James Mountain
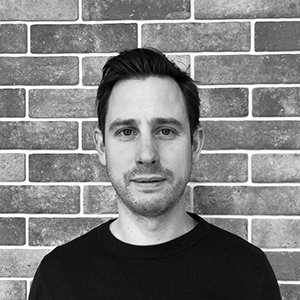
James Mountain
Sales and Marketing Director, Fire Shield SystemsArticles by James Mountain
The UK’s demand for sustainable heat and power sources is increasing rapidly. This is seeing a growing dependence on renewable energy sources for electricity, and, as we’re facing a landsc...
Businesses operating within the waste industry are susceptible to a wide range of fire risks. Storage of combustible materials, the ongoing use of industrial vehicles and waste’s natural ability...
In any business, fire can cause significant damage and substantial loss of revenue, assets, or productivity due to a period of downtime. However, fires can be prevented through continuous temperature...
Due to the nature of their design and uses, tunnels have particularly unique fire risks, and any fire can spread quickly, risking damage to assets or injuries to teams. Mining, cable and communication...
Recent years have seen fire risks and resulting insurance claims in commercial premises grow significantly. This increase has been influenced by various factors, such as unusually hot and dry weather,...
The UK’s electric bus fleet is set to become the largest in Europe by 2024, with numbers projected to grow by almost 180%. Risks associated with fire safety The primary technology fuelling our...
The greatest fire risk to waste and recycling businesses is, without doubt, battery waste. You can find batteries everywhere – in children’s toys, mobile phones and other general WEEE (was...
The global drive towards sustainability is causing businesses to continually search for alternative fuel sources, seeing an increase in rubber and plastic recycling across the UK. However, recycling t...
The UK’s demand for sustainable heat and power sources is increasing rapidly. This is seeing a growing dependence on renewable energy sources for electricity, and, as we’re facing a landsc...
Businesses operating within the waste industry are susceptible to a wide range of fire risks. Storage of combustible materials, the ongoing use of industrial vehicles and waste’s natural ability...
In any business, fire can cause significant damage and substantial loss of revenue, assets, or productivity due to a period of downtime. However, fires can be prevented through continuous temperature...
Due to the nature of their design and uses, tunnels have particularly unique fire risks, and any fire can spread quickly, risking damage to assets or injuries to teams. Mining, cable and communication...
Recent years have seen fire risks and resulting insurance claims in commercial premises grow significantly. This increase has been influenced by various factors, such as unusually hot and dry weather,...
The UK’s electric bus fleet is set to become the largest in Europe by 2024, with numbers projected to grow by almost 180%. Risks associated with fire safety The primary technology fuelling our...
The greatest fire risk to waste and recycling businesses is, without doubt, battery waste. You can find batteries everywhere – in children’s toys, mobile phones and other general WEEE (was...
The global drive towards sustainability is causing businesses to continually search for alternative fuel sources, seeing an increase in rubber and plastic recycling across the UK. However, recycling t...
Fire protection Experts
The New Future For Fire Agencies
DownloadThe Eight Key Trends in Fire Detection in 2023
DownloadA Digital Platform to Improve Fire Safety Compliance and Inspections
DownloadOvercoming the Challenges of Fire Safety in the Paper Industry
DownloadCarbon Monoxide: Creeping Killer Caught In The Act
Download