Road Rescue FIRE TRUCKS AND VEHICLES (8)
Browse FIRE TRUCKS AND VEHICLES
Vehicle products updated recently
Vehicles - Expert Commentary
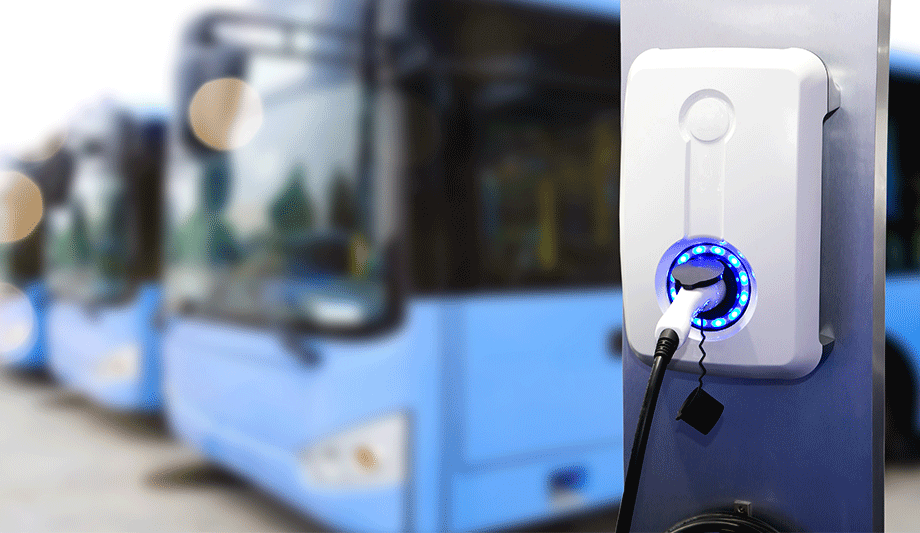
The UK’s electric bus fleet is set to become the largest in Europe by 2024, with numbers projected to grow by almost 180%. Risks associated with fire safety The primary tec...
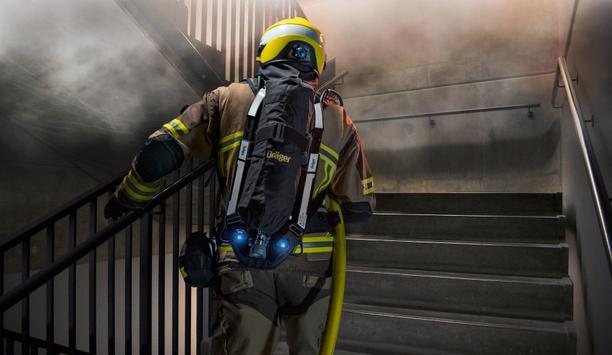
The product lifecycle of self-contained breathing apparatus (SCBA) is approximately ten years, during which time technology inevitably advances considerably in terms of digitizatio...
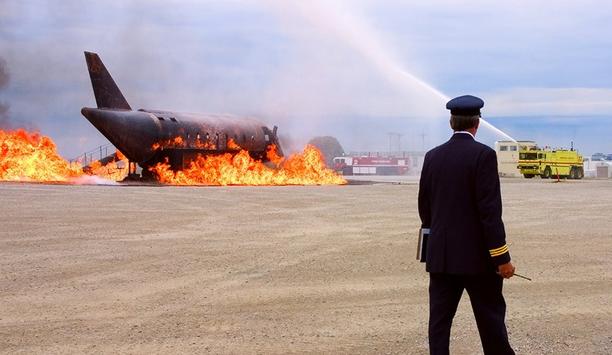
One if the few bonuses of the 2020 COVID-19 Lockdown in the UK was the dramatic reduction of aircraft noise around our homes. Certainly in the Southeast of England, it gave us some...
