POK FIRE MONITORS (2)
Browse FIRE MONITORS
Monitor products updated recently
Monitors - Expert Commentary
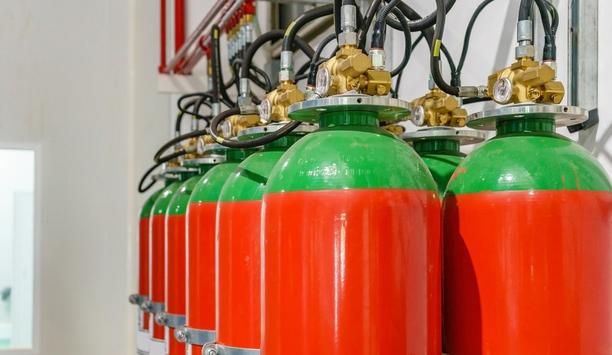
Technological advances in recent decades have considerably improved fire alert systems. Fire sprinkler systems are now installed at a rate of 40 million units per year and now, 96%...
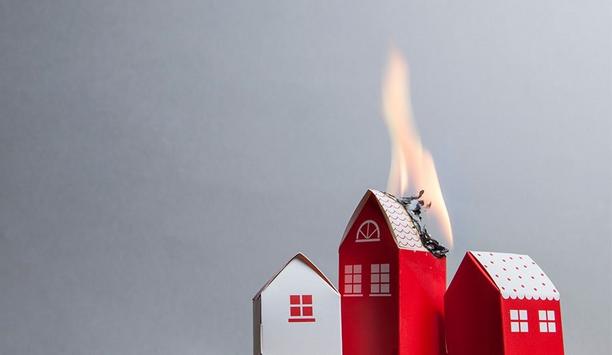
As organizations start to plan for next year’s operating budget, it’s a good time to take a closer look at fire prevention, what’s its costing and the value it de...
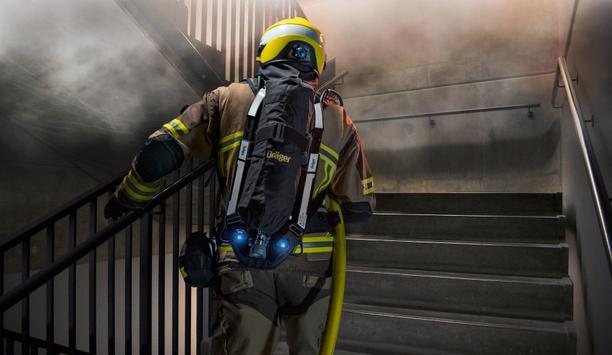
The product lifecycle of self-contained breathing apparatus (SCBA) is approximately ten years, during which time technology inevitably advances considerably in terms of digitizatio...
Latest POK S.A.S news
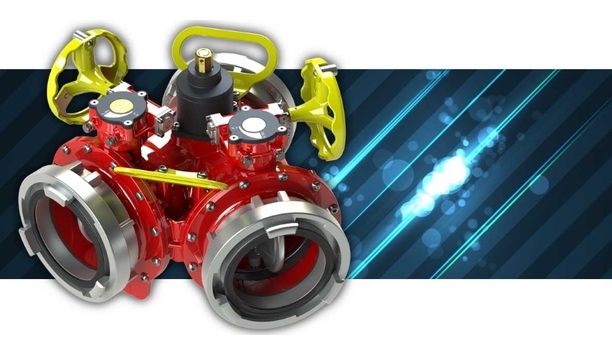
With a pump outlet, the divider is used to supply several pressurized water lines. The most commonly used dividers have 2 or 3 outlets and are equipped with quick couplings at the...
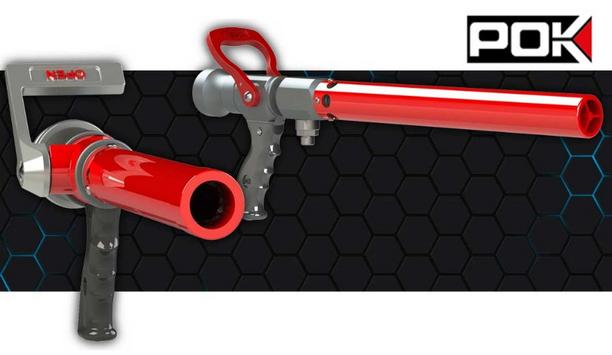
Optimized according to the percentage of the aspirated product, the eductor’s viscosity, and the duration of the operation, there are several techniques for proportionally mi...
