Globe FIRE SPRINKLERS (1)
Browse FIRE SPRINKLERS
- Type
- Automatic
- Open-Orifice
- ESFR?
- Yes
- NFPA temperature class
- Ordinary
- Intermediate
- High
- Very Extra High
- Ultra High
- Make
- Globe
- Other Globe products
- Globe Boots
- Globe Turnout/Bunker Gear
Fire Sprinkler products updated recently
Fire Sprinklers - Expert Commentary
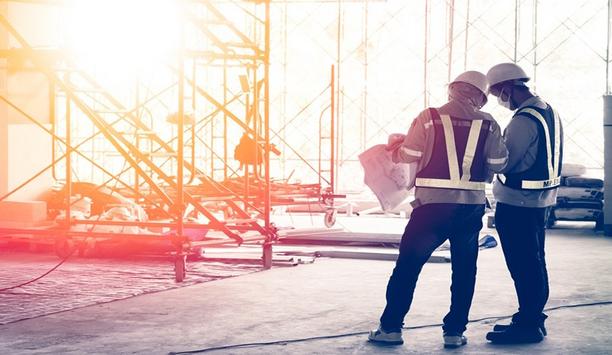
The construction sector has faced heightened scrutiny regarding its handling of fire safety in recent years. 2017’s devastating Grenfell Tower fire, served as a catalyst for...
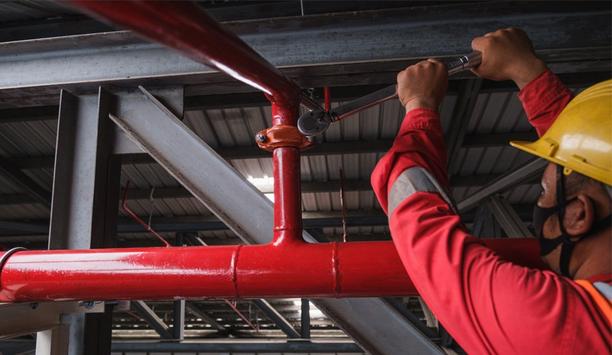
The fifth anniversary of the Grenfell Tower disaster has passed, yet debate surrounding building safety best practice continues. Last year, the UK Government announced steps to fur...
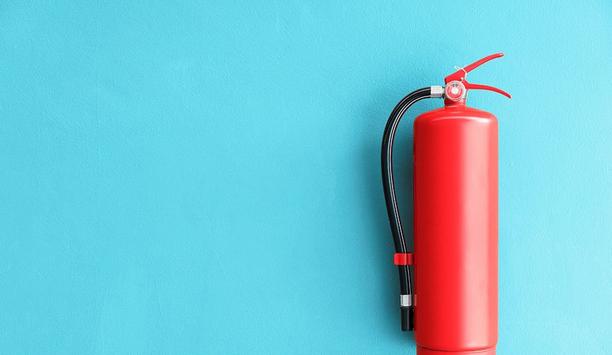
When it comes to investments, fire suppression is the one we hope to never utilize. All too often it acts like a safety blanket, unseen yet always there, a hidden investment policy...
Latest Globe Manufacturing Company, LLC news
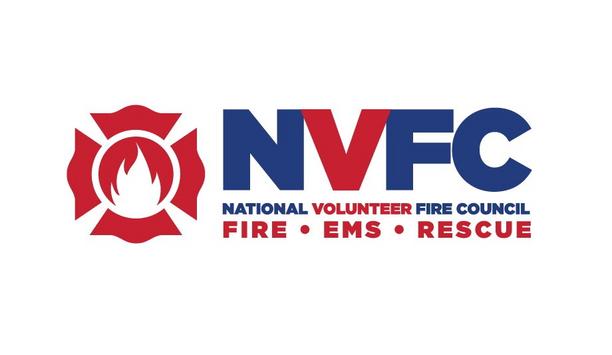
The final three recipients of MSA and DuPont’s 2023 Globe Gear Giveaway, conducted in partnership with the National Volunteer Fire Council (NVFC), have been selected. The Bel...
