Fire Safety Testing
AdvanTec Marine is pleased to announce a major milestone: both its Canadian manufacturing facility in British Columbia and its Oregon, USA facility are now certified to produce fire-rated marine doors. With the Canadian site receiving MED Wheel Mark certification — making it the only such facility in Canada — AdvanTec now proudly holds fire-rated door certifications on both sides of the border. Commitment to safety and innovation New chapter as AdvanTec strengthens its posit...
In September 2024, the UK government announced an extension for the recognition of CE marking on construction products in Great Britain. The sudden change was described as part of a wider strategy to enhance building and fire safety, though, in effectively reversing the previous decision to phase out CE marking, how can the industry ensure it’s moving forward and not simply turning back? Active and passive fire systems Building regulations are paramount in maintaining safety throughout...
Globally renowned provider of testing, inspection, and certification services, SOCOTEC UK and Ireland has announced the acquisition of United Kingdom Testing and Certification (UKTC), a renowned independent fire testing laboratory based in East Kilbride. The strategic acquisition significantly expands SOCOTEC’s capabilities in the critical field of fire safety and compliance, while reinforcing the company’s growing presence in Scotland, with its second acquisition in the country, fo...
Fire and Rescue NSW (FRNSW) crews have door-knocked more than 60 homes at Macquarie Fields, in Sydney’s south-west, in the wake of a devastating house fire in the neighbourhood. On 28 May, 10 people made a narrow and very lucky escape when their two-storey house in Groundsel Avenue went up in flames. FRNSW had installed working smoke alarms in the home just a few days earlier, allowing the mother and her nine children to safely evacuate upon hearing the alert. Alarm testing and provisio...
D-Tools, a major provider of business management software for electronics systems contractors, and FireCAD, powered by Inspect Point, a cloud-based fire alarm CAD solution, are pleased to announce a strategic integration to be unveiled at the 2025 NFPA Conference & Expo. This partnership represents a significant opportunity for fire and security industry professionals, combining D-Tools' end-to-end business management capabilities with FireCAD’s purpose-built tools for fire alarm syst...
Johnson Controls, the global pioneer for smart, healthy, and sustainable buildings, launches Simplex Incident Manager, a complete web-based fire alarm management workstation for campuses and large facilities. This next-generation workstation from Johnson Controls includes an advanced interface and feature set that enhances the fire alarm management experience, helping facility teams keep their buildings protected around the clock. Simplex Incident Manager Simplex Incident Manager gives facili...
News
Renowned fire and life safety solutions manufacturer, Advanced, has won an award at the 2025 Fire & Security Matters (FSM) Awards, recognizing its achievements in fire safety, customer service, innovation, and sustainability. At the ceremony, held at Coventry’s CBS Arena on 5th June, Advanced won the award for Fire Safety Project of the Year, and was also commended in the Fire Safety Manufacturer of the Year category. Modernize fire safety Advanced’s double win at last year’s FSM Awards and mark a significant milestone in its ongoing mission These accolades follow Advanced’s double win at last year’s FSM Awards and mark a significant milestone in its ongoing mission to create a safer, more sustainable future. Advanced’s installation of its AdvancedLive system at Blists Hill Victorian Town earned the company Fire Safety Project of the Year. Delivered in partnership with Chubb Fire & Security, the project showcased how cutting-edge technology can be tailored to meet the challenges of a historically sensitive, multi-structure site. Wireless connectivity, intuitive controls, and a bespoke visual interface helped modernize fire safety across the landmark site without compromising its heritage. Fire system management Meanwhile, the judging panel commended the strength and innovation behind Advanced’s next-generation MxPro 5 fire panel, which played a key role in earning recognition in the Fire Safety Manufacturer of the Year category. Featuring a faster processor, improved configuration speeds, and seamless integration with AdvancedLive, the panel highlights the company’s commitment to smarter, more connected fire system management. Combined with continued investment in product development and responsiveness to market needs, these advancements helped distinguish Advanced in a highly competitive category. R&D and customer support Combined with continued investment in product growth and responsiveness to market needs Commenting on the awards, Advanced Managing Director, Antonio Telesca, said: "To be recognized at this year’s FSM Awards is an incredible achievement and a reflection of the hard work, talent, and passion of our entire team." He adds, "These awards celebrate every department across the business, from R&D and customer support to sustainability and project delivery, and I’d like to thank our customers and partners for their continued trust and support." Innovation and achievement The 2025 FSM Awards brought together over 400 fire and security professionals to celebrate innovation and achievement across the sector. Representing Advanced at the event were Salvy Vittozzi, Phil Calvey, Paul Duffy, Rachael Houghton, Mark Ramshaw, Paul Taylor, Conor MacLeod, and Sarah Yule.
Three veterans of Fire and Rescue NSW (FRNSW) have been recognized in this year’s King’s Birthday honors for their commitment to the fire service and community safety. The Australian Fire Service Medal (AFSM) was established in 1988 to recognize the distinguished service of firefighters – permanent or volunteer – to their organizations. The medals are awarded on the King’s Birthday each year by the Governor-General, on recommendation of Commonwealth and State ministers. major emergency incidents Assistant Commissioner Steer began her firefighting career 28 years ago This year’s recipients are: Assistant Commissioner – Regional Operations, Cheryl Anne Steer. Assistant Commissioner Steer began her firefighting career 28 years ago and has worked her way up the ranks to command Regional Operations for FRNSW. She has consistently demonstrated operational excellence throughout her service and has effectively managed major emergency incidents. Assistant Commissioner Steer continues to mentor and encourage female firefighters through her actions and values-based leadership. Not only is Assistant Commissioner Steer the co-chair of the FRNSW Women’s Inclusive Network (WIN), she is a director of the Relief and Welfare Fund, providing care and assistance to colleagues in need, and a director of the Museum of Fire, where she is helping to document the first 40 years of female firefighters in FRNSW. forefront of significant transformations Chief Superintendent Johnstone has been at the forefront of significant transformations within the service Chief Superintendent – Capability Management, Paul Johnstone. Chief Superintendent Paul Johnstone joined the then-New South Wales Fire Brigades in July 1985 and has shown outstanding leadership, unwavering commitment to community service, and exceptional contributions to the fire service over his 38 years of service. With a long background as a firefighter in inner Sydney, Operational Staffing and HAZMAT/Counter Terrorism, Chief Superintendent Johnstone has been at the forefront of significant transformations within the service. These include enhancing medical capabilities, firefighter training and readiness, and augmenting FRNSW’s In-water rescue capabilities. He has also introduced instrumental improvements in relation to policies, standards and procedures reflecting best practice for FRNSW and he played a pivotal role in the response to the devastating floods of 2021/22. Developing safety initiatives Captain, Paul James Dorin. Corrimal Fire Station Paul Dorin joined FRNSW in July 1993 as an On-Call firefighter and has since consistently demonstrated the values of the organization. Captain Dorin has a passion for helping others and has become a role model for his peers and local community. He has developed many safety initiatives, including the Home Care Disability Fire Safety Program in which he promoted fire safety efforts involving clients and their carers, and this winter’s Smoke Alarm Action Day project, aimed at reducing complacency around fire risks in the home. Beyond his operational duties, Capt. Dorin is a talented cartoonist and has used his artistic abilities to raise funds for research into birth defects and childhood diseases such as cancer, epilepsy, and a range of genetic disorders. outstanding commitment to service FRNSW Commissioner, Jeremy Fewtrell, congratulated the three award recipients for their outstanding commitment to service. “All three firefighters are widely recognised for their exemplary devotion to duty and their “can do” attitudes towards their work,” Commissioner Fewtrell reflected. “They present a professional, thoughtful and caring approach to their duties and they exemplify the values that FRNSW promotes,” he said. “I’m personally very proud of them…they thoroughly deserve the recognition and I thank them for their tremendous efforts to date.” Praising the professionalism Emergency Services Minister, Jihad Dib, said the AFSMs have been awarded to three exceptional role models within the service. “Their professionalism consistently gets the job done, they have earned this recognition through courage and commitment, and I’m very pleased these firefighters are being honoured on the King’s Birthday in this way.”
Over 100 representatives from across Illinois’ fire service organizations recently gathered in Glenview, IL, for the Metropolitan Fire Chiefs Association of Illinois’ 19th Annual Fire Services Home Day, held this year at Northeastern Illinois Public Safety Training Academy (NIPSTA.) The fire professionals were joined by elected officials and staffers from several state and federal offices with 20 fire service vendors displaying key equipment used in the fire service. Paul Darley, President and CEO of Darley, a fire and defense equipment supplier in Itasca, IL, founded and co-chairs the annual event with retired Schiller Park Fire Chief Tom Deegan. Items on Display Various equipment and vehicles were on display during the event Various equipment and vehicles were on display during the event and were all purchased through funds from the Assistance to Firefighters Grant during the past 20 years. The events are held to keep fire service issues in front of Illinois’ federal and state legislators. Assistance to Firefighters Grant Program According to the FAMA (Fire Apparatus Manufacturers’ Association) FEMSA (Fire and Emergency Manufacturers and Services Association) Government Affairs Committee, “The Assistance to Firefighters Grant Program was established by Congress in 2001 to assist communities in equipping our nation’s first responders, including firefighters and EMS personnel.” Local fire departments can apply for grants to purchase new and needed equipment to replace older, outdated equipment that no longer meets the safety standards of the National Fire Protection Association (NFPA). Esteemed Speakers Speakers included James Rivera, Illinois State Fire Marshal (OSFM), Chief Chad Hoefle, President, Illinois Fire Chiefs Association (IFCA), Jill Ramaker, Executive Director, Northeastern Illinois Public Safety Training Academy (NIPSTA), Glenn Ericksen, CEO, Mutual Aid Box Alarm System (MABAS), Kevin Lyne , Section Chief, Mutual Aid Box Alarm System (MABAS), Chief Alan Wax, President, Metropolitan Fire Chiefs Association (MFCA), and Jim Keiken, Director, Illinois Fire Service Institute (IFSI). The Assistance to Firefighters Grant (AFG) This grant ensures that firefighters have access to the necessary tools and resources to perform their duties The Assistance to Firefighters Grant (AFG) program fills essential equipment gaps for approximately 1.1 million first responders nationwide. This grant ensures that firefighters have access to the necessary tools and resources to perform their duties effectively and enhance public safety. The significance of the Staffing for Adequate Fire and Emergency Response (SAFER) program was also stressed. This program is crucial for helping fire departments increase or maintain the number of trained frontline firefighters available in their communities. By supporting the SAFER program, the need to ensure that fire departments are adequately staffed to respond to emergencies and protect the public was emphasized. Federal support for local fire departments The reauthorization of the AFG and SAFER Programs ensure continued federal support for local fire departments, helping them maintain safety and emergency response capabilities. Additionally, funding for fiscal year 2025 has been approved for both the U.S. Fire Administration (USFA) and the Urban Search and Rescue Response System (USAR.) The USFA provides critical training for first responders, maintaining a cutting-edge force prepared for various emergencies. The USAR system is vital for disaster response, deploying specialized units to disasters across the country. Authority comment Jim Keiken, Director of the Illinois Fire Service, spoke highly of the opportunities provided to him in being a resource to so many prospective members of the fire service, but to also be recognized as a training resource in the world. Keiken added,”I get the chance to interact with my peers from across the country and to an extent across the world, and what I've seen is second to none in what we do and the way we do it.”
