Draeger UK Fire Protection Suits (2)
Browse Fire Protection Suits
- Make
- Draeger UK
Protective Suit products updated recently
Protective Suits - Expert Commentary
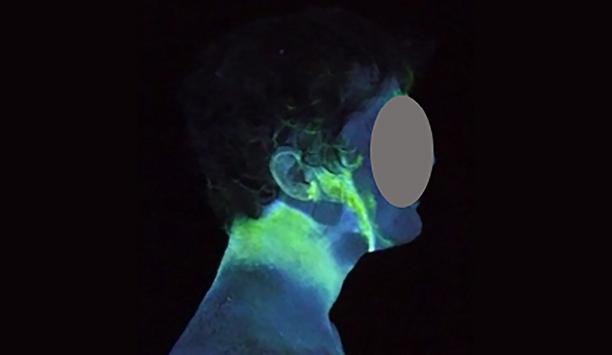
Last year was the largest wildfire season recorded in California in modern history, with six of the top 20 largest wildfires in the state, according to the California Department of...
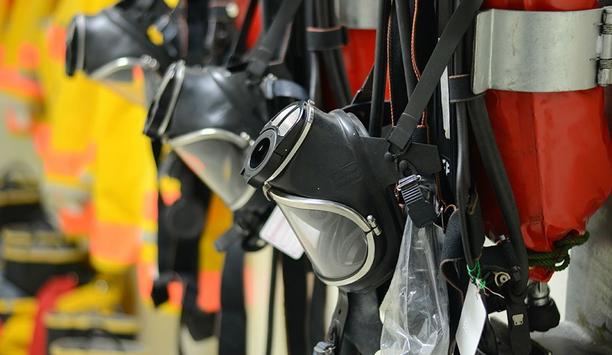
Fire conditions and extrication events that firefighters arrive at today are very different from the conditions faced years ago. According to research at Underwriter Laboratories (...
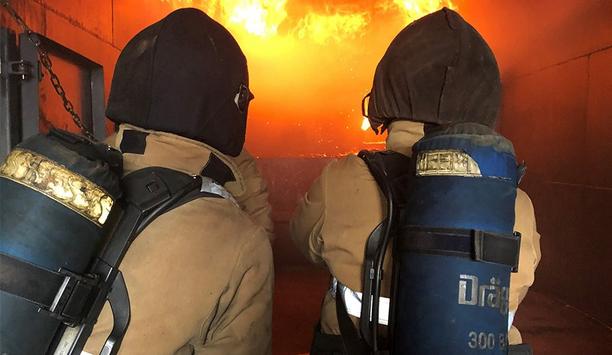
The importance of firefighter health has received increased media attention in recent times, and rightly so. Following Covid-19 more emphasis is now being placed on...
Latest Draeger Safety UK Limited news
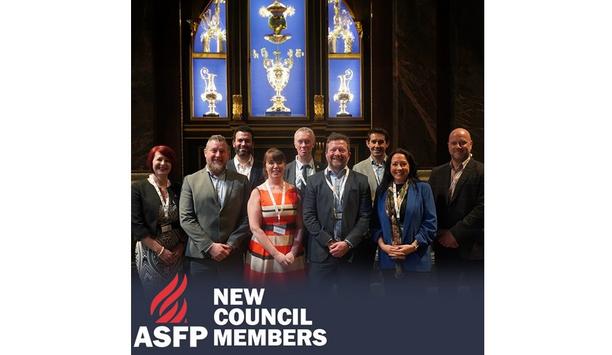
The Association for Specialist Fire Protection (ASFP) appointed its new Council at its 2024 Annual General Meeting (AGM) at Drapers’ Hall, in London, UK, on 11 April, 2024.&n...
