Rosenbauer FIRE HOSE REELS (1)
Browse FIRE HOSE REELS
- Hose Type
- Water
- Hydraulic Fluid
- Air
- Oil
- Grease
- Make
- Rosenbauer
- Other Rosenbauer products
- Rosenbauer Vehicles
- Rosenbauer Boots
- Rosenbauer Pumps
- Rosenbauer Helmets
- Rosenbauer Nozzles
Hose Reel products updated recently
Hose Reels - Expert Commentary
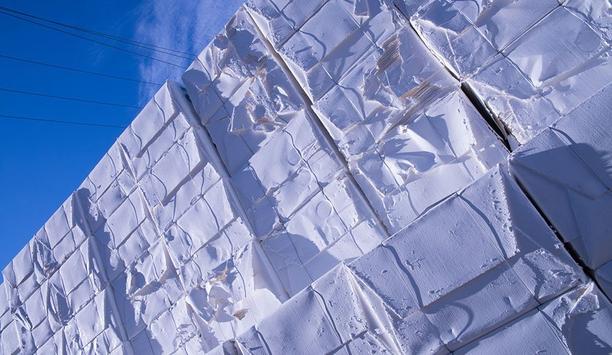
There is a sense in some markets that the paper and pulp industry will decline owing to the digital technologies with which people interact every day. While this might be considere...
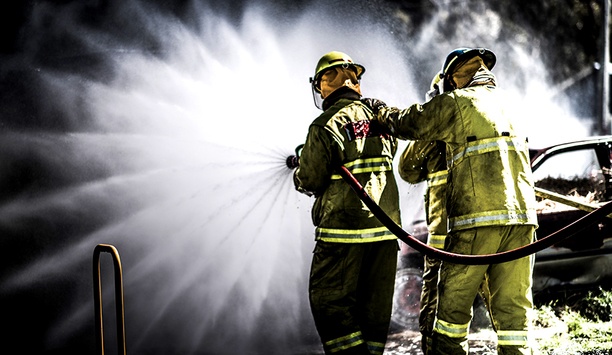
Want to know an easy way to judge the quality of a fire department? Look at how much they train. Career, volunteer or combination, fire departments become successful through traini...
Latest Rosenbauer International AG news
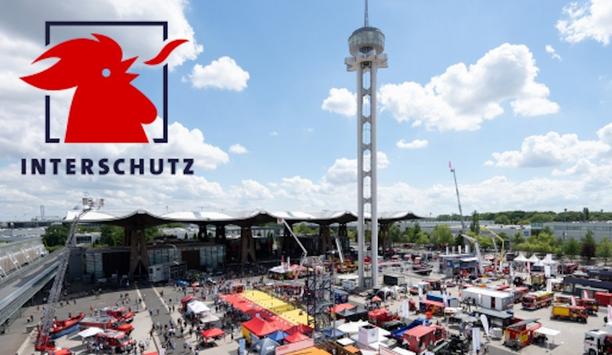
One and a half years before INTERSCHUTZ 2026, many well-known companies have already confirmed their participation in the world's renowned trade fair for firefighting, rescue, and...
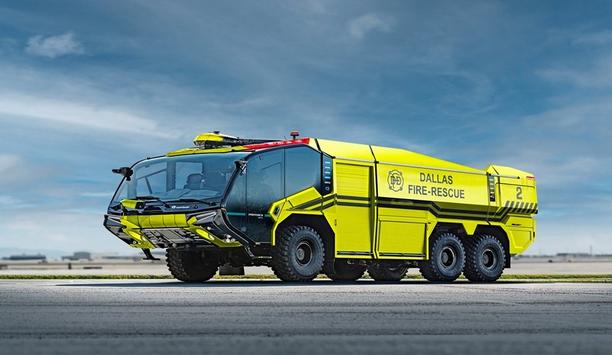
Rosenbauer America and the Dallas Fire Rescue Department have entered into an innovative partnership aimed at the joint further development of the PANTHER 6x6 electric through to s...
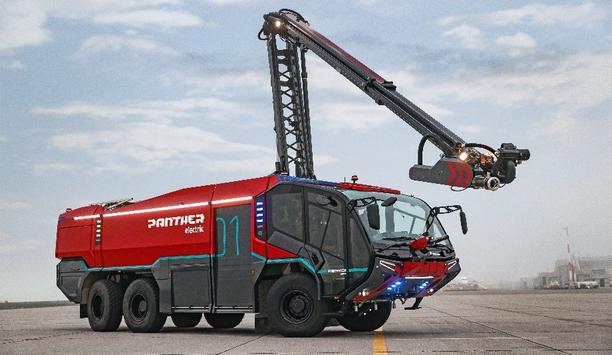
Interested emergency organizations can now order the new PANTHER 6x6 electric. The fully electric twin of the legendary PANTHER unleashes its full power in pure electric mode and a...
Trending topic articles
Skills for Security, the UK’s pioneering fire and security apprenticeship provider, has appointed Gavin Wilson as Head of Sales, reinforcing its commitment to industry development and workforce...
Dräger, a pioneer in the fields of medical and safety technology will be exhibiting at the Blue Light Show to showcase a wide range of technologies that support emergency responders to perform th...
Teledyne Gas & Flame Detection (Teledyne GFD) is supporting its business presence in the Middle East by partnering with Industrial Detection Solutions (IDS) to establish a new 699 m² manufact...