Rosenbauer America, a pioneer in fire apparatus innovation and performance, announces the initial delivery of new state-of-the-art Tractor Drawn Aerials (TDAs) to the Los Angeles County Fire Department (L.A.Co. FD). In addition, the Los Angeles County Fire will also soon be receiving new Rosenbauer America Engines/Custom Pumpers. Rosenbauer COMMANDER™ cab In total, this order includes: Eleven (11) Tractor Drawn Aerial (TDA) Quints: Built on the Rosenbauer COMMANDER™ custom cab and chassis, these units feature Rosenbauer’s heavy-duty extruded aluminum EXT body, 2000 GPM Waterous pumps, 300-gallon water tanks, and the technologically advanced 100-foot Rosenbauer SMART aerial ladder. The SMART system offers enhanced safety features, operational efficiencies, and precise controls for aerial operations. Eight (8) Engines (aka Custom Pumpers): These rigs are built on the Rosenbauer WARRIOR™ custom cab and chassis with the rugged and durable Rosenbauer extruded aluminum EXT bodies. They are equipped with 1500 GPM Hale pumps, 350 GPM Darley HM350 auxiliary pumps, 500-gallon water tanks, and 30-gallon foam concentrate pumps. The auxiliary pumps enable wildland firefighting capabilities. fire protection and emergency medical services Fire protection and emergency medical favors across a vast and diverse region covering 2,300 square miles Established in 1923, the Los Angeles County Fire Department is one of the largest and busiest fire departments in the United States. It provides vital fire protection and emergency medical services across a vast and diverse region covering over 2,300 square miles, encompassing 59 cities and all unincorporated areas of Los Angeles County, plus the City of La Habra in Orange County. With nearly 5,000 personnel operating out of 177 fire stations, the department protects the lives and property of over 4.1 million residents, responding to more than 400,000 calls for service annually. Integrated SMART aerial system Conducted March 10-13, 2025, at the L.A. County Fire Department Headquarters, the intensive familiarization program utilized the first two Rosenbauer America TDAs delivered under the department's contract. The training brought together over 100 L.A.Co. FD personnel, including approximately 75 firefighters and 30 mechanics. The training was specifically designed to build the department's proficiency in operating the Rosenbauer TDA, with a particular focus on the capabilities and safety features of the integrated SMART aerial system. SMART aerial technology Velocity Fire Equipment has worked closely with LA County and will provide on-going security, service, and parts "The delivery of these initial TDAs and the completion of this comprehensive familiarization training represent a significant milestone for this important project," said Ernie Young, Western Regional Sales Manager for Rosenbauer America. He adds, "Seeing the L.A. County Fire Department personnel quickly adapt to and gain confidence with our SMART aerial technology was incredibly rewarding." From the contract onset, Rosenbauer America’s authorized dealer, Velocity Fire Equipment, has worked closely with LA County and will provide on-going warranty, service, and parts support to Los Angeles County. Collaboration with the Los Angeles County Fire Department "Our partnership and ongoing collaboration with the Los Angeles County Fire Department are something we deeply value," said Tim Noeding, General Manager at Velocity Fire Equipment Sales. He adds, "Working together on this significant order, as well as previous apparatus procurements, allows us to help equip their dedicated personnel with the reliable, high-performance Rosenbauer apparatus they need to serve their vast community effectively."
Armstrong Fluid Technology has expanded its family of Vertical-In-Line Fire Pumps with the addition of the new 750gpm 5x4x10PF model. This new size is available with Design Envelope technology, featuring connected intelligence, performance tracking and automated alerts to support more cost-effective maintenance and better occupant safety. Due to the managed 'ramp-up' of output, there are no pressure spikes on startup, pipes are better protected, water delivery is ensured and the risk of water hammer is reduced. Features Other features include: Reduced on-site work for power cabling Reduction of PRVs and drain lines Elimination of safety issues related to supply pressure Reduced costs for design engineers, contractors and building owners New dimensions and size "This new size of Vertical In-Line fire pump offers excellent performance in a key range of flow and pressure output," said Michael DeMille, Global Offering Manager, Fire Pumps at Armstrong. He adds, "And with the addition of Design Envelope technology, customers can enjoy the security of performance tracking throughout the lifecycle of the pump."
Fire and Rescue NSW (FRNSW) firefighters and administration staff have raised a staggering amount of donations for children suffering serious burns. The volunteer fundraisers today presented a cheque for $215,406 to the Sydney Children’s Hospitals Foundation (SCHF) at FRNSW’s official number ‘002’ Station, The Burns Unit at The Children’s Hospital at Westmead. The significant total is the culmination of year-long efforts by FRNSW’s ‘Beat the Burn’ volunteer group, including dozens of public fundraising events such as the group’s annual five-day event in Jindabyne that allows fundraisers to cycle, mountain bike, run, hike and paddle for the cause. Authority comment FRNSW Commissioner, Jeremy Fewtrell AFSM, said he is proud of the dedication and effort his people have shown to ease the burden for the kids. “Since 2006, ‘Beat the Burn’, formerly known as ‘400in4’, has raised over $1.3 million for the children in the Burns Unit,” Commissioner Fewtrell said. “This year’s fundraising total is the highest ever for ‘Beat the Burn,” he said. “These consistent and mammoth fundraising efforts just go to show that community truly is at the heart of what we do.” SCHF and FRNSW Collaboration SCHF works in collaboration with FRNSW’s ‘Beat the Burn’ volunteers to determine fund allocation SCHF works in collaboration with FRNSW’s ‘Beat the Burn’ volunteers to determine fund allocation and ensure the money raised is as impactful as possible. FRNSW Station Officer and Beat the Burn committee member, Daniel Austin, said the vision is for this year’s funds to go towards upskilling the nurses, allied health professionals and doctors who work across SCHF’s nine ‘Step Down’ clinics across the state. Equitable burn care for kids “It's our intention that the 2024 fundraising efforts go towards bringing staff from regional clinics to Sydney for tailored, in-depth training and up-skilling,” Station Officer Austin said. “The purpose of this training is to strengthen connections and referral pathways with the tertiary Burns Unit at The Children’s Hospital at Westmead, upskill regional staff with burns care skills to capacity build local clinicians and burns centres." “All of this is to ensure that kids in NSW get equitable burns care, regardless of their postcode," he added. “This would remove the need for excessive travel to Westmead, no doubt easing the burden on many families across the state.” ‘Beat the Burn’ fundraising In previous years, ‘Beat the Burn’ fundraising has paid the wages of a specialist burns anaesthetist In previous years, ‘Beat the Burn’ fundraising has paid the wages of a specialist burns anaesthetist, burns physiotherapists, and a research manager, plus funded equipment such as a laser machine that immediately identifies the depth of a burn, allowing for fast and tailored treatment options. SCHF's Chief Product and Impact Officer, Yvonne Stewart, said the generosity of FRSNW staff and their families will continue making a positive difference to the lives of the children and families cared for by the Sydney Children’s Hospitals Network. “For some kids, childhood is far from what it should be,” Stewart said. “Instead of playdates, there are appointments, instead of sleepovers, there are stays, instead of firsts, there can be lasts,” She added. “No child should have to go through this, but those who do deserve our all. Thanks to FRNSW’s support, we will continue having both immediate effect and long-term impact on the lives and treatment of New South Wales’s injured and ill children.”
Renowned fire and life safety solutions manufacturer, Advanced, has won an award at the 2025 Fire & Security Matters (FSM) Awards, recognizing its achievements in fire safety, customer service, innovation, and sustainability. At the ceremony, held at Coventry’s CBS Arena on 5th June, Advanced won the award for Fire Safety Project of the Year, and was also commended in the Fire Safety Manufacturer of the Year category. Modernize fire safety Advanced’s double win at last year’s FSM Awards and mark a significant milestone in its ongoing mission These accolades follow Advanced’s double win at last year’s FSM Awards and mark a significant milestone in its ongoing mission to create a safer, more sustainable future. Advanced’s installation of its AdvancedLive system at Blists Hill Victorian Town earned the company Fire Safety Project of the Year. Delivered in partnership with Chubb Fire & Security, the project showcased how cutting-edge technology can be tailored to meet the challenges of a historically sensitive, multi-structure site. Wireless connectivity, intuitive controls, and a bespoke visual interface helped modernize fire safety across the landmark site without compromising its heritage. Fire system management Meanwhile, the judging panel commended the strength and innovation behind Advanced’s next-generation MxPro 5 fire panel, which played a key role in earning recognition in the Fire Safety Manufacturer of the Year category. Featuring a faster processor, improved configuration speeds, and seamless integration with AdvancedLive, the panel highlights the company’s commitment to smarter, more connected fire system management. Combined with continued investment in product development and responsiveness to market needs, these advancements helped distinguish Advanced in a highly competitive category. R&D and customer support Combined with continued investment in product growth and responsiveness to market needs Commenting on the awards, Advanced Managing Director, Antonio Telesca, said: "To be recognized at this year’s FSM Awards is an incredible achievement and a reflection of the hard work, talent, and passion of our entire team." He adds, "These awards celebrate every department across the business, from R&D and customer support to sustainability and project delivery, and I’d like to thank our customers and partners for their continued trust and support." Innovation and achievement The 2025 FSM Awards brought together over 400 fire and security professionals to celebrate innovation and achievement across the sector. Representing Advanced at the event were Salvy Vittozzi, Phil Calvey, Paul Duffy, Rachael Houghton, Mark Ramshaw, Paul Taylor, Conor MacLeod, and Sarah Yule.
Three veterans of Fire and Rescue NSW (FRNSW) have been recognized in this year’s King’s Birthday honors for their commitment to the fire service and community safety. The Australian Fire Service Medal (AFSM) was established in 1988 to recognize the distinguished service of firefighters – permanent or volunteer – to their organizations. The medals are awarded on the King’s Birthday each year by the Governor-General, on recommendation of Commonwealth and State ministers. major emergency incidents Assistant Commissioner Steer began her firefighting career 28 years ago This year’s recipients are: Assistant Commissioner – Regional Operations, Cheryl Anne Steer. Assistant Commissioner Steer began her firefighting career 28 years ago and has worked her way up the ranks to command Regional Operations for FRNSW. She has consistently demonstrated operational excellence throughout her service and has effectively managed major emergency incidents. Assistant Commissioner Steer continues to mentor and encourage female firefighters through her actions and values-based leadership. Not only is Assistant Commissioner Steer the co-chair of the FRNSW Women’s Inclusive Network (WIN), she is a director of the Relief and Welfare Fund, providing care and assistance to colleagues in need, and a director of the Museum of Fire, where she is helping to document the first 40 years of female firefighters in FRNSW. forefront of significant transformations Chief Superintendent Johnstone has been at the forefront of significant transformations within the service Chief Superintendent – Capability Management, Paul Johnstone. Chief Superintendent Paul Johnstone joined the then-New South Wales Fire Brigades in July 1985 and has shown outstanding leadership, unwavering commitment to community service, and exceptional contributions to the fire service over his 38 years of service. With a long background as a firefighter in inner Sydney, Operational Staffing and HAZMAT/Counter Terrorism, Chief Superintendent Johnstone has been at the forefront of significant transformations within the service. These include enhancing medical capabilities, firefighter training and readiness, and augmenting FRNSW’s In-water rescue capabilities. He has also introduced instrumental improvements in relation to policies, standards and procedures reflecting best practice for FRNSW and he played a pivotal role in the response to the devastating floods of 2021/22. Developing safety initiatives Captain, Paul James Dorin. Corrimal Fire Station Paul Dorin joined FRNSW in July 1993 as an On-Call firefighter and has since consistently demonstrated the values of the organization. Captain Dorin has a passion for helping others and has become a role model for his peers and local community. He has developed many safety initiatives, including the Home Care Disability Fire Safety Program in which he promoted fire safety efforts involving clients and their carers, and this winter’s Smoke Alarm Action Day project, aimed at reducing complacency around fire risks in the home. Beyond his operational duties, Capt. Dorin is a talented cartoonist and has used his artistic abilities to raise funds for research into birth defects and childhood diseases such as cancer, epilepsy, and a range of genetic disorders. outstanding commitment to service FRNSW Commissioner, Jeremy Fewtrell, congratulated the three award recipients for their outstanding commitment to service. “All three firefighters are widely recognised for their exemplary devotion to duty and their “can do” attitudes towards their work,” Commissioner Fewtrell reflected. “They present a professional, thoughtful and caring approach to their duties and they exemplify the values that FRNSW promotes,” he said. “I’m personally very proud of them…they thoroughly deserve the recognition and I thank them for their tremendous efforts to date.” Praising the professionalism Emergency Services Minister, Jihad Dib, said the AFSMs have been awarded to three exceptional role models within the service. “Their professionalism consistently gets the job done, they have earned this recognition through courage and commitment, and I’m very pleased these firefighters are being honoured on the King’s Birthday in this way.”
