Det-Tronics Fire Detectors (14)
Browse Fire Detectors
- Make
- Det-Tronics
- Other Det-Tronics products
- Det-Tronics Fire Suppression System Accessories
Detector products updated recently
Detectors - Expert Commentary
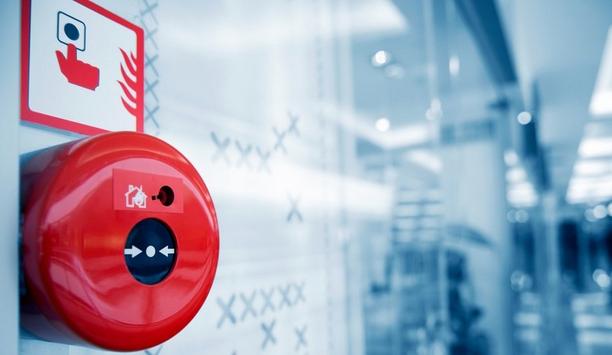
The National Fire Protection Association (NFPA) has developed over 300 codes and standards to support the rapidly changing needs of the fire and life safety industry. NFPA 72, Na...
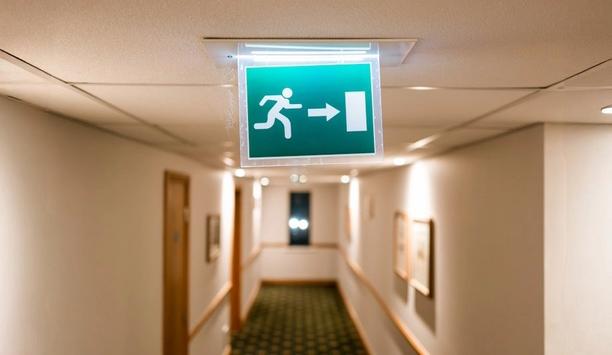
Are people too passive when it comes to fire door safety? Research conducted by the British Woodworking Federation (BWF) in 2022 would suggest so, with a third of the British publi...
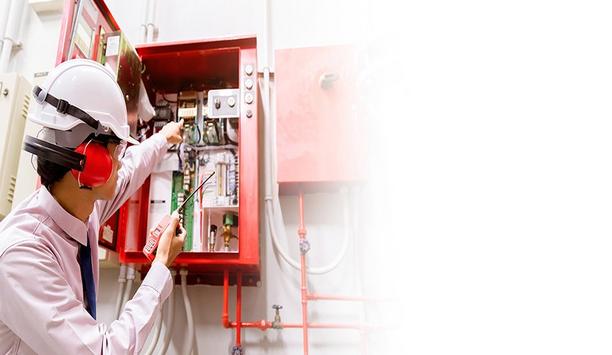
It’s been three years since the National Fire Protection Association (NFPA) published the most recent edition of the wide-ranging standard that spans “the application,...
Latest Detector Electronics Corporation (Det-Tronics) news
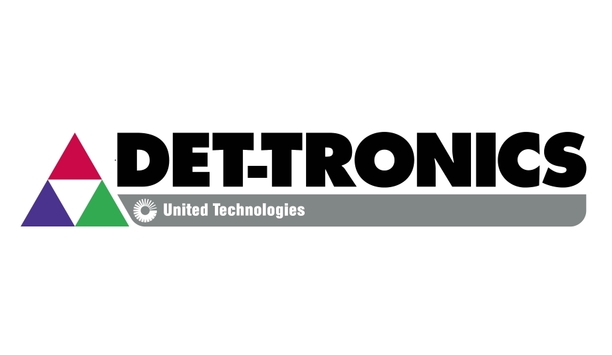
AAR MRO Services supports airline operators with everything from maintenance inspections and equipment upgrades to airframe painting and heavy maintenance for all major aircraft in...
