Fireco Ltd FIRE SUPPRESSION SYSTEM ACCESSORIES (7)
Browse FIRE SUPPRESSION SYSTEM ACCESSORIES
- Make
- Fireco Ltd
- Other Fireco Ltd products
- Fireco Ltd Pumps
Fire Suppression System Accessories products updated recently
Fire Suppression System Accessories - Expert Commentary
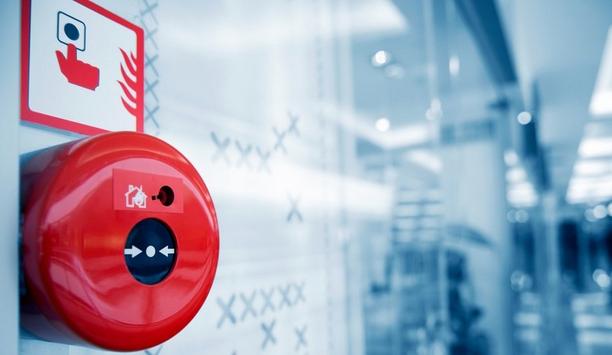
The National Fire Protection Association (NFPA) has developed over 300 codes and standards to support the rapidly changing needs of the fire and life safety industry. NFPA 72, Na...
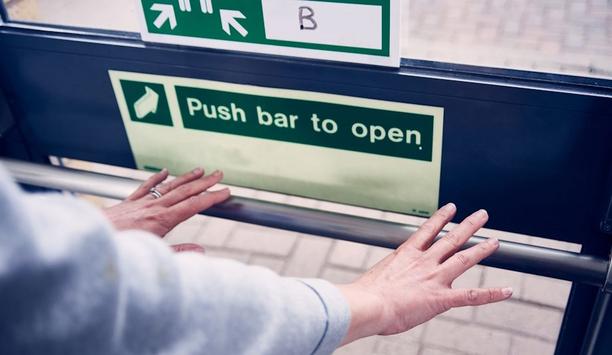
Healthcare environments are synonymous with caution, wellness and safety. Though, where National Health Service professionals work determinedly to meet the needs of their patients,...
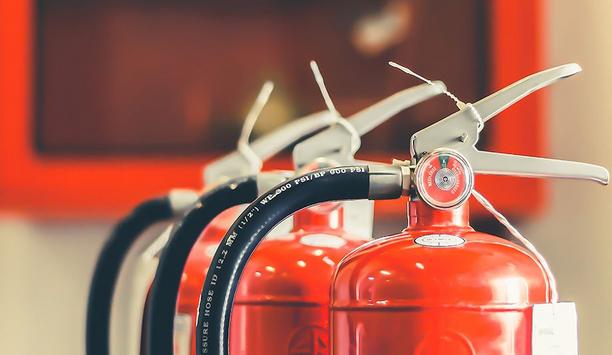
Nearly a decade has passed since the devastating Grenfell Fire, and still the UK construction industry finds itself grappling with the imperative of ensuring fire safety standards...
Latest Fireco Ltd news
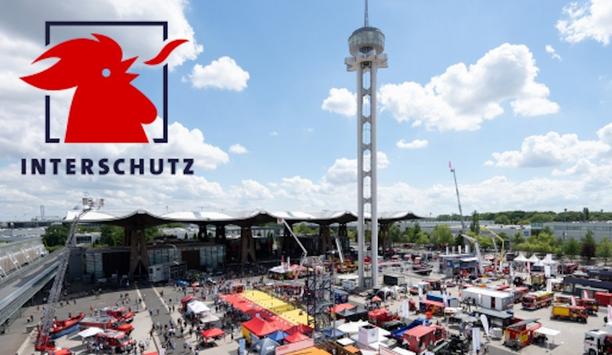
One and a half years before INTERSCHUTZ 2026, many well-known companies have already confirmed their participation in the world's renowned trade fair for firefighting, rescue, and...

With 20 exhibitors and 180 delegates, FIM Expo offered an excellent opportunity for networking and conversations with individuals from all sectors of the fire industry. This event...
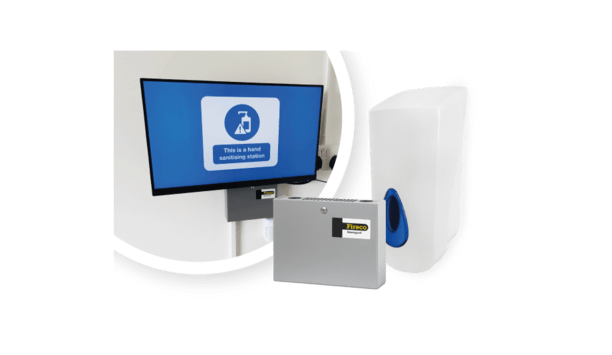
Fireco has released its newest innovation, Germgard, a smart sanitizer combined with digital signage. Germgard has been designed to promote awareness of the importance of hand sani...
Trending topic articles
Oshkosh Airport Products, an Oshkosh Corporation business, announced the delivery of two Oshkosh Airport Products Striker® 6x6 ARFF vehicles to MET – Montreal Metropolitan Airport ...
Fire protection solutions manufacturer, Advanced, has supplied an intelligent fire panel with wireless detection to iconic Scottish knitwear brand Eribé. An Advanced MxPro 5 analog addressable...