Over 100 representatives from across Illinois’ fire service organizations recently gathered in Glenview, IL, for the Metropolitan Fire Chiefs Association of Illinois’ 19th Annual Fire Services Home Day, held this year at Northeastern Illinois Public Safety Training Academy (NIPSTA.) The fire professionals were joined by elected officials and staffers from several state and federal offices with 20 fire service vendors displaying key equipment used in the fire service. Paul Darley, President and CEO of Darley, a fire and defense equipment supplier in Itasca, IL, founded and co-chairs the annual event with retired Schiller Park Fire Chief Tom Deegan. Items on Display Various equipment and vehicles were on display during the event Various equipment and vehicles were on display during the event and were all purchased through funds from the Assistance to Firefighters Grant during the past 20 years. The events are held to keep fire service issues in front of Illinois’ federal and state legislators. Assistance to Firefighters Grant Program According to the FAMA (Fire Apparatus Manufacturers’ Association) FEMSA (Fire and Emergency Manufacturers and Services Association) Government Affairs Committee, “The Assistance to Firefighters Grant Program was established by Congress in 2001 to assist communities in equipping our nation’s first responders, including firefighters and EMS personnel.” Local fire departments can apply for grants to purchase new and needed equipment to replace older, outdated equipment that no longer meets the safety standards of the National Fire Protection Association (NFPA). Esteemed Speakers Speakers included James Rivera, Illinois State Fire Marshal (OSFM), Chief Chad Hoefle, President, Illinois Fire Chiefs Association (IFCA), Jill Ramaker, Executive Director, Northeastern Illinois Public Safety Training Academy (NIPSTA), Glenn Ericksen, CEO, Mutual Aid Box Alarm System (MABAS), Kevin Lyne , Section Chief, Mutual Aid Box Alarm System (MABAS), Chief Alan Wax, President, Metropolitan Fire Chiefs Association (MFCA), and Jim Keiken, Director, Illinois Fire Service Institute (IFSI). The Assistance to Firefighters Grant (AFG) This grant ensures that firefighters have access to the necessary tools and resources to perform their duties The Assistance to Firefighters Grant (AFG) program fills essential equipment gaps for approximately 1.1 million first responders nationwide. This grant ensures that firefighters have access to the necessary tools and resources to perform their duties effectively and enhance public safety. The significance of the Staffing for Adequate Fire and Emergency Response (SAFER) program was also stressed. This program is crucial for helping fire departments increase or maintain the number of trained frontline firefighters available in their communities. By supporting the SAFER program, the need to ensure that fire departments are adequately staffed to respond to emergencies and protect the public was emphasized. Federal support for local fire departments The reauthorization of the AFG and SAFER Programs ensure continued federal support for local fire departments, helping them maintain safety and emergency response capabilities. Additionally, funding for fiscal year 2025 has been approved for both the U.S. Fire Administration (USFA) and the Urban Search and Rescue Response System (USAR.) The USFA provides critical training for first responders, maintaining a cutting-edge force prepared for various emergencies. The USAR system is vital for disaster response, deploying specialized units to disasters across the country. Authority comment Jim Keiken, Director of the Illinois Fire Service, spoke highly of the opportunities provided to him in being a resource to so many prospective members of the fire service, but to also be recognized as a training resource in the world. Keiken added,”I get the chance to interact with my peers from across the country and to an extent across the world, and what I've seen is second to none in what we do and the way we do it.”
Rosenbauer America, a pioneer in fire apparatus innovation and performance, announces the initial delivery of new state-of-the-art Tractor Drawn Aerials (TDAs) to the Los Angeles County Fire Department (L.A.Co. FD). In addition, the Los Angeles County Fire will also soon be receiving new Rosenbauer America Engines/Custom Pumpers. Rosenbauer COMMANDER™ cab In total, this order includes: Eleven (11) Tractor Drawn Aerial (TDA) Quints: Built on the Rosenbauer COMMANDER™ custom cab and chassis, these units feature Rosenbauer’s heavy-duty extruded aluminum EXT body, 2000 GPM Waterous pumps, 300-gallon water tanks, and the technologically advanced 100-foot Rosenbauer SMART aerial ladder. The SMART system offers enhanced safety features, operational efficiencies, and precise controls for aerial operations. Eight (8) Engines (aka Custom Pumpers): These rigs are built on the Rosenbauer WARRIOR™ custom cab and chassis with the rugged and durable Rosenbauer extruded aluminum EXT bodies. They are equipped with 1500 GPM Hale pumps, 350 GPM Darley HM350 auxiliary pumps, 500-gallon water tanks, and 30-gallon foam concentrate pumps. The auxiliary pumps enable wildland firefighting capabilities. fire protection and emergency medical services Fire protection and emergency medical favors across a vast and diverse region covering 2,300 square miles Established in 1923, the Los Angeles County Fire Department is one of the largest and busiest fire departments in the United States. It provides vital fire protection and emergency medical services across a vast and diverse region covering over 2,300 square miles, encompassing 59 cities and all unincorporated areas of Los Angeles County, plus the City of La Habra in Orange County. With nearly 5,000 personnel operating out of 177 fire stations, the department protects the lives and property of over 4.1 million residents, responding to more than 400,000 calls for service annually. Integrated SMART aerial system Conducted March 10-13, 2025, at the L.A. County Fire Department Headquarters, the intensive familiarization program utilized the first two Rosenbauer America TDAs delivered under the department's contract. The training brought together over 100 L.A.Co. FD personnel, including approximately 75 firefighters and 30 mechanics. The training was specifically designed to build the department's proficiency in operating the Rosenbauer TDA, with a particular focus on the capabilities and safety features of the integrated SMART aerial system. SMART aerial technology Velocity Fire Equipment has worked closely with LA County and will provide on-going security, service, and parts "The delivery of these initial TDAs and the completion of this comprehensive familiarization training represent a significant milestone for this important project," said Ernie Young, Western Regional Sales Manager for Rosenbauer America. He adds, "Seeing the L.A. County Fire Department personnel quickly adapt to and gain confidence with our SMART aerial technology was incredibly rewarding." From the contract onset, Rosenbauer America’s authorized dealer, Velocity Fire Equipment, has worked closely with LA County and will provide on-going warranty, service, and parts support to Los Angeles County. Collaboration with the Los Angeles County Fire Department "Our partnership and ongoing collaboration with the Los Angeles County Fire Department are something we deeply value," said Tim Noeding, General Manager at Velocity Fire Equipment Sales. He adds, "Working together on this significant order, as well as previous apparatus procurements, allows us to help equip their dedicated personnel with the reliable, high-performance Rosenbauer apparatus they need to serve their vast community effectively."
Armstrong Fluid Technology has expanded its family of Vertical-In-Line Fire Pumps with the addition of the new 750gpm 5x4x10PF model. This new size is available with Design Envelope technology, featuring connected intelligence, performance tracking and automated alerts to support more cost-effective maintenance and better occupant safety. Due to the managed 'ramp-up' of output, there are no pressure spikes on startup, pipes are better protected, water delivery is ensured and the risk of water hammer is reduced. Features Other features include: Reduced on-site work for power cabling Reduction of PRVs and drain lines Elimination of safety issues related to supply pressure Reduced costs for design engineers, contractors and building owners New dimensions and size "This new size of Vertical In-Line fire pump offers excellent performance in a key range of flow and pressure output," said Michael DeMille, Global Offering Manager, Fire Pumps at Armstrong. He adds, "And with the addition of Design Envelope technology, customers can enjoy the security of performance tracking throughout the lifecycle of the pump."
Fire and Rescue NSW (FRNSW) firefighters and administration staff have raised a staggering amount of donations for children suffering serious burns. The volunteer fundraisers today presented a cheque for $215,406 to the Sydney Children’s Hospitals Foundation (SCHF) at FRNSW’s official number ‘002’ Station, The Burns Unit at The Children’s Hospital at Westmead. The significant total is the culmination of year-long efforts by FRNSW’s ‘Beat the Burn’ volunteer group, including dozens of public fundraising events such as the group’s annual five-day event in Jindabyne that allows fundraisers to cycle, mountain bike, run, hike and paddle for the cause. Authority comment FRNSW Commissioner, Jeremy Fewtrell AFSM, said he is proud of the dedication and effort his people have shown to ease the burden for the kids. “Since 2006, ‘Beat the Burn’, formerly known as ‘400in4’, has raised over $1.3 million for the children in the Burns Unit,” Commissioner Fewtrell said. “This year’s fundraising total is the highest ever for ‘Beat the Burn,” he said. “These consistent and mammoth fundraising efforts just go to show that community truly is at the heart of what we do.” SCHF and FRNSW Collaboration SCHF works in collaboration with FRNSW’s ‘Beat the Burn’ volunteers to determine fund allocation SCHF works in collaboration with FRNSW’s ‘Beat the Burn’ volunteers to determine fund allocation and ensure the money raised is as impactful as possible. FRNSW Station Officer and Beat the Burn committee member, Daniel Austin, said the vision is for this year’s funds to go towards upskilling the nurses, allied health professionals and doctors who work across SCHF’s nine ‘Step Down’ clinics across the state. Equitable burn care for kids “It's our intention that the 2024 fundraising efforts go towards bringing staff from regional clinics to Sydney for tailored, in-depth training and up-skilling,” Station Officer Austin said. “The purpose of this training is to strengthen connections and referral pathways with the tertiary Burns Unit at The Children’s Hospital at Westmead, upskill regional staff with burns care skills to capacity build local clinicians and burns centres." “All of this is to ensure that kids in NSW get equitable burns care, regardless of their postcode," he added. “This would remove the need for excessive travel to Westmead, no doubt easing the burden on many families across the state.” ‘Beat the Burn’ fundraising In previous years, ‘Beat the Burn’ fundraising has paid the wages of a specialist burns anaesthetist In previous years, ‘Beat the Burn’ fundraising has paid the wages of a specialist burns anaesthetist, burns physiotherapists, and a research manager, plus funded equipment such as a laser machine that immediately identifies the depth of a burn, allowing for fast and tailored treatment options. SCHF's Chief Product and Impact Officer, Yvonne Stewart, said the generosity of FRSNW staff and their families will continue making a positive difference to the lives of the children and families cared for by the Sydney Children’s Hospitals Network. “For some kids, childhood is far from what it should be,” Stewart said. “Instead of playdates, there are appointments, instead of sleepovers, there are stays, instead of firsts, there can be lasts,” She added. “No child should have to go through this, but those who do deserve our all. Thanks to FRNSW’s support, we will continue having both immediate effect and long-term impact on the lives and treatment of New South Wales’s injured and ill children.”


Expert Commentary
Building safety has always been an ever-evolving landscape of legislation and regulatory frameworks. The industry strives for stronger construction safety practice and in doing so, the need for reliable, transparent and accessible product information is clear - especially when fire door safety compliance is on the line. It was in response to the Grenfell Tower fire and Dame Judith Hackitt’s review that the Building Safety Act 2022 was passed, which has since looked to introduce a number of ground-breaking reforms to improve fire safety standards and facilitate greater accountability across the board. Fire and structural safety information A key component of the regulation has been the need for duty holders to retain fire and structural safety information A key component of the regulation has been the requirement for duty holders to retain fire and structural safety information, making it necessary to manage an accessible digital record of decisions and updates throughout a building’s lifecycle. This "Golden Thread of Information," as it’s known, has placed a renewed focus on the presentation and management of construction product information and ensures the right people have the right information at the right time. Driving standards and saving lives From a single source, building owners, developers, regulators, and residents are given a greater understanding of the materials and assets used during the construction process, as a way of driving standards and saving lives. With emphasis shifting from product performance claims to verified, traceable assurances, there has never been a better time to assure peace of mind when it comes to fire door safety. Fire door confidence The Building Safety Act recognizes the importance of fire safety systems and mandates that the Golden Thread of Information must include comprehensive data on all fire detection and prevention systems in high-risk buildings, including fire doors. As a vital element of passive fire protection, fire doors and their hardware are often the first line of defense As a vital element of passive fire protection, fire doors and their hardware are often the first line of defence against fire and smoke, and as such are a legal requirement in all non-domestic properties and houses in multiple occupation. To operate as intended, fire doors will call on their various hardware components, including hinges, latches, seals, door closers and opening mechanisms, meaning they are only as effective as the weakest link in their assembly. Maintenance of fire door hardware is key As such, the correct specification, installation, and maintenance of fire door hardware is considered crucial if a building is to meet both its functional and safety standards. With that, decision makers must be confident they can identify the necessary hardware for their building, and in doing so, must also ensure components are fit for purpose and comply with UK Construction Products Regulations. UKCA and CE certifications To assist duty holders in meeting these expectations, conscious manufacturers have stepped up, and as part of the Golden Thread regulatory framework are providing more detailed information in the form of product datasheets, installation guides, and training portals. From a compliance standpoint, decision makers can instantly check a product’s associated Declaration of Performance (DOPs) to show hardware conforms to the correct testing standards and UKCA and CE certifications, as well as Environmental Product Declarations (EPDs) when looking to conform to the latest environmental benchmarks. With this information, those involved in product selection can assure their installed fire door hardware will perform when it is called upon. Transparent product information Transparent product information is also useful when it comes to maintenance periods Transparent product information is also useful when it comes to maintenance periods and conforming to Approved Document B, with amendments made as recently as March 2025 focusing on Regulation 38, which states that “the person carrying out the work shall give fire safety information to the responsible person no later than the date of the completion of the work, or the date of occupation”. By providing this material, manufacturers are offering improved traceability on products and their performance, empowering duty holders to comply with legal obligations and keeping occupants safe in the process. Transparency equals opportunity Data is a critical resource in decision making and with several schemes evolving such as the Golden Thread and the Code for Construction Product Information, a real strategy is forming. Where information is accessible and no longer ambiguous, the industry is fostering a proactive culture of collaboration, further transitioning from reactive compliance-driven tasks to a more effective method for tackling fire door safety and building design as a whole. Latest standards and hardware options Outside of duty holders being able to demonstrate compliance by showing how they are managing risks throughout their buildings, there is perhaps a greater opportunity presented with clear communication among stakeholders. Outside of duty holders being able to reveal compliance by showing how they are managing risks Where it’s imperative for industry professionals to remain informed on the latest standards and hardware options, a collaborative approach can lead to better and more informed design choices that continue to deliver post-project delivery and improve fire safety outcomes. Furthermore, with information readily available, there is an opportunity for early identification of potential hazards and vulnerabilities. For existing projects, decision makers can check what hardware product has been used and where, deciding if it has been suitable and further reducing the use of ineffective options and avoiding costly retrofits when the time has come to repair or replace products. Fire door safety products From an operational perspective, when reliable product information can be accessed and assessed instantaneously, duty holders are able to streamline their decisions-assuring any changes or issues with fire door safety products are rectified quickly and actioned efficiently. The Golden Thread is setting the standard and protecting all stakeholders in the process With this holistic approach to information sharing, building and fire safety management becomes a shared duty. The Golden Thread is setting the standard and protecting all stakeholders in the process - helping to build trust in an area it is most needed. The use of traceable and transparent product information means the approach to fire door safety and building management is changing and the industry is urged to continue building upon this culture while navigating the latest standards. Traceability is no longer a burden of best practice-it’s an industry expectation and equally, a golden opportunity that must not be missed. How Allegion UK Can Help Allegion UK is committed to supporting transparency and traceability in construction and has a wealth of product information resources to help professionals undertake product selection, installation, and maintenance checks on fire doors and hardware. For information on product selection and installation, please speak to experts or head to the download center for technical fitting instructions and product certifications. Allegion UK also proactively participates in the EPD program, with full EPD documentation available for download on Briton products, based on ISO 14025 and EN 15804 environmental declarations, from the Allegion and Briton websites.
