Globe FIRE DEPARTMENT SOFTWARE (1)
Browse FIRE DEPARTMENT SOFTWARE
Software products updated recently
Software - Expert Commentary
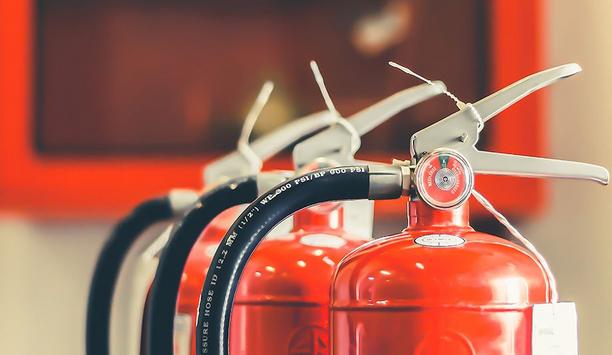
Nearly a decade has passed since the devastating Grenfell Fire, and still the UK construction industry finds itself grappling with the imperative of ensuring fire safety standards...
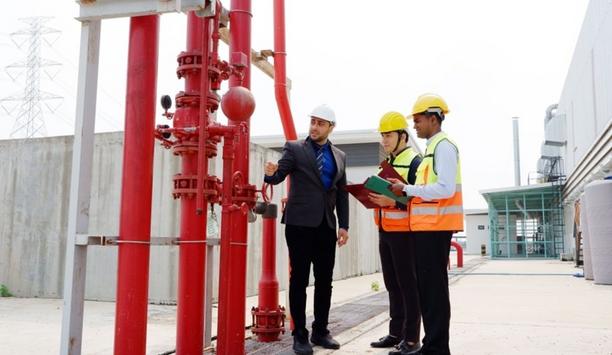
In the challenging world of fire safety and security services, organizations are constantly juggling the need to maintain high efficiency with the relentless push for technological...
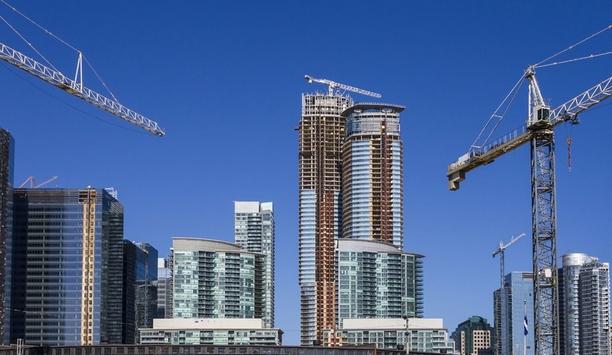
Using technology to provide the information required under the new Building Safety Act 2022, which has been enforceable since October 1st, can help relieve the pressure on sup...
Latest Globe Manufacturing Company, LLC news
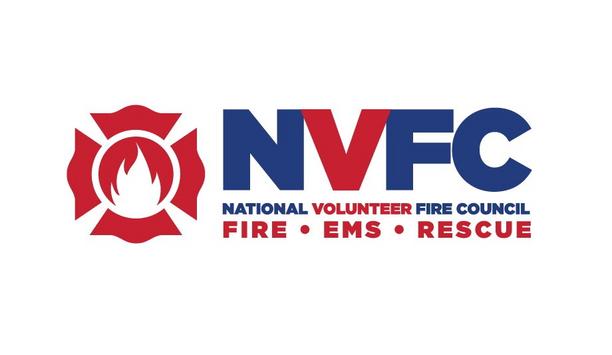
The final three recipients of MSA and DuPont’s 2023 Globe Gear Giveaway, conducted in partnership with the National Volunteer Fire Council (NVFC), have been selected. The Bel...
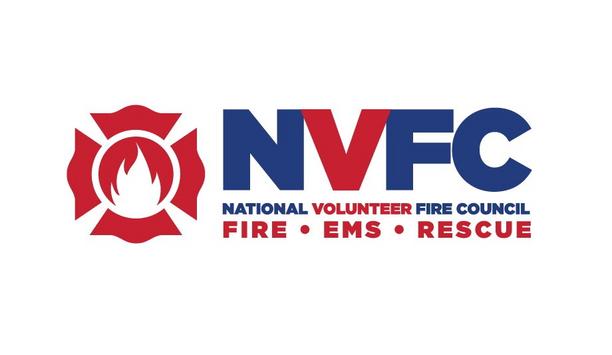
The ability, or lack thereof, to purchase adequate personal protective equipment is a well-known struggle for many volunteer fire departments across the U.S. To help combat...
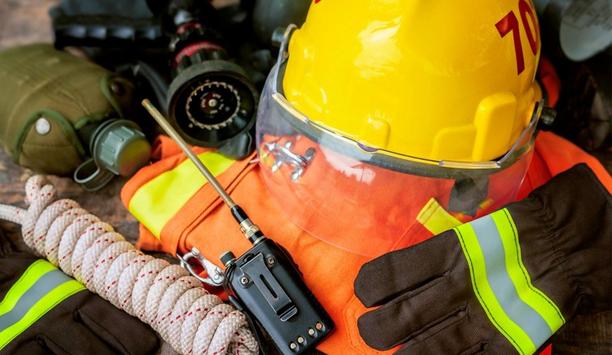
Trends in garments and protective gear for firefighters are evolving to address the changing needs of the fire service. Garments worn by firefighters must be comfortable and allow...
Trending topic articles
Fire and Rescue NSW (FRNSW) is further encouraging respectful and honest conversations and the sharing of Traditional Knowledge by opening a Yarning Circle at its training center at Orchard Hills, in...
