LUKAS FIRE HOSE REELS (5)
Browse FIRE HOSE REELS
Hose Reel products updated recently
Hose Reels - Expert Commentary
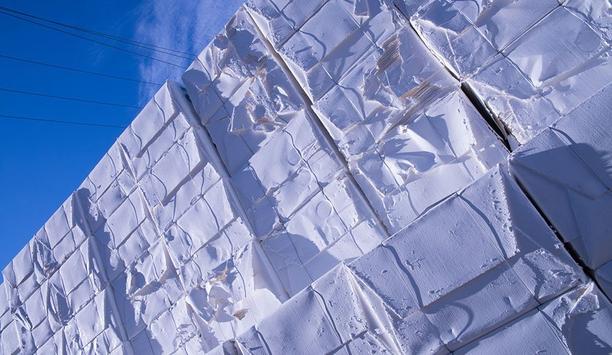
There is a sense in some markets that the paper and pulp industry will decline owing to the digital technologies with which people interact every day. While this might be considere...
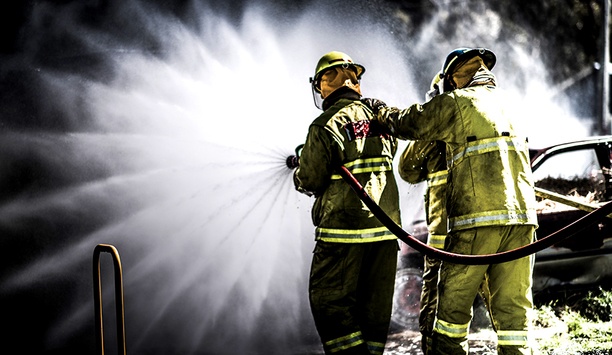
Want to know an easy way to judge the quality of a fire department? Look at how much they train. Career, volunteer or combination, fire departments become successful through traini...
Latest LUKAS Hydraulik GmbH news
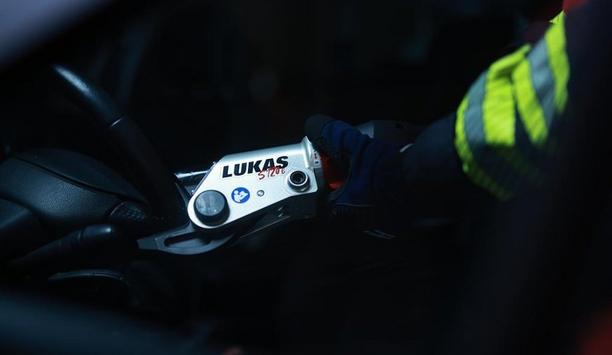
Lukas Hydraulics is proud to announce the launch of the S120e Power Cut, a compact extrication tool, which enables firefighters to quickly and precisely navigate tight spaces - pro...

Continuing its transition from component supplier to provider of integrated solutions, focused on solving complex problems, IDEX Fire & Safety is tapping into its vast cadre of...
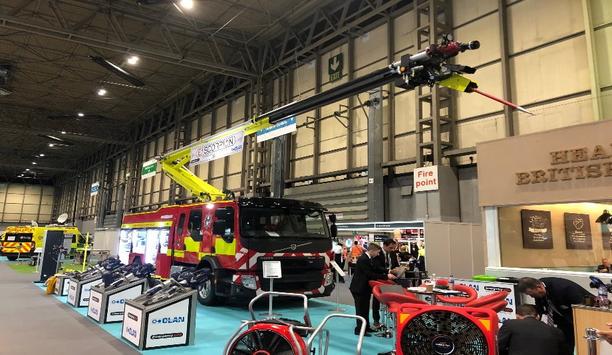
This February saw the launch of Emergency One (UK) Limited’s (E1) flagship new appliance, the E1 Scorpion™ The event, hosted by E1 and sister company, Clan Tools and P...
Trending topic articles
Pierce Manufacturing Inc., an Oshkosh Corporation business, is proud to announce the continued momentum of the 2025 Pierce Road Rally as it nears its midpoint, visiting locations across the United Sta...
Andy Spence, Joint Managing Director of Britannia Fire, the pioneering manufacturer of fire extinguishers in the UK, has addressed the Environmental Audit Committee in the House of Commons. He highli...
FeuerTrutz will be setting new standards on 25 and 26 June 2025 at the Exhibition Centre Nuremberg, not only with its exhibition floor space, but also with the diversity of the supporting program. Ar...
Fire and Rescue NSW (FRNSW) is reminding travellers heading to and from the snowfields this winter to exercise patience and safety on the icy roads. The FRNSW crews of permanent firefighters, seconde...
Teledyne Gas & Flame Detection (Teledyne GFD) is unveiling its PS DUO, a portable dual-gas detector set to enhance personal safety in gas monitoring applications. This innovative handheld device...
Fire and Rescue NSW (FRNSW) crews have door-knocked more than 60 homes at Macquarie Fields, in Sydney’s south-west, in the wake of a devastating house fire in the neighbourhood. On 28 May, 10 p...
