Oshkosh FIRE TRUCKS AND VEHICLES (5)
Browse FIRE TRUCKS AND VEHICLES
Vehicle products updated recently
Vehicles - Expert Commentary
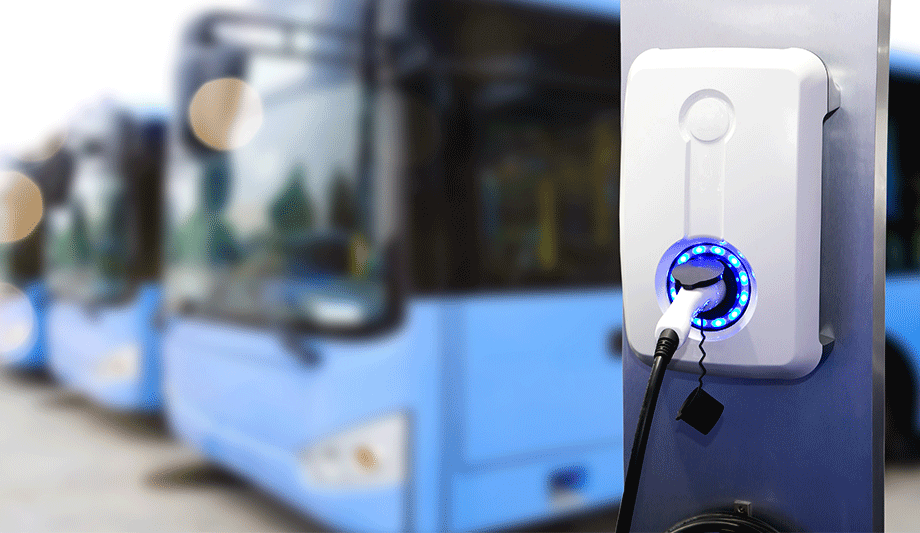
The UK’s electric bus fleet is set to become the largest in Europe by 2024, with numbers projected to grow by almost 180%. Risks associated with fire safety The primary tec...
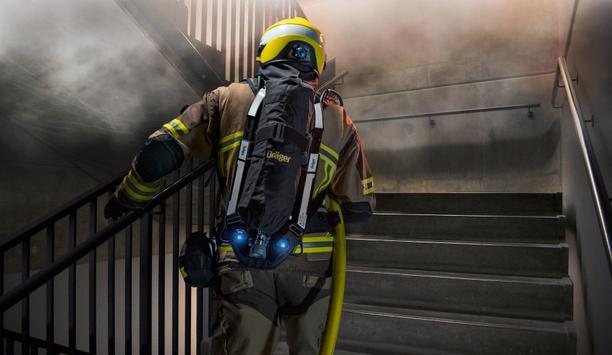
The product lifecycle of self-contained breathing apparatus (SCBA) is approximately ten years, during which time technology inevitably advances considerably in terms of digitizatio...
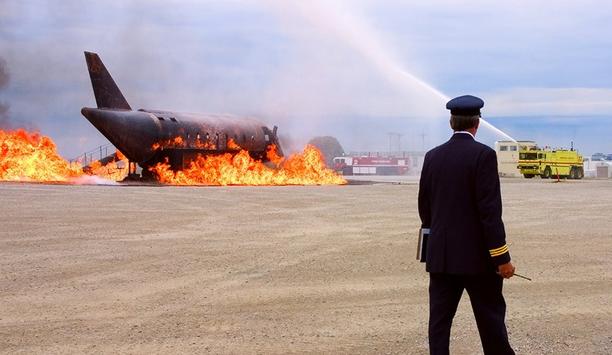
One if the few bonuses of the 2020 COVID-19 Lockdown in the UK was the dramatic reduction of aircraft noise around our homes. Certainly in the Southeast of England, it gave us some...
Latest Oshkosh Corp. news

Pierce Manufacturing Inc., an Oshkosh Corporation business, is pleased to announce Cary Fire Department in North Carolina has introduced into service a Pierce Volterra electric pum...

Darley, a globally renowned provider of defense, fire, and emergency services equipment, is pleased to announce the appointment of Jim Johnson to its Fire Advisory Board. Jim Johns...

