Morley-IAS FIRE SUPPRESSION SYSTEM ACCESSORIES (3)
Browse FIRE SUPPRESSION SYSTEM ACCESSORIES
- Make
- Morley-IAS
- Other Morley-IAS products
- Morley-IAS Detectors
- Morley-IAS Warning Lights & Sirens
Fire Suppression System Accessories products updated recently
Fire Suppression System Accessories - Expert Commentary
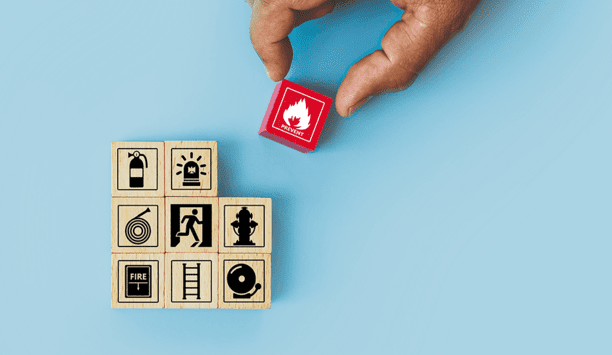
The 2022 Building Safety Act, instituted in direct response to the Grenfell Tower tragedy in London, UK, has outlined a raft of new responsibilities that building owners and manage...
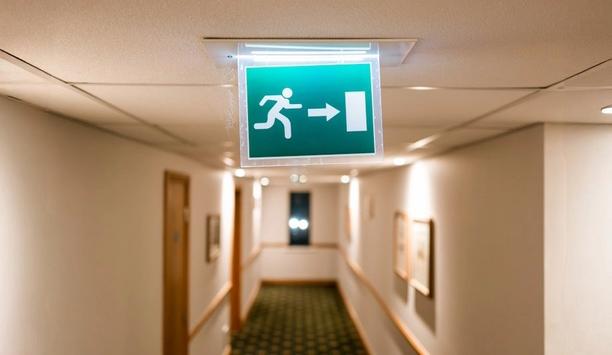
Are people too passive when it comes to fire door safety? Research conducted by the British Woodworking Federation (BWF) in 2022 would suggest so, with a third of the British publi...
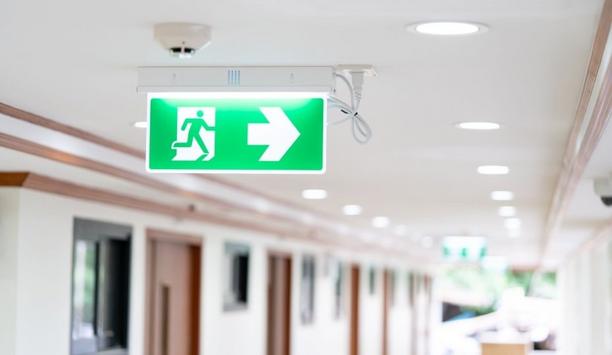
When fire safety fails, lives are put at risk. In all buildings, reasonable steps must be made to reduce the likelihood and impact of fire, yet, many people remain unsure and indec...
Latest Morley-IAS news

With 20 exhibitors and 180 delegates, FIM Expo offered an excellent opportunity for networking and conversations with individuals from all sectors of the fire industry. This event...
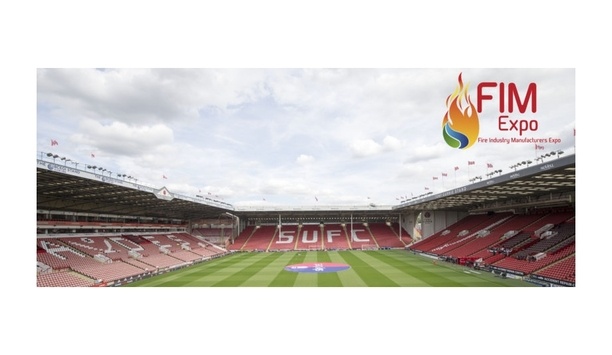
The next Fire Industry Manufacturers’ (FIM) Expo which will take place Wednesday 16th October, 2019. This time the FIM Expo will take place at Sheffield United Football Club....
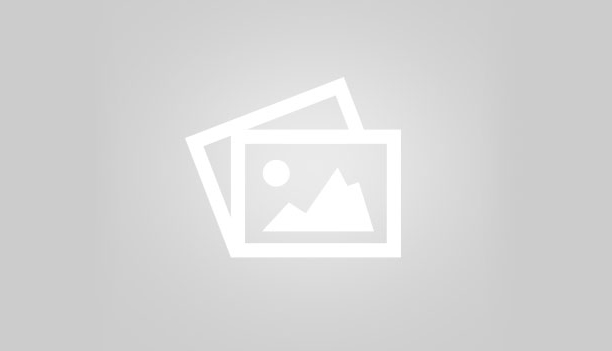
Also, Honeywell D1 system and All-Spec air sampling device were installed at the zoo In 1930, George Mottershead bought Oakfield House in Chester, along with sev...
The New Future For Fire Agencies
DownloadThe Eight Key Trends in Fire Detection in 2023
DownloadA Digital Platform to Improve Fire Safety Compliance and Inspections
DownloadOvercoming the Challenges of Fire Safety in the Paper Industry
DownloadCarbon Monoxide: Creeping Killer Caught In The Act
Download