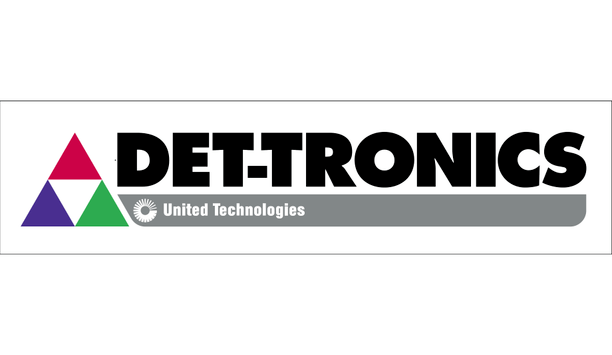
Det-Tronics has introduced a new high-speed deluge module (HSDM) for the Det-Tronics Eagle Quantum Premier (EQP) fire and gas safety controller. The HSDM expands the capability of...
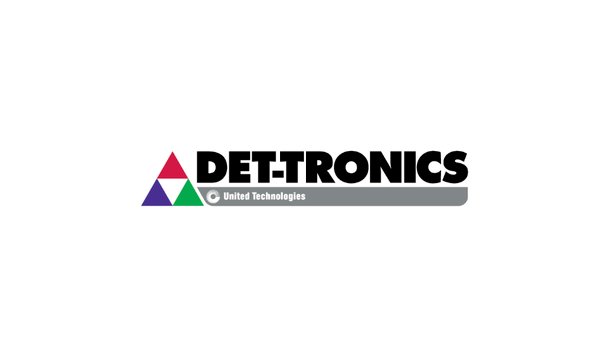
The X3302 multispectrum infrared flame detector (X3302) from Det-Tronics is now third-party approved for the industry’s field-of-view for hydrogen fires, as well as approved...
Trending topic articles
Fire and Rescue NSW (FRNSW) investigators will examine the scene of a major gas fire at a service station last night at Fairfield, in Sydney's south-west. Around 50 firefighters responded to numerous...
Fire and Rescue NSW (FRNSW) crews have extinguished a major factory fire in Sydney's south-west. Just before 4 am this morning, a Triple Zero (000) emergency call alerted firefighters to a plastic pi...
His younger colleagues lovingly call him “the dinosaur,” and after five decades of serving the public, Fire and Rescue NSW (FRNSW) Station Officer Fred Parkhouse, has called ‘time&rs...
Fire and Rescue NSW (FRNSW) crews are at the scene of a helicopter crash in Sydney's south-west. Two people were aboard the single-engine aircraft when it plummeted to the ground at the Bankstown Aer...
Fire and Rescue NSW (FRNSW) crews are working to clear a major spill of combustible liquid at Mascot, in Sydney's inner south. The operation began around 4:30 am when two semi-trailers collided at th...
Fire and Rescue NSW (FRNSW) investigators are working to determine the cause of a fire which has engulfed a factory at Jamisontown, in Sydney's west. More than 40 firefighters and 14 fire trucks were...
Fire and Rescue NSW (FRNSW) crews are battling a large warehouse fire at Five Dock, in Sydney's inner west. Shortly after 3 pm, FRNSW received multiple Triple-Zero (000) calls reporting large volumes...
Fire and Rescue NSW (FRNSW) has determined there was a 12 percent increase in house fires during winter this year, sparking calls for more working smoke alarms in NSW homes. The latest statistics gat...
State Farm® and the National Volunteer Fire Council (NVFC) have teamed up for the second year to support local volunteer fire departments with funding to secure needed equipment to help keep their...
With wildfires overwhelming Los Angeles and dominating headlines across the country, dramatically changing the landscape that people live and work in the wildland-urban interface, there...
Darley, a globally renowned provider of defense, fire, and emergency services equipment, is proud to announce the launch of a new section on its website, darley.com/uncrewed-systems, dedicated exclusi...
Growing fire safety industry organization - Fire Aware aims to change the culture of the built environment sector, by introducing a moral code of conduct via a series of charters designed to influence...
