquids and electrical machinery that can cause fires if not properly managed well. Palladium Safety Solutions completely specialize in providing top tire safety solutions to protect businesses from catastrophic fire hazards. Here in this case study, people can learn everything about how the fire safety solutions prevent a major disaster at a large manufacturing plant. The manufacturing plant and its fire safety challenges The manufacturing plant that will help is the major producer of industrial equipment operating in a 1, 00, 000 square foot facility. The plant houses different production units, including welding solutions, painting booths and chemical storage areas. It employs more than 500 workers and operates 24/7 to meet the high production demands. Fire safety challenges Overload circuits, faulty wiring and overheating machines posed a major fire risk Overload circuits, faulty wiring and overheating machines posed a major fire risk. The plant stored large amounts of chemicals, solvents and gases increasing the likelihood of outbreaks. While the plant fire extinguishers lacked the advanced fire suppression system. The workers were not sufficiently trained in fire safety protocols, which could also lead to slow response in emergencies. The existing smoke detectors were old and unreliable that led to delays in fire detection. Considering all these risks the plant needs a complete fire safety overall to ensure the safety of employees and even prevent damage to infrastructure. Palladium’s safety solutions After conducting a thorough risk assessment, they implemented a comprehensive fire safety plan tailored to the plant’s requirements. They had placed the outdated smoke detectors with modern high sensitivity fire alarm systems. These detectors can quickly identify smoke and also heat changes allowing early warning alerts for plants. They install an automatic fire suppression unit also like sprinkler systems that activate automatically when a file is detected. It helps contain small fires before they spread. Gas based suppression for sensitive areas are really important in areas with electronic equipment. They have used gas based suppression instead of water to prevent damage. To reduce the risk of electrical fires, they inspected and so upgraded faulty wiring and installed circuit Breakers to prevent overloads. Their experts have implemented regular maintenance scheduled for electrical equipment. They conducted fire safety training sessions for all employees covering how to use fire extinguishers correctly and evacuation procedures in case of fire. They can help identify the hazards in the workplace. They have designed a clear fire exit plan and placed visible emergency exit signs throughout the plant. They also organize monthly fire drills to ensure that the workers know how to react swiftly in an emergency. They have introduced safety protocols for handling flammable substances like storing chemicals in fire resistant cabinets and using proper ventilation and chemical storage areas, while implementing a labeling system to identify hazardous materials. how Palladium's solutions prevented disaster? Three months after they implemented a new fire safety solution, the plant faced a real life emergency. One of the welding machines malfunctioned causing a major spark that ignited flammable fumes in the painting booth. The advanced fire alarm system detected the smoke immediately and triggered an alarm Within seconds flames started spreading towards the chemical storage area. The advanced fire alarm system detected the smoke immediately and triggered an alarm. The sprinkler activated and also controlled the flames. In the chemical storage area, the gas based fire suppression system prevented the fire from spreading. Because of the fire safety training, workers responded well. They also used fire extinguishers to control small flames and evacuated safely. Local fire department notified instantly The local fire department was notified instantly and they arrived within just a few minutes, so as to ensure a complete containment. There were no injuries or casualties occurred and there was minimum property damage, as the fire was contained in less than five minutes. Impact of Palladium’s safety solutions The best part about Palladium’s safety solutions is that the employees felt really confident working in a safer environment. The training and drills ensured they knew how to react and agencies. By preventing a major fire the plant saved a lot of damage, legal liabilities and downtime expenses. Palladium’s solutions helped the plant meet all the required fire safety standards and avoid fines or even penalties. With a safer work environment, employees could focus on their work without the stress of fire hazards will stop. Palladium Safety Solutions secure manufacturing plant So above all, Palladium Safety Solutions are completely committed to provide the best fire safety solutions to protect businesses from devastating fire accidents. Their successful intervention at the manufacturing plant completely demonstrates the importance of advanced fire detection suppression employee training and risk assessment. By investing in fire safety, property managers can protect their employees’ assets and operations.
