Elkhart Brass FIRE MONITORS (6)
Browse FIRE MONITORS
- Type
- Fixed
- Portable
- Quick Attack
- Make
- Elkhart Brass
- Other Elkhart Brass products
- Elkhart Brass Nozzles
- Elkhart Brass Valves
Monitor products updated recently
Monitors - Expert Commentary
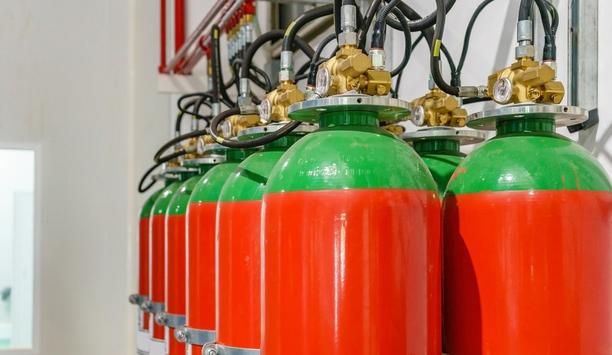
Technological advances in recent decades have considerably improved fire alert systems. Fire sprinkler systems are now installed at a rate of 40 million units per year and now, 96%...
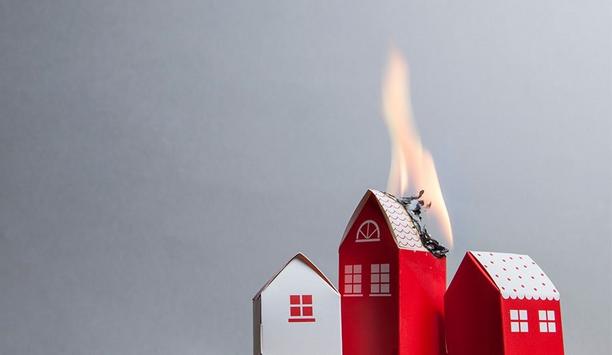
As organizations start to plan for next year’s operating budget, it’s a good time to take a closer look at fire prevention, what’s its costing and the value it de...
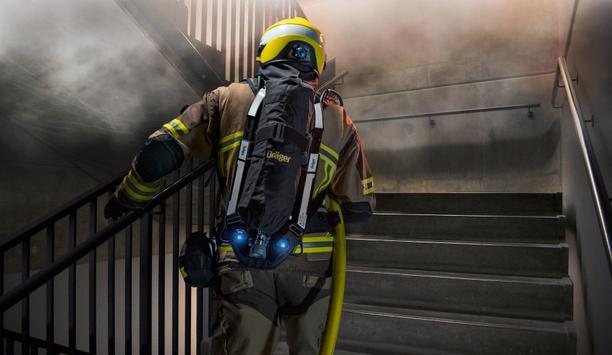
The product lifecycle of self-contained breathing apparatus (SCBA) is approximately ten years, during which time technology inevitably advances considerably in terms of digitizatio...
Latest Elkhart Brass Mfg Co., Inc. news
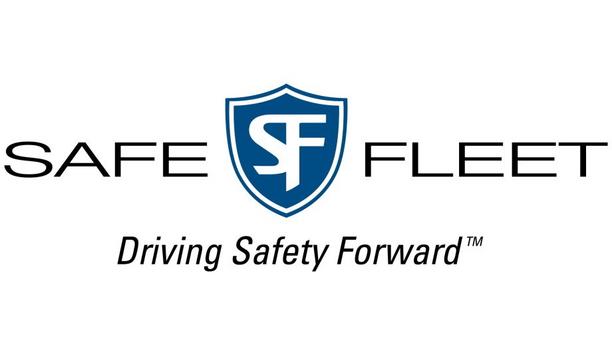
Safe Fleet: Fire, EMS, and Industrial (FRC, FoamPro, Elkhart Brass, ROM) is excited to announce the addition of David Hawkins as the Regional Sales Manager - Industrial. In his ne...
