System Sensor Fire Detectors (71)

DescriptionModel 2151 (photoelectric sensor) and model 2151T (photoelectric sensor with th...
Add to CompareBrowse Fire Detectors
- Make
- System Sensor
- Other System Sensor products
- System Sensor Warning Lights & Sirens
- System Sensor Fire Suppression System Accessories
Detector products updated recently
Detectors - Expert Commentary
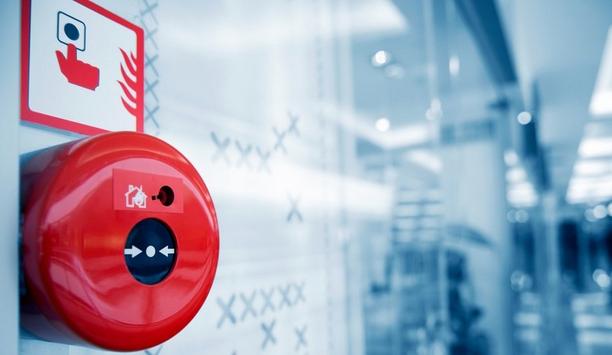
The National Fire Protection Association (NFPA) has developed over 300 codes and standards to support the rapidly changing needs of the fire and life safety industry. NFPA 72, Na...
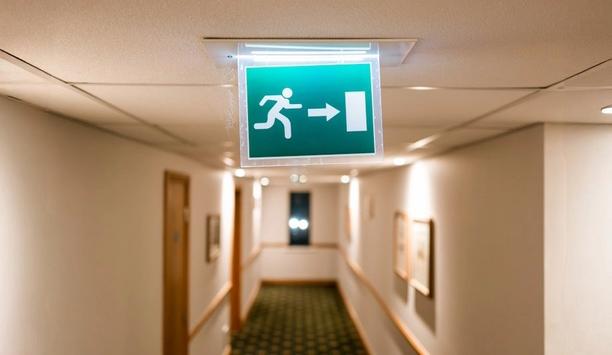
Are people too passive when it comes to fire door safety? Research conducted by the British Woodworking Federation (BWF) in 2022 would suggest so, with a third of the British publi...
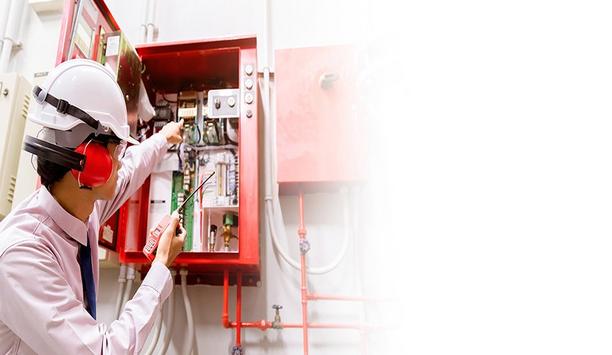
It’s been three years since the National Fire Protection Association (NFPA) published the most recent edition of the wide-ranging standard that spans “the application,...
Latest System Sensor news
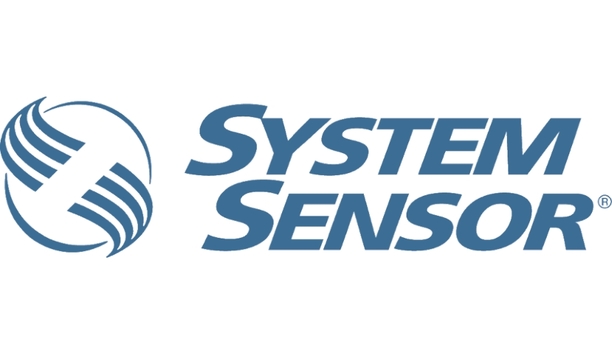
System Sensor is pleased to announce the next phase of our L-Series product line with the availability of low frequency (520 Hz) sounder and sounder strobes. The L-Series offers th...
