Chubb Fire Detectors (46)
Browse Fire Detectors
- Make
- Chubb
- Other Chubb products
- Chubb Fire Sprinklers
- Chubb Warning Lights & Sirens
- Chubb Fire Suppression System Accessories
Detector products updated recently
Detectors - Expert Commentary
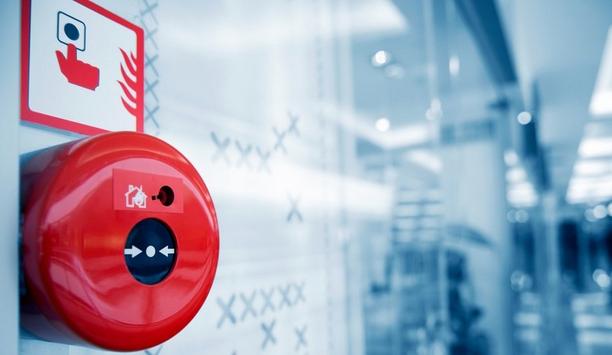
The National Fire Protection Association (NFPA) has developed over 300 codes and standards to support the rapidly changing needs of the fire and life safety industry. NFPA 72, Na...
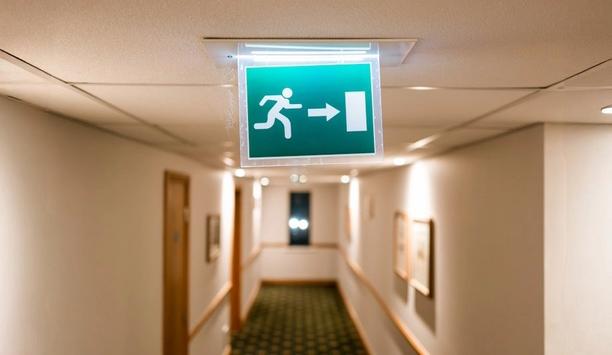
Are people too passive when it comes to fire door safety? Research conducted by the British Woodworking Federation (BWF) in 2022 would suggest so, with a third of the British publi...
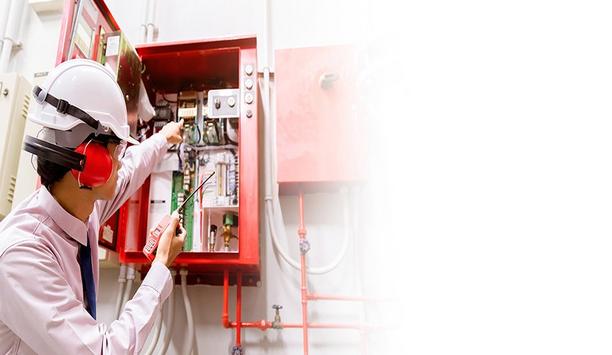
It’s been three years since the National Fire Protection Association (NFPA) published the most recent edition of the wide-ranging standard that spans “the application,...
Latest Chubb Fire & Security news

Renowned fire and life safety solutions manufacturer, Advanced, has won an award at the 2025 Fire & Security Matters (FSM) Awards, recognizing its achievements in fire safety,...
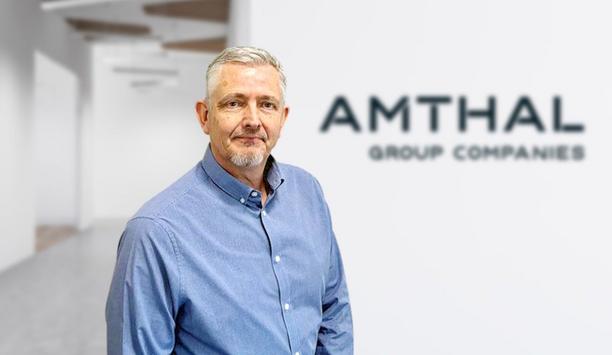
Amthal Group Companies has appointed Richard Parker as its new Group Head of Sales. With over three decades of experience in the fire and security industry, Richard brings a wealth...
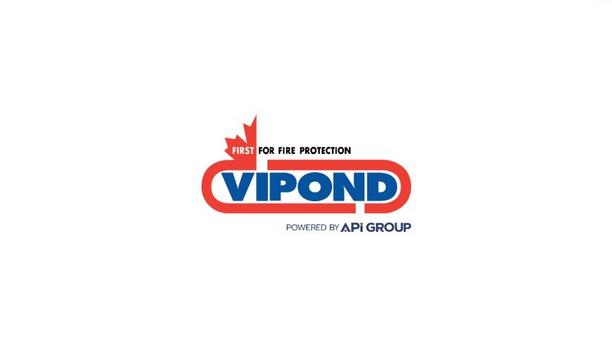
Chubb, one of the major providers of fire safety and security solutions, has announced the successful integration of Vipond Fire Protection Ltd to Chubb Fire and Security Ltd in th...
Trending topic articles
State Farm® and the National Volunteer Fire Council (NVFC) have teamed up for the second year to support local volunteer fire departments with funding to secure needed equipment to help keep their...
With wildfires overwhelming Los Angeles and dominating headlines across the country, dramatically changing the landscape that people live and work in the wildland-urban interface, there...