Hampshire and Isle of Wight Fire and Rescue Service (HIWFRS) is changing the way it responds to Automatic Fire Alarms in certain types of buildings as of 01 August 2025. Following a public consultati...
SMARTSHOOTER, a world pioneer in fire control systems, will showcase its handheld and remotely controlled SMASH solutions at the DEFEA 2025 defense exhibition in Athens, Greece. The company will pre...
Global safety equipment manufacturer MSA Safety, Inc. announced it has secured a $10 million contract to provide respiratory protective equipment to the Orange County Fire Authorit...
Skills for Security welcomes EFT Group as a new sponsor, further strengthening its mission to develop the next generation of skilled professionals in the fire and security industry. As one of the UK&...
Johnson Controls, the pioneer for smart, healthy, and sustainable buildings, launches the new Simplex 4017ES Fire Alarm Control Unit to help customers meet evolving life safety voice regulations. ...
Hochiki Europe, a manufacturer of innovative life safety solutions, is partnering with Jendee Trading, a global provider with nearly 50 years of experience exporting British electrical and fire safety...
Volunteer first responders balance demanding schedules, making it challenging to pursue personal goals like higher education. Fortunately, online learning offers greater flexibility, helping emergenc...
Rosenbauer America, a pioneering manufacturer of fire apparatus and emergency equipment, is pleased to announce a significant expansion of All American Fire Equipment’s area of responsibility (A...
Godiva, a global pioneer in fire pump innovation, proudly announces the launch of The SAMFlows Experience—a dynamic, interactive digital journey that redefines how users engage with and understa...
Darley is proud to announce it has been selected as a 2025 US Best Managed Company. Sponsored by Deloitte Private and The Wall Street Journal, the program recognizes outstanding U.S. private companies...
Blackline Safety Corp., a pioneer in connected safety technology, has announced that its new EXO 8 area monitor — the world’s only direct-to-cloud portable area monitor capable of detectin...
The surge in demand seen by the cables industry for Category 3 Control fire performance cables can be met with the supply chains working together, says pioneering cable supplier - AEI Cables. The inc...
Hochiki Europe has brought the thrill of live football to the heart of the Gillingham community, awarding 35 coveted tickets to a Gillingham FC home game to the deserving Medway Soccer Academy. The a...
Oshkosh Airport Products, an Oshkosh Corporation business, announced the delivery of two Oshkosh Airport Products Striker® 6x6 ARFF vehicles to MET – Montreal Metropolitan Airport ...
Fire protection solutions manufacturer, Advanced, has supplied an intelligent fire panel with wireless detection to iconic Scottish knitwear brand Eribé. An Advanced MxPro 5 analog addressable...
Hampshire and Isle of Wight Fire and Rescue Service (HIWFRS) is changing the way it responds to Automatic Fire Alarms in certain types of buildings as of 01 August 2025. Following a public consultati...
SMARTSHOOTER, a world pioneer in fire control systems, will showcase its handheld and remotely controlled SMASH solutions at the DEFEA 2025 defense exhibition in Athens, Greece. The company will pre...
Global safety equipment manufacturer MSA Safety, Inc. announced it has secured a $10 million contract to provide respiratory protective equipment to the Orange County Fire Authorit...
Skills for Security welcomes EFT Group as a new sponsor, further strengthening its mission to develop the next generation of skilled professionals in the fire and security industry. As one of the UK&...
Johnson Controls, the pioneer for smart, healthy, and sustainable buildings, launches the new Simplex 4017ES Fire Alarm Control Unit to help customers meet evolving life safety voice regulations. ...
Hochiki Europe, a manufacturer of innovative life safety solutions, is partnering with Jendee Trading, a global provider with nearly 50 years of experience exporting British electrical and fire safety...
Volunteer first responders balance demanding schedules, making it challenging to pursue personal goals like higher education. Fortunately, online learning offers greater flexibility, helping emergenc...
Rosenbauer America, a pioneering manufacturer of fire apparatus and emergency equipment, is pleased to announce a significant expansion of All American Fire Equipment’s area of responsibility (A...
Godiva, a global pioneer in fire pump innovation, proudly announces the launch of The SAMFlows Experience—a dynamic, interactive digital journey that redefines how users engage with and understa...
Darley is proud to announce it has been selected as a 2025 US Best Managed Company. Sponsored by Deloitte Private and The Wall Street Journal, the program recognizes outstanding U.S. private companies...
Blackline Safety Corp., a pioneer in connected safety technology, has announced that its new EXO 8 area monitor — the world’s only direct-to-cloud portable area monitor capable of detectin...
The surge in demand seen by the cables industry for Category 3 Control fire performance cables can be met with the supply chains working together, says pioneering cable supplier - AEI Cables. The inc...
Hochiki Europe has brought the thrill of live football to the heart of the Gillingham community, awarding 35 coveted tickets to a Gillingham FC home game to the deserving Medway Soccer Academy. The a...
Oshkosh Airport Products, an Oshkosh Corporation business, announced the delivery of two Oshkosh Airport Products Striker® 6x6 ARFF vehicles to MET – Montreal Metropolitan Airport ...
The New Future For Fire Agencies
DownloadThe Eight Key Trends in Fire Detection in 2023
DownloadA Digital Platform to Improve Fire Safety Compliance and Inspections
DownloadOvercoming the Challenges of Fire Safety in the Paper Industry
DownloadCarbon Monoxide: Creeping Killer Caught In The Act
Download