Responding to reports regarding culture in the fire and rescue service, the National Fire Chiefs Council (NFCC) has reiterated that the behaviors outlined are wholly unacceptable, making it clear ther...
A South Yorkshire recruitment campaign aims to change perceptions of women in the fire service. South Yorkshire Fire & Rescue’s ‘A Firefighter Is A Firefighter’ campaign include...
The Fire Standards Board (FSB) is delighted to announce the launch of two new Fire Standards - Fire Control and Communications & Engagement. The development of the Fire Control Standard was drive...
Gavin Skelly, CEO of growing fire safety industry body - Fire Aware, spoke of the moral and behavioral changes in culture needed to improve standards at the Scotland Housing Leaders’ Summit. He...
Using the highest-rated fire performance cables will help firefighters in the event of a fire in some of the largest new buildings being developed, says pioneering cable supplier AEI Cables. AEI Cabl...
Rescue Intellitech, a pioneering provider of innovative cleaning solutions for the fire and rescue industry, is set to unveil its latest innovation in firefighter PPE care, with the launch of a new li...
Secutech Vietnam 2025 came to a close on 16 August at the Saigon Exhibition and Convention Centre (SECC), after bringing together key stakeholders and buyers from across Vietnam’s security...
WAGNER Group GmbH has once again been awarded for its research and development work. In a decision dated August 11, 2025, the Research Allowance Certification Authority (BSFZ) confirmed the eligibili...
Orr Protection, a provider of mission-critical fire protection solutions, has acquired all of the business assets of Compass Fire Protection, LLC, based in the Seattle, Washington area. The acquisit...
Hochiki Europe, a global pioneer in life safety solutions, has partnered with VOLT EHF, a specialist in electrical and fire alarm systems, to install a comprehensive and scalable fire detection system...
Whether it’s the end of the day or end of term, when schools close, it’s not unusual to see children and staff alike scrambling out the doors as they head for a much needed period of relax...
Sensor solutions provider HENSOLDT will present its latest technological advancements at DSEI 2025 in London from 9 to 12 September 2025. One of HENSOLDT's core competencies is the active and passive...
New Government data of fire and rescue service incidents analyzed by HETAS for Chimney Fire Safety Week (CFSW), reveals that Devon and Somerset Fire and Rescue Service responded to 181 chimney fires o...
Fire and Rescue NSW (FRNSW) investigators are now at the scene of a house fire, which has claimed the lives of two people in Sydney's south-west. Neighbors phoned Triple-Zero (000) around 6:45 am as...
Fire and Rescue NSW (FRNSW) is further encouraging respectful and honest conversations and the sharing of Traditional Knowledge by opening a Yarning Circle at its training center at Orchard Hills, in...
Responding to reports regarding culture in the fire and rescue service, the National Fire Chiefs Council (NFCC) has reiterated that the behaviors outlined are wholly unacceptable, making it clear ther...
A South Yorkshire recruitment campaign aims to change perceptions of women in the fire service. South Yorkshire Fire & Rescue’s ‘A Firefighter Is A Firefighter’ campaign include...
The Fire Standards Board (FSB) is delighted to announce the launch of two new Fire Standards - Fire Control and Communications & Engagement. The development of the Fire Control Standard was drive...
Gavin Skelly, CEO of growing fire safety industry body - Fire Aware, spoke of the moral and behavioral changes in culture needed to improve standards at the Scotland Housing Leaders’ Summit. He...
Using the highest-rated fire performance cables will help firefighters in the event of a fire in some of the largest new buildings being developed, says pioneering cable supplier AEI Cables. AEI Cabl...
Rescue Intellitech, a pioneering provider of innovative cleaning solutions for the fire and rescue industry, is set to unveil its latest innovation in firefighter PPE care, with the launch of a new li...
Secutech Vietnam 2025 came to a close on 16 August at the Saigon Exhibition and Convention Centre (SECC), after bringing together key stakeholders and buyers from across Vietnam’s security...
WAGNER Group GmbH has once again been awarded for its research and development work. In a decision dated August 11, 2025, the Research Allowance Certification Authority (BSFZ) confirmed the eligibili...
Orr Protection, a provider of mission-critical fire protection solutions, has acquired all of the business assets of Compass Fire Protection, LLC, based in the Seattle, Washington area. The acquisit...
Hochiki Europe, a global pioneer in life safety solutions, has partnered with VOLT EHF, a specialist in electrical and fire alarm systems, to install a comprehensive and scalable fire detection system...
Whether it’s the end of the day or end of term, when schools close, it’s not unusual to see children and staff alike scrambling out the doors as they head for a much needed period of relax...
Sensor solutions provider HENSOLDT will present its latest technological advancements at DSEI 2025 in London from 9 to 12 September 2025. One of HENSOLDT's core competencies is the active and passive...
New Government data of fire and rescue service incidents analyzed by HETAS for Chimney Fire Safety Week (CFSW), reveals that Devon and Somerset Fire and Rescue Service responded to 181 chimney fires o...
Fire and Rescue NSW (FRNSW) investigators are now at the scene of a house fire, which has claimed the lives of two people in Sydney's south-west. Neighbors phoned Triple-Zero (000) around 6:45 am as...
Fire and Rescue NSW (FRNSW) is further encouraging respectful and honest conversations and the sharing of Traditional Knowledge by opening a Yarning Circle at its training center at Orchard Hills, in...
The New Future For Fire Agencies
DownloadThe Eight Key Trends in Fire Detection in 2023
DownloadA Digital Platform to Improve Fire Safety Compliance and Inspections
DownloadOvercoming the Challenges of Fire Safety in the Paper Industry
DownloadCarbon Monoxide: Creeping Killer Caught In The Act
Download