Fire doors are designed to save lives. When closed, they form a crucial barrier against smoke and fire and provide vital time for occupants to escape in an emergency situation. An open fire door on the other hand is rendered useless in the event of a fire, and for this reason, fire door closers are equally recognized for their life-saving capabilities. The relationship between fire doors and fire door closers is synergetic in fact, with both considered key elements of a building’s passive fire protection system. When a fire door must close to completion during a fire incident, it will always rely on its mechanical closing device to do so effectively. Door closers - essential operational component Door closers are an essential operational component and must be capable of closing the door leaf from any angle of opening and strong enough to overcome the resistance of any latch seal, ensuring the door is held firmly in place by its frame. Specifiers and decision makers alike must be confident in their door closer selection While all fire door closers serve this same function, decision makers are reminded that an incorrectly specified door closer can compromise the integrity of an entire fire door assembly. With different project requirements and hardware options available, specifiers and decision makers alike must be confident in their door closer selection. Where occupant safety is on the line, what should specification teams look out for? Fire door closers are key to fire door safety Kirk Smith of Allegion UK, explains: “Fire door closers are paramount to the success of fire door safety and specification should be a structured process to ensure appropriate closers are chosen at each touchpoint.” He adds, “There are various types of door closers available on the market, but whether concealed or surface-mounted, all controlled door closer models use spring hydraulics to close and engage fire doors onto their latch, allowing buildings to compartmentalize areas and provide occupants with vital escape routes. To perform this task, fire door closers call upon a number of elements including: the door closer mechanism, mounting hardware, arms and links.” Door closers tested to EN 1634, UKCA, CE standards Kirk Smith continues, “There are often a number of considerations to make when choosing between door closer products. In any instance, specifiers must first establish whether their door is a fire door or a non-fire door, for example. To ensure a closer is fit for purpose and meets fire safety compliance, all door closers installed on fire-rated doors must be tested to EN 1634 and UKCA and CE marked.” He further states, “Mechanical variants must also conform to EN 1154 and electromagnetic hold-open devices to EN 1155, which test and classify hardware over its category of use, number of test cycles, power size, fire behavior, safety and corrosion resistance. A Declaration of Performance (DoP) must also be reviewed to ensure a door closer is certified when fitted with backcheck or delayed action.” Kirk Smith adds, “From an operational viewpoint, it’s important that a chosen door closer meets the needs of a building and its users too. Buildings with high footfall will often benefit from an electromagnetic hold-open device, which keep certain fire doors open until a fire alarm is activated, in which the system will automatically release and close doors to completion.” Surface mounted closers are the most durable and common type of door closer Selecting the most appropriate door closer Kirk Smith continues, “The size of a door can sometimes be a key factor when selecting a door closer too. Unusually tall or heavy doors may often require a door closer with a higher power size, in accordance with EN 1154 - it’s key to remember that fire doors require a minimum Power Size EN 3 to conform to this standard.” He adds, “Should a specification team be unsure about the size of the door, it is often best practice to choose a door closer unit that can be adjusted during the installation stage.” Durable in application Regardless of where a fire door may be positioned, operation must always be controlled Regardless of where a fire door may be positioned, its size or how it may be used, operation must always be controlled, as this will prevent future damage to the door and its frame - which can be a crucial step towards retaining fire safety performance. Kirk Smith continues: “Surface mounted closers are the most durable and common type of door closer, with units mounted to the surface of the door or frame with a quick and simple installation process. Comparably, concealed door closers are fitted within the door leaf and frame and while providing the functionality of a surface mounted closer is hidden from view as a way of enhancing aesthetics.” Most common ways to fit a door closer Kirk Smith adds, “When reviewing the mounting requirements, it’s important to consider door closers can be installed in different ways, often depending on the application.” The four most common ways to fit a door closer are: Figure 1 door mount fixing: where the closer body is mounted on the pull face of the door Figure 61 transom mount push side: where the closer body is mounted on the transom, on the push side of the door Figure 66 parallel mount push side: where the closer body is mounted on the push side of the door Slide track fixing: where the closer with slide arm and track is door or transom mounted, on either the pull or push side of the door Door closers with adjustable backcheck Kirk Smith states, “Specifiers must also evaluate whether backcheck control is necessary. Door closers with adjustable backcheck can better control the speed of the door, slowing it down prior to making contact with a door stop or before reaching the fully open position. This function prevents or minimizes damage to the door, hardware and adjacent walls, which would otherwise be caused by the door being forcefully open or caught by a gust of wind.” He adds, “Equally, specifiers must consider whether a door closer requires delayed action. A delayed action closer offers a period of delay from when the door is opened to closed, which is usually set to be a maximum of 25 seconds (recommended for fire doors). This functionality makes delayed action closers ideal for environments that require easy passage, such as doors used by children, the elderly or wheelchair users, for example.”
The National Fire Protection Association (NFPA) has developed over 300 codes and standards to support the rapidly changing needs of the fire and life safety industry. NFPA 72, National Fire Alarm and Signaling Code®, is perhaps one of the most wide-ranging, designed to “meet society's changing fire detection, signaling, and emergency communications demands.” Development of building solutions Updated every three years, the 2025 edition of NFPA 72 took effect on September 18, 2024 Updated every three years, the 2025 edition of NFPA 72 took effect on September 18, 2024, and contains several key updates around technology, cybersecurity, and integration to support the continued development of connected building solutions. Staying ahead of these updates will ensure your building not only meets current needs but is able to adapt for future challenges. Cybersecurity and Remote Access While the 2022 edition of NFPA 72 introduced a variety of cybersecurity updates, it did not specify how they should be achieved. In the 2025 edition, Chapter 11 addresses this and outlines requirements to protect fire alarm and signaling systems from cyber-attacks across configuration, implementation, security, and access. This is particularly of interest when it comes to continued use of remote access processes across building systems, which allow a variety of maintenance to be done partially offsite, such as programming and resetting support. This includes the installation of patch updates, for example, much like those we have on our phones and laptops. Cybersecurity guidelines Reliability is of the utmost importance, meaning a technician needs to be on-site With life safety systems, however, you can’t simply push a button to start an update and move on. Reliability is of the utmost importance, meaning a technician needs to be on-site, while another installs patch updates remotely to ensure continuity of service and troubleshoot if needed. In an increasingly hybrid world, clear cybersecurity guidelines for remote access allow service providers to take advantage of such capabilities without fear of infiltration by threat actors. Advanced Technology Enhancements The incorporation of acoustic leak detection, thermal imaging, and a new notification mode in the 2025 edition of NFPA 72 offer both new applications for existing life safety technologies and advantages for increased accessibility. While acoustic leak detection is not a new technology, its use in the fire industry is a relatively recent application. These detectors identify the sound produced by a pressurized gas release or water leak in a pipe or its threads. In some cases, they can pinpoint the exact location of the leak. Integration with fire alarm systems Introduction of acoustic leak detection in NFPA 72 provides fire professionals with an understanding The introduction of acoustic leak detection in NFPA 72 provides fire professionals with an understanding of how to install, maintain, and test detectors, supporting integration with fire alarm systems for a more integrated life safety system across facilities. Thermal imaging, in a similar manner, can detect quickly developing fire threats by identifying changes in heat range. While traditional fire detection methods remain essential, thermal imaging enhances early threat detection and can identify risks, such as the self-combustion of lithium-ion batteries, which can occur in a matter of seconds, even before conventional sensors would trigger an alarm. New notification operation mode NFPA 72 also introduces a new notification operation mode, Restricted Audible Mode Operation (RAMO), which “recognizes the need for notification options in areas where loud sounds might be detrimental to typical occupants of the notification zones.” This can include spaces such as schools or healthcare facilities occupied by people with autism spectrum disorder, neurodiverse individuals, or others sensitive to stimuli like sound and light. With the approval of the authority having jurisdiction, facility managers can reduce the level of audio from fire alarm systems to better accommodate occupants, increase facility accessibility and experiences. Streamlined System Integration Architects and engineers can now plan for expansive areas without the constraints of challenges A significant update in the 2025 edition clarifies the allowance of smoke detectors on ceilings up to 40 feet high, impacting school design, hotel lobbies and other large spaces. While a seemingly minor change, this modification enhances design flexibility and fire alarm system effectiveness. Architects and engineers can now plan for expansive areas without the constraints of computer modeling or challenges posed by structural elements like beams or ventilation systems, ultimately improving safety and efficiency. Guidelines for auxiliary service providers The addition of guidelines for auxiliary service providers (ASPs) and communications technologies is another noteworthy integration update, ensuring that fire protection signals are processed effectively and aligning safety systems with evolving technology trends. Historically, fire alarm systems have not been able to directly contact fire departments to minimize the prevalence of false alarms; instead, supervising stations have served as the middle party to vet fire alarm activations from ASPs. In the last 10-15 years, this process has become largely electronic (via text or email) as opposed to picking up the phone, and continued technological advancements have created several new methods for service providers to send fire alarm system signals to supervising stations. Introduction of guidelines for ASPs Intro of policies for ASPs has given jurisdictions the flexibility to execute new technologies This shift is largely due to a trickle-down effect from the residential technology market, where smart technology and IoT devices have become the norm, influencing technological development in the commercial realm. While some municipalities may want to take advantage of new technologies to streamline the fire response process where possible, many fire departments are still relying on older technologies and may not have the resources available to implement major tech upgrades. The introduction of guidelines for ASPs has provided jurisdictions with the flexibility to implement new, progressive technologies where viable, while protecting the ability of others to maintain their current processes for fire alarm notifications and action by emergency response agencies. Looking Ahead As fire and life safety professionals navigate rapid technological developments, staying current with the latest NFPA codes and standards remains essential to ensuring safety and maintaining seamless service across the built environment. The 2025 edition of NFPA 72 introduces important updates that reflect the evolving capabilities of modern fire alarm and signaling systems. With these advancements, facility managers have a responsibility to familiarize themselves with the new requirements to ensure their systems are not only code-compliant, but also more secure, scalable and seamlessly connected to other building technologies. While the 2025 edition has only been in effect for a short time, the next revision cycle for 2028 is already on the horizon, making now the ideal moment for industry pioneers to evaluate the standard’s implementation and identify areas for continued improvement.