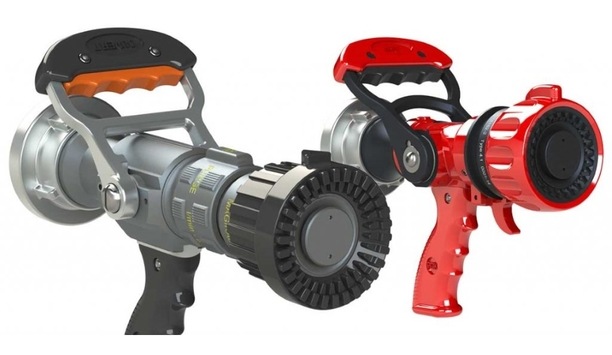
To meet the ever-increasing demand from firefighters for automatic nozzles, POK® has carried out in-depth work in partnership with professionals to create a nozzle perfectly ad...
Trending topic articles
Dräger, an international pioneer in the fields of medical and safety technology, has launched the new FPS-COM Voice mask-integrated unit to improve voice firefighter communication when using brea...
AdvanTec Marine is pleased to announce a major milestone: both its Canadian manufacturing facility in British Columbia and its Oregon, USA facility are now certified to produce fire-rated marine doors...
Oshkosh Airport Products, an Oshkosh Corporation business, is proud to announce the delivery of three state-of-the-art Striker® Aircraft Rescue and Fire Fighting (ARFF) vehicles to Bradley Interna...
In September 2024, the UK government announced an extension for the recognition of CE marking on construction products in Great Britain. The sudden change was described as part of a wider strategy t...
Fire and Rescue NSW (FRNSW) has isolated the last of the gas cylinders which ignited at an industrial facility at Port Kembla, in the state's Illawarra. Eight cylinders of highly flammable and potent...
Residents in the Newcastle suburb of Wickham are advised to keep their doors and windows closed as Fire and Rescue NSW (FRNSW) crews battle a large fire in an auto-electrical business. The blaze brok...
A Fire and Rescue NSW (FRNSW) fleet mechanic has described how she rushed to the aid of a heavily pregnant woman, trapped by a car fire in Sydney’s Eastern Distributor. Belinda Jackson, a civil...
Honeywell has been selected by Phoenix Sky Harbor International Airport (PHX) to complete a comprehensive fire alarm system upgrade at its Terminal 4, which houses more than 80 airline gates spanning...
Henkel Adhesive Technologies India is excited to share the launch of its new automotive warehouse in Chakan, strategically located in one of India’s key automotive hubs. This built-to-suit...
The acquisition of Australian company Aerial Fire Control strengthens Vallfirest’s global position in aerial firefighting and accelerates the development of next-generation wildfire suppressio...
Hochiki Europe is proud to announce the successful installation of its ESP Addressable fire detection system as part of the ambitious conversion of the former Scott Harbor office building in Cardiff B...
Pierce Manufacturing Inc., an Oshkosh Corporation business, is pleased to announce Cary Fire Department in North Carolina has introduced into service a Pierce Volterra electric pumper, which is the fi...
Honeywell has acquired from Nexceris its Li-ion Tamer business, a major off-gas detection solution for lithium-ion (Li-ion) batteries that detects thermal runaway events. The acquisition enhances Hon...
Milwaukee® continues its commitment to relentless innovation with the M18™ Backpack Fluid Pump Gen 2, M18™ SWITCH TANK™ 15L Chemical Spray Tank, and M18™ SWITCH TANK™...
The 17th Real Estate Development (RED) Summit – Saudi Arabia | Europe Edition, hosted by GBB Venture, turned the spotlight on Lisbon as it welcomed some of the most influential names from Saudi...
Dräger, an international pioneer in the fields of medical and safety technology, has launched the new FPS-COM Voice mask-integrated unit to improve voice firefighter communication when using brea...
AdvanTec Marine is pleased to announce a major milestone: both its Canadian manufacturing facility in British Columbia and its Oregon, USA facility are now certified to produce fire-rated marine doors...
Oshkosh Airport Products, an Oshkosh Corporation business, is proud to announce the delivery of three state-of-the-art Striker® Aircraft Rescue and Fire Fighting (ARFF) vehicles to Bradley Interna...
In September 2024, the UK government announced an extension for the recognition of CE marking on construction products in Great Britain. The sudden change was described as part of a wider strategy t...
Fire and Rescue NSW (FRNSW) has isolated the last of the gas cylinders which ignited at an industrial facility at Port Kembla, in the state's Illawarra. Eight cylinders of highly flammable and potent...
Residents in the Newcastle suburb of Wickham are advised to keep their doors and windows closed as Fire and Rescue NSW (FRNSW) crews battle a large fire in an auto-electrical business. The blaze brok...
A Fire and Rescue NSW (FRNSW) fleet mechanic has described how she rushed to the aid of a heavily pregnant woman, trapped by a car fire in Sydney’s Eastern Distributor. Belinda Jackson, a civil...
Honeywell has been selected by Phoenix Sky