Chubb FIRE RESCUE ACESSORIES (1)
Browse FIRE RESCUE ACESSORIES
Rescue/RIT Accessories products updated recently
Rescue/RIT Accessories - Expert Commentary
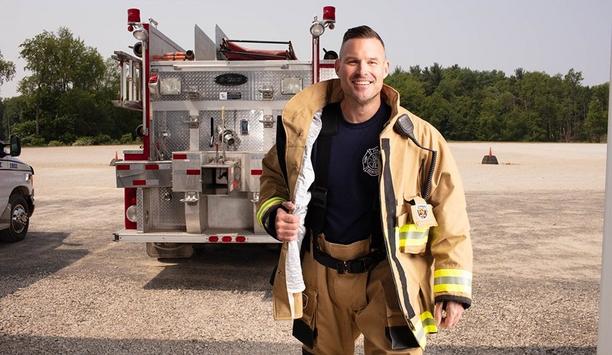
For firefighters, sleep is a valuable commodity. But duty often calls no matter what the clock says. Sleep deprivation Indeed, sleep deprivation is a common challenge...
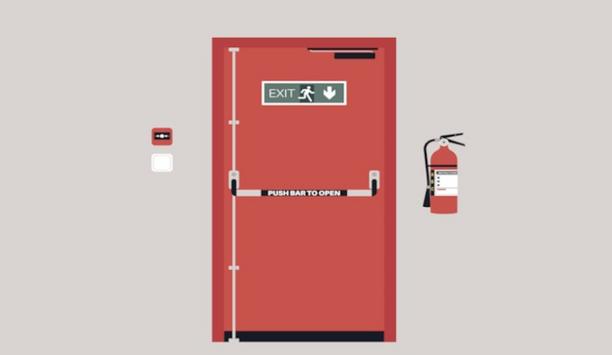
Sue Corrick of Allegion UK explores the evolution of panic and emergency exit hardware, examining the specification and installation points that decision-makers must consider throu...
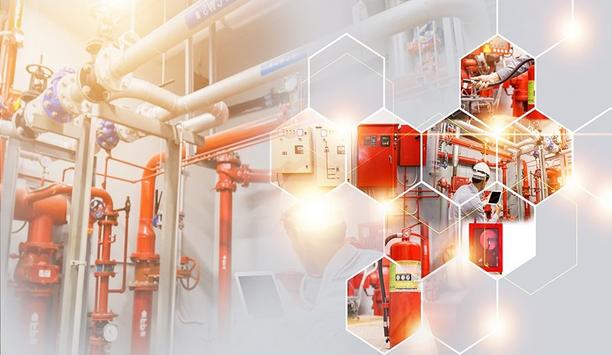
In the six years since the tragic Grenfell Tower disaster, the construction industry's approach to fire safety has faced rigorous examination, and sparked a series of legislative c...
Latest Chubb Fire & Security news
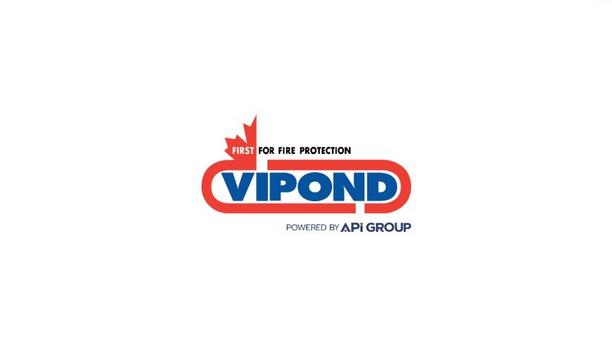
Chubb, one of the major providers of fire safety and security solutions, has announced the successful integration of Vipond Fire Protection Ltd to Chubb Fire and Security Ltd in th...
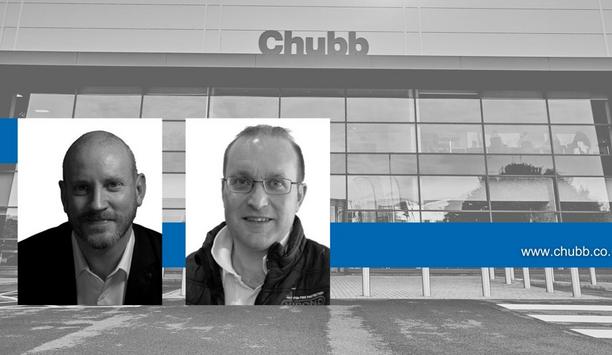
Chubb, one of the renowned providers of fire safety and security solutions, has announced the successful integration of ownership and operational responsibilities of Vipond Fire Pr...
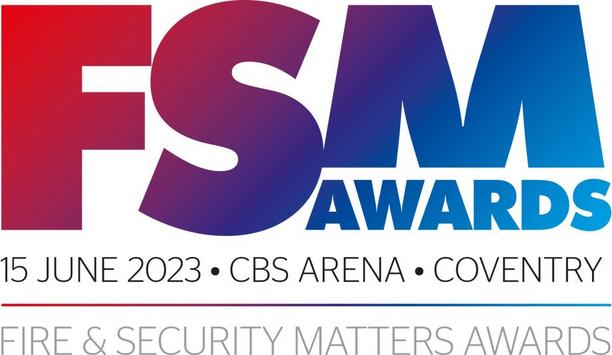
The official awards of publications Fire Safety Matters and Security Matters, the "FSM Awards," took place yesterday evening at the Coventry Building Society Arena. Established to...