Editor's Dispatch
The Dingell Act, signed into law in 2019, has far-reaching implications, including effects on fire management and emergency services. Officially named the John D. Dingell, Jr. Conservation, Management, and Recreation Act, the law impacts fire professionals and their operations and fire prevention strategies. The Dingell Act is a comprehensive public lands bill that touches on various aspects of natural resource management, conservation, and recreation. Fire mitigation efforts One of the key provisions of the act deals with wildfire management, specifically addressing how federal agencies collaborate to prevent and respond to wildfires. The act streamlines fire mitigation efforts, enhances interagency cooperation, and encourages fire prevention measures on public lands. For fire professionals, this means better coordination among federal and local fire services, access to more resources, and improved strategies to combat wildfires. How the Dingell Act Changes Fire Management The act benefits both large fire departments and smaller teams working near public lands The Dingell Act mandates that federal agencies must coordinate with local fire services to develop effective wildfire management plans. This ensures that fire professionals have a direct line to federal resources, which can drastically improve response times. Additionally, the law increases funding for fire prevention initiatives, such as clearing vegetation in high-risk areas. Fire professionals working near national parks and other public lands will find these changes beneficial, as they create more opportunities for proactive fire control. The Dingell Act strengthens fire prevention protocols by prioritizing wildfire risk mitigation in areas under federal jurisdiction. The act benefits both large fire departments and smaller teams working near public lands. Fire professionals should recognize the broad scope of the Dingell Act and understand how it enhances safety measures in their regions. Federal and Local Collaboration Interagency collaboration is one of the key components of the Dingell Act. Fire departments in areas near public lands can now work more closely with federal agencies such as the U.S. Forest Service and the Bureau of Land Management. This collaboration is not limited to wildfire response but extends to training and resource-sharing, which can empower local teams to be better prepared for large-scale fires. By building stronger partnerships, fire professionals can develop more cohesive strategies for fire mitigation and management. The Dingell Act significantly increases the resources available to fire departments, especially in high-risk areas. Through grants and federal funding, fire professionals can access better equipment, training, and personnel to tackle fire hazards. This investment in fire prevention technology, including satellite-based fire detection systems and drones, ensures that teams have the tools they need to act quickly and effectively when fires threaten communities. Environmental Considerations Dingell Act highlights the extent of balancing fire suppression with environmental protection The Dingell Act highlights the importance of balancing fire suppression with environmental preservation. Fire professionals are encouraged to integrate eco-friendly practices into their operations, such as controlled burns that reduce vegetation buildup without damaging ecosystems. Understanding the environmental impact of fire prevention measures is essential for fire professionals who manage lands rich in biodiversity. By aligning fire prevention strategies with conservation goals, professionals can contribute to both safety and sustainability. Along with the increased collaboration between federal and local agencies come more training opportunities for fire professionals than ever before. The Dingell Act opens avenues for specialized training programs that focus on wildfire management and prevention. Firefighters can take advantage of workshops, courses, and simulation-based training to improve their skills in handling large-scale fires. This professional development is especially valuable for those looking to expand their capabilities in the face of growing wildfire risks. Future Considerations Looking ahead, fire professionals should be mindful of the evolving landscape of fire prevention. The Dingell Act represents just one piece of a broader legislative push to improve fire safety in the United States. Future regulations may build on this foundation, with more emphasis on climate change, land management, and fire technology. As professionals assess their current strategies, it is important to stay informed about upcoming changes and ensure that fire prevention efforts are aligned with national standards and policies. {##Poll1728377023 - What is the most critical resource for effective wildfire management?##}
The integration of technology into the fire service has significantly enhanced operations, but it has also introduced new vulnerabilities. Cybersecurity has become a concern for fire departments, possibly impacting their ability to respond effectively to emergencies and protect communities. Potential problems emanating from cybersecurity concerns include a disruption of a community’s emergency response system. False alarms could result from malicious computer hackers manipulating fire alarm systems, thus wasting resources, and causing potential danger for firefighters. Fire Risks From A Cyber-Attack Medical devices are connected to the IoT and are therefore vulnerable to attack Communication is another vulnerability: A cyber-attack on communication systems could hinder coordination among firefighters and with other emergency services. Potential cybersecurity targets related to the fire service include 911 systems, public safety radios, computer-aided dispatch systems, mobile data computers, and phone systems. In the EMS arena, electronic patient reporting and records management systems are at risk. Medical devices are connected to the Internet of Things (IoT) and are therefore vulnerable to attack. Many firefighter tools are operated by computers, so equipment malfunction is a real possibility. The digital world continues to infiltrate almost every aspect of firefighting. Critical equipment, such as fire trucks and rescue tools could be compromised, resulting in longer response times. Vulnerability to Ransomware Attacks Ransomware is a pernicious type of cyber-attack, involving the use of malicious software (malware) that encrypts files, rendering them inaccessible. The attackers then demand a ransom payment in exchange for the decryption key to restore the data. The city of Leeds, Ala., was hit by a ransomware attack in February 2018 that locked all city computers and data, including fire and police departments. A month later, Atlanta’s municipal systems were attacked, resulting in widespread outages, and disrupting city services. Impact on Data Loss and Privacy Fire units handle sensitive data, including the personal data of citizens and crisis responders In addition to operational concerns, there are also possible cybersecurity consequences relating to data loss and privacy. Fire departments handle sensitive data, including the personal information of citizens and emergency responders. A breach could lead to identity theft and reputational damage. On a more intangible level, a cyber-attack could erode public trust in the fire department's ability to protect the community. Negative publicity from a data breach can harm the fire department's image. Phishing schemes Among the cybersecurity threats are phishing schemes, which involve scammers attempting to obtain sensitive information from individuals, usually via email, by disguising themselves as trustworthy entities. Phishing can take the form of fake emails or websites that mimic legitimate businesses like banks, online retailers, or social media platforms. They lure victims by offering enticing deals, creating a sense of urgency, or claiming there's a problem with an account. Once the user clicks on a malicious link or provides personal information, the scammers can steal login credentials, credit card numbers, or other sensitive data. Top motivators of cyber-attacks Malicious files can be delivered as email attachments, which can contain viruses, ransomware, or other malware. Clicking a link in a suspicious email can redirect the user to a malicious website that can download malware or steal personal information. One of the top motivators of cyber-attacks is to collect personally identifiable information (PII) One of the top motivators of cyber-attacks is to collect personally identifiable information (PII), which is any data that can be used to identify an individual. This information includes name, address, phone number, social security or driver's license number, medical records, credit card or bank account numbers, and biometric data, such as fingerprints or facial images. The fire service handles a lot of PII, especially in emergency situations, including incident reports, property records, or patient information related to emergency medical services (EMS). Cyber-Criminals Have a Variety of Profiles Cyber-criminals come from a range of backgrounds and motivations. Individual hackers might be motivated by financial gain, ideology, or simply by the concept of a personal challenge. Organized crime groups might be motivated by profit, power, and/or influence. Other cyber-crime perpetrators include nation-state actors, who might be pursuing espionage, sabotage, or political influence. These threats have significant financial and technical capabilities. They include advanced persistent threats (APTs) from countries like China, Russia, and North Korea. Cyber threats posed by 'hacktivists' So-called 'hacktivists' can be motivated by political or social causes to launch distributed denial of service (DDoS) attacks, website defacement and/or data leaks. There is also the possibility of cyber-terrorists seeking to cause mass disruption or to achieve political or ideological goals. They are capable of large-scale attacks on critical infrastructure. Increased cyber-risks may lead to higher insurance premiums for fire departments There is a cost component of protecting against cybersecurity threats, a critical financial implication for cash-strapped fire departments. Implementing robust cybersecurity measures requires significant financial resources. At the other extreme, responding to a cyber-attack can be expensive, including legal fees, public relations, and system recovery. Increased cyber-risks may lead to higher insurance premiums for fire departments. Mitigation Strategies at a Glance Here are some mitigation strategies fire departments should consider: Risk assessment: Identify vulnerabilities and prioritize mitigation efforts. Employee training: Educate firefighters about cybersecurity best practices. Network security: Implement strong network security measures, including firewalls and intrusion detection systems. Data protection: Regularly back up data and encrypt sensitive information. Data minimization: Collect only the personal data that is necessary, and then limit access. Incident response plan: Develop a comprehensive plan for responding to cyber-attacks. Contingency: Create a backup plan to mitigate risk and minimize loss of critical assets in the event of an attack. Compliance: Ensure adherence with relevant privacy laws such as HIPAA and GDPR. Collaboration: Work with other agencies and cybersecurity experts to share information and best practices.
Thousands of industry professionals gathered at the 2024 NFPA Conference and Expo in Orlando in June. The event brought together educational sessions, networking opportunities, and an exhibitor showcase. NFPA is the National Fire Protection Association. The NFPA annual meeting allowed members and the public to discuss and vote on proposed changes to fire codes and standards. “It’s a gathering place for people in the industry,” says Dr. Rodger Reiswig, Vice President of Industry Relations at Johnson Controls. “You can walk around the floor and observe the trends, see what people are talking about, and view industry trends through a clear set of eyes.” New Foundation Series As vice president of industry relations, Reiswig acts as Johnson Controls’ liaison with the NFPA, works with NFPA technology committees, and serves on the Standards Council that oversees more than 300 NFPA codes and standards documents. Foundation Series is a complete family of fire alarm control units and peripheral devices At the NFPA Conference and Expo in Orlando, Johnson Controls provided “spotlight” seminars at their exhibit booth and highlighted products and services including interactive tools, inspections, remote services, restaurant systems, and the new Foundation Series Fire Safety Solution for the protection of small to mid-size buildings. The Foundation Series is a complete family of fire alarm control units and peripheral devices. NFPA’s codes and standards In addition, Reiswig attended seminars and Standards Council sessions. Technical sessions covered codes and standards that are currently “in cycle” (i.e., in the process of being updated). In a technical session on the last day of NFPA, anyone could attend to suggest changes and garner support from others on various changes. Consensus is a core principle of NFPA’s codes and standards. “This is a chance for everyone to participate, whether your interest is in roofing materials, how buildings are built, or life safety systems,” Reiswig adds. “Codes tell us when to do something, but standards tell us how to do it. If the occupancy standard says put in a fire alarm, the NFPA standard tells you how to do that.” Anyone at any level in any role or discipline can participate. new NFPA 915 Standard Fire alarm and life safety have yet lagged industry sectors when it comes to remote connectivity “Technology is changing rapidly, and the type of construction is different than 20 or 30 years ago. Use of new tools and materials in buildings is changing how much time I have to escape smoke or fire,” Reiswig says. “New construction materials allow fires to happen quickly, spread faster, and give off toxic chemicals. Tighter buildings ensure energy efficiency, but they allow less ventilation, so carbon monoxide can accumulate faster.” A common theme at the show was remote connectivity, highlighting the new NFPA 915 Standard for Remote Inspections, which guides new technologies to enable remote access and testing of life safety systems. Fire alarm and life safety have previously lagged other industry sectors when it comes to remote connectivity, but the new NFPA 915 standard opens new possibilities, and vendors at the show were promoting remote capabilities and inspections. develop safeguards and capabilities NFPA 915 Standard sets need for performing remote inspections safely and effectively The NFPA 915 Standard establishes requirements for performing remote inspections safely and effectively. It addresses various types of remote inspections. The standard also defines the responsibilities of various parties involved in a remote inspection, such as the inspector, property owner, and authority having jurisdiction (AHJ). The standard covers data collection procedures, data security, and data ownership. Overall, the standard helps to ensure that remote inspections can be conducted in a way that meets safety requirements. In effect, NFPA 915 gives the green light to manufacturers and Underwriters Laboratories (UL) to develop safeguards and capabilities to log into life safety systems remotely. The approach can help to simplify inspections, which can be performed remotely or with only one technician required on-site rather than two. Requirements include how systems communicate, the cybersecurity and credentials required, and the prevention of outside connections. Beyond fire alarms, the standard also allows other remote inspections, such as using a drone in a large warehouse to inspect sprinkler heads. Real-time information and instructions Inspectors are not allowed into buildings such as nursing homes and clinics to check their safety systems NFPA 915 was being considered before the COVID pandemic, but the business shutdowns and social distancing requirements during the worst of the pandemic increased awareness of the needs and benefits of remote inspections. During COVID, inspectors were not allowed into buildings such as nursing homes and hospitals to inspect their life safety systems. Remote access and inspections became critical, thus raising awareness of the feasibility of remote inspections that continue to drive their adoption. Another area of interest in NFPA was mass notification systems, which have matured a lot since they were introduced into the NFPA code in 2007. It’s easier than ever to provide real-time information and instructions to people in an area. Connectivity among fire alarm systems inside buildings, digital signage, and other life safety systems are promoting better notification. Area of refuge systems A new area of discussion and product development is “area of refuge” systems that complement Americans with Disabilities (ADA) requirements in buildings. In a high-rise building, for example, if the elevators are disabled, it may be impossible for a person using a wheelchair to evacuate. Instead, there are designated “areas of refuge,” which are rated to provide two hours of protection from fire. New notification systems can communicate with first responders about occupants in these areas. The NFPA conference increasingly incorporates a global presence, encouraging more collaboration among entities, countries, and associations about needs around the world. Manufacturers can work together through various associations including the Automatic Fire Alarm Association, Euralarm in Europe, and others. “Life safety is worldwide, and fires may be the same or different in various areas,” says Reiswig. “We need to remember that standards are not just for the United States because people are active from other countries.”
