Hochiki Europe Firefighting Mounting Brackets (1)
Browse Firefighting Mounting Brackets
- Material
- Plastic
- Poly
- Nylon
- Cast Aluminum
- Stainless Steel
- Mount Type
- Horizontal
- Vertical
- Restraints
- Web
- Rubber
- Bungee
- Mechanical
- Make
- Hochiki Europe
- Other Hochiki Europe products
- Hochiki Europe Detectors
- Hochiki Europe Warning Lights & Sirens
Mounting Bracket products updated recently
Latest Hochiki Europe (UK) Ltd news

Hochiki Europe has brought the thrill of live football to the heart of the Gillingham community, awarding 35 coveted tickets to a Gillingham FC home game to the deserving Medway So...

Hochiki Europe, a manufacturer of innovative life safety solutions, is partnering with Jendee Trading, a global provider with nearly 50 years of experience exporting British electr...
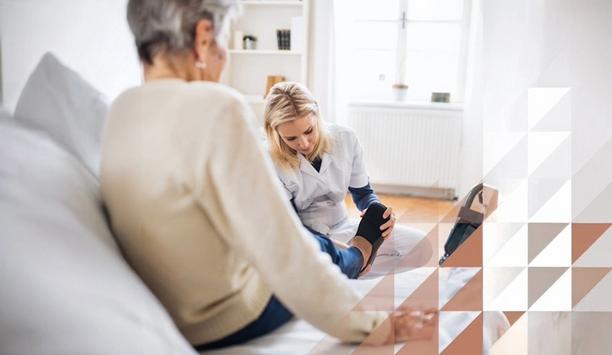
Merriman Grange, a beautiful new care home from Cinnamon Care Collection, located in Worthing, West Sussex, is designed to provide a warm, comfortable, and thanks to Hochiki's ESP...
Trending topic articles
In September 2024, the UK government announced an extension for the recognition of CE marking on construction products in Great Britain. The sudden change was described as part of a wider strategy t...
Fire and Rescue NSW (FRNSW) has isolated the last of the gas cylinders which ignited at an industrial facility at Port Kembla, in the state's Illawarra. Eight cylinders of highly flammable and potent...
Residents in the Newcastle suburb of Wickham are advised to keep their doors and windows closed as Fire and Rescue NSW (FRNSW) crews battle a large fire in an auto-electrical business. The blaze brok...
A Fire and Rescue NSW (FRNSW) fleet mechanic has described how she rushed to the aid of a heavily pregnant woman, trapped by a car fire in Sydney’s Eastern Distributor. Belinda Jackson, a civil...
Honeywell has been selected by Phoenix Sky Harbor International Airport (PHX) to complete a comprehensive fire alarm system upgrade at its Terminal 4, which houses more than 80 airline gates spanning...
Globally renowned provider of testing, inspection, and certification services, SOCOTEC UK and Ireland has announced the acquisition of United Kingdom Testing and Certification (UKTC), a renowned indep...
A Fire and Rescue NSW (FRNSW) crew has teamed up with NSW Health to conduct an emergency exercise in the Southern Tablelands. The Southern NSW Local Health District (SNSWLHD) recently invited the cre...
More than 400 current and former service personnel who work for Fire and Rescue NSW (FRNSW) now have access to an enhanced support network as RSL NSW re-establishes a standalone sub-branch for the sta...
Pierce Manufacturing Inc., an Oshkosh Corporation business, is pleased to announce Cary Fire Department in North Carolina has introduced into service a Pierce Volterra electric pumper, which is the fi...
Honeywell has acquired from Nexceris its Li-ion Tamer business, a major off-gas detection solution for lithium-ion (Li-ion) batteries that detects thermal runaway events. The acquisition enhances Hon...
Milwaukee® continues its commitment to relentless innovation with the M18™ Backpack Fluid Pump Gen 2, M18™ SWITCH TANK™ 15L Chemical Spray Tank, and M18™ SWITCH TANK™...