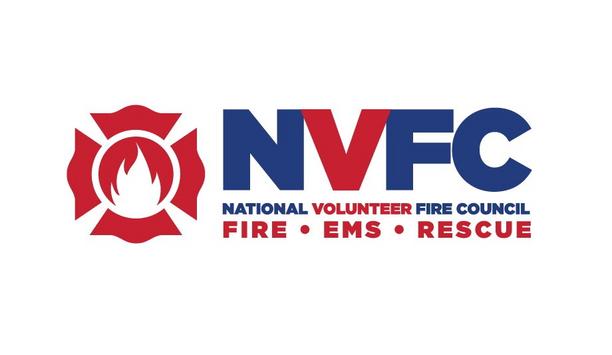
The ability, or lack thereof, to purchase adequate personal protective equipment is a well-known struggle for many volunteer fire departments across the U.S. To help combat...
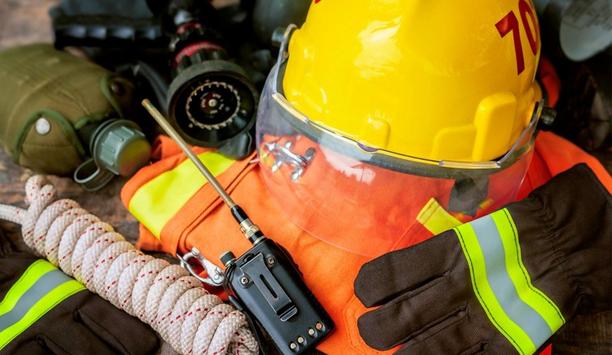
Trends in garments and protective gear for firefighters are evolving to address the changing needs of the fire service. Garments worn by firefighters must be comfortable and allow...
Trending topic articles
SMARTSHOOTER, a world pioneer in fire control systems, will showcase its handheld and remotely controlled SMASH solutions at the DEFEA 2025 defense exhibition in Athens, Greece. The company will pre...
Global safety equipment manufacturer MSA Safety, Inc. announced it has secured a $10 million contract to provide respiratory protective equipment to the Orange County Fire Authorit...
Skills for Security welcomes EFT Group as a new sponsor, further strengthening its mission to develop the next generation of skilled professionals in the fire and security industry. As one of the UK&...
Johnson Controls, the pioneer for smart, healthy, and sustainable buildings, launches the new Simplex 4017ES Fire Alarm Control Unit to help customers meet evolving life safety voice regulations. ...
Hochiki Europe, a manufacturer of innovative life safety solutions, is partnering with Jendee Trading, a global provider with nearly 50 years of experience exporting British electrical and fire safety...
Fire doors are designed to save lives. When closed, they form a crucial barrier against smoke and fire and provide vital time for occupants to escape in an emergency situation. An open fire door on th...
Sabrina Cohen-Hatton has been appointed as the new Chief Fire Officer to lead Hampshire and Isle of Wight Fire and Rescue Service, becoming the organization’s first female chief. Set to s...
Merriman Grange, a beautiful new care home from Cinnamon Care Collection, located in Worthing, West Sussex, is designed to provide a warm, comfortable, and thanks to Hochiki's ESP range, safe environm...
Darley is proud to announce it has been selected as a 2025 US Best Managed Company. Sponsored by Deloitte Private and The Wall Street Journal, the program recognizes outstanding U.S. private companies...
Blackline Safety Corp., a pioneer in connected safety technology, has announced that its new EXO 8 area monitor — the world’s only direct-to-cloud portable area monitor capable of detectin...
The surge in demand seen by the cables industry for Category 3 Control fire performance cables can be met with the supply chains working together, says pioneering cable supplier - AEI Cables. The inc...
Hochiki Europe has brought the thrill of live football to the heart of the Gillingham community, awarding 35 coveted tickets to a Gillingham FC home game to the deserving Medway Soccer Academy. The a...
