MSA FIRE RESCUE ACESSORIES (4)
Browse FIRE RESCUE ACESSORIES
Rescue/RIT Accessories products updated recently
Rescue/RIT Accessories - Expert Commentary
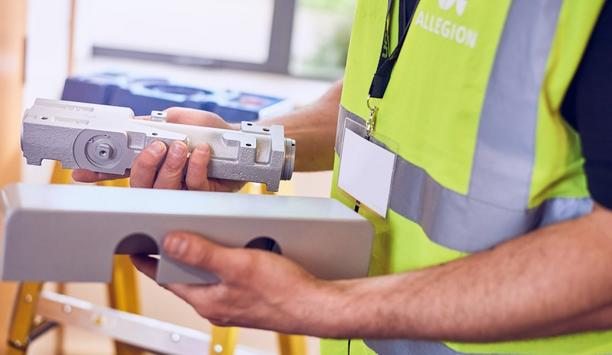
Fire doors are designed to save lives. When closed, they form a crucial barrier against smoke and fire and provide vital time for occupants to escape in an emergency situation. An...
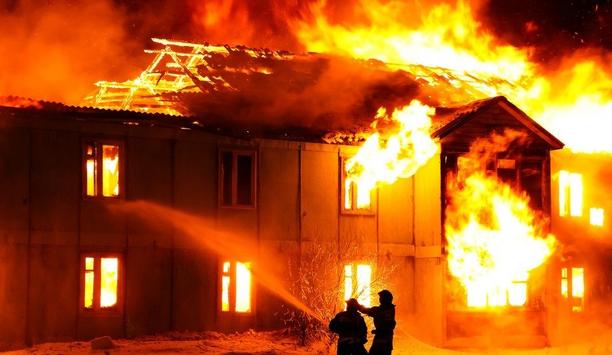
It is no secret that electricity can have a significant impact on the fire industry, and this is not just something that is restricted to a single country. Daily, we see the deva...
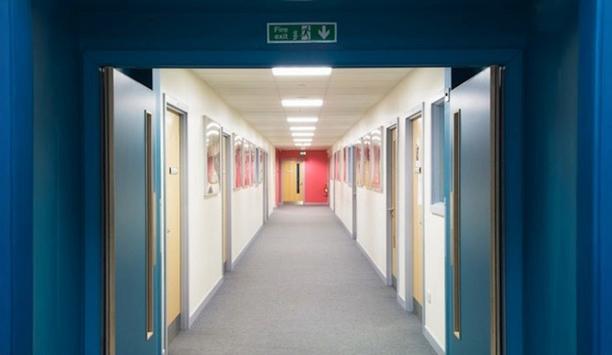
Safe and seamless movement in our built environment hinges on accurately specified and installed door hardware, explains Russell Marks, managing director of Boss Door Controls. Wi...
Latest MSA Safety Incorporated news
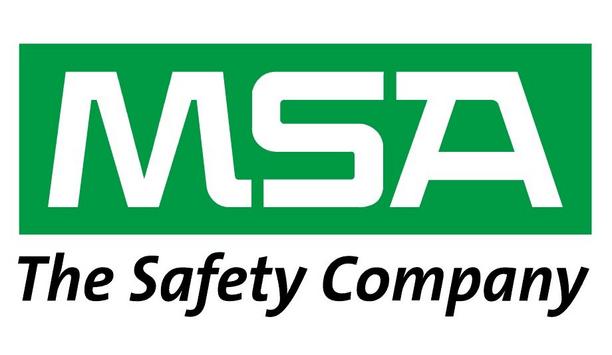
Global safety equipment manufacturer MSA Safety, Inc. announced it has secured a $10 million contract to provide respiratory protective equipment to the Orange Count...
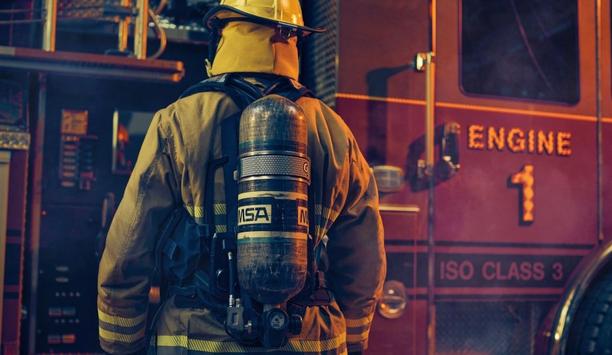
Innovation in the fire service is a continuous journey, where changing customer needs are driving forces in developing the newest safety solutions. For MSA Safety, that means takin...
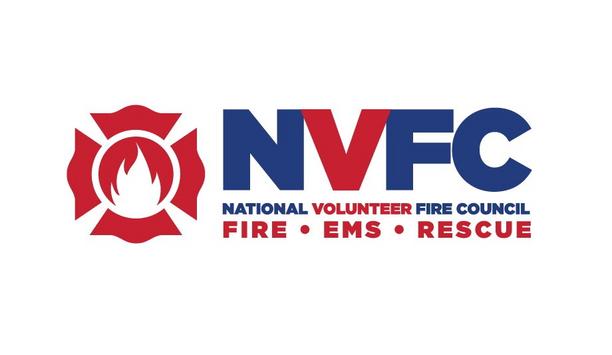
Each year, MSA Safety and DuPont Personal Protection partner with the National Volunteer Fire Council (NVFC) to provide Globe turnout gear and MSA fire helmets to volunteer fire...
Trending topic articles
The surge in demand seen by the cables industry for Category 3 Control fire performance cables can be met with the supply chains working together, says pioneering cable supplier - AEI Cables. The inc...
