Rosenbauer Firefighting Accessories (5)
Browse Firefighting Accessories
- Make
- Rosenbauer
- Other Rosenbauer products
- Rosenbauer Vehicles
- Rosenbauer Boots
- Rosenbauer Pumps
- Rosenbauer Helmets
- Rosenbauer Nozzles
Apparatus and Equipment Accessories products updated recently
Apparatus and Equipment Accessories - Expert Commentary
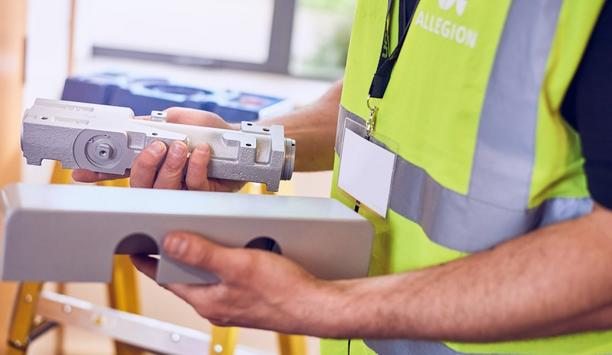
Fire doors are designed to save lives. When closed, they form a crucial barrier against smoke and fire and provide vital time for occupants to escape in an emergency situation. An...
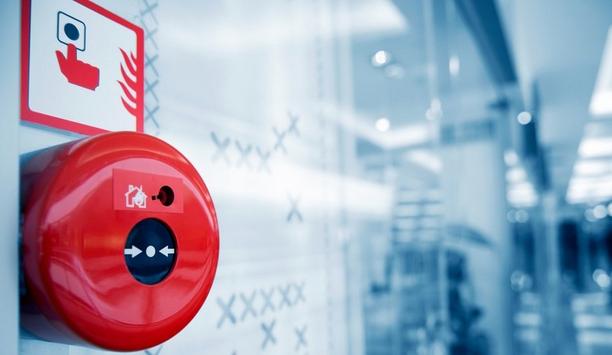
The National Fire Protection Association (NFPA) has developed over 300 codes and standards to support the rapidly changing needs of the fire and life safety industry. NFPA 72, Na...
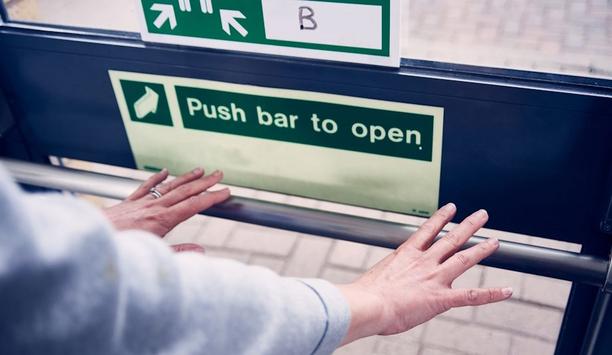
Healthcare environments are synonymous with caution, wellness and safety. Though, where National Health Service professionals work determinedly to meet the needs of their patients,...
Latest Rosenbauer International AG news
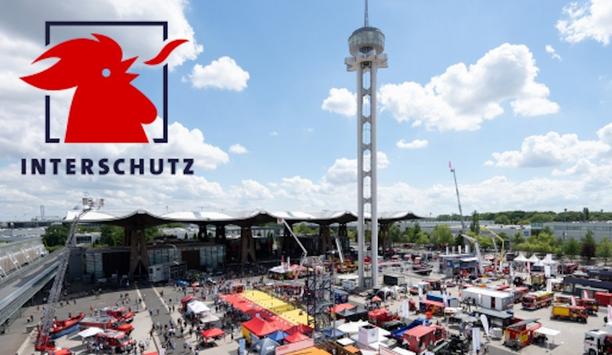
One and a half years before INTERSCHUTZ 2026, many well-known companies have already confirmed their participation in the world's renowned trade fair for firefighting, rescue, and...