Oshkosh Airport Products, an Oshkosh Corporation business, announced the delivery of three new Striker® 8x8 Aircraft Rescue and Firefighting (ARFF) vehicles to serve Minneapoli...
Trending topic articles
Fire and Rescue NSW (FRNSW) crews are battling a large warehouse fire at Five Dock, in Sydney's inner west. Shortly after 3 pm, FRNSW received multiple Triple-Zero (000) calls reporting large volumes...
Fire and Rescue NSW (FRNSW) has determined there was a 12 percent increase in house fires during winter this year, sparking calls for more working smoke alarms in NSW homes. The latest statistics gat...
Fire and Rescue NSW (FRNSW) crews have saved a home from a large Lithium-Ion battery fire at Warrawee, on Sydney’s upper north shore. A resident was charging the battery used to power a leaf bl...
Darley, a major provider of defense, fire, and emergency services equipment, is proud to announce it has been named one of Crain’s 2025 Fast 50 by Crain’s Chicago Business. This honor re...
Fire and Rescue NSW (FRNSW) crews have successfully completed a strategic hazard reduction burn to protect the headland at North Mona Vale, on Sydney's northern beaches. FRNSW deployed firefighters f...
Johnson Controls marks the one-year anniversary of Autocall as it introduces the brand of proven fire detection systems to the Canadian market. By bringing Autocall to Canada, Johnson Controls is pr...
The latest updates to UL 268, Standard for Safety of Smoke Detectors for Fire Alarm Systems, call for significant improvements to smoke detection technology. Set to take effect in June 2021, the new...
While building fire and life safety codes are typically viewed as set in stone, the reality is not quite as concrete. As facilities add unique design elements to achieve aesthetic or functional goals,...
Fire and Rescue NSW (FRNSW) investigators have determined a tobacco pipe sparked a fire at Seven Hills, in Sydney's north-west, which injured two people last night. The blaze broke out at the back of...
Fire and Rescue NSW (FRNSW) investigators will examine the scene of a major gas fire at a service station last night at Fairfield, in Sydney's south-west. Around 50 firefighters responded to numerous...
Fire and Rescue NSW (FRNSW) crews have extinguished a major factory fire in Sydney's south-west. Just before 4 am this morning, a Triple Zero (000) emergency call alerted firefighters to a plastic pi...
His younger colleagues lovingly call him “the dinosaur,” and after five decades of serving the public, Fire and Rescue NSW (FRNSW) Station Officer Fred Parkhouse, has called ‘time&rs...
Fire and Rescue NSW (FRNSW) crews are at the scene of a helicopter crash in Sydney's south-west. Two people were aboard the single-engine aircraft when it plummeted to the ground at the Bankstown Aer...
Fire and Rescue NSW (FRNSW) crews are working to clear a major spill of combustible liquid at Mascot, in Sydney's inner south. The operation began around 4:30 am when two semi-trailers collided at th...
Fire and Rescue NSW (FRNSW) investigators are working to determine the cause of a fire which has engulfed a factory at Jamisontown, in Sydney's west. More than 40 firefighters and 14 fire trucks were...
Fire and Rescue NSW (FRNSW) crews are battling a large warehouse fire at Five Dock, in Sydney's inner west. Shortly after 3 pm, FRNSW received multiple Triple-Zero (000) calls reporting large volumes...
Fire and Rescue NSW (FRNSW) has determined there was a 12 percent increase in house fires during winter this year, sparking calls for more working smoke alarms in NSW homes. The latest statistics gat...
Fire and Rescue NSW (FRNSW) crews have saved a home from a large Lithium-Ion battery fire at Warrawee, on Sydney’s upper north shore. A resident was charging the battery used to power a leaf bl...
Darley, a major provider of defense, fire, and emergency services equipment, is proud to announce it has been named one of Crain’s 2025 Fast 50 by Crain’s Chicago Business. This honor re...
Fire and Rescue NSW (FRNSW) crews have successfully completed a strategic hazard reduction burn to protect the headland at North Mona Vale, on Sydney's northern beaches. FRNSW deployed firefighters f...
Johnson Controls marks the one-year anniversary of Autocall as it introduces the brand of proven fire detection systems to the Canadian market. By bringing Autocall to Canada, Johnson Controls is pr...
The latest updates to UL 268, Standard for Safety of Smoke Detectors for Fire Alarm Systems, call for significant improvements to smoke detection technology. Set to take effect in June 2021, the new...
While building fire and life safety codes are typically viewed as set in stone, the reality is not quite as concrete. As facilities add unique design elements to achieve aesthetic or functional goals,...
Fire and Rescue NSW (FRNSW) investigators have determined a tobacco pipe sparked a fire at Seven Hills, in Sydney's north-west, which injured two people last night. The blaze broke out at the back of...
Fire and Rescue NSW (FRNSW) investigators will examine the scene of a major gas fire at a service station last night at Fairfield, in Sydney's south-west. Around 50 firefighters responded to numerous...
Fire and Rescue NSW (FRNSW) crews have extinguished a major factory fire in Sydney's south-west. Just before 4 am this morning, a Triple Zero (000) emergency call alerted firefighters to a plastic pi...
His younger colleagues lovingly call him “the dinosaur,” and after five decades of serving the public, Fire and Rescue NSW (FRNSW) Station Officer Fred Parkhouse, has called ‘time&rs...
Fire and Rescue NSW (FRNSW) crews are at the scene of a helicopter crash in Sydney's south-west. Two people were aboard the single-engine aircraft when it plummeted to the ground at the Bankstown Aer...
Fire and Rescue NSW (FRNSW) crews are working to clear a major spill of combustible liquid at Mascot, in Sydney's inner south. The operation began around 4:30 am when two semi-trailers collided at th...
Fire and Rescue NSW (FRNSW) investigators are working to determine the cause of a fire which has engulfed a factory at Jamisontown, in Sydney's west. More than 40 firefighters and 14 fire trucks were...
Fire and Rescue NSW (FRNSW) crews are battling a large warehouse fire at Five Dock, in Sydney's inner west. Shortly after 3 pm, FRNSW received multiple Triple-Zero (000) calls reporting large volumes...
The New Future For Fire Agencies
DownloadThe Eight Key Trends in Fire Detection in 2023
DownloadA Digital Platform to Improve Fire Safety Compliance and Inspections
DownloadOvercoming the Challenges of Fire Safety in the Paper Industry
DownloadCarbon Monoxide: Creeping Killer Caught In The Act
Download