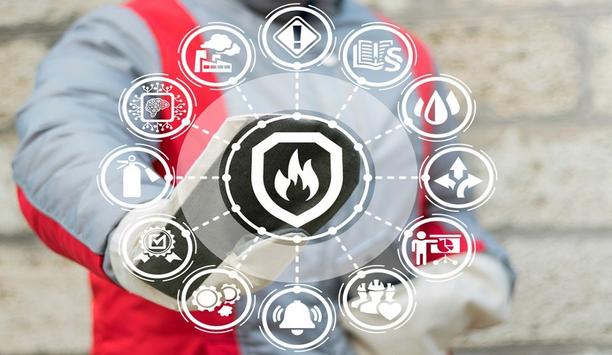
Fostering fire safety is a basic principle, but one that suggests many different approaches and technologies. Best practices and greater innovation can play a role to ensure variou...
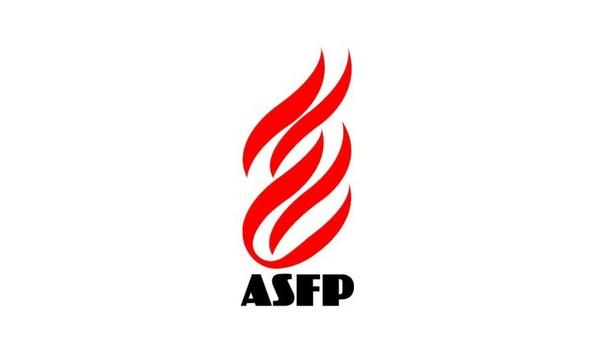
The Association for Specialist Fire Protection (ASFP) will once again be hosting the ASFP Pavilion on stand FI1224 at Firex International at London Excel from 17-19 May....
Trending topic articles
Fire and Rescue NSW (FRNSW) crews are working to clear a major spill of combustible liquid at Mascot, in Sydney's inner south. The operation began around 4:30 am when two semi-trailers collided at th...
Fire and Rescue NSW (FRNSW) investigators are working to determine the cause of a fire which has engulfed a factory at Jamisontown, in Sydney's west. More than 40 firefighters and 14 fire trucks were...
Fire and Rescue NSW (FRNSW) crews are battling a large warehouse fire at Five Dock, in Sydney's inner west. Shortly after 3 pm, FRNSW received multiple Triple-Zero (000) calls reporting large volumes...
Fire and Rescue NSW (FRNSW) has determined there was a 12 percent increase in house fires during winter this year, sparking calls for more working smoke alarms in NSW homes. The latest statistics gat...
Fire and Rescue NSW (FRNSW) crews have saved a home from a large Lithium-Ion battery fire at Warrawee, on Sydney’s upper north shore. A resident was charging the battery used to power a leaf bl...
Darley, a major provider of defense, fire, and emergency services equipment, is proud to announce it has been named one of Crain’s 2025 Fast 50 by Crain’s Chicago Business. This honor re...
Fire and Rescue NSW (FRNSW) crews have successfully completed a strategic hazard reduction burn to protect the headland at North Mona Vale, on Sydney's northern beaches. FRNSW deployed firefighters f...
Johnson Controls marks the one-year anniversary of Autocall as it introduces the brand of proven fire detection systems to the Canadian market. By bringing Autocall to Canada, Johnson Controls is pr...
Dräger, the international pioneer in medical and safety technology, has launched a browser-based software solution to optimize daily operations in fire service workshops. Resource and Asse...
Pierce Manufacturing Inc., an Oshkosh Corporation business, is pleased to announce Pierce's authorized dealer, Atlantic Emergency Solutions, has completed a significant expansion of its Charlotte, Nor...
Fire and Rescue NSW (FRNSW) investigators have determined a tobacco pipe sparked a fire at Seven Hills, in Sydney's north-west, which injured two people last night. The blaze broke out at the back of...
Fire and Rescue NSW (FRNSW) investigators will examine the scene of a major gas fire at a service station last night at Fairfield, in Sydney's south-west. Around 50 firefighters responded to numerous...