JCB Fire Ltd, a major fire alarm contractor, recently partnered with Hochiki to supply and commission a state-of-the-art fire detection system at Costa Coffee’s brand-new flagship store at Solihull's Touchwood Shopping Center for their long-standing client - Otec Electrical Limited. Costa Coffee, a beloved British coffeehouse chain, has become synonymous with high-quality coffee and a warm, inviting atmosphere. With a wide range of handcrafted beverages, from classic espressos to innovative seasonal drinks, Costa offers something for everyone. Situated in the popular Touchwood Shopping Center, which attracts over 13 million visitors annually, the new flagship Costa required a fire safety system that would meet the demands of this busy retail hub and ensure the safety of all coffee lovers who visited. Hochiki's fire detection devices JCB Fire Ltd selected Hochiki's fire detection devices for their innovative features The Solihull store, a former Foot Locker, needed a complete overhaul to accommodate Costa Coffee's unique brief. This included the integration of a new fire detection system that would interface seamlessly with the existing building's infrastructure, including security and sprinkler systems and meet the company's strict adherence policy to the Disability Discrimination Act (DDA). JCB Fire Ltd selected Hochiki's fire detection devices for their innovative features and because their open protocol capability ensures compatibility with various fire alarm control panels, providing flexibility in system design. Additionally, the devices are easy to install, reducing project timelines, and offer ultra-reliability, minimizing false alarms. Hochiki's ESP range of sensors To meet the stringent safety requirements of the DDA, Hochiki's market-pioneering Audio and Visual alarm devices were also installed. These devices are designed to enhance visibility for individuals with hearing impairments and improve the audibility of fire alarms, ensuring that all occupants can be evacuated quickly and efficiently. Hochiki's ESP range of sensors further simplifies the installation process Hochiki's ESP range of sensors further simplifies the installation process with electronics-free mounting bases and easy addressing. The versatile sensors offer a variety of detection options, including smoke, heat, and multi-criteria detection. Customizable settings, such as adjustable sensitivity and drift compensation, allow for tailored fire protection – perfect for this restaurant spread over two floors. Hochiki’s innovative technology Grant Wheeler, General Manager of JCB Fire, highlighted the benefits of partnering with Hochiki. He emphasized the advanced technology, reduced false alarms, and efficient installation processes that contribute to the overall success of the fire safety project at Costa. Grant Wheeler said, "The successful installation at the Solihull store was completed in less than a week, by our client Otec Electrical demonstrating the effectiveness of our partnership with Hochiki. We were able to combine our expertise with Hochiki’s innovative technology ensuring the safety and security of Costa Coffee's customers and staff in this brand-new store." Fire detection solution Hochiki's ESP range, as demonstrated in this exciting project at Costa Coffee's new outlet, offers a robust and reliable fire detection solution for retail and restaurant environments. By providing advanced features like open protocol capability, easy installation, and customizable settings, Hochiki empowers retail businesses to prioritize safety without compromising esthetics. To learn more about how Hochiki's ESP range can elevate fire safety measures, visit the Hochiki website or contact a local authorized distributor.
Reel Cinemas in Bahrain’s popular Marassi Mall has enhanced its fire safety infrastructure by installing a state-of-the-art Axis AX fire alarm system from Advanced. Axis AX fire system The installation was designed to protect both cinema-goers and staff across a wide range of areas, including seven cinema screens, an IMAX theatre, VIP lounges, the kitchen, a waiting lobby, and common areas. This project was spearheaded by Alpha Fire & Safety and used the powerful Axis AX fire system, known for its flexibility, reliability, and compliance with UL 864 10th Edition standards. scalability and advanced configuration With the installation covering such a dynamic environment, including high-ceiling auditoriums and specialized spaces like the IMAX screen, the project posed significant logistical challenges. However, the scalability and advanced configuration options of the Axis AX system allowed the team to overcome these hurdles seamlessly. 