Draeger Fire Detectors (27)
Browse Fire Detectors
- Make
- Draeger
- Other Draeger products
- Draeger Radios
- Draeger Fire Suppression System Accessories
- Draeger Thermal Imagers
Detector products updated recently
Detectors - Expert Commentary
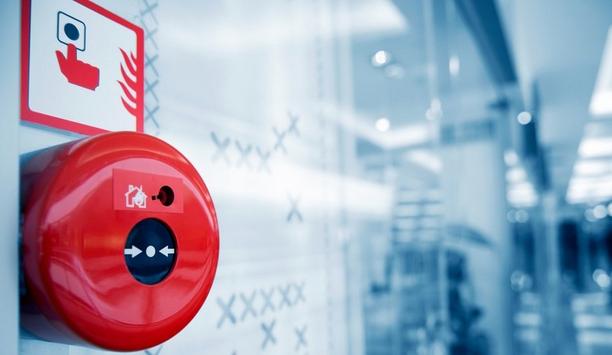
The National Fire Protection Association (NFPA) has developed over 300 codes and standards to support the rapidly changing needs of the fire and life safety industry. NFPA 72, Na...
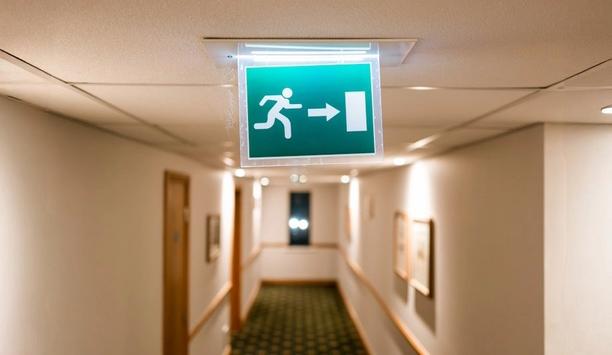
Are people too passive when it comes to fire door safety? Research conducted by the British Woodworking Federation (BWF) in 2022 would suggest so, with a third of the British publi...
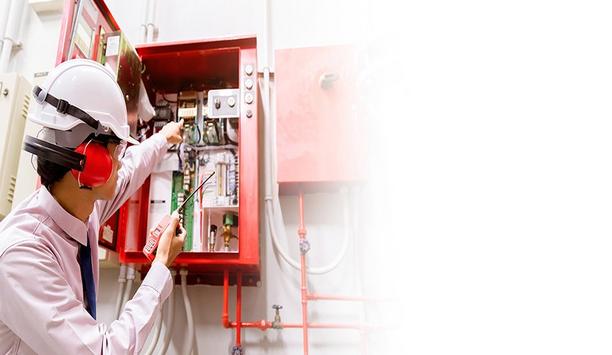
It’s been three years since the National Fire Protection Association (NFPA) published the most recent edition of the wide-ranging standard that spans “the application,...
Latest Drägerwerk AG & Co. KGaA news

Dräger, an international pioneer in the fields of medical and safety technology, will showcase a range of systems designed to protect fire and rescue and police personnel duri...

Dräger, the international pioneer in medical and safety technology, has launched a browser-based software solution to optimize daily operations in fire service workshops. ...