Case studies
Fire and Rescue NSW is deploying three water rescue strike teams and specialised equipment to support emergency efforts in the state’s north today as Cyclone Alfred approaches. The teams, made up of 14 highly-trained firefighters and a team leader, will be working in Lismore, Bellingen and Coffs Harbour where they will support the NSW State Emergency Service-led response to any potential flood emergency. Regional Rescue Teams Metropolitan-based firefighters will be supported by specially trained on-call and regional firefighters, with many of them living in, or close to, the towns they will be supporting. FRNSW will deploy new rescue boats that can be rolled up and packed to enable helicopter deployment to locations isolated by floodwater. The Strike Teams will be on standby to conduct flood rescues over the next few days, when it is expected there will be a heightened level of activity in line with weather forecasts. Emergency Response Upgrade FRNSW Acting Assistant Commissioner, Graham Kingsland, said the impacted communities should feel reassured by the presence of water rescue technicians. "When it comes to water rescues, these firefighters are among the most highly skilled and trained. They are equipped and ready to support locals at their time of need. "We've learned from past flood events and adapted our approach to make sure the best resources and support is available when it's most needed.” “The rescue boats, vehicles and wetsuits being utilised are all new, a result of FRNSW’s capability uplift and recommendations of the 2022 NSW Flood Inquiry. Importantly, this deployment is delivering on government recommendations and funding in a very practical sense.”
Comelit-PAC has worked with Centurion Fire & Security Ltd to install Logfire’s wireless solution at Guardian House, forming part of an initiative by the Inspired Neighborhoods to develop the listed building for community and economic regeneration. Guardian House, a listed building with a rich history as the former Bradford City Registry Office, had been unused and at risk of dilapidation. It is being refurbished to create modern offices and community space. Comelit-PAC’s LogiFire system Centurion recommended Comelit-PAC’s LogiFire system, with the wireless option seamlessly installed As part of the process of revitalizing the building, Centurion Fire & Security Ltd advised updating the fire detection and alarm system in place, reflecting on the inefficiencies and significant failings of the current alarm solution. Centurion recommended Comelit-PAC’s LogiFire system, with the wireless option seamlessly installed in the Graded area of the building to eliminate the need for extra cabling. Regeneration of Bradford's city center Says Assim Hussain, Chief Executive Officer of Inspired Neighborhoods: "We are committed to revitalizing the building, maximizing community benefit, and contributing to the economic regeneration of Bradford's city center. The redevelopment plan anticipates hosting a range of services that will attract up to 300 people to the city center daily.” “With such a responsibility to the community, we have to ensure their complete safety. Centurion Fire & Security Ltd supported us to deliver on total fire protection, recommending Comelit-PAC’s LogiFire wireless system to perfectly suit the building's intended needs while preserving its historical integrity.” Comelit-PAC's range of wireless devices Comelit-PAC introduced a new range of wireless devices, ideal for installations Building on the hugely successful LogiFire system, Comelit-PAC introduced a new range of wireless devices, ideal for installations where wired solutions may not be practical. Designed for ease of installation, the translators can expand a system efficiently, eliminating the need for costly and time-consuming cabling. Flexibility and reliability of the LogiFire system Nathan Douglas-Smith, Director of Centurion Fire & Security Ltd, adds: “The installation at Guardian House was a unique challenge due to its listed status and historical significance. Comelit-PAC’s LogiFire wireless system provided the perfect solution, allowing us to enhance fire safety without compromising the building's structure and aesthetics." "The flexibility and reliability of the LogiFire system ensures we can deliver total fire protection with ongoing remote reporting by the panel via the cloud.” Comelit-PAC’s wireless devices Comelit-PAC’s wireless devices come with addressable or conventional translators capable of cloud Comelit-PAC’s wireless devices come with addressable or conventional translators capable of cloud and remote monitoring. This feature eliminates the need for extensive cabling, significantly reducing installation time and overall project costs. The addressable translator sits directly on the loop with a built-in isolator, enhancing the system's protection by allowing for the indication of tamper faults, battery faults, device faults, contamination levels, and alarm reporting by the panel and remotely via the cloud. Demand for wireless fire detection systems Mandy Bowden, Comelit-PAC Fire Manager, concludes: “The demand for wireless fire detection systems is growing significantly, and our LogiFire solution is at the forefront of this innovation." "By offering a system that combines ease of installation with advanced monitoring capabilities, we can ensure listed buildings like Guardian House are protected. At the same time, we demonstrate how heritage and modern technology can work hand in hand to create safer communities.”
Fire and Rescue NSW crews responded to a fire involving a car carrier on the Hume Highway at Denham Court, in Sydney's south west. The prime mover, carrying several new hybrid vehicles, was successfully detached from the trailer; however, five of the vehicles were destroyed by fire. Lithium Battery Risk The hybrid vehicles containing lithium-ion batteries, added to the complexity to the operation. Lithium-ion batteries can ignite with significant force when exposed to fire. Crews removed the vehicles to a safe location, where the batteries will be monitored. The Hume Highway was closed northbound for approximately 40 minutes while crews worked to extinguish the fire and render the scene safe. Traffic has since resumed, with all lanes reopened and vehicles moving freely. Fire investigators have determined cause of the fire appears to be a mechanical fault in the trailer's wheels.
Hochiki Europe has brought the thrill of live football to the heart of the Gillingham community, awarding 35 coveted tickets to a Gillingham FC home game to the deserving Medway Soccer Academy. The academy, a grassroots initiative providing affordable football training to local children, emerged as the winners of Hochiki’s “Golden Ticket” competition. Essential equipment and kit Medway Soccer Academy addresses the financial barriers that prevent many children Founded in 2019 by Matt Waters, Medway Soccer Academy addresses the financial barriers that prevent many children from participating in organized football. Matt’s vision of a £4 “pay and play” model, run by nine dedicated volunteer coaches, ensures that football remains accessible to all. All funds are reinvested into the club, providing essential equipment and kit for its 64 regular attendees. Matt’s unwavering commitment The academy’s dedication to fostering a love for the game, promoting physical activity, and building confidence resonated deeply with Hochiki Europe. Kara Martin, Marketing Projects Specialist at Hochiki, who nominated the academy, highlighted Matt’s unwavering commitment to the community, noting that many children would otherwise miss out on the experience of a live football match. Academy’s training sessions The children were eager to learn about everything from the pre-game atmosphere to Coleman’s football idols Hochiki’s Marketing Manager, Craig Taylor, and Kara Martin, Marketing Project Specialist, visited one of the academy’s training sessions at a local community park, accompanied by Gillingham FC midfielder Ethan Coleman. Coleman spent over an hour engaging with the children and coaches, sharing insights into his professional journey and answering enthusiastic questions. The children were eager to learn about everything from the pre-game atmosphere to Coleman’s football idols and even his car. Affordable and engaging activities Kara Martin also spoke with parents, who emphasized the academy's vital role in providing affordable and engaging activities for local children. The “pay and play” flexibility was particularly valued by families who couldn’t commit to weekly team schedules, while the supportive environment helped build confidence in the children. The smiles and palpable joy on the children’s faces attested to the academy’s positive impact. Gillingham FC training experience The day culminated in an exciting penalty shootout, with successful participants entered into a raffle The day culminated in an exciting penalty shootout, with successful participants entered into a raffle for a Gillingham FC training experience at a later date. To cap off the memorable visit, Ethan Coleman presented Matt Waters with a golden envelope containing the 35 tickets for the Gillingham FC vs. Swindon Town match, which took place last week on April 26th. “We are incredibly grateful to Hochiki Europe for this amazing opportunity,” said Matt Waters. “This means the world to our children, many of whom have never experienced a live football game. It’s a testament to the hard work of our volunteer coaches and the dedication of our young players.” Benefit from the academy’s inclusive Looking ahead, Matt is striving to establish an U11s team for the 2025/26 season and is actively seeking sponsorship to cover the associated grassroots fees. This expansion would enable even more children to benefit from the academy’s inclusive and supportive environment. Hochiki Europe is proud to support Medway Soccer Academy and its commitment to providing accessible football opportunities for the local community. The company believes in the power of sport to inspire and unite and is thrilled to have played a role in creating lasting memories for these young football enthusiasts. Hochiki Europe is the Gillingham Football Club Rainham End Sponsor.
Oshkosh Airport Products, an Oshkosh Corporation business, announced the delivery of two Oshkosh Airport Products Striker® 6x6 ARFF vehicles to MET – Montreal Metropolitan Airport — formerly known as Montreal Saint-Hubert Airport. The new ARFF units will play a key role in supporting emergency operations as MET undergoes a significant transformation into a major domestic airport in Canada. MET’s new ARFF units were supplied through Oshkosh Airport Products’ Quebec-based dealer L’Arsenal. Fire protection solution “MET – Montreal Metropolitan Airport is entering an exciting new chapter, and we are proud to support their expansion with world-class ARFF vehicles,” said Alexandre Séguin, Sales Manager for L’Arsenal. “Our team has built a long-standing relationship with MET, working closely with them to identify and deliver the best fire protection solution for their evolving needs. The Striker 6x6 is engineered to deliver exceptional performance and safety, backed by our dedicated service and support.” Transition of MET The transition of MET from a small airport to a hub capable of handling more than 1 million passengers The transition of MET from a small regional airport to a hub capable of handling more than one million passengers annually, necessitated an upgrade to its fire protection services. The acquisition of these Striker 6x6 ARFF vehicles ensures compliance with airport regulations and provides state-of-the-art emergency response capabilities. Latest airport regulations “The decision to purchase Oshkosh ARFF vehicles was based on the brand’s strong reputation, strong service network, and the positive experiences of other airports in the region,” said Pierre-Luc Clement, Fleet Maintenance Manager at MET– Montreal Metropolitan Airport. “We needed a solution that offered reliability, safety features, and compliance with the latest airport regulations. The Striker 6x6 met all of our criteria and will be instrumental in ensuring the highest level of emergency response at our airport.” Striker 6x6 Features and Capabilities The two new Striker 6x6 ARFF vehicles are designed to handle the demands of MET’s growing operations. Notable features include: Industry-pioneering modular cab design for exceptional visibility TAK-4® all-wheel independent suspension for world-class off-road performance Seating capacity for four firefighters Scania DC16 V8 670HP Tier 4 engine for optimal power and efficiency Water capacity: 12,500 L Foam capacity: 1,600 L Dry chemical capacity: 227 kg Eco-EFP™ Foam Measurement System to enhance firefighting efficiency Electronic Foam Proportioning System to manage environmental impact MET prioritized foam testing systems With a mix of high-reach extendable turrets and bumper turrets, these vehicles are equipped to handle a range of emergency scenarios. Additionally, MET prioritized foam testing systems that minimize the environmental impact of training and maintenance, aligning with the airport’s broader sustainability goals. Sustainability initiatives The airport is committed to sustainability initiatives, including a GHG emissions reduction plan Slated to welcome its first passengers in 2025, MET is undergoing a significant transformation, with a 226,000 sq. ft. terminal, nine gates, and an anticipated capacity of four million travelers per year. The airport is committed to sustainability initiatives, including a GHG emissions reduction plan, Airport Carbon Accreditation, and new shuttle services to downtown Montreal. MET dedicated fire services unit As part of this expansion, MET established a dedicated fire services unit and invested in world-class emergency response equipment. The Striker 6x6 vehicles will provide essential fire protection for the airport’s evolving infrastructure and growing passenger base.