Oshkosh Airport Products, an Oshkosh Corporation business, announced the delivery of two Oshkosh Airport Products Striker® 6x6 ARFF vehicles to MET – Montreal Metropolitan Airport ...
Fire protection solutions manufacturer, Advanced, has supplied an intelligent fire panel with wireless detection to iconic Scottish knitwear brand Eribé. An Advanced MxPro 5 analog addressable...
Hampshire and Isle of Wight Fire and Rescue Service (HIWFRS) is changing the way it responds to Automatic Fire Alarms in certain types of buildings as of 01 August 2025. Following a public consultati...
SMARTSHOOTER, a world pioneer in fire control systems, will showcase its handheld and remotely controlled SMASH solutions at the DEFEA 2025 defense exhibition in Athens, Greece. The company will pre...
Global safety equipment manufacturer MSA Safety, Inc. announced it has secured a $10 million contract to provide respiratory protective equipment to the Orange County Fire Authorit...
Skills for Security welcomes EFT Group as a new sponsor, further strengthening its mission to develop the next generation of skilled professionals in the fire and security industry. As one of the UK&...
Johnson Controls, the pioneer for smart, healthy, and sustainable buildings, launches the new Simplex 4017ES Fire Alarm Control Unit to help customers meet evolving life safety voice regulations. ...
Hochiki Europe, a manufacturer of innovative life safety solutions, is partnering with Jendee Trading, a global provider with nearly 50 years of experience exporting British electrical and fire safety...
Fire doors are designed to save lives. When closed, they form a crucial barrier against smoke and fire and provide vital time for occupants to escape in an emergency situation. An open fire door on th...
Sabrina Cohen-Hatton has been appointed as the new Chief Fire Officer to lead Hampshire and Isle of Wight Fire and Rescue Service, becoming the organization’s first female chief. Set to s...
Merriman Grange, a beautiful new care home from Cinnamon Care Collection, located in Worthing, West Sussex, is designed to provide a warm, comfortable, and thanks to Hochiki's ESP range, safe environm...
Darley is proud to announce it has been selected as a 2025 US Best Managed Company. Sponsored by Deloitte Private and The Wall Street Journal, the program recognizes outstanding U.S. private companies...
Blackline Safety Corp., a pioneer in connected safety technology, has announced that its new EXO 8 area monitor — the world’s only direct-to-cloud portable area monitor capable of detectin...
The surge in demand seen by the cables industry for Category 3 Control fire performance cables can be met with the supply chains working together, says pioneering cable supplier - AEI Cables. The inc...
Hochiki Europe has brought the thrill of live football to the heart of the Gillingham community, awarding 35 coveted tickets to a Gillingham FC home game to the deserving Medway Soccer Academy. The a...
Oshkosh Airport Products, an Oshkosh Corporation business, announced the delivery of two Oshkosh Airport Products Striker® 6x6 ARFF vehicles to MET – Montreal Metropolitan Airport ...
Fire protection solutions manufacturer, Advanced, has supplied an intelligent fire panel with wireless detection to iconic Scottish knitwear brand Eribé. An Advanced MxPro 5 analog addressable...
Hampshire and Isle of Wight Fire and Rescue Service (HIWFRS) is changing the way it responds to Automatic Fire Alarms in certain types of buildings as of 01 August 2025. Following a public consultati...
SMARTSHOOTER, a world pioneer in fire control systems, will showcase its handheld and remotely controlled SMASH solutions at the DEFEA 2025 defense exhibition in Athens, Greece. The company will pre...
The New Future For Fire Agencies
DownloadThe Eight Key Trends in Fire Detection in 2023
DownloadA Digital Platform to Improve Fire Safety Compliance and Inspections
DownloadOvercoming the Challenges of Fire Safety in the Paper Industry
DownloadCarbon Monoxide: Creeping Killer Caught In The Act
Download