Fire and Rescue NSW (FRNSW) crews have extinguished a major factory fire in Sydney's south-west. Just before 4 am this morning, a Triple Zero (000) emergency call alerted firefighters to a plastic pi...
His younger colleagues lovingly call him “the dinosaur,” and after five decades of serving the public, Fire and Rescue NSW (FRNSW) Station Officer Fred Parkhouse, has called ‘time&rs...
Fire and Rescue NSW (FRNSW) crews are at the scene of a helicopter crash in Sydney's south-west. Two people were aboard the single-engine aircraft when it plummeted to the ground at the Bankstown Aer...
Fire and Rescue NSW (FRNSW) crews are working to clear a major spill of combustible liquid at Mascot, in Sydney's inner south. The operation began around 4:30 am when two semi-trailers collided at th...
Fire and Rescue NSW (FRNSW) investigators are working to determine the cause of a fire which has engulfed a factory at Jamisontown, in Sydney's west. More than 40 firefighters and 14 fire trucks were...
Fire and Rescue NSW (FRNSW) crews are battling a large warehouse fire at Five Dock, in Sydney's inner west. Shortly after 3 pm, FRNSW received multiple Triple-Zero (000) calls reporting large volumes...
Fire and Rescue NSW (FRNSW) has determined there was a 12 percent increase in house fires during winter this year, sparking calls for more working smoke alarms in NSW homes. The latest statistics gat...
Fire and Rescue NSW (FRNSW) crews have saved a home from a large Lithium-Ion battery fire at Warrawee, on Sydney’s upper north shore. A resident was charging the battery used to power a leaf bl...
Darley, a major provider of defense, fire, and emergency services equipment, is proud to announce it has been named one of Crain’s 2025 Fast 50 by Crain’s Chicago Business. This honor re...
Fire and Rescue NSW (FRNSW) crews have successfully completed a strategic hazard reduction burn to protect the headland at North Mona Vale, on Sydney's northern beaches. FRNSW deployed firefighters f...
Johnson Controls marks the one-year anniversary of Autocall as it introduces the brand of proven fire detection systems to the Canadian market. By bringing Autocall to Canada, Johnson Controls is pr...
Dräger, the international pioneer in medical and safety technology, has launched a browser-based software solution to optimize daily operations in fire service workshops. Resource and Asse...
Pierce Manufacturing Inc., an Oshkosh Corporation business, is pleased to announce Pierce's authorized dealer, Atlantic Emergency Solutions, has completed a significant expansion of its Charlotte, Nor...
Fire and Rescue NSW (FRNSW) investigators have determined a tobacco pipe sparked a fire at Seven Hills, in Sydney's north-west, which injured two people last night. The blaze broke out at the back of...
Fire and Rescue NSW (FRNSW) investigators will examine the scene of a major gas fire at a service station last night at Fairfield, in Sydney's south-west. Around 50 firefighters responded to numerous...
Fire and Rescue NSW (FRNSW) crews have extinguished a major factory fire in Sydney's south-west. Just before 4 am this morning, a Triple Zero (000) emergency call alerted firefighters to a plastic pi...
His younger colleagues lovingly call him “the dinosaur,” and after five decades of serving the public, Fire and Rescue NSW (FRNSW) Station Officer Fred Parkhouse, has called ‘time&rs...
Fire and Rescue NSW (FRNSW) crews are at the scene of a helicopter crash in Sydney's south-west. Two people were aboard the single-engine aircraft when it plummeted to the ground at the Bankstown Aer...
Fire and Rescue NSW (FRNSW) crews are working to clear a major spill of combustible liquid at Mascot, in Sydney's inner south. The operation began around 4:30 am when two semi-trailers collided at th...
The New Future For Fire Agencies
DownloadThe Eight Key Trends in Fire Detection in 2023
DownloadA Digital Platform to Improve Fire Safety Compliance and Inspections
DownloadOvercoming the Challenges of Fire Safety in the Paper Industry
DownloadCarbon Monoxide: Creeping Killer Caught In The Act
Download