A lithium-ion battery from an e-bike has caused a fire in a unit at Lethbridge Park in Sydney's west earlier today. Crews were called to the second-floor unit in Hawaii Avenue just before 3.00 am aft...
D-Tools, a major provider of business management software for electronics systems contractors, and FireCAD, powered by Inspect Point, a cloud-based fire alarm CAD solution, are pleased to announce a s...
Ballyclare, a major designer and manufacturer of firefighter personal protective equipment (PPE), announces a raft of strategic appointments as it focuses on further expansion in the UK market. The f...
Perimeter Solutions, a renowned global manufacturer of high-quality fire retardant and firefighting foam concentrates, marked the grand opening of its new PHOS-CHEK facility at McClellan Park in Sacra...
The Engineered Solutions division of Dräger, an international pioneer in the fields of medical and safety technology, has designed a breathing air panel for Staffordshire Fire and Rescue to prote...
INTERSCHUTZ 2026, taking place from 1 to 6 June in Hanover, will be shaped by what many are calling a “turning point”. With eleven months to go before the event starts, strong exhibitor i...
FeuerTrutz 2025 has once again proven itself as the central platform for preventive fire protection. With new formats, a strong congress program and intensive expert discussions, the trade fair p...
Oshkosh Airport Products, an Oshkosh Corporation business, is proud to announce the delivery of three advanced Striker Aircraft Rescue and Fire Fighting (ARFF) vehicles to the Metropolitan Washington...
An upgrade to the Johnson Controls flagship building automation system (BAS), Metasys 14.1 offers a suite of new and enhanced features that answers the need for more comprehensive energy management....
Pierce Manufacturing Inc., an Oshkosh Corporation business, is proud to announce the continued momentum of the 2025 Pierce Road Rally as it nears its midpoint, visiting locations across the United Sta...
Andy Spence, Joint Managing Director of Britannia Fire, the pioneering manufacturer of fire extinguishers in the UK, has addressed the Environmental Audit Committee in the House of Commons. He highli...
FeuerTrutz will be setting new standards on 25 and 26 June 2025 at the Exhibition Centre Nuremberg, not only with its exhibition floor space, but also with the diversity of the supporting program. Ar...
Fire and Rescue NSW (FRNSW) is reminding travellers heading to and from the snowfields this winter to exercise patience and safety on the icy roads. The FRNSW crews of permanent firefighters, seconde...
Teledyne Gas & Flame Detection (Teledyne GFD) is unveiling its PS DUO, a portable dual-gas detector set to enhance personal safety in gas monitoring applications. This innovative handheld device...
Fire and Rescue NSW (FRNSW) crews have door-knocked more than 60 homes at Macquarie Fields, in Sydney’s south-west, in the wake of a devastating house fire in the neighbourhood. On 28 May, 10 p...
A lithium-ion battery from an e-bike has caused a fire in a unit at Lethbridge Park in Sydney's west earlier today. Crews were called to the second-floor unit in Hawaii Avenue just before 3.00 am aft...
D-Tools, a major provider of business management software for electronics systems contractors, and FireCAD, powered by Inspect Point, a cloud-based fire alarm CAD solution, are pleased to announce a s...
Ballyclare, a major designer and manufacturer of firefighter personal protective equipment (PPE), announces a raft of strategic appointments as it focuses on further expansion in the UK market. The f...
Perimeter Solutions, a renowned global manufacturer of high-quality fire retardant and firefighting foam concentrates, marked the grand opening of its new PHOS-CHEK facility at McClellan Park in Sacra...
The Engineered Solutions division of Dräger, an international pioneer in the fields of medical and safety technology, has designed a breathing air panel for Staffordshire Fire and Rescue to prote...
INTERSCHUTZ 2026, taking place from 1 to 6 June in Hanover, will be shaped by what many are calling a “turning point”. With eleven months to go before the event starts, strong exhibitor i...
FeuerTrutz 2025 has once again proven itself as the central platform for preventive fire protection. With new formats, a strong congress program and intensive expert discussions, the trade fair p...
Oshkosh Airport Products, an Oshkosh Corporation business, is proud to announce the delivery of three advanced Striker Aircraft Rescue and Fire Fighting (ARFF) vehicles to the Metropolitan Washington...
An upgrade to the Johnson Controls flagship building automation system (BAS), Metasys 14.1 offers a suite of new and enhanced features that answers the need for more comprehensive energy management....
Pierce Manufacturing Inc., an Oshkosh Corporation business, is proud to announce the continued momentum of the 2025 Pierce Road Rally as it nears its midpoint, visiting locations across the United Sta...
The New Future For Fire Agencies
DownloadThe Eight Key Trends in Fire Detection in 2023
DownloadA Digital Platform to Improve Fire Safety Compliance and Inspections
DownloadOvercoming the Challenges of Fire Safety in the Paper Industry
DownloadCarbon Monoxide: Creeping Killer Caught In The Act
Download