The 17th Real Estate Development (RED) Summit – Saudi Arabia | Europe Edition, hosted by GBB Venture, turned the spotlight on Lisbon as it welcomed some of the most influential names from Saudi...
Dräger, an international pioneer in the fields of medical and safety technology, has launched the new FPS-COM Voice mask-integrated unit to improve voice firefighter communication when using brea...
AdvanTec Marine is pleased to announce a major milestone: both its Canadian manufacturing facility in British Columbia and its Oregon, USA facility are now certified to produce fire-rated marine doors...
Oshkosh Airport Products, an Oshkosh Corporation business, is proud to announce the delivery of three state-of-the-art Striker® Aircraft Rescue and Fire Fighting (ARFF) vehicles to Bradley Interna...
In September 2024, the UK government announced an extension for the recognition of CE marking on construction products in Great Britain. The sudden change was described as part of a wider strategy t...
Fire and Rescue NSW (FRNSW) has isolated the last of the gas cylinders which ignited at an industrial facility at Port Kembla, in the state's Illawarra. Eight cylinders of highly flammable and potent...
Residents in the Newcastle suburb of Wickham are advised to keep their doors and windows closed as Fire and Rescue NSW (FRNSW) crews battle a large fire in an auto-electrical business. The blaze brok...
A Fire and Rescue NSW (FRNSW) fleet mechanic has described how she rushed to the aid of a heavily pregnant woman, trapped by a car fire in Sydney’s Eastern Distributor. Belinda Jackson, a civil...
Honeywell has been selected by Phoenix Sky Harbor International Airport (PHX) to complete a comprehensive fire alarm system upgrade at its Terminal 4, which houses more than 80 airline gates spanning...
Globally renowned provider of testing, inspection, and certification services, SOCOTEC UK and Ireland has announced the acquisition of United Kingdom Testing and Certification (UKTC), a renowned indep...
A Fire and Rescue NSW (FRNSW) crew has teamed up with NSW Health to conduct an emergency exercise in the Southern Tablelands. The Southern NSW Local Health District (SNSWLHD) recently invited the cre...
More than 400 current and former service personnel who work for Fire and Rescue NSW (FRNSW) now have access to an enhanced support network as RSL NSW re-establishes a standalone sub-branch for the sta...
Pierce Manufacturing Inc., an Oshkosh Corporation business, is pleased to announce Cary Fire Department in North Carolina has introduced into service a Pierce Volterra electric pumper, which is the fi...
Honeywell has acquired from Nexceris its Li-ion Tamer business, a major off-gas detection solution for lithium-ion (Li-ion) batteries that detects thermal runaway events. The acquisition enhances Hon...
Milwaukee® continues its commitment to relentless innovation with the M18™ Backpack Fluid Pump Gen 2, M18™ SWITCH TANK™ 15L Chemical Spray Tank, and M18™ SWITCH TANK™...
The 17th Real Estate Development (RED) Summit – Saudi Arabia | Europe Edition, hosted by GBB Venture, turned the spotlight on Lisbon as it welcomed some of the most influential names from Saudi...
Dräger, an international pioneer in the fields of medical and safety technology, has launched the new FPS-COM Voice mask-integrated unit to improve voice firefighter communication when using brea...
AdvanTec Marine is pleased to announce a major milestone: both its Canadian manufacturing facility in British Columbia and its Oregon, USA facility are now certified to produce fire-rated marine doors...
Oshkosh Airport Products, an Oshkosh Corporation business, is proud to announce the delivery of three state-of-the-art Striker® Aircraft Rescue and Fire Fighting (ARFF) vehicles to Bradley Interna...
In September 2024, the UK government announced an extension for the recognition of CE marking on construction products in Great Britain. The sudden change was described as part of a wider strategy t...
The New Future For Fire Agencies
DownloadThe Eight Key Trends in Fire Detection in 2023
DownloadA Digital Platform to Improve Fire Safety Compliance and Inspections
DownloadOvercoming the Challenges of Fire Safety in the Paper Industry
DownloadCarbon Monoxide: Creeping Killer Caught In The Act
Download