4-loop Axis AX panel An audio booster panel was also installed to ensure that emergency communications would be transmitted Alpha Fire & Safety chose a 4-loop Axis AX panel, along with a comprehensive range of devices including smoke detectors, heat detectors, sounders, manual call points, and duct detectors. In addition, a voice evacuation system was integrated into the installation, ensuring clear and effective emergency communications across all areas of the cinema. An audio booster panel was also installed to ensure that emergency communications would be transmitted throughout the expansive complex. comprehensive control and safety The system's versatility was further demonstrated through its integration with third-party systems critical to Reel Cinemas' operations. Access control, fan control units, kitchen hoods, motorized smoke dampers, and FM200 gas control systems were all seamlessly connected to the Axis AX platform, ensuring comprehensive control and safety management from a central point. reliability and ease of programming "The Axis AX installation at Reel Cinemas was smooth and efficient, despite the complexities of working in a large-scale entertainment venue. The system’s flexibility and advanced configuration options allowed us to tailor it to the project’s specific fire safety needs, seamlessly integrating with the cinema’s existing infrastructure," said Adithya Karne, Draughtsman & Estimator at Alpha Fire & Safety. He adds, "The Axis AX’s reliability and ease of programming enabled us to meet the challenges of this dynamic environment, while ensuring top-level safety for cinema-goers and staff." powerful fire protection Sargunan Sellamuthu, Advanced’s Business Development Manager for the Middle East, said, "We’re proud to see the Axis AX system installed at such a prestigious location as Reel Cinemas in Bahrain." Sargunan Sellamuthu adds, "This project highlights the system’s ability to manage complex environments, easily integrating with other critical building systems, while offering the flexibility to meet the unique demands of an entertainment venue. It’s a great example of how our technology delivers scalable, powerful fire protection for even the most challenging applications." advanced fire detection and control The reliability of the Axis AX system ensures that safety remains a priority without compromising the cinema’s design Reel Cinemas equipped with the Axis AX system, is well prepared to protect its visitors, providing peace of mind through advanced fire detection and control technology. As a venue with thousands of patrons passing through its doors daily, the reliability of the Axis AX system ensures that safety remains a priority without compromising the cinema’s sleek, modern design. fire protection solutions This installation is a testament to Advanced’s ongoing commitment to providing robust and scalable fire protection solutions for entertainment complexes and beyond. With its ability to support intelligent devices and integrate with building management systems, the Axis AX continues to be the preferred choice for major installations in the Middle East and around the world. UL 864-approved devices The versatile system is suited to a wide range of settings, from mass transportation and industrial complexes Axis AX is their complete solution for customers demanding a versatile fire alarm system of high-performance fire panels, audio systems, command centers, and devices that are fully UL 864-approved. The versatile system is suited to a wide range of settings, from mass transportation and industrial complexes to landmark developments, and historic and public buildings. Advanced portfolio As a world pioneer in the development and manufacture of intelligent fire systems, Advanced products are specified in locations around the world, from single-panel installations to large, multi-site networks. The Advanced portfolio includes complete fire detection systems, multiprotocol fire panels, extinguishing control, false alarm management, and reduction systems as well as emergency lighting. Advanced is owned by FTSE 100 company Halma PLC – a global group of life-saving technology companies with a clear purpose to grow a safer, cleaner, healthier future for everyone, every day.
A blend of historic charm and modern functionality, the Printworks Belfast has undergone a significant renovation to meet the demands of contemporary office spaces, while preserving its Victorian heritage. Central to this transformation is a robust fire safety system powered by Hochiki devices, ensuring the protection of occupants and the building's architectural integrity. Printworks Belfast The Printworks Belfast, a historic Victorian warehouse dating back to 1890, is located in the heart of Belfast's vibrant business district. Originally built for R Carswell & Son, a renowned printing and stationery firm, the building has undergone meticulous restoration. Angus Properties acquired the property in 2019 and has transformed it into a modern, open-plan office space, while preserving its industrial character. comprehensive modernization Key features include a new atrium, a cobbled courtyard, and additional floors with panoramic city views Key features include a new atrium, a cobbled courtyard, and additional floors with panoramic city views. The Printworks is a sought-after location, offering flexible office spaces and potential retail or hospitality opportunities on the ground floor. The comprehensive modernization of the Printworks Belfast across its five floors necessitated the installation of a robust life safety system that would safeguard future occupants, while integrating sympathetically with the building's historical features. user-friendly fire safety systems 365 Fire Security, a premier provider of life safety