Latest Road Rescue news
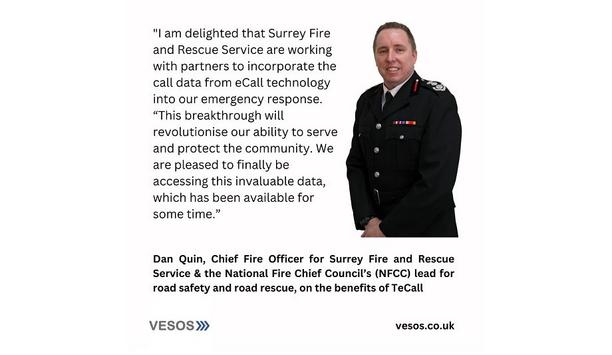
The UK’s pioneer firefighter for road rescue has welcomed the news that real-time road crash data could soon be made available to the emergency services, helping to speed up...
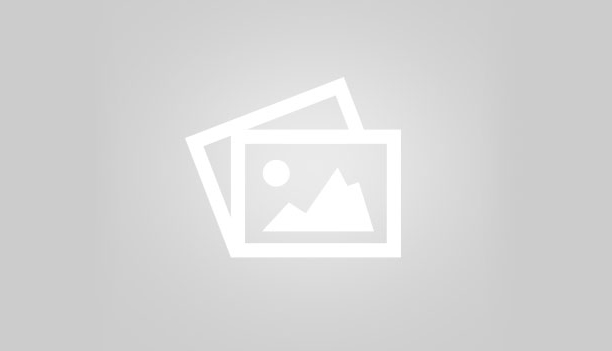
The newly displayed ambulance by Road Rescue is equipped to tackle critical medical situations Built on a Furion Chassis, the New Ambulance Serves as an Eme...
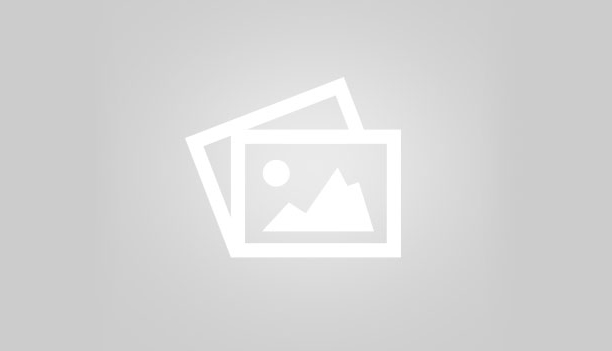
The Road Rescue manufacturing facility in South Carolina Investments in facilities and equipment will increase productivity In a move to strengthen its operat...
Trending topic articles
Perimeter Solutions, a renowned global manufacturer of high-quality fire retardant and firefighting foam concentrates, marked the grand opening of its new PHOS-CHEK facility at McClellan Park in Sacra...
The Engineered Solutions division of Dräger, an international pioneer in the fields of medical and safety technology, has designed a breathing air panel for Staffordshire Fire and Rescue to prote...
INTERSCHUTZ 2026, taking place from 1 to 6 June in Hanover, will be shaped by what many are calling a “turning point”. With eleven months to go before the event starts, strong exhibitor i...
FeuerTrutz 2025 has once again proven itself as the central platform for preventive fire protection. With new formats, a strong congress program and intensive expert discussions, the trade fair p...
Oshkosh Airport Products, an Oshkosh Corporation business, is proud to announce the delivery of three advanced Striker Aircraft Rescue and Fire Fighting (ARFF) vehicles to the Metropolitan Washington...
An upgrade to the Johnson Controls flagship building automation system (BAS), Metasys 14.1 offers a suite of new and enhanced features that answers the need for more comprehensive energy management....
Pierce Manufacturing Inc., an Oshkosh Corporation business, is proud to announce the continued momentum of the 2025 Pierce Road Rally as it nears its midpoint, visiting locations across the United Sta...
Andy Spence, Joint Managing Director of Britannia Fire, the pioneering manufacturer of fire extinguishers in the UK, has addressed the Environmental Audit Committee in the House of Commons. He highli...
Darley, a globally renowned provider of defense, fire, and emergency services equipment, is pleased to announce the appointment of Jim Johnson to its Fire Advisory Board. Jim Johnson brings a wealth o...
QuickFitting highlighted its comprehensive flame-free fitting portfolio, addressing industry data from construction research firm FMI showing construction rework now consumes 12-15% of total North Ame...