Dräger, the international pioneer in medical and safety technology, has launched a browser-based software solution to optimize daily operations in fire service workshops. Resource and Asse...
Pierce Manufacturing Inc., an Oshkosh Corporation business, is pleased to announce Pierce's authorized dealer, Atlantic Emergency Solutions, has completed a significant expansion of its Charlotte, Nor...
Fire and Rescue NSW (FRNSW) investigators have determined a tobacco pipe sparked a fire at Seven Hills, in Sydney's north-west, which injured two people last night. The blaze broke out at the back of...
Fire and Rescue NSW (FRNSW) investigators will examine the scene of a major gas fire at a service station last night at Fairfield, in Sydney's south-west. Around 50 firefighters responded to numerous...
Fire and Rescue NSW (FRNSW) crews have extinguished a major factory fire in Sydney's south-west. Just before 4 am this morning, a Triple Zero (000) emergency call alerted firefighters to a plastic pi...
His younger colleagues lovingly call him “the dinosaur,” and after five decades of serving the public, Fire and Rescue NSW (FRNSW) Station Officer Fred Parkhouse, has called ‘time&rs...
Fire and Rescue NSW (FRNSW) crews are at the scene of a helicopter crash in Sydney's south-west. Two people were aboard the single-engine aircraft when it plummeted to the ground at the Bankstown Aer...
Fire and Rescue NSW (FRNSW) crews are working to clear a major spill of combustible liquid at Mascot, in Sydney's inner south. The operation began around 4:30 am when two semi-trailers collided at th...
Fire and Rescue NSW (FRNSW) investigators are working to determine the cause of a fire which has engulfed a factory at Jamisontown, in Sydney's west. More than 40 firefighters and 14 fire trucks were...
Fire and Rescue NSW (FRNSW) crews are battling a large warehouse fire at Five Dock, in Sydney's inner west. Shortly after 3 pm, FRNSW received multiple Triple-Zero (000) calls reporting large volumes...
Fire and Rescue NSW (FRNSW) has determined there was a 12 percent increase in house fires during winter this year, sparking calls for more working smoke alarms in NSW homes. The latest statistics gat...
State Farm® and the National Volunteer Fire Council (NVFC) have teamed up for the second year to support local volunteer fire departments with funding to secure needed equipment to help keep their...
With wildfires overwhelming Los Angeles and dominating headlines across the country, dramatically changing the landscape that people live and work in the wildland-urban interface, there...
Darley, a globally renowned provider of defense, fire, and emergency services equipment, is proud to announce the launch of a new section on its website, darley.com/uncrewed-systems, dedicated exclusi...
Growing fire safety industry organization - Fire Aware aims to change the culture of the built environment sector, by introducing a moral code of conduct via a series of charters designed to influence...
Dräger, the international pioneer in medical and safety technology, has launched a browser-based software solution to optimize daily operations in fire service workshops. Resource and Asse...
Pierce Manufacturing Inc., an Oshkosh Corporation business, is pleased to announce Pierce's authorized dealer, Atlantic Emergency Solutions, has completed a significant expansion of its Charlotte, Nor...
Fire and Rescue NSW (FRNSW) investigators have determined a tobacco pipe sparked a fire at Seven Hills, in Sydney's north-west, which injured two people last night. The blaze broke out at the back of...
Fire and Rescue NSW (FRNSW) investigators will examine the scene of a major gas fire at a service station last night at Fairfield, in Sydney's south-west. Around 50 firefighters responded to numerous...
The New Future For Fire Agencies
DownloadThe Eight Key Trends in Fire Detection in 2023
DownloadA Digital Platform to Improve Fire Safety Compliance and Inspections
DownloadOvercoming the Challenges of Fire Safety in the Paper Industry
DownloadCarbon Monoxide: Creeping Killer Caught In The Act
Download