Hochiki Europe has brought the thrill of live football to the heart of the Gillingham community, awarding 35 coveted tickets to a Gillingham FC home game to the deserving Medway Soccer Academy. The a...
Oshkosh Airport Products, an Oshkosh Corporation business, announced the delivery of two Oshkosh Airport Products Striker® 6x6 ARFF vehicles to MET – Montreal Metropolitan Airport ...
Fire protection solutions manufacturer, Advanced, has supplied an intelligent fire panel with wireless detection to iconic Scottish knitwear brand Eribé. An Advanced MxPro 5 analog addressable...
Hampshire and Isle of Wight Fire and Rescue Service (HIWFRS) is changing the way it responds to Automatic Fire Alarms in certain types of buildings as of 01 August 2025. Following a public consultati...
SMARTSHOOTER, a world pioneer in fire control systems, will showcase its handheld and remotely controlled SMASH solutions at the DEFEA 2025 defense exhibition in Athens, Greece. The company will pre...
Global safety equipment manufacturer MSA Safety, Inc. announced it has secured a $10 million contract to provide respiratory protective equipment to the Orange County Fire Authorit...
Skills for Security welcomes EFT Group as a new sponsor, further strengthening its mission to develop the next generation of skilled professionals in the fire and security industry. As one of the UK&...
Fire-Dex, a pioneer in PPE for first responders, is gearing up for its next chapter, announcing a leadership succession as CEO Steve Allison looks toward retirement in early 2027. Effective at the s...
G4S has been awarded the contract as the principal security provider for Sizewell C, the new 3.2GW nuclear power station under construction on the Suffolk coast. G4S will supply and support the...
Volunteer first responders balance demanding schedules, making it challenging to pursue personal goals like higher education. Fortunately, online learning offers greater flexibility, helping emergenc...
Rosenbauer America, a pioneering manufacturer of fire apparatus and emergency equipment, is pleased to announce a significant expansion of All American Fire Equipment’s area of responsibility (A...
Godiva, a global pioneer in fire pump innovation, proudly announces the launch of The SAMFlows Experience—a dynamic, interactive digital journey that redefines how users engage with and understa...
Darley is proud to announce it has been selected as a 2025 US Best Managed Company. Sponsored by Deloitte Private and The Wall Street Journal, the program recognizes outstanding U.S. private companies...
Blackline Safety Corp., a pioneer in connected safety technology, has announced that its new EXO 8 area monitor — the world’s only direct-to-cloud portable area monitor capable of detectin...
The surge in demand seen by the cables industry for Category 3 Control fire performance cables can be met with the supply chains working together, says pioneering cable supplier - AEI Cables. The inc...
Hochiki Europe has brought the thrill of live football to the heart of the Gillingham community, awarding 35 coveted tickets to a Gillingham FC home game to the deserving Medway Soccer Academy. The a...
Oshkosh Airport Products, an Oshkosh Corporation business, announced the delivery of two Oshkosh Airport Products Striker® 6x6 ARFF vehicles to MET – Montreal Metropolitan Airport ...
Fire protection solutions manufacturer, Advanced, has supplied an intelligent fire panel with wireless detection to iconic Scottish knitwear brand Eribé. An Advanced MxPro 5 analog addressable...
Hampshire and Isle of Wight Fire and Rescue Service (HIWFRS) is changing the way it responds to Automatic Fire Alarms in certain types of buildings as of 01 August 2025. Following a public consultati...
SMARTSHOOTER, a world pioneer in fire control systems, will showcase its handheld and remotely controlled SMASH solutions at the DEFEA 2025 defense exhibition in Athens, Greece. The company will pre...
Global safety equipment manufacturer MSA Safety, Inc. announced it has secured a $10 million contract to provide respiratory protective equipment to the Orange County Fire Authorit...
Skills for Security welcomes EFT Group as a new sponsor, further strengthening its mission to develop the next generation of skilled professionals in the fire and security industry. As one of the UK&...
Fire-Dex, a pioneer in PPE for first responders, is gearing up for its next chapter, announcing a leadership succession as CEO Steve Allison looks toward retirement in early 2027. Effective at the s...
G4S has been awarded the contract as the principal security provider for Sizewell C, the new 3.2GW nuclear power station under construction on the Suffolk coast. G4S will supply and support the...
Volunteer first responders balance demanding schedules, making it challenging to pursue personal goals like higher education. Fortunately, online learning offers greater flexibility, helping emergenc...
Rosenbauer America, a pioneering manufacturer of fire apparatus and emergency equipment, is pleased to announce a significant expansion of All American Fire Equipment’s area of responsibility (A...
Godiva, a global pioneer in fire pump innovation, proudly announces the launch of The SAMFlows Experience—a dynamic, interactive digital journey that redefines how users engage with and understa...
Darley is proud to announce it has been selected as a 2025 US Best Managed Company. Sponsored by Deloitte Private and The Wall Street Journal, the program recognizes outstanding U.S. private companies...
Blackline Safety Corp., a pioneer in connected safety technology, has announced that its new EXO 8 area monitor — the world’s only direct-to-cloud portable area monitor capable of detectin...
The surge in demand seen by the cables industry for Category 3 Control fire performance cables can be met with the supply chains working together, says pioneering cable supplier - AEI Cables. The inc...
The New Future For Fire Agencies
DownloadThe Eight Key Trends in Fire Detection in 2023
DownloadA Digital Platform to Improve Fire Safety Compliance and Inspections
DownloadOvercoming the Challenges of Fire Safety in the Paper Industry
DownloadCarbon Monoxide: Creeping Killer Caught In The Act
Download