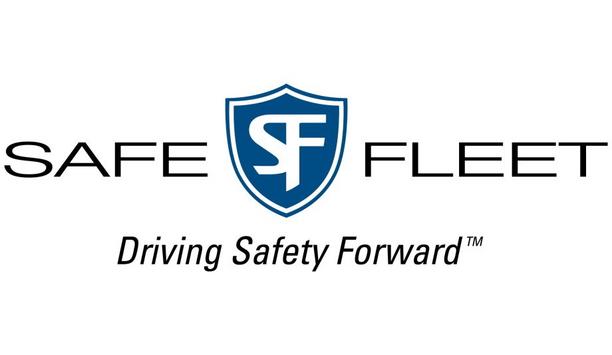
Safe Fleet: Fire, EMS, and Industrial (FRC, FoamPro, Elkhart Brass, ROM) is excited to announce the promotion of Matt Pitzer to the position of Vice President of North American Sal...
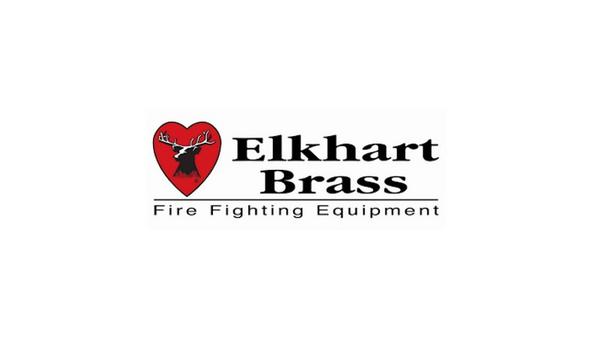
Safe Fleet: Fire, EMS, and Industrial (FRC, FoamPro, Elkhart Brass, ROM) is excited to announce the addition of Steve Falke as the company’s new Senior Director of Industrial...
Trending topic articles
Fire and Rescue NSW (FRNSW) investigators today have determined that a Lithium-ion battery has caused a fire which destroyed five cars at Sydney Airport last night. Firefighters were called around 8:...
Fire and Rescue NSW (FRNSW) firefighter, Gavin Clifton, is just days away from his latest fund-raising venture for charity, climbing 18 hours non-stop up and down the Furber Steps at Katoomba in the B...
A firefighting couple has relied on their on-the-job experience to deliver their own baby in the car park of a Hunter Valley fast food restaurant. Pregnant Fire and Rescue NSW (FRNSW) Communication C...
Fire and Rescue NSW (FRNSW) has determined a fire, which caused major damage to a volunteer organization's ambulance station in Sydney's inner west overnight, was sparked by a Lithium-ion battery in a...
The Fire and Rescue NSW (FRNSW) Firefighter Championships at Wagga Wagga have come to a close, following three days of hard-fought competition and skills development. Making a return to its inaugural...
Oshkosh Airport Products, an Oshkosh Corporation business, is proud to announce the delivery of three advanced Striker Aircraft Rescue and Fire Fighting (ARFF) vehicles to Kansas City International Ai...
Henkel Adhesive Technologies India is excited to share the launch of its new automotive warehouse in Chakan, strategically located in one of India’s key automotive hubs. This built-to-suit...
The acquisition of Australian company Aerial Fire Control strengthens Vallfirest’s global position in aerial firefighting and accelerates the development of next-generation wildfire suppressio...
Darley, a major provider of defense, fire, and emergency services equipment, is proud to announce it has been named one of Crain’s 2025 Fast 50 by Crain’s Chicago Business. This honor re...
Fire and Rescue NSW (FRNSW) crews have successfully completed a strategic hazard reduction burn to protect the headland at North Mona Vale, on Sydney's northern beaches. FRNSW deployed firefighters f...
Johnson Controls marks the one-year anniversary of Autocall as it introduces the brand of proven fire detection systems to the Canadian market. By bringing Autocall to Canada, Johnson Controls is pr...
