TriTech FIRE DEPARTMENT SOFTWARE (7)
Browse FIRE DEPARTMENT SOFTWARE
Software products updated recently
Software - Expert Commentary
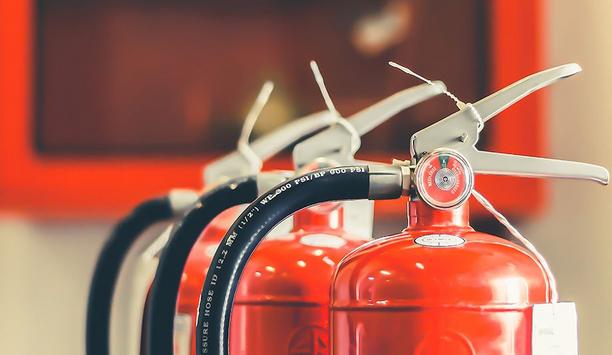
Nearly a decade has passed since the devastating Grenfell Fire, and still the UK construction industry finds itself grappling with the imperative of ensuring fire safety standards...
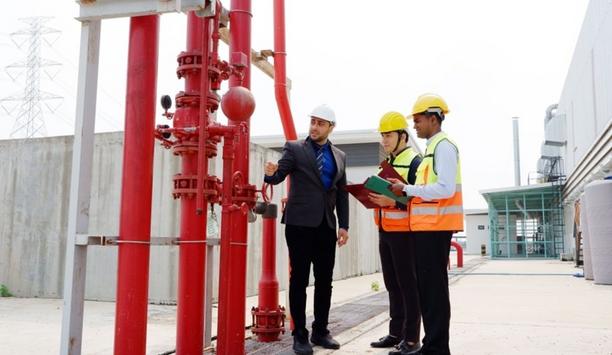
In the challenging world of fire safety and security services, organizations are constantly juggling the need to maintain high efficiency with the relentless push for technological...
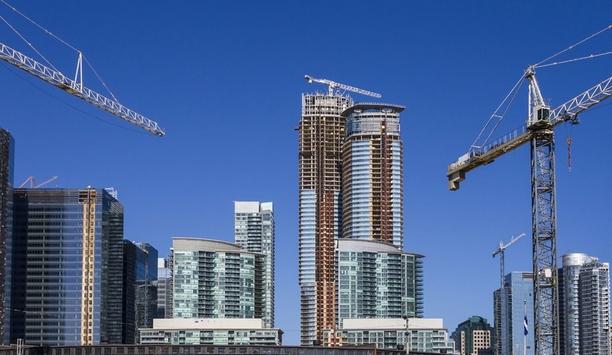
Using technology to provide the information required under the new Building Safety Act 2022, which has been enforceable since October 1st, can help relieve the pressure on sup...
Latest TriTech Software Systems news
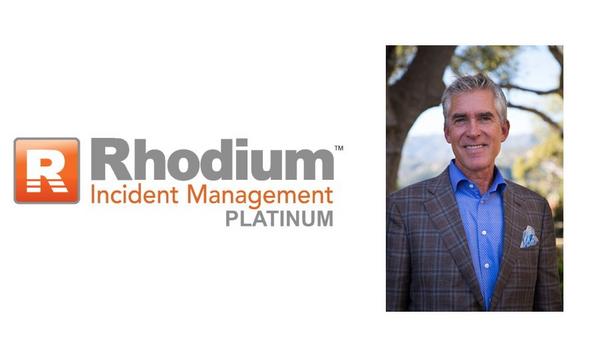
Denver-based crisis response software company, Incident Response Technologies, Inc. (IRT), also the developer of the Rhodium Incident Management platform, has received a personal i...
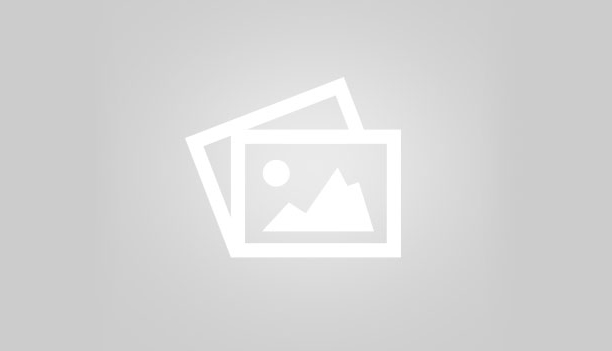
TriTech Software Systems and Lucas County Department of Emergency Services sign a beneficial contract TriTech to provide integrated computer-aided dispatch...