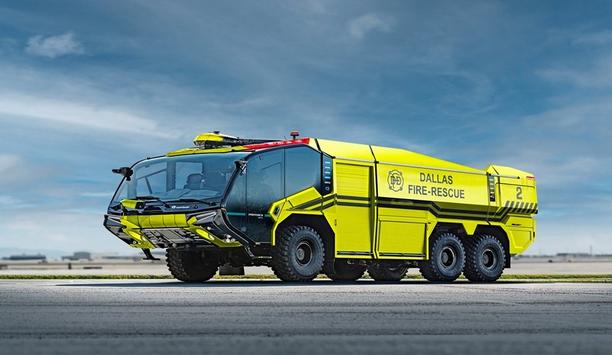
Rosenbauer America and the Dallas Fire Rescue Department have entered into an innovative partnership aimed at the joint further development of the PANTHER 6x6 electric through to s...
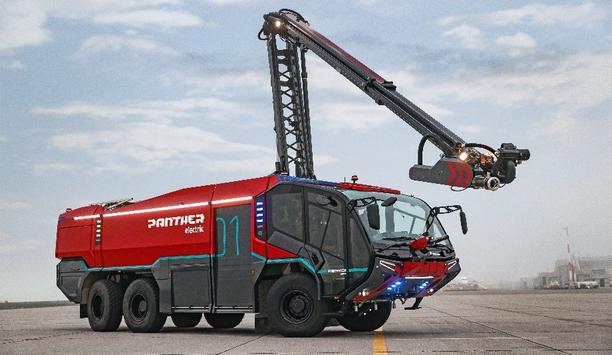
Interested emergency organizations can now order the new PANTHER 6x6 electric. The fully electric twin of the legendary PANTHER unleashes its full power in pure electric mode and a...
Trending topic articles
Honeywell has completed the sale of its Personal Protective Equipment (PPE) business to Protective Industrial Products, Inc. for $1.325 billion in an all-cash transaction. PIP is a global supplier an...
At FeuerTrutz, the globally renowned trade fair for preventive fire protection in Nuremberg, WAGNER will showcase its comprehensive fire protection solutions for various room sizes and applications fr...
Fire-Dex, a pioneer in PPE for first responders, is gearing up for its next chapter, announcing a leadership succession as CEO Steve Allison looks toward retirement in early 2027. Effective at the s...
G4S has been awarded the contract as the principal security provider for Sizewell C, the new 3.2GW nuclear power station under construction on the Suffolk coast. G4S will supply and support the...
Volunteer first responders balance demanding schedules, making it challenging to pursue personal goals like higher education. Fortunately, online learning offers greater flexibility, helping emergenc...
Rosenbauer America, a pioneering manufacturer of fire apparatus and emergency equipment, is pleased to announce a significant expansion of All American Fire Equipment’s area of responsibility (A...
Godiva, a global pioneer in fire pump innovation, proudly announces the launch of The SAMFlows Experience—a dynamic, interactive digital journey that redefines how users engage with and understa...
Darley is proud to announce it has been selected as a 2025 US Best Managed Company. Sponsored by Deloitte Private and The Wall Street Journal, the program recognizes outstanding U.S. private companies...
Blackline Safety Corp., a pioneer in connected safety technology, has announced that its new EXO 8 area monitor — the world’s only direct-to-cloud portable area monitor capable of detectin...
The surge in demand seen by the cables industry for Category 3 Control fire performance cables can be met with the supply chains working together, says pioneering cable supplier - AEI Cables. The inc...
Hochiki Europe has brought the thrill of live football to the heart of the Gillingham community, awarding 35 coveted tickets to a Gillingham FC home game to the deserving Medway Soccer Academy. The a...
Oshkosh Airport Products, an Oshkosh Corporation business, announced the delivery of two Oshkosh Airport Products Striker® 6x6 ARFF vehicles to MET – Montreal Metropolitan Airport ...
Fire protection solutions manufacturer, Advanced, has supplied an intelligent fire panel with wireless detection to iconic Scottish knitwear brand Eribé. An Advanced MxPro 5 analog addressable...
Hampshire and Isle of Wight Fire and Rescue Service (HIWFRS) is changing the way it responds to Automatic Fire Alarms in certain types of buildings as of 01 August 2025. Following a public consultati...
SMARTSHOOTER, a world pioneer in fire control systems, will showcase its handheld and remotely controlled SMASH solutions at the DEFEA 2025 defense exhibition in Athens, Greece. The company will pre...
The New Future For Fire Agencies
DownloadThe Eight Key Trends in Fire Detection in 2023
DownloadA Digital Platform to Improve Fire Safety Compliance and Inspections
DownloadOvercoming the Challenges of Fire Safety in the Paper Industry
DownloadCarbon Monoxide: Creeping Killer Caught In The Act
Download