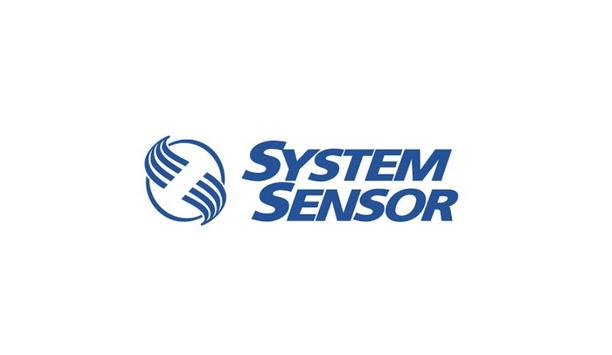
System Sensor is pleased to announce the availability of the CO-REPL, a replacement CO cell for use with i4 Series COSMO-2W and COSMO-4W combination CO/smoke detectors. The i4 Seri...
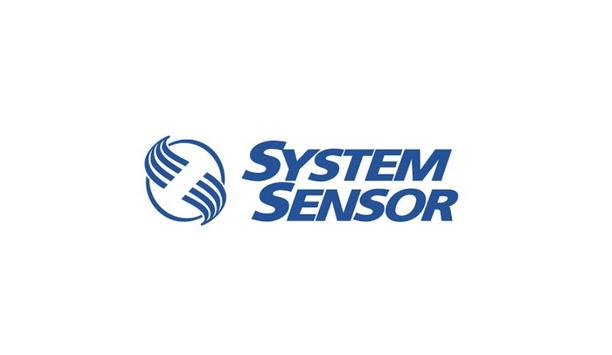
System Sensor is pleased to announce the next evolution in beam smoke detection with the availability of the OSI-R-SS conventional and OSI-RI-SS intelligent single-ended, reflectiv...
Trending topic articles
Fire and Rescue NSW (FRNSW) is further encouraging respectful and honest conversations and the sharing of Traditional Knowledge by opening a Yarning Circle at its training center at Orchard Hills, in...
Responding to reports regarding culture in the fire and rescue service, the National Fire Chiefs Council (NFCC) has reiterated that the behaviors outlined are wholly unacceptable, making it clear ther...
A South Yorkshire recruitment campaign aims to change perceptions of women in the fire service. South Yorkshire Fire & Rescue’s ‘A Firefighter Is A Firefighter’ campaign include...
The Fire Standards Board (FSB) is delighted to announce the launch of two new Fire Standards - Fire Control and Communications & Engagement. The development of the Fire Control Standard was drive...
Gavin Skelly, CEO of growing fire safety industry body - Fire Aware, spoke of the moral and behavioral changes in culture needed to improve standards at the Scotland Housing Leaders’ Summit. He...
Using the highest-rated fire performance cables will help firefighters in the event of a fire in some of the largest new buildings being developed, says pioneering cable supplier AEI Cables. AEI Cabl...
Rescue Intellitech, a pioneering provider of innovative cleaning solutions for the fire and rescue industry, is set to unveil its latest innovation in firefighter PPE care, with the launch of a new li...
Secutech Vietnam 2025 came to a close on 16 August at the Saigon Exhibition and Convention Centre (SECC), after bringing together key stakeholders and buyers from across Vietnam’s security...
WAGNER Group GmbH has once again been awarded for its research and development work. In a decision dated August 11, 2025, the Research Allowance Certification Authority (BSFZ) confirmed the eligibili...
Orr Protection, a provider of mission-critical fire protection solutions, has acquired all of the business assets of Compass Fire Protection, LLC, based in the Seattle, Washington area. The acquisit...
Hochiki Europe, a global pioneer in life safety solutions, has partnered with VOLT EHF, a specialist in electrical and fire alarm systems, to install a comprehensive and scalable fire detection system...