Oshkosh Airport Products, an Oshkosh Corporation business, announced the delivery of three new Striker® 8x8 Aircraft Rescue and Firefighting (ARFF) vehicles to serve Minneapolis–St. Paul Int...
Fire detection and life safety specialist, Hispec, has partnered with Vericon Systems, a pioneering manufacturer of remote technologies for essential building services, to enable social housing provid...
Pierce Manufacturing Inc., an Oshkosh Corporation business, is proud to announce Canadian Pierce dealer, Commercial Emergency Equipment Co., has secured an apparatus contract and initial order with th...
With building safety facing more scrutiny than ever before, renowned multi-disciplinary contractor - Miller Knight has secured a place on Fusion21’s £800 million Building Safety and Compli...
Ballyclare, a major designer and manufacturer of firefighter personal protective equipment (PPE), announces a raft of strategic appointments as it focuses on further expansion in the UK market. The f...
Perimeter Solutions, a renowned global manufacturer of high-quality fire retardant and firefighting foam concentrates, marked the grand opening of its new PHOS-CHEK facility at McClellan Park in Sacra...
The Engineered Solutions division of Dräger, an international pioneer in the fields of medical and safety technology, has designed a breathing air panel for Staffordshire Fire and Rescue to prote...
INTERSCHUTZ 2026, taking place from 1 to 6 June in Hanover, will be shaped by what many are calling a “turning point”. With eleven months to go before the event starts, strong exhibitor i...
FeuerTrutz 2025 has once again proven itself as the central platform for preventive fire protection. With new formats, a strong congress program and intensive expert discussions, the trade fair p...
Oshkosh Airport Products, an Oshkosh Corporation business, is proud to announce the delivery of three advanced Striker Aircraft Rescue and Fire Fighting (ARFF) vehicles to the Metropolitan Washington...
An upgrade to the Johnson Controls flagship building automation system (BAS), Metasys 14.1 offers a suite of new and enhanced features that answers the need for more comprehensive energy management....
Pierce Manufacturing Inc., an Oshkosh Corporation business, is proud to announce the continued momentum of the 2025 Pierce Road Rally as it nears its midpoint, visiting locations across the United Sta...
Andy Spence, Joint Managing Director of Britannia Fire, the pioneering manufacturer of fire extinguishers in the UK, has addressed the Environmental Audit Committee in the House of Commons. He highli...
Darley, a globally renowned provider of defense, fire, and emergency services equipment, is pleased to announce the appointment of Jim Johnson to its Fire Advisory Board. Jim Johnson brings a wealth o...
QuickFitting highlighted its comprehensive flame-free fitting portfolio, addressing industry data from construction research firm FMI showing construction rework now consumes 12-15% of total North Ame...
Oshkosh Airport Products, an Oshkosh Corporation business, announced the delivery of three new Striker® 8x8 Aircraft Rescue and Firefighting (ARFF) vehicles to serve Minneapolis–St. Paul Int...
Fire detection and life safety specialist, Hispec, has partnered with Vericon Systems, a pioneering manufacturer of remote technologies for essential building services, to enable social housing provid...
Pierce Manufacturing Inc., an Oshkosh Corporation business, is proud to announce Canadian Pierce dealer, Commercial Emergency Equipment Co., has secured an apparatus contract and initial order with th...
With building safety facing more scrutiny than ever before, renowned multi-disciplinary contractor - Miller Knight has secured a place on Fusion21’s £800 million Building Safety and Compli...
Ballyclare, a major designer and manufacturer of firefighter personal protective equipment (PPE), announces a raft of strategic appointments as it focuses on further expansion in the UK market. The f...
Perimeter Solutions, a renowned global manufacturer of high-quality fire retardant and firefighting foam concentrates, marked the grand opening of its new PHOS-CHEK facility at McClellan Park in Sacra...
The New Future For Fire Agencies
DownloadThe Eight Key Trends in Fire Detection in 2023
DownloadA Digital Platform to Improve Fire Safety Compliance and Inspections
DownloadOvercoming the Challenges of Fire Safety in the Paper Industry
DownloadCarbon Monoxide: Creeping Killer Caught In The Act
Download