Darley, a globally renowned provider of defense, fire, and emergency services equipment, is proud to announce the launch of a new section on its website, darley.com/uncrewed-systems, dedicated exclusi...
Growing fire safety industry organization - Fire Aware aims to change the culture of the built environment sector, by introducing a moral code of conduct via a series of charters designed to influence...
Dräger, the international pioneer in medical and safety technology, has launched a browser-based software solution to optimize daily operations in fire service workshops. Resource and Asse...
Pierce Manufacturing Inc., an Oshkosh Corporation business, is pleased to announce Pierce's authorized dealer, Atlantic Emergency Solutions, has completed a significant expansion of its Charlotte, Nor...
Fire and Rescue NSW (FRNSW) investigators have determined a tobacco pipe sparked a fire at Seven Hills, in Sydney's north-west, which injured two people last night. The blaze broke out at the back of...
Fire and Rescue NSW (FRNSW) investigators will examine the scene of a major gas fire at a service station last night at Fairfield, in Sydney's south-west. Around 50 firefighters responded to numerous...
The National Fire Protection Association (NFPA) released findings from its third annual industry survey conducted at the NFPA 2025 Conference & Expo, the premier conference for fire, electrical, a...
A fire door is designed to stop fire and smoke from spreading, giving people time to escape and protecting property. It looks similar to a regular door but is built and tested as part of a complete sy...
Fire and Rescue NSW (FRNSW) crews have rescued a Pomeranian precariously perched on the side of an apartment building at Wentworth Point, in Sydney's west. Firefighters were called around 9:45 last n...
Senior firefighters have expressed concern over a sharp rise in residential fires in New South Wales this winter, urging the public to end the complacency over household smoke alarms. There were 337...
The bravery and dedication of 80 firefighters from Newcastle and Lake Macquarie will be formally recognized tonight at a special Fire and Rescue NSW (FRNSW) awards ceremony. Firefighters, from a rang...
Fire and Rescue NSW (FRNSW) crews have converged on Merriwa, in the upper Hunter, this week to doorknock the entire town with winter fire safety advice. It is the first proactive blitz of its kind in...
Dräger, an international pioneer in the fields of medical and safety technology, will showcase a range of systems designed to protect fire and rescue and police personnel during a wide variety of...
State Farm® and the National Volunteer Fire Council (NVFC) have teamed up for the second year to support local volunteer fire departments with funding to secure needed equipment to help keep their...
With wildfires overwhelming Los Angeles and dominating headlines across the country, dramatically changing the landscape that people live and work in the wildland-urban interface, there...
Darley, a globally renowned provider of defense, fire, and emergency services equipment, is proud to announce the launch of a new section on its website, darley.com/uncrewed-systems, dedicated exclusi...
Growing fire safety industry organization - Fire Aware aims to change the culture of the built environment sector, by introducing a moral code of conduct via a series of charters designed to influence...
Dräger, the international pioneer in medical and safety technology, has launched a browser-based software solution to optimize daily operations in fire service workshops. Resource and Asse...
Pierce Manufacturing Inc., an Oshkosh Corporation business, is pleased to announce Pierce's authorized dealer, Atlantic Emergency Solutions, has completed a significant expansion of its Charlotte, Nor...
Fire and Rescue NSW (FRNSW) investigators have determined a tobacco pipe sparked a fire at Seven Hills, in Sydney's north-west, which injured two people last night. The blaze broke out at the back of...
Fire and Rescue NSW (FRNSW) investigators will examine the scene of a major gas fire at a service station last night at Fairfield, in Sydney's south-west. Around 50 firefighters responded to numerous...
The National Fire Protection Association (NFPA) released findings from its third annual industry survey conducted at the NFPA 2025 Conference & Expo, the premier conference for fire, electrical, a...
A fire door is designed to stop fire and smoke from spreading, giving people time to escape and protecting property. It looks similar to a regular door but is built and tested as part of a complete sy...
Fire and Rescue NSW (FRNSW) crews have rescued a Pomeranian precariously perched on the side of an apartment building at Wentworth Point, in Sydney's west. Firefighters were called around 9:45 last n...
Senior firefighters have expressed concern over a sharp rise in residential fires in New South Wales this winter, urging the public to end the complacency over household smoke alarms. There were 337...
The bravery and dedication of 80 firefighters from Newcastle and Lake Macquarie will be formally recognized tonight at a special Fire and Rescue NSW (FRNSW) awards ceremony. Firefighters, from a rang...
Fire and Rescue NSW (FRNSW) crews have converged on Merriwa, in the upper Hunter, this week to doorknock the entire town with winter fire safety advice. It is the first proactive blitz of its kind in...
Dräger, an international pioneer in the fields of medical and safety technology, will showcase a range of systems designed to protect fire and rescue and police personnel during a wide variety of...
State Farm® and the National Volunteer Fire Council (NVFC) have teamed up for the second year to support local volunteer fire departments with funding to secure needed equipment to help keep their...
The New Future For Fire Agencies
DownloadThe Eight Key Trends in Fire Detection in 2023
DownloadA Digital Platform to Improve Fire Safety Compliance and Inspections
DownloadOvercoming the Challenges of Fire Safety in the Paper Industry
DownloadCarbon Monoxide: Creeping Killer Caught In The Act
Download