Fire protection solutions manufacturer, Advanced, has supplied an intelligent fire panel with wireless detection to iconic Scottish knitwear brand Eribé. An Advanced MxPro 5 analog addressable fire panel has been installed at Eribé Knitwear to provide industry-pioneering protection that is high-performance and fault-tolerant. The system was installed following a fire risk assessment, which required Category L2 coverage. Internal and external systems Founded in 1986, Eribé’s knitwear design house and manufacturing company is based in Melrose, in the Scottish Borders. The company prides itself in championing Made in Scotland and has a dedicated fan base worldwide. During 2024, the company took time to assess the whole business to strengthen its internal and external systems and processes for its staff and customers. As part of this process, Eribé reviewed its fire system to ensure full compliance and prioritize staff, premises, and customer safety by investing in Advanced fire protection. EMS Firecell wireless system MxPro 5 was retrofitted at Eribé; the Advanced panel was seamlessly integrated with an EMS Fire and security service providers, Safe Services, installed an Advanced MxPro 5 single-loop analog addressable fire panel to replace the existing fire system, as it was old and could not be brought up to standard. Since the MxPro 5 was being retrofitted at Eribé the Advanced panel was seamlessly integrated with an EMS Firecell wireless system, this simplified the installation since cabling was not required throughout the building. Advanced fire safety system “In 2024 we reviewed our business as a whole to strengthen our processes. The safety of our staff, premises, and customers was a priority and so we were fully behind investing in an Advanced fire safety system." "We are now really proud to say that with the help of Safe Services, our extended team, managers and directors feel far more knowledgeable regarding the risks and actions, and the whole team feels safer and more invested in it as a result,” said Tamsin Ansdell, Eribé Knitwear. Advanced panel with the wireless EMS Firecell Graeme Millar, Fire Technical Sales Engineer at Safe Services, said: “We were responsible for the installation, commissioning, verification and handover of the system at Eribé, and will also be conducting ongoing maintenance." "As we installed the Advanced panel with the wireless EMS Firecell it made it far more straightforward and meant less disruption for Eribé. We have several sites we have worked on with the same combination, and know the Advanced MxPro 5 works well with EMS equipment. The Advanced MxPro 5 is our panel of choice as it’s a trusted and reliable panel with our design and installation teams.” MxPro 5 panels Neil Parkin, Sales Manager at Advanced, said: “Choosing wireless equipment when installing a fire system is ideal for retrofitting, where cabling can be trickier to install and visually unappealing. Add to that the time and cost benefits they provide to installers, and it is a great choice in multiple scenarios both large and small." "Our MxPro 5 panels are designed to make life as easy as possible, delivering robust protection that offers real peace of mind, all backed up by our highly rated technical support.” FM Approvals to the EN 54 standard MxPro 5 is the fire industry’s pioneering multiprotocol fire panel and is certified by FM Approvals MxPro 5 is the fire industry’s pioneering multiprotocol fire panel and is certified by FM Approvals to the EN 54 standard. It offers customers a choice of four detector protocols and a completely open installer network, backed up by free training and support. MxPro 5 can be used in single-loop, single-panel format, or easily configured into high-speed networks of up to 200 panels covering huge areas. Ease of installation and configuration, as well as its wide range of peripheral options, make MxPro 5 customizable to almost any application. MxPro 5’s versatile wireless capabilities As well as compatibility with pioneering wired detector brands, MxPro 5’s versatile wireless capabilities make it easy to install robust fire alarm systems while saving crucial time, cost and disruption. Harnessing the power of proven technology, MxPro 5’s wireless solutions are scalable, adaptable, and reliable – for complete fire safety peace of mind. Battery replacement and fault reporting Wireless solutions not only mean lower visual and physical impact, but they are also faster Wireless solutions not only mean lower visual and physical impact, but they are also faster and cheaper to install, making them an increasingly popular alternative for sites where downtime is not an option, or re-wiring would prove disruptive. Thanks to two-way communication with the panel, battery replacement and fault reporting can also be worked into the on-going maintenance schedule via the panel service tools. MxPro 5’s stand-out false alarm management capabilities The MxPro 5’s stand-out false alarm management capabilities are available as standard. AlarmCalm delivers unprecedented control of verification and investigation delays. By dividing sites up into virtual false alarm ‘building areas’ independent of fire zones, much more precise control of false alarm management and reduction strategies can be achieved that exactly fit the needs of each part of a building. Development of intelligent fire systems Advanced products are specified in locations around the world, from single-panel installations An optional AlarmCalm button allows trained occupants to verify if they believe a local fire signal is a false alarm too – a highly effective way of eliminating unwanted alarms. As a world pioneer in the development and manufacture of intelligent fire systems, Advanced products are specified in locations around the world, from single-panel installations to large, multi-site networks. Advanced portfolio The Advanced portfolio includes complete fire detection systems, multiprotocol fire panels, extinguishing control, false alarm management and reduction systems. Advanced is owned by FTSE 100 company Halma PLC – a global group of life-saving technology companies with a clear purpose to grow a safer, cleaner, healthier future for everyone, every day.
Fire and Rescue NSW is deploying three water rescue strike teams and specialised equipment to support emergency efforts in the state’s north today as Cyclone Alfred approaches. The teams, made up of 14 highly-trained firefighters and a team leader, will be working in Lismore, Bellingen and Coffs Harbour where they will support the NSW State Emergency Service-led response to any potential flood emergency. Regional Rescue Teams Metropolitan-based firefighters will be supported by specially trained on-call and regional firefighters, with many of them living in, or close to, the towns they will be supporting. FRNSW will deploy new rescue boats that can be rolled up and packed to enable helicopter deployment to locations isolated by floodwater. The Strike Teams will be on standby to conduct flood rescues over the next few days, when it is expected there will be a heightened level of activity in line with weather forecasts. Emergency Response Upgrade FRNSW Acting Assistant Commissioner, Graham Kingsland, said the impacted communities should feel reassured by the presence of water rescue technicians. "When it comes to water rescues, these firefighters are among the most highly skilled and trained. They are equipped and ready to support locals at their time of need. "We've learned from past flood events and adapted our approach to make sure the best resources and support is available when it's most needed.” “The rescue boats, vehicles and wetsuits being utilised are all new, a result of FRNSW’s capability uplift and recommendations of the 2022 NSW Flood Inquiry. Importantly, this deployment is delivering on government recommendations and funding in a very practical sense.”
Comelit-PAC has worked with Centurion Fire & Security Ltd to install Logfire’s wireless solution at Guardian House, forming part of an initiative by the Inspired Neighborhoods to develop the listed building for community and economic regeneration. Guardian House, a listed building with a rich history as the former Bradford City Registry Office, had been unused and at risk of dilapidation. It is being refurbished to create modern offices and community space. Comelit-PAC’s LogiFire system Centurion recommended Comelit-PAC’s LogiFire system, with the wireless option seamlessly installed As part of the process of revitalizing the building, Centurion Fire & Security Ltd advised updating the fire detection and alarm system in place, reflecting on the inefficiencies and significant failings of the current alarm solution. Centurion recommended Comelit-PAC’s LogiFire system, with the wireless option seamlessly installed in the Graded area of the building to eliminate the need for extra cabling. Regeneration of Bradford's city center Says Assim Hussain, Chief Executive Officer of Inspired Neighborhoods: "We are committed to revitalizing the building, maximizing community benefit, and contributing to the economic regeneration of Bradford's city center. The redevelopment plan anticipates hosting a range of services that will attract up to 300 people to the city center daily.” “With such a responsibility to the community, we have to ensure their complete safety. Centurion Fire & Security Ltd supported us to deliver on total fire protection, recommending Comelit-PAC’s LogiFire wireless system to perfectly suit the building's intended needs while preserving its historical integrity.” Comelit-PAC's range of wireless devices Comelit-PAC introduced a new range of wireless devices, ideal for installations Building on the hugely successful LogiFire system, Comelit-PAC introduced a new range of wireless devices, ideal for installations where wired solutions may not be practical. Designed for ease of installation, the translators can expand a system efficiently, eliminating the need for costly and time-consuming cabling. Flexibility and reliability of the LogiFire system Nathan Douglas-Smith, Director of Centurion Fire & Security Ltd, adds: “The installation at Guardian House was a unique challenge due to its listed status and historical significance. Comelit-PAC’s LogiFire wireless system provided the perfect solution, allowing us to enhance fire safety without compromising the building's structure and aesthetics." "The flexibility and reliability of the LogiFire system ensures we can deliver total fire protection with ongoing remote reporting by the panel via the cloud.” Comelit-PAC’s wireless devices Comelit-PAC’s wireless devices come with addressable or conventional translators capable of cloud Comelit-PAC’s wireless devices come with addressable or conventional translators capable of cloud and remote monitoring. This feature eliminates the need for extensive cabling, significantly reducing installation time and overall project costs. The addressable translator sits directly on the loop with a built-in isolator, enhancing the system's protection by allowing for the indication of tamper faults, battery faults, device faults, contamination levels, and alarm reporting by the panel and remotely via the cloud. Demand for wireless fire detection systems Mandy Bowden, Comelit-PAC Fire Manager, concludes: “The demand for wireless fire detection systems is growing significantly, and our LogiFire solution is at the forefront of this innovation." "By offering a system that combines ease of installation with advanced monitoring capabilities, we can ensure listed buildings like Guardian House are protected. At the same time, we demonstrate how heritage and modern technology can work hand in hand to create safer communities.”
Fire and Rescue NSW crews responded to a fire involving a car carrier on the Hume Highway at Denham Court, in Sydney's south west. The prime mover, carrying several new hybrid vehicles, was successfully detached from the trailer; however, five of the vehicles were destroyed by fire. Lithium Battery Risk The hybrid vehicles containing lithium-ion batteries, added to the complexity to the operation. Lithium-ion batteries can ignite with significant force when exposed to fire. Crews removed the vehicles to a safe location, where the batteries will be monitored. The Hume Highway was closed northbound for approximately 40 minutes while crews worked to extinguish the fire and render the scene safe. Traffic has since resumed, with all lanes reopened and vehicles moving freely. Fire investigators have determined cause of the fire appears to be a mechanical fault in the trailer's wheels.
Hochiki Europe has brought the thrill of live football to the heart of the Gillingham community, awarding 35 coveted tickets to a Gillingham FC home game to the deserving Medway Soccer Academy. The academy, a grassroots initiative providing affordable football training to local children, emerged as the winners of Hochiki’s “Golden Ticket” competition. Essential equipment and kit Medway Soccer Academy addresses the financial barriers that prevent many children Founded in 2019 by Matt Waters, Medway Soccer Academy addresses the financial barriers that prevent many children from participating in organized football. Matt’s vision of a £4 “pay and play” model, run by nine dedicated volunteer coaches, ensures that football remains accessible to all. All funds are reinvested into the club, providing essential equipment and kit for its 64 regular attendees. Matt’s unwavering commitment The academy’s dedication to fostering a love for the game, promoting physical activity, and building confidence resonated deeply with Hochiki Europe. Kara Martin, Marketing Projects Specialist at Hochiki, who nominated the academy, highlighted Matt’s unwavering commitment to the community, noting that many children would otherwise miss out on the experience of a live football match. Academy’s training sessions The children were eager to learn about everything from the pre-game atmosphere to Coleman’s football idols Hochiki’s Marketing Manager, Craig Taylor, and Kara Martin, Marketing Project Specialist, visited one of the academy’s training sessions at a local community park, accompanied by Gillingham FC midfielder Ethan Coleman. Coleman spent over an hour engaging with the children and coaches, sharing insights into his professional journey and answering enthusiastic questions. The children were eager to learn about everything from the pre-game atmosphere to Coleman’s football idols and even his car. Affordable and engaging activities Kara Martin also spoke with parents, who emphasized the academy's vital role in providing affordable and engaging activities for local children. The “pay and play” flexibility was particularly valued by families who couldn’t commit to weekly team schedules, while the supportive environment helped build confidence in the children. The smiles and palpable joy on the children’s faces attested to the academy’s positive impact. Gillingham FC training experience The day culminated in an exciting penalty shootout, with successful participants entered into a raffle The day culminated in an exciting penalty shootout, with successful participants entered into a raffle for a Gillingham FC training experience at a later date. To cap off the memorable visit, Ethan Coleman presented Matt Waters with a golden envelope containing the 35 tickets for the Gillingham FC vs. Swindon Town match, which took place last week on April 26th. “We are incredibly grateful to Hochiki Europe for this amazing opportunity,” said Matt Waters. “This means the world to our children, many of whom have never experienced a live football game. It’s a testament to the hard work of our volunteer coaches and the dedication of our young players.” Benefit from the academy’s inclusive Looking ahead, Matt is striving to establish an U11s team for the 2025/26 season and is actively seeking sponsorship to cover the associated grassroots fees. This expansion would enable even more children to benefit from the academy’s inclusive and supportive environment. Hochiki Europe is proud to support Medway Soccer Academy and its commitment to providing accessible football opportunities for the local community. The company believes in the power of sport to inspire and unite and is thrilled to have played a role in creating lasting memories for these young football enthusiasts. Hochiki Europe is the Gillingham Football Club Rainham End Sponsor.
Oshkosh Airport Products, an Oshkosh Corporation business, announced the delivery of two Oshkosh Airport Products Striker® 6x6 ARFF vehicles to MET – Montreal Metropolitan Airport — formerly known as Montreal Saint-Hubert Airport. The new ARFF units will play a key role in supporting emergency operations as MET undergoes a significant transformation into a major domestic airport in Canada. MET’s new ARFF units were supplied through Oshkosh Airport Products’ Quebec-based dealer L’Arsenal. Fire protection solution “MET – Montreal Metropolitan Airport is entering an exciting new chapter, and we are proud to support their expansion with world-class ARFF vehicles,” said Alexandre Séguin, Sales Manager for L’Arsenal. “Our team has built a long-standing relationship with MET, working closely with them to identify and deliver the best fire protection solution for their evolving needs. The Striker 6x6 is engineered to deliver exceptional performance and safety, backed by our dedicated service and support.” Transition of MET The transition of MET from a small airport to a hub capable of handling more than 1 million passengers The transition of MET from a small regional airport to a hub capable of handling more than one million passengers annually, necessitated an upgrade to its fire protection services. The acquisition of these Striker 6x6 ARFF vehicles ensures compliance with airport regulations and provides state-of-the-art emergency response capabilities. Latest airport regulations “The decision to purchase Oshkosh ARFF vehicles was based on the brand’s strong reputation, strong service network, and the positive experiences of other airports in the region,” said Pierre-Luc Clement, Fleet Maintenance Manager at MET– Montreal Metropolitan Airport. “We needed a solution that offered reliability, safety features, and compliance with the latest airport regulations. The Striker 6x6 met all of our criteria and will be instrumental in ensuring the highest level of emergency response at our airport.” Striker 6x6 Features and Capabilities The two new Striker 6x6 ARFF vehicles are designed to handle the demands of MET’s growing operations. Notable features include: Industry-pioneering modular cab design for exceptional visibility TAK-4® all-wheel independent suspension for world-class off-road performance Seating capacity for four firefighters Scania DC16 V8 670HP Tier 4 engine for optimal power and efficiency Water capacity: 12,500 L Foam capacity: 1,600 L Dry chemical capacity: 227 kg Eco-EFP™ Foam Measurement System to enhance firefighting efficiency Electronic Foam Proportioning System to manage environmental impact MET prioritized foam testing systems With a mix of high-reach extendable turrets and bumper turrets, these vehicles are equipped to handle a range of emergency scenarios. Additionally, MET prioritized foam testing systems that minimize the environmental impact of training and maintenance, aligning with the airport’s broader sustainability goals. Sustainability initiatives The airport is committed to sustainability initiatives, including a GHG emissions reduction plan Slated to welcome its first passengers in 2025, MET is undergoing a significant transformation, with a 226,000 sq. ft. terminal, nine gates, and an anticipated capacity of four million travelers per year. The airport is committed to sustainability initiatives, including a GHG emissions reduction plan, Airport Carbon Accreditation, and new shuttle services to downtown Montreal. MET dedicated fire services unit As part of this expansion, MET established a dedicated fire services unit and invested in world-class emergency response equipment. The Striker 6x6 vehicles will provide essential fire protection for the airport’s evolving infrastructure and growing passenger base.