solutions, was entrusted with installing the fire safety systems at Printworks Belfast. This marked the company's inaugural use of Hochiki equipment, renowned for its dependability, quality, and user-friendly installation. The decision was influenced by a recommendation from James Morrison, National Key Accounts Manager for Hochiki, who highlighted the advantages of Hochiki's cutting-edge technology and streamlined installation process. heat and smoke detectors The heat and smoke sensors are engineered to deliver swift and precise fire detection The installation at Printworks Belfast encompassed a variety of standard heat and smoke detectors from Hochiki, interconnected to a central fire alarm control panel equipped with a selection of other Hochiki field devices. The heat and smoke sensors are engineered to deliver swift and precise fire detection, ensuring optimal safety for the building's occupants. ease of installation Wesley Allan, Managing Director at 365 Fire Security explained how the Hochiki equipment proved to be an asset in the Printworks Belfast restoration project. He said, "Its ease of installation was a significant advantage, given the complex nature of the building and the need to minimize disruptions during the upgrade works." Wesley Allan adds, "Even though we installed over 500 devices, the process was remarkably smooth thanks to Hochiki's consistent base design. This standardization significantly simplified the installation process and reduced the overall project timeline." reliable and early detection The detectors provide comprehensive fire protection across all five floors, offering reliable and early detection of potential hazards. Moreover, the devices seamlessly integrate with the building's architectural elements, preserving its historic charm, while ensuring state-of-the-art fire safety. The successful installation of Hochiki's fire detection system by 365 Fire Security has fortified Printworks Belfast with a robust and reliable life safety infrastructure. quality and reliability This project exemplifies the effectiveness of Hochiki's technology in a complex, mixed-use building This project exemplifies the effectiveness of Hochiki's technology in a complex, mixed-use building, balancing historical preservation and modern safety standards. Wesley Allan continues, "Despite having no prior experience with Hochiki devices, the Printworks Belfast project has convinced us of their exceptional quality and reliability. Unless specified otherwise, we'll now make Hochiki our first choice for fire detection systems and devices." dependability and effectiveness Consequently, Printworks Belfast is primed for its modern office space role, equipped with a fire safety system that safeguards both the building's heritage and its occupants. The triumph of this installation marks a promising commencement for 365 Fire Security's utilization of Hochiki equipment, underscoring the systems' user-friendliness, dependability, and effectiveness in intricate and demanding environments.
Masterfire Project Managed a Site-Wide Fire Detection & Alarm & Emergency Lighting Upgrade at University Hospital Waterford. Masterfire successfully completed a large-scale upgrade of both the Fire Alarm & Emergency Lighting systems at University Hospital Waterford in early 2021. University Hospital Waterford is a large acute hospital facility with a capacity for 431 inpatients and a further 85-day procedure beds. Fire Alarm System Upgrade The Fire Alarm System upgrade involved the installation of 75 new fire alarm control panel networks and graphic packages, 6050 new fire detection points, and 65 km of fire-rated cable. The Emergency Lighting System upgrade involved the installation of 50 new emergency light control panels, 5200 new emergency luminaires and 47 km of fire rated cable. Masterfire managed this project from design to installation, commission, system handover and continued maintenance. During the project, they consistently met the needs of the live healthcare environment, from complying with infection control measures to protecting patient privacy & dignity and assigning fall back areas.
Fire and Rescue NSW Hazardous Materials crews remain at the scene of yesterday's major fire and chemical emergency in Sydney's west. More than 100 firefighters and 20 fire trucks were confronted by 60-metre-high fireballs at the waste recycling plant in Christies Street, St Marys. Industrial Fire Fallout FRNSW is working with site management, the NSW Environment Protection Agency and Comcare Burning gas bottles and chemicals caused numerous explosions at the height of the blaze, forcing authorities to evacuate workers nearby. Once the fire was contained early last night, firefighters worked through the evening to extinguish persistent hot spots. FRNSW is working with site management, the NSW Environment Protection Agency and Comcare to execute a Hazardous Materials management plan, including monitoring runoff from firefighting efforts. Aerial Threat Assessment FRNSW's Aviation Unit is using Remotely Piloted Aircraft Systems or drones, to provide valuable threat and damage assessments at the scene. FRNSW fire investigators are also at the site to determine the origin and cause of the fire.
