Industrieelektronik Polz Firefighting Accessories (3)
Browse Firefighting Accessories
Apparatus and Equipment Accessories products updated recently
Apparatus and Equipment Accessories - Expert Commentary
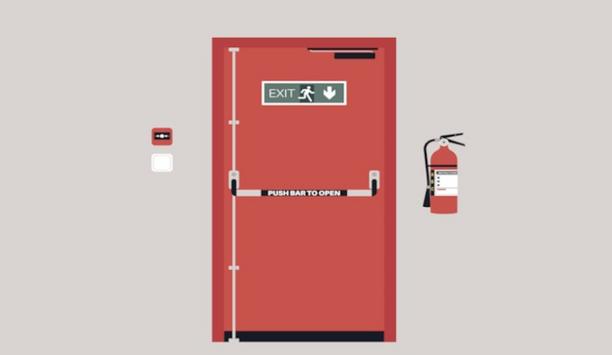
Sue Corrick of Allegion UK explores the evolution of panic and emergency exit hardware, examining the specification and installation points that decision-makers must consider throu...
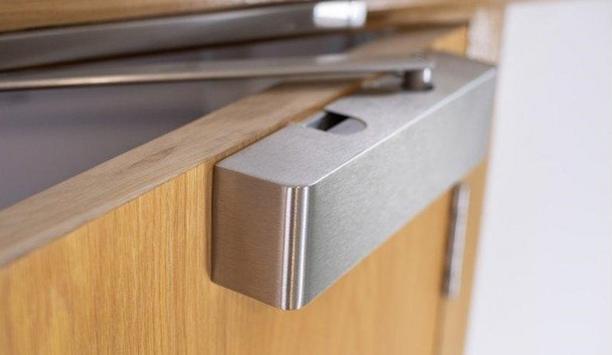
Working fire doors are a prerequisite for fire safety, but what differentiates them from regular doors Kirk Smith of Allegion UK outlines the technical features that form fire-rate...

With new fire safety regulations around the corner and a renewed focus on responsible persons and coordination, Karen Trigg of Allegion UK discusses the significance of fire door h...
The Eight Key Trends in Fire Detection in 2023
DownloadA Digital Platform to Improve Fire Safety Compliance and Inspections
DownloadCarbon Monoxide: Creeping Killer Caught In The Act
DownloadSiemens Webinar: Fire Safety In Parking Garages With E-vehicles
Download