Fire protection solutions manufacturer, Advanced, has supplied an intelligent fire panel with wireless detection to iconic Scottish knitwear brand Eribé. An Advanced MxPro 5 analog addressable fire panel has been installed at Eribé Knitwear to provide industry-pioneering protection that is high-performance and fault-tolerant. The system was installed following a fire risk assessment, which required Category L2 coverage. Internal and external systems Founded in 1986, Eribé’s knitwear design house and manufacturing company is based in Melrose, in the Scottish Borders. The company prides itself in championing Made in Scotland and has a dedicated fan base worldwide. During 2024, the company took time to assess the whole business to strengthen its internal and external systems and processes for its staff and customers. As part of this process, Eribé reviewed its fire system to ensure full compliance and prioritize staff, premises, and customer safety by investing in Advanced fire protection. EMS Firecell wireless system MxPro 5 was retrofitted at Eribé; the Advanced panel was seamlessly integrated with an EMS Fire and security service providers, Safe Services, installed an Advanced MxPro 5 single-loop analog addressable fire panel to replace the existing fire system, as it was old and could not be brought up to standard. Since the MxPro 5 was being retrofitted at Eribé the Advanced panel was seamlessly integrated with an EMS Firecell wireless system, this simplified the installation since cabling was not required throughout the building. Advanced fire safety system “In 2024 we reviewed our business as a whole to strengthen our processes. The safety of our staff, premises, and customers was a priority and so we were fully behind investing in an Advanced fire safety system." "We are now really proud to say that with the help of Safe Services, our extended team, managers and directors feel far more knowledgeable regarding the risks and actions, and the whole team feels safer and more invested in it as a result,” said Tamsin Ansdell, Eribé Knitwear. Advanced panel with the wireless EMS Firecell Graeme Millar, Fire Technical Sales Engineer at Safe Services, said: “We were responsible for the installation, commissioning, verification and handover of the system at Eribé, and will also be conducting ongoing maintenance." "As we installed the Advanced panel with the wireless EMS Firecell it made it far more straightforward and meant less disruption for Eribé. We have several sites we have worked on with the same combination, and know the Advanced MxPro 5 works well with EMS equipment. The Advanced MxPro 5 is our panel of choice as it’s a trusted and reliable panel with our design and installation teams.” MxPro 5 panels Neil Parkin, Sales Manager at Advanced, said: “Choosing wireless equipment when installing a fire system is ideal for retrofitting, where cabling can be trickier to install and visually unappealing. Add to that the time and cost benefits they provide to installers, and it is a great choice in multiple scenarios both large and small." "Our MxPro 5 panels are designed to make life as easy as possible, delivering robust protection that offers real peace of mind, all backed up by our highly rated technical support.” FM Approvals to the EN 54 standard MxPro 5 is the fire industry’s pioneering multiprotocol fire panel and is certified by FM Approvals MxPro 5 is the fire industry’s pioneering multiprotocol fire panel and is certified by FM Approvals to the EN 54 standard. It offers customers a choice of four detector protocols and a completely open installer network, backed up by free training and support. MxPro 5 can be used in single-loop, single-panel format, or easily configured into high-speed networks of up to 200 panels covering huge areas. Ease of installation and configuration, as well as its wide range of peripheral options, make MxPro 5 customizable to almost any application. MxPro 5’s versatile wireless capabilities As well as compatibility with pioneering wired detector brands, MxPro 5’s versatile wireless capabilities make it easy to install robust fire alarm systems while saving crucial time, cost and disruption. Harnessing the power of proven technology, MxPro 5’s wireless solutions are scalable, adaptable, and reliable – for complete fire safety peace of mind. Battery replacement and fault reporting Wireless solutions not only mean lower visual and physical impact, but they are also faster Wireless solutions not only mean lower visual and physical impact, but they are also faster and cheaper to install, making them an increasingly popular alternative for sites where downtime is not an option, or re-wiring would prove disruptive. Thanks to two-way communication with the panel, battery replacement and fault reporting can also be worked into the on-going maintenance schedule via the panel service tools. MxPro 5’s stand-out false alarm management capabilities The MxPro 5’s stand-out false alarm management capabilities are available as standard. AlarmCalm delivers unprecedented control of verification and investigation delays. By dividing sites up into virtual false alarm ‘building areas’ independent of fire zones, much more precise control of false alarm management and reduction strategies can be achieved that exactly fit the needs of each part of a building. Development of intelligent fire systems Advanced products are specified in locations around the world, from single-panel installations An optional AlarmCalm button allows trained occupants to verify if they believe a local fire signal is a false alarm too – a highly effective way of eliminating unwanted alarms. As a world pioneer in the development and manufacture of intelligent fire systems, Advanced products are specified in locations around the world, from single-panel installations to large, multi-site networks. Advanced portfolio The Advanced portfolio includes complete fire detection systems, multiprotocol fire panels, extinguishing control, false alarm management and reduction systems. Advanced is owned by FTSE 100 company Halma PLC – a global group of life-saving technology companies with a clear purpose to grow a safer, cleaner, healthier future for everyone, every day.


Round table discussion
Fostering fire safety is a basic principle, but one that suggests many different approaches and technologies. Best practices and greater innovation can play a role to ensure various aspects of fire safety (and health), but the first step is awareness. We asked our Expert Panel Roundtable: What is a fire safety trend that isn't widely adopted but should be?
Thermal imaging is an advantageous tool for firefighters on the frontline. As thermal cameras have become more compact and affordable, their availability has expanded, along with their usefulness. We asked our Expert Panel Roundtable: How does thermal imaging serve the needs of firefighters and how is it changing?
The COVID-19 pandemic has had ramifications for almost every industry, some more than others. With the pandemic stretching well into a second year, the non-medical consequences continue, and many are wondering about which of the required changes might become permanent. As regards the fire sector, we asked our Expert Panel Roundtable: What impact has COVID-19 had on the fire industry?
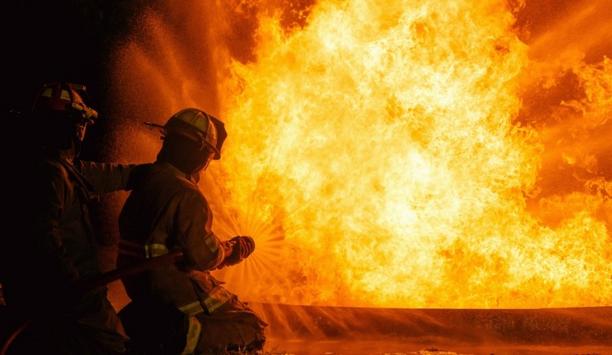
The New Future For Fire Agencies
Download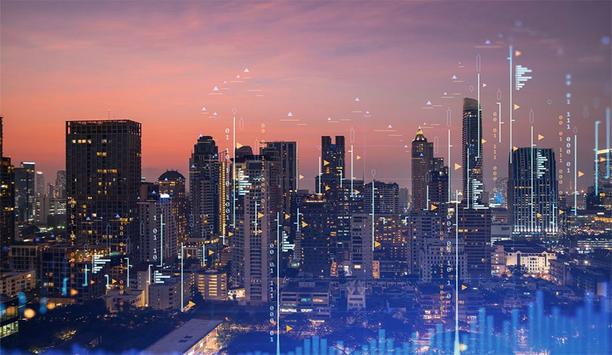
The Eight Key Trends in Fire Detection in 2023
Download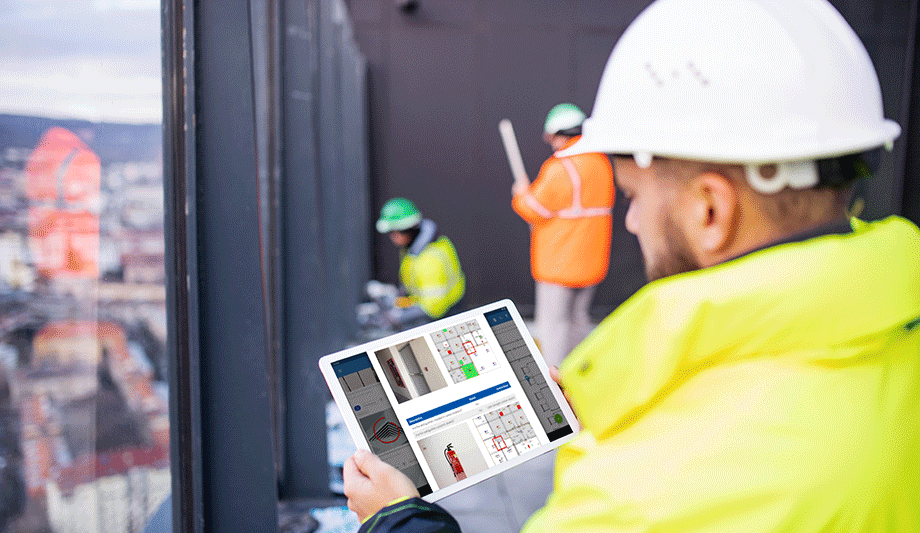
A Digital Platform to Improve Fire Safety Compliance and Inspections
Download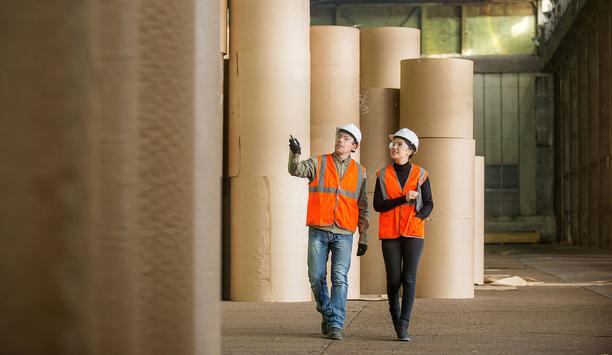
Overcoming the Challenges of Fire Safety in the Paper Industry
Download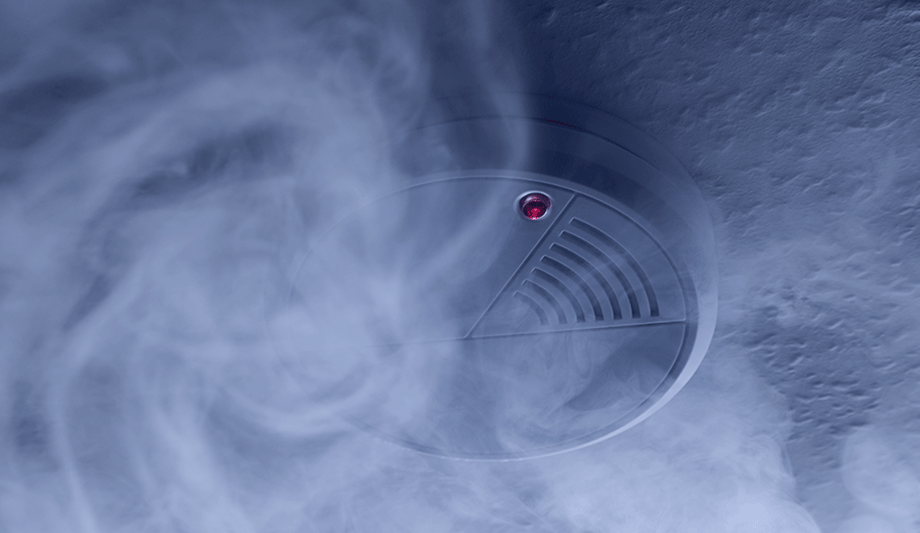
Carbon Monoxide: Creeping Killer Caught In The Act
Download