Fire safety is one of the most critical paths of industrial operations especially in manufacturing plants. Factories handle a lot of combustible materials, flammable liquids and electrical machinery that can cause fires if not properly managed well. Palladium Safety Solutions completely specialize in providing top tire safety solutions to protect businesses from catastrophic fire hazards. Here in this case study, people can learn everything about how the fire safety solutions prevent a major disaster at a large manufacturing plant. The manufacturing plant and its fire safety challenges The manufacturing plant that will help is the major producer of industrial equipment operating in a 1, 00, 000 square foot facility. The plant houses different production units, including welding solutions, painting booths and chemical storage areas. It employs more than 500 workers and operates 24/7 to meet the high production demands. Fire safety challenges Overload circuits, faulty wiring and overheating machines posed a major fire risk Overload circuits, faulty wiring and overheating machines posed a major fire risk. The plant stored large amounts of chemicals, solvents and gases increasing the likelihood of outbreaks. While the plant fire extinguishers lacked the advanced fire suppression system. The workers were not sufficiently trained in fire safety protocols, which could also lead to slow response in emergencies. The existing smoke detectors were old and unreliable that led to delays in fire detection. Considering all these risks the plant needs a complete fire safety overall to ensure the safety of employees and even prevent damage to infrastructure. Palladium’s safety solutions After conducting a thorough risk assessment, they implemented a comprehensive fire safety plan tailored to the plant’s requirements. They had placed the outdated smoke detectors with modern high sensitivity fire alarm systems. These detectors can quickly identify smoke and also heat changes allowing early warning alerts for plants. They install an automatic fire suppression unit also like sprinkler systems that activate automatically when a file is detected. It helps contain small fires before they spread. Gas based suppression for sensitive areas are really important in areas with electronic equipment. They have used gas based suppression instead of water to prevent damage. To reduce the risk of electrical fires, they inspected and so upgraded faulty wiring and installed circuit Breakers to prevent overloads. Their experts have implemented regular maintenance scheduled for electrical equipment. They conducted fire safety training sessions for all employees covering how to use fire extinguishers correctly and evacuation procedures in case of fire. They can help identify the hazards in the workplace. They have designed a clear fire exit plan and placed visible emergency exit signs throughout the plant. They also organize monthly fire drills to ensure that the workers know how to react swiftly in an emergency. They have introduced safety protocols for handling flammable substances like storing chemicals in fire resistant cabinets and using proper ventilation and chemical storage areas, while implementing a labeling system to identify hazardous materials. how Palladium's solutions prevented disaster? Three months after they implemented a new fire safety solution, the plant faced a real life emergency. One of the welding machines malfunctioned causing a major spark that ignited flammable fumes in the painting booth. The advanced fire alarm system detected the smoke immediately and triggered an alarm Within seconds flames started spreading towards the chemical storage area. The advanced fire alarm system detected the smoke immediately and triggered an alarm. The sprinkler activated and also controlled the flames. In the chemical storage area, the gas based fire suppression system prevented the fire from spreading. Because of the fire safety training, workers responded well. They also used fire extinguishers to control small flames and evacuated safely. Local fire department notified instantly The local fire department was notified instantly and they arrived within just a few minutes, so as to ensure a complete containment. There were no injuries or casualties occurred and there was minimum property damage, as the fire was contained in less than five minutes. Impact of Palladium’s safety solutions The best part about Palladium’s safety solutions is that the employees felt really confident working in a safer environment. The training and drills ensured they knew how to react and agencies. By preventing a major fire the plant saved a lot of damage, legal liabilities and downtime expenses. Palladium’s solutions helped the plant meet all the required fire safety standards and avoid fines or even penalties. With a safer work environment, employees could focus on their work without the stress of fire hazards will stop. Palladium Safety Solutions secure manufacturing plant So above all, Palladium Safety Solutions are completely committed to provide the best fire safety solutions to protect businesses from devastating fire accidents. Their successful intervention at the manufacturing plant completely demonstrates the importance of advanced fire detection suppression employee training and risk assessment. By investing in fire safety, property managers can protect their employees’ assets and operations.