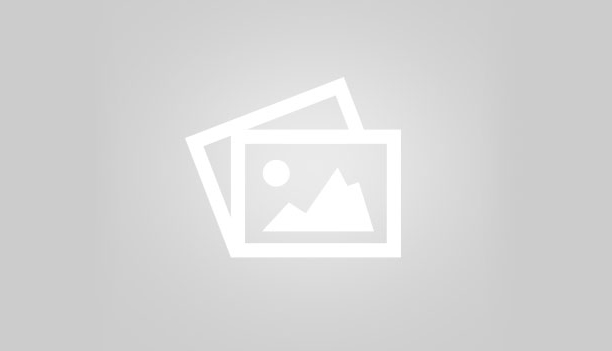
Tritech's Imc Solutions Suite is an affordable and fully integrated systems TriTech Software Systems, a leading provider of integrated public safety software sol...
Trending topic articles
With wildfires overwhelming Los Angeles and dominating headlines across the country, dramatically changing the landscape that people live and work in the wildland-urban interface, there...
Darley, a globally renowned provider of defense, fire, and emergency services equipment, is proud to announce the launch of a new section on its website, darley.com/uncrewed-systems, dedicated exclusi...
Growing fire safety industry organization - Fire Aware aims to change the culture of the built environment sector, by introducing a moral code of conduct via a series of charters designed to influence...
Dräger, the international pioneer in medical and safety technology, has launched a browser-based software solution to optimize daily operations in fire service workshops. Resource and Asse...
Pierce Manufacturing Inc., an Oshkosh Corporation business, is pleased to announce Pierce's authorized dealer, Atlantic Emergency Solutions, has completed a significant expansion of its Charlotte, Nor...
Fire and Rescue NSW (FRNSW) investigators have determined a tobacco pipe sparked a fire at Seven Hills, in Sydney's north-west, which injured two people last night. The blaze broke out at the back of...
Fire and Rescue NSW (FRNSW) investigators will examine the scene of a major gas fire at a service station last night at Fairfield, in Sydney's south-west. Around 50 firefighters responded to numerous...
Fire and Rescue NSW (FRNSW) crews have extinguished a major factory fire in Sydney's south-west. Just before 4 am this morning, a Triple Zero (000) emergency call alerted firefighters to a plastic pi...
His younger colleagues lovingly call him “the dinosaur,” and after five decades of serving the public, Fire and Rescue NSW (FRNSW) Station Officer Fred Parkhouse, has called ‘time&rs...
Fire and Rescue NSW (FRNSW) crews are at the scene of a helicopter crash in Sydney's south-west. Two people were aboard the single-engine aircraft when it plummeted to the ground at the Bankstown Aer...
Fire and Rescue NSW (FRNSW) crews are working to clear a major spill of combustible liquid at Mascot, in Sydney's inner south. The operation began around 4:30 am when two semi-trailers collided at th...
Fire and Rescue NSW (FRNSW) investigators are working to determine the cause of a fire which has engulfed a factory at Jamisontown, in Sydney's west. More than 40 firefighters and 14 fire trucks were...
Fire and Rescue NSW (FRNSW) crews are battling a large warehouse fire at Five Dock, in Sydney's inner west. Shortly after 3 pm, FRNSW received multiple Triple-Zero (000) calls reporting large volumes...
Fire and Rescue NSW (FRNSW) has determined there was a 12 percent increase in house fires during winter this year, sparking calls for more working smoke alarms in NSW homes. The latest statistics gat...
Fire and Rescue NSW (FRNSW) crews have saved a home from a large Lithium-Ion battery fire at Warrawee, on Sydney’s upper north shore. A resident was charging the battery used to power a leaf bl...
The New Future For Fire Agencies
DownloadThe Eight Key Trends in Fire Detection in 2023
DownloadA Digital Platform to Improve Fire Safety Compliance and Inspections
DownloadOvercoming the Challenges of Fire Safety in the Paper Industry
DownloadCarbon Monoxide: Creeping Killer Caught In The Act
Download