Whether it’s the end of the day or end of term, when schools close, it’s not unusual to see children and staff alike scrambling out the doors as they head for a much needed period of relax...
Sensor solutions provider HENSOLDT will present its latest technological advancements at DSEI 2025 in London from 9 to 12 September 2025. One of HENSOLDT's core competencies is the active and passive...
New Government data of fire and rescue service incidents analyzed by HETAS for Chimney Fire Safety Week (CFSW), reveals that Devon and Somerset Fire and Rescue Service responded to 181 chimney fires o...
Fire and Rescue NSW (FRNSW) investigators are now at the scene of a house fire, which has claimed the lives of two people in Sydney's south-west. Neighbors phoned Triple-Zero (000) around 6:45 am as...
Fire and Rescue NSW (FRNSW) is further encouraging respectful and honest conversations and the sharing of Traditional Knowledge by opening a Yarning Circle at its training center at Orchard Hills, in...
Responding to reports regarding culture in the fire and rescue service, the National Fire Chiefs Council (NFCC) has reiterated that the behaviors outlined are wholly unacceptable, making it clear ther...
A South Yorkshire recruitment campaign aims to change perceptions of women in the fire service. South Yorkshire Fire & Rescue’s ‘A Firefighter Is A Firefighter’ campaign include...
The Fire Standards Board (FSB) is delighted to announce the launch of two new Fire Standards - Fire Control and Communications & Engagement. The development of the Fire Control Standard was drive...
Gavin Skelly, CEO of growing fire safety industry body - Fire Aware, spoke of the moral and behavioral changes in culture needed to improve standards at the Scotland Housing Leaders’ Summit. He...
Using the highest-rated fire performance cables will help firefighters in the event of a fire in some of the largest new buildings being developed, says pioneering cable supplier AEI Cables. AEI Cabl...
Rescue Intellitech, a pioneering provider of innovative cleaning solutions for the fire and rescue industry, is set to unveil its latest innovation in firefighter PPE care, with the launch of a new li...
Secutech Vietnam 2025 came to a close on 16 August at the Saigon Exhibition and Convention Centre (SECC), after bringing together key stakeholders and buyers from across Vietnam’s security...
WAGNER Group GmbH has once again been awarded for its research and development work. In a decision dated August 11, 2025, the Research Allowance Certification Authority (BSFZ) confirmed the eligibili...
Orr Protection, a provider of mission-critical fire protection solutions, has acquired all of the business assets of Compass Fire Protection, LLC, based in the Seattle, Washington area. The acquisit...
Hochiki Europe, a global pioneer in life safety solutions, has partnered with VOLT EHF, a specialist in electrical and fire alarm systems, to install a comprehensive and scalable fire detection system...
Whether it’s the end of the day or end of term, when schools close, it’s not unusual to see children and staff alike scrambling out the doors as they head for a much needed period of relax...
Sensor solutions provider HENSOLDT will present its latest technological advancements at DSEI 2025 in London from 9 to 12 September 2025. One of HENSOLDT's core competencies is the active and passive...
New Government data of fire and rescue service incidents analyzed by HETAS for Chimney Fire Safety Week (CFSW), reveals that Devon and Somerset Fire and Rescue Service responded to 181 chimney fires o...
Fire and Rescue NSW (FRNSW) investigators are now at the scene of a house fire, which has claimed the lives of two people in Sydney's south-west. Neighbors phoned Triple-Zero (000) around 6:45 am as...
Fire and Rescue NSW (FRNSW) is further encouraging respectful and honest conversations and the sharing of Traditional Knowledge by opening a Yarning Circle at its training center at Orchard Hills, in...
The New Future For Fire Agencies
DownloadThe Eight Key Trends in Fire Detection in 2023
DownloadA Digital Platform to Improve Fire Safety Compliance and Inspections
DownloadOvercoming the Challenges of Fire Safety in the Paper Industry
DownloadCarbon Monoxide: Creeping Killer Caught In The Act
Download