Dräger, an international pioneer in the fields of medical and safety technology, has launched the new FPS-COM Voice mask-integrated unit to improve voice firefighter communica...
Trending topic articles
Fire and Rescue NSW (FRNSW) is further encouraging respectful and honest conversations and the sharing of Traditional Knowledge by opening a Yarning Circle at its training center at Orchard Hills, in...
Responding to reports regarding culture in the fire and rescue service, the National Fire Chiefs Council (NFCC) has reiterated that the behaviors outlined are wholly unacceptable, making it clear ther...
A South Yorkshire recruitment campaign aims to change perceptions of women in the fire service. South Yorkshire Fire & Rescue’s ‘A Firefighter Is A Firefighter’ campaign include...
The Fire Standards Board (FSB) is delighted to announce the launch of two new Fire Standards - Fire Control and Communications & Engagement. The development of the Fire Control Standard was drive...
Gavin Skelly, CEO of growing fire safety industry body - Fire Aware, spoke of the moral and behavioral changes in culture needed to improve standards at the Scotland Housing Leaders’ Summit. He...
Using the highest-rated fire performance cables will help firefighters in the event of a fire in some of the largest new buildings being developed, says pioneering cable supplier AEI Cables. AEI Cabl...
Rescue Intellitech, a pioneering provider of innovative cleaning solutions for the fire and rescue industry, is set to unveil its latest innovation in firefighter PPE care, with the launch of a new li...
Secutech Vietnam 2025 came to a close on 16 August at the Saigon Exhibition and Convention Centre (SECC), after bringing together key stakeholders and buyers from across Vietnam’s security...
WAGNER Group GmbH has once again been awarded for its research and development work. In a decision dated August 11, 2025, the Research Allowance Certification Authority (BSFZ) confirmed the eligibili...
Orr Protection, a provider of mission-critical fire protection solutions, has acquired all of the business assets of Compass Fire Protection, LLC, based in the Seattle, Washington area. The acquisit...
Hochiki Europe, a global pioneer in life safety solutions, has partnered with VOLT EHF, a specialist in electrical and fire alarm systems, to install a comprehensive and scalable fire detection system...
Whether it’s the end of the day or end of term, when schools close, it’s not unusual to see children and staff alike scrambling out the doors as they head for a much needed period of relax...
Sensor solutions provider HENSOLDT will present its latest technological advancements at DSEI 2025 in London from 9 to 12 September 2025. One of HENSOLDT's core competencies is the active and passive...
New Government data of fire and rescue service incidents analyzed by HETAS for Chimney Fire Safety Week (CFSW), reveals that Devon and Somerset Fire and Rescue Service responded to 181 chimney fires o...
Fire and Rescue NSW (FRNSW) investigators are now at the scene of a house fire, which has claimed the lives of two people in Sydney's south-west. Neighbors phoned Triple-Zero (000) around 6:45 am as...
Fire and Rescue NSW (FRNSW) is further encouraging respectful and honest conversations and the sharing of Traditional Knowledge by opening a Yarning Circle at its training center at Orchard Hills, in...
Responding to reports regarding culture in the fire and rescue service, the National Fire Chiefs Council (NFCC) has reiterated that the behaviors outlined are wholly unacceptable, making it clear ther...
A South Yorkshire recruitment campaign aims to change perceptions of women in the fire service. South Yorkshire Fire & Rescue’s ‘A Firefighter Is A Firefighter’ campaign include...
The Fire Standards Board (FSB) is delighted to announce the launch of two new Fire Standards - Fire Control and Communications & Engagement. The development of the Fire Control Standard was drive...
Gavin Skelly, CEO of growing fire safety industry body - Fire Aware, spoke of the moral and behavioral changes in culture needed to improve standards at the Scotland Housing Leaders’ Summit. He...
Using the highest-rated fire performance cables will help firefighters in the event of a fire in some of the largest new buildings being developed, says pioneering cable supplier AEI Cables. AEI Cabl...
Rescue Intellitech, a pioneering provider of innovative cleaning solutions for the fire and rescue industry, is set to unveil its latest innovation in firefighter PPE care, with the launch of a new li...
Secutech Vietnam 2025 came to a close on 16 August at the Saigon Exhibition and Convention Centre (SECC), after bringing together key stakeholders and buyers from across Vietnam’s security...
WAGNER Group GmbH has once again been awarded for its research and development work. In a decision dated August 11, 2025, the Research Allowance Certification Authority (BSFZ) confirmed the eligibili...
Orr Protection, a provider of mission-critical fire protection solutions, has acquired all of the business assets of Compass Fire Protection, LLC, based in the Seattle, Washington area. The acquisit...
Hochiki Europe, a global pioneer in life safety solutions, has partnered with VOLT EHF, a specialist in electrical and fire alarm systems, to install a comprehensive and scalable fire detection system...
Whether it’s the end of the day or end of term, when schools close, it’s not unusual to see children and staff alike scrambling out the doors as they head for a much needed period of relax...
Sensor solutions provider HENSOLDT will present its latest technological advancements at DSEI 2025 in London from 9 to 12 September 2025. One of HENSOLDT's core competencies is the active and passive...
New Government data of fire and rescue service incidents analyzed by HETAS for Chimney Fire Safety Week (CFSW), reveals that Devon and Somerset Fire and Rescue Service responded to 181 chimney fires o...
Fire and Rescue NSW (FRNSW) investigators are now at the scene of a house fire, which has claimed the lives of two people in Sydney's south-west. Neighbors phoned Triple-Zero (000) around 6:45 am as...
Fire and Rescue NSW (FRNSW) is further encouraging respectful and honest conversations and the sharing of Traditional Knowledge by opening a Yarning Circle at its training center at Orchard Hills, in...
The New Future For Fire Agencies
DownloadThe Eight Key Trends in Fire Detection in 2023
DownloadA Digital Platform to Improve Fire Safety Compliance and Inspections
DownloadOvercoming the Challenges of Fire Safety in the Paper Industry
DownloadCarbon Monoxide: Creeping Killer Caught In The Act
Download