JCB Fire Ltd, a major fire alarm contractor, recently partnered with Hochiki to supply and commission a state-of-the-art fire detection system at Costa Coffee’s brand-new flagship store at Solihull's Touchwood Shopping Center for their long-standing client - Otec Electrical Limited. Costa Coffee, a beloved British coffeehouse chain, has become synonymous with high-quality coffee and a warm, inviting atmosphere. With a wide range of handcrafted beverages, from classic espressos to innovative seasonal drinks, Costa offers something for everyone. Situated in the popular Touchwood Shopping Center, which attracts over 13 million visitors annually, the new flagship Costa required a fire safety system that would meet the demands of this busy retail hub and ensure the safety of all coffee lovers who visited. Hochiki's fire detection devices JCB Fire Ltd selected Hochiki's fire detection devices for their innovative features The Solihull store, a former Foot Locker, needed a complete overhaul to accommodate Costa Coffee's unique brief. This included the integration of a new fire detection system that would interface seamlessly with the existing building's infrastructure, including security and sprinkler systems and meet the company's strict adherence policy to the Disability Discrimination Act (DDA). JCB Fire Ltd selected Hochiki's fire detection devices for their innovative features and because their open protocol capability ensures compatibility with various fire alarm control panels, providing flexibility in system design. Additionally, the devices are easy to install, reducing project timelines, and offer ultra-reliability, minimizing false alarms. Hochiki's ESP range of sensors To meet the stringent safety requirements of the DDA, Hochiki's market-pioneering Audio and Visual alarm devices were also installed. These devices are designed to enhance visibility for individuals with hearing impairments and improve the audibility of fire alarms, ensuring that all occupants can be evacuated quickly and efficiently. Hochiki's ESP range of sensors further simplifies the installation process Hochiki's ESP range of sensors further simplifies the installation process with electronics-free mounting bases and easy addressing. The versatile sensors offer a variety of detection options, including smoke, heat, and multi-criteria detection. Customizable settings, such as adjustable sensitivity and drift compensation, allow for tailored fire protection – perfect for this restaurant spread over two floors. Hochiki’s innovative technology Grant Wheeler, General Manager of JCB Fire, highlighted the benefits of partnering with Hochiki. He emphasized the advanced technology, reduced false alarms, and efficient installation processes that contribute