The latest updates to UL 268, Standard for Safety of Smoke Detectors for Fire Alarm Systems, call for significant improvements to smoke detection technology. Set to take effect in June 2021, the new...
While building fire and life safety codes are typically viewed as set in stone, the reality is not quite as concrete. As facilities add unique design elements to achieve aesthetic or functional goals,...
A number of hazard reduction burns are scheduled for NSW, including the Greater Sydney Area, over the coming days. Smoke from these burns is likely to settle across residential areas, especially in t...
Fire and Rescue NSW (FRNSW) firefighters have saved a historic boat shed from fire on the Parramatta River at Putney, in Sydney's north-west. More than 30 firefighters and eight fire trucks were depl...
Fire and Rescue NSW (FRNSW) investigators today have determined that a Lithium-ion battery has caused a fire which destroyed five cars at Sydney Airport last night. Firefighters were called around 8:...
Fire and Rescue NSW (FRNSW) firefighter, Gavin Clifton, is just days away from his latest fund-raising venture for charity, climbing 18 hours non-stop up and down the Furber Steps at Katoomba in the B...
A firefighting couple has relied on their on-the-job experience to deliver their own baby in the car park of a Hunter Valley fast food restaurant. Pregnant Fire and Rescue NSW (FRNSW) Communication C...
Fire and Rescue NSW (FRNSW) has determined a fire, which caused major damage to a volunteer organization's ambulance station in Sydney's inner west overnight, was sparked by a Lithium-ion battery in a...
The Fire and Rescue NSW (FRNSW) Firefighter Championships at Wagga Wagga have come to a close, following three days of hard-fought competition and skills development. Making a return to its inaugural...
Oshkosh Airport Products, an Oshkosh Corporation business, is proud to announce the delivery of three advanced Striker Aircraft Rescue and Fire Fighting (ARFF) vehicles to Kansas City International Ai...
Henkel Adhesive Technologies India is excited to share the launch of its new automotive warehouse in Chakan, strategically located in one of India’s key automotive hubs. This built-to-suit...
The acquisition of Australian company Aerial Fire Control strengthens Vallfirest’s global position in aerial firefighting and accelerates the development of next-generation wildfire suppressio...
Darley, a major provider of defense, fire, and emergency services equipment, is proud to announce it has been named one of Crain’s 2025 Fast 50 by Crain’s Chicago Business. This honor re...
Fire and Rescue NSW (FRNSW) crews have successfully completed a strategic hazard reduction burn to protect the headland at North Mona Vale, on Sydney's northern beaches. FRNSW deployed firefighters f...
Johnson Controls marks the one-year anniversary of Autocall as it introduces the brand of proven fire detection systems to the Canadian market. By bringing Autocall to Canada, Johnson Controls is pr...
The latest updates to UL 268, Standard for Safety of Smoke Detectors for Fire Alarm Systems, call for significant improvements to smoke detection technology. Set to take effect in June 2021, the new...
While building fire and life safety codes are typically viewed as set in stone, the reality is not quite as concrete. As facilities add unique design elements to achieve aesthetic or functional goals,...
A number of hazard reduction burns are scheduled for NSW, including the Greater Sydney Area, over the coming days. Smoke from these burns is likely to settle across residential areas, especially in t...
Fire and Rescue NSW (FRNSW) firefighters have saved a historic boat shed from fire on the Parramatta River at Putney, in Sydney's north-west. More than 30 firefighters and eight fire trucks were depl...
Fire and Rescue NSW (FRNSW) investigators today have determined that a Lithium-ion battery has caused a fire which destroyed five cars at Sydney Airport last night. Firefighters were called around 8:...
The New Future For Fire Agencies
DownloadThe Eight Key Trends in Fire Detection in 2023
DownloadA Digital Platform to Improve Fire Safety Compliance and Inspections
DownloadOvercoming the Challenges of Fire Safety in the Paper Industry
DownloadCarbon Monoxide: Creeping Killer Caught In The Act
Download