Kent Fire & Rescue Service (KFRS) responds to national wildfire rise with launch of innovative workwear to protect crews and help to keep the public safe. Firefighters responding to wildfires acr...
Pierce Manufacturing Inc., an Oshkosh Corporation business, proudly announces registration is now open for the 13th annual 9/11 Memorial Stair Climb at Lambeau Field in Green Bay, Wisconsin, USA. Co-s...
Natural and smoke ventilation experts - WindowMaster unveils its latest innovation in smoke and heat extraction technology: the WSC 106 compact SHEV control unit. With one smoke zone, this high-perfo...
Bull Products, a pioneering provider of fire, safety, and access control solutions, will be exhibiting at the Fire Safety Live event in London. On stand F80, Bull Products will be showcasing its rang...
Alco, a pioneer in firefighting innovation since 1871, proudly announces the launch of TerraStream3 - a game-changing monitor engineered for both portable and truck-mounted operations. Designed with...
FeuerTrutz, the international trade fair and congress for preventive fire protection, has had a director of exhibitions since mid-May 2025: Phillip Blass has joined the team led by Stefan Dittrich, Ex...
Rosenbauer America, a renowned manufacturer of fire apparatus and firefighting equipment, is pleased to announce the expansion of C.W. Williams and Company's authorized dealer territory to include the...
Fire and Rescue NSW (FRNSW) was busy across many parts of Sydney and the Illawarra yesterday afternoon due to the wild and windy weather. Between midday and midnight, FRNSW received almost 1,000 Trip...
A group of Fire and Rescue NSW (FRNSW) firefighters is just days away from a mammoth 24-hour stair climb of the Furber Steps at Katoomba, in the Blue Mountains, to raise money for charity. The group...
Rescue Intellitech, a major provider of innovative cleaning solutions for the fire and rescue industry, has launched advanced, dual-drying cabinets for PPE, which will help fire and rescue services in...
Mann McGowan, manufacturer of high-performance intumescent fire, smoke, and acoustic seals, is pleased to announce the appointment of Paul Haynes as Business Development Manager. Paul has a strong sa...
Ranger Fire and Security has strengthened its presence in the Irish market with the acquisition of Aqua Fire Prevention, a pioneering Dublin-based fire safety business and the latest to join...
Skills for Security, the UK’s pioneering fire and security apprenticeship provider, has appointed Gavin Wilson as Head of Sales, reinforcing its commitment to industry development and workforce...
Dräger, a pioneer in the fields of medical and safety technology will be exhibiting at the Blue Light Show to showcase a wide range of technologies that support emergency responders to perform th...
Teledyne Gas & Flame Detection (Teledyne GFD) is supporting its business presence in the Middle East by partnering with Industrial Detection Solutions (IDS) to establish a new 699 m² manufact...
Kent Fire & Rescue Service (KFRS) responds to national wildfire rise with launch of innovative workwear to protect crews and help to keep the public safe. Firefighters responding to wildfires acr...
Pierce Manufacturing Inc., an Oshkosh Corporation business, proudly announces registration is now open for the 13th annual 9/11 Memorial Stair Climb at Lambeau Field in Green Bay, Wisconsin, USA. Co-s...
Natural and smoke ventilation experts - WindowMaster unveils its latest innovation in smoke and heat extraction technology: the WSC 106 compact SHEV control unit. With one smoke zone, this high-perfo...
Bull Products, a pioneering provider of fire, safety, and access control solutions, will be exhibiting at the Fire Safety Live event in London. On stand F80, Bull Products will be showcasing its rang...
Alco, a pioneer in firefighting innovation since 1871, proudly announces the launch of TerraStream3 - a game-changing monitor engineered for both portable and truck-mounted operations. Designed with...
FeuerTrutz, the international trade fair and congress for preventive fire protection, has had a director of exhibitions since mid-May 2025: Phillip Blass has joined the team led by Stefan Dittrich, Ex...
Rosenbauer America, a renowned manufacturer of fire apparatus and firefighting equipment, is pleased to announce the expansion of C.W. Williams and Company's authorized dealer territory to include the...
Fire and Rescue NSW (FRNSW) was busy across many parts of Sydney and the Illawarra yesterday afternoon due to the wild and windy weather. Between midday and midnight, FRNSW received almost 1,000 Trip...
A group of Fire and Rescue NSW (FRNSW) firefighters is just days away from a mammoth 24-hour stair climb of the Furber Steps at Katoomba, in the Blue Mountains, to raise money for charity. The group...
Rescue Intellitech, a major provider of innovative cleaning solutions for the fire and rescue industry, has launched advanced, dual-drying cabinets for PPE, which will help fire and rescue services in...
Mann McGowan, manufacturer of high-performance intumescent fire, smoke, and acoustic seals, is pleased to announce the appointment of Paul Haynes as Business Development Manager. Paul has a strong sa...
Ranger Fire and Security has strengthened its presence in the Irish market with the acquisition of Aqua Fire Prevention, a pioneering Dublin-based fire safety business and the latest to join...
Skills for Security, the UK’s pioneering fire and security apprenticeship provider, has appointed Gavin Wilson as Head of Sales, reinforcing its commitment to industry development and workforce...
The New Future For Fire Agencies
DownloadThe Eight Key Trends in Fire Detection in 2023
DownloadA Digital Platform to Improve Fire Safety Compliance and Inspections
DownloadOvercoming the Challenges of Fire Safety in the Paper Industry
DownloadCarbon Monoxide: Creeping Killer Caught In The Act
Download