to the overall success of the fire safety project at Costa. Grant Wheeler said, "The successful installation at the Solihull store was completed in less than a week, by our client Otec Electrical demonstrating the effectiveness of our partnership with Hochiki. We were able to combine our expertise with Hochiki’s innovative technology ensuring the safety and security of Costa Coffee's customers and staff in this brand-new store." Fire detection solution Hochiki's ESP range, as demonstrated in this exciting project at Costa Coffee's new outlet, offers a robust and reliable fire detection solution for retail and restaurant environments. By providing advanced features like open protocol capability, easy installation, and customizable settings, Hochiki empowers retail businesses to prioritize safety without compromising esthetics. To learn more about how Hochiki's ESP range can elevate fire safety measures, visit the Hochiki website or contact a local authorized distributor.


Round table discussion
Thermal imaging is an advantageous tool for firefighters on the frontline. As thermal cameras have become more compact and affordable, their availability has expanded, along with their usefulness. We asked our Expert Panel Roundtable: How does thermal imaging serve the needs of firefighters and how is it changing?
New tools and technologies are emerging that augment the efforts of the fire market to prevent and fight fires. Modern firefighting is benefiting from an ongoing sea change in technological capabilities, spanning equipment, electronic components, greater connectivity and firefighter monitoring, to name just a few. We asked our Expert Panel Roundtable: What technologies will have the greatest impact on the fire industry in 2021?
Welcome to our Expert Panel Roundtable, a new feature of TheBigRedGuide.com. We will be asking timely questions about the fire market and seeking out experts in the field to provide responses. Our goal is to promote a useful exchange of information on a variety of topics and to create a forum for discussion of important issues facing the fire service and market. For our first question, we look to the year ahead and ask our panelists: What trends are likely to change the fire market in 2020?
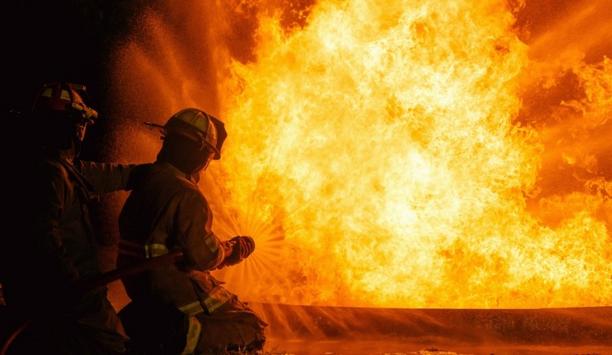
The New Future For Fire Agencies
Download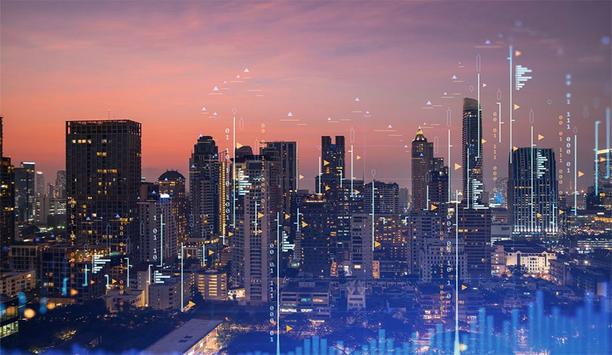
The Eight Key Trends in Fire Detection in 2023
Download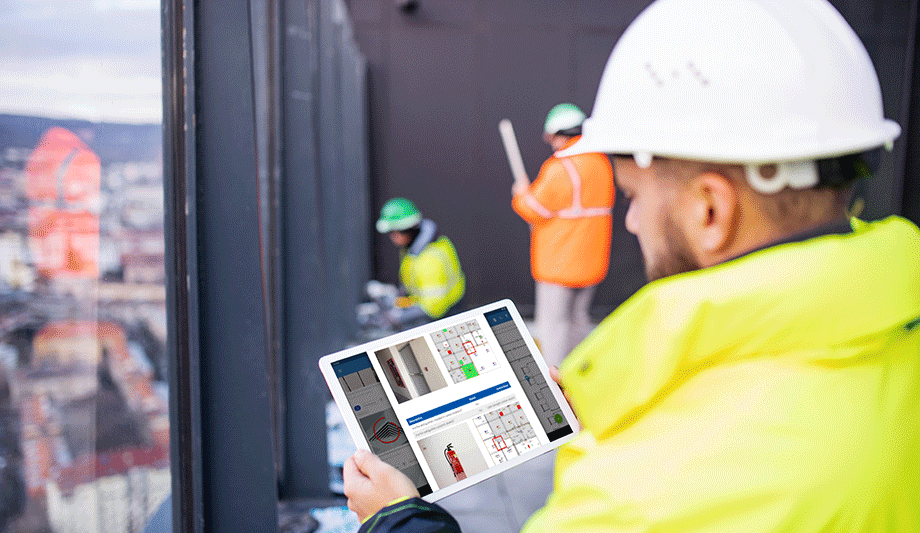
A Digital Platform to Improve Fire Safety Compliance and Inspections
Download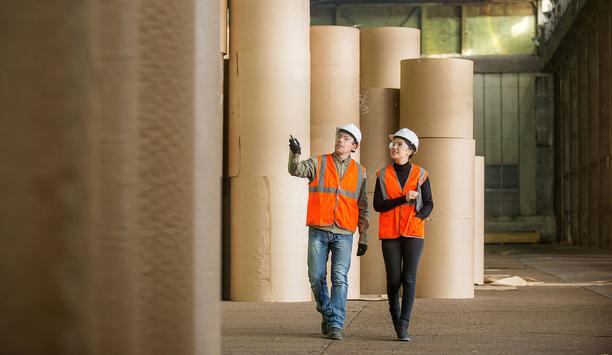
Overcoming the Challenges of Fire Safety in the Paper Industry
Download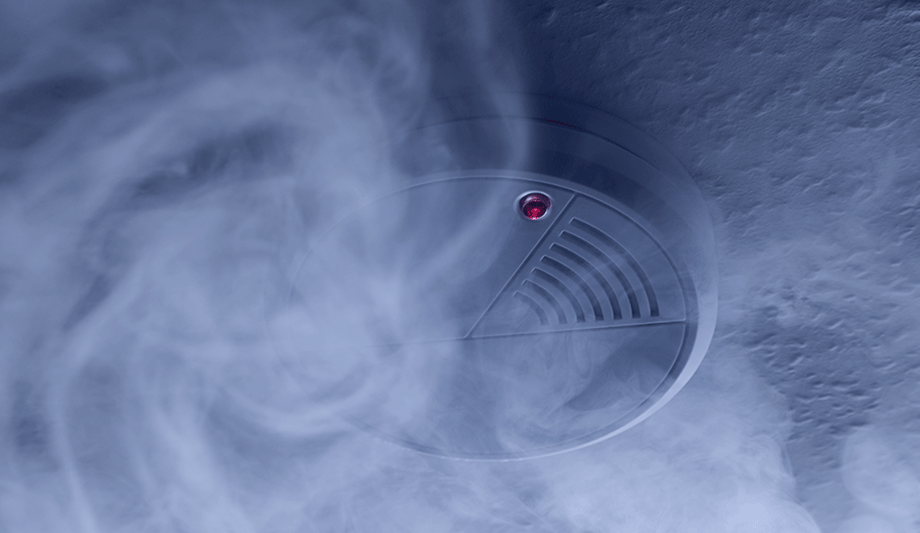
Carbon Monoxide: Creeping Killer Caught In The Act
Download