Draeger Thermal Imaging for Fire Fighters (2)
Browse Thermal Imaging for Fire Fighters
- Display
- Standard Resolution
- High Resolution
- Vehicle Charger?
- Yes
- Make
- Draeger
- Other Draeger products
- Draeger Detectors
- Draeger Radios
- Draeger Fire Suppression System Accessories
Thermal Imager products updated recently
Thermal Imagers - Expert Commentary
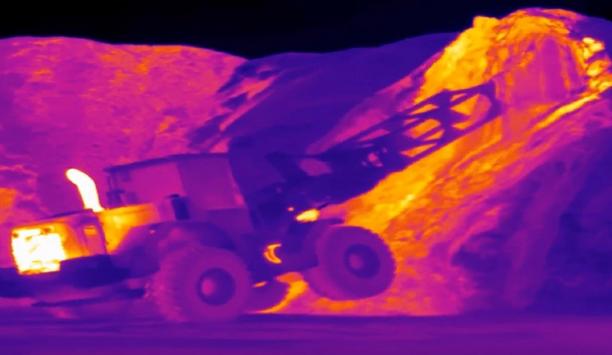
Waste management sites are particularly vulnerable to fires, with hundreds reported every year, just in the UK. The materials stored in a waste heap make them particularly risky e...
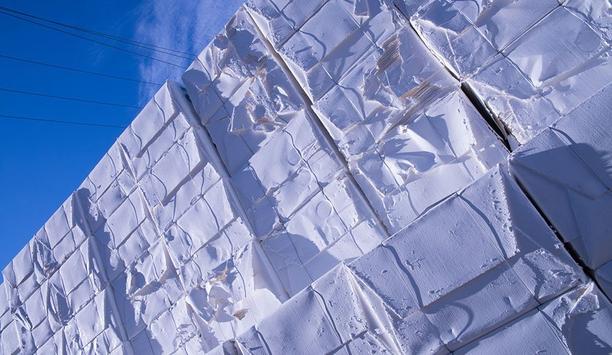
There is a sense in some markets that the paper and pulp industry will decline owing to the digital technologies with which people interact every day. While this might be considere...
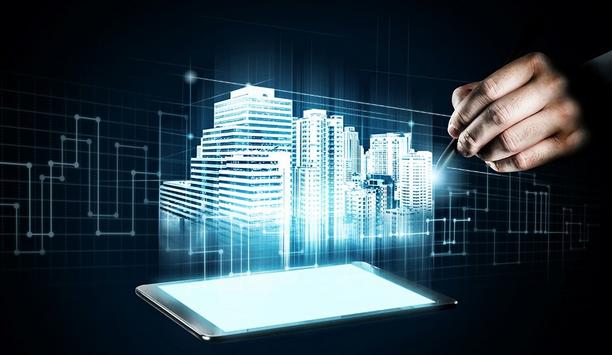
As Grenfell remains a chilling reminder of the importance of fire safety in construction, new digital methods are now being adopted to guarantee the safety of end users. But how is...
Latest Drägerwerk AG & Co. KGaA news

Dräger, the international pioneer in medical and safety technology, has launched a browser-based software solution to optimize daily operations in fire service workshops. ...

Dräger, an international pioneer in the fields of medical and safety technology, has launched the new FPS-COM Voice mask-integrated unit to improve voice firefighter communica...

The Engineered Solutions division of Dräger, an international pioneer in the fields of medical and safety technology, has designed a breathing air panel for Staffordshire Fire...
Trending topic articles
Fire and Rescue NSW (FRNSW) crews are working to clear a major spill of combustible liquid at Mascot, in Sydney's inner south. The operation began around 4:30 am when two semi-trailers collided at th...
Fire and Rescue NSW (FRNSW) investigators are working to determine the cause of a fire which has engulfed a factory at Jamisontown, in Sydney's west. More than 40 firefighters and 14 fire trucks were...
Fire and Rescue NSW (FRNSW) crews are battling a large warehouse fire at Five Dock, in Sydney's inner west. Shortly after 3 pm, FRNSW received multiple Triple-Zero (000) calls reporting large volumes...
Fire and Rescue NSW (FRNSW) has determined there was a 12 percent increase in house fires during winter this year, sparking calls for more working smoke alarms in NSW homes. The latest statistics gat...
Fire and Rescue NSW (FRNSW) crews have saved a home from a large Lithium-Ion battery fire at Warrawee, on Sydney’s upper north shore. A resident was charging the battery used to power a leaf bl...
Darley, a major provider of defense, fire, and emergency services equipment, is proud to announce it has been named one of Crain’s 2025 Fast 50 by Crain’s Chicago Business. This honor re...
Fire and Rescue NSW (FRNSW) crews have successfully completed a strategic hazard reduction burn to protect the headland at North Mona Vale, on Sydney's northern beaches. FRNSW deployed firefighters f...
Johnson Controls marks the one-year anniversary of Autocall as it introduces the brand of proven fire detection systems to the Canadian market. By bringing Autocall to Canada, Johnson Controls is pr...
Dräger, the international pioneer in medical and safety technology, has launched a browser-based software solution to optimize daily operations in fire service workshops. Resource and Asse...
Pierce Manufacturing Inc., an Oshkosh Corporation business, is pleased to announce Pierce's authorized dealer, Atlantic Emergency Solutions, has completed a significant expansion of its Charlotte, Nor...
Fire and Rescue NSW (FRNSW) investigators have determined a tobacco pipe sparked a fire at Seven Hills, in Sydney's north-west, which injured two people last night. The blaze broke out at the back of...
Fire and Rescue NSW (FRNSW) investigators will examine the scene of a major gas fire at a service station last night at Fairfield, in Sydney's south-west. Around 50 firefighters responded to numerous...
Fire and Rescue NSW (FRNSW) crews have extinguished a major factory fire in Sydney's south-west. Just before 4 am this morning, a Triple Zero (000) emergency call alerted firefighters to a plastic pi...
His younger colleagues lovingly call him “the dinosaur,” and after five decades of serving the public, Fire and Rescue NSW (FRNSW) Station Officer Fred Parkhouse, has called ‘time&rs...
Fire and Rescue NSW (FRNSW) crews are at the scene of a helicopter crash in Sydney's south-west. Two people were aboard the single-engine aircraft when it plummeted to the ground at the Bankstown Aer...
Fire and Rescue NSW (FRNSW) crews are working to clear a major spill of combustible liquid at Mascot, in Sydney's inner south. The operation began around 4:30 am when two semi-trailers collided at th...
Fire and Rescue NSW (FRNSW) investigators are working to determine the cause of a fire which has engulfed a factory at Jamisontown, in Sydney's west. More than 40 firefighters and 14 fire trucks were...
Fire and Rescue NSW (FRNSW) crews are battling a large warehouse fire at Five Dock, in Sydney's inner west. Shortly after 3 pm, FRNSW received multiple Triple-Zero (000) calls reporting large volumes...
Fire and Rescue NSW (FRNSW) has determined there was a 12 percent increase in house fires during winter this year, sparking calls for more working smoke alarms in NSW homes. The latest statistics gat...
Fire and Rescue NSW (FRNSW) crews have saved a home from a large Lithium-Ion battery fire at Warrawee, on Sydney’s upper north shore. A resident was charging the battery used to power a leaf bl...
Darley, a major provider of defense, fire, and emergency services equipment, is proud to announce it has been named one of Crain’s 2025 Fast 50 by Crain’s Chicago Business. This honor re...
Fire and Rescue NSW (FRNSW) crews have successfully completed a strategic hazard reduction burn to protect the headland at North Mona Vale, on Sydney's northern beaches. FRNSW deployed firefighters f...
Johnson Controls marks the one-year anniversary of Autocall as it introduces the brand of proven fire detection systems to the Canadian market. By bringing Autocall to Canada, Johnson Controls is pr...
Dräger, the international pioneer in medical and safety technology, has launched a browser-based software solution to optimize daily operations in fire service workshops. Resource and Asse...
Pierce Manufacturing Inc., an Oshkosh Corporation business, is pleased to announce Pierce's authorized dealer, Atlantic Emergency Solutions, has completed a significant expansion of its Charlotte, Nor...
Fire and Rescue NSW (FRNSW) investigators have determined a tobacco pipe sparked a fire at Seven Hills, in Sydney's north-west, which injured two people last night. The blaze broke out at the back of...
Fire and Rescue NSW (FRNSW) investigators will examine the scene of a major gas fire at a service station last night at Fairfield, in Sydney's south-west. Around 50 firefighters responded to numerous...
Fire and Rescue NSW (FRNSW) crews have extinguished a major factory fire in Sydney's south-west. Just before 4 am this morning, a Triple Zero (000) emergency call alerted firefighters to a plastic pi...
His younger colleagues lovingly call him “the dinosaur,” and after five decades of serving the public, Fire and Rescue NSW (FRNSW) Station Officer Fred Parkhouse, has called ‘time&rs...
Fire and Rescue NSW (FRNSW) crews are at the scene of a helicopter crash in Sydney's south-west. Two people were aboard the single-engine aircraft when it plummeted to the ground at the Bankstown Aer...
Fire and Rescue NSW (FRNSW) crews are working to clear a major spill of combustible liquid at Mascot, in Sydney's inner south. The operation began around 4:30 am when two semi-trailers collided at th...
The New Future For Fire Agencies
DownloadThe Eight Key Trends in Fire Detection in 2023
DownloadA Digital Platform to Improve Fire Safety Compliance and Inspections
DownloadOvercoming the Challenges of Fire Safety in the Paper Industry
DownloadCarbon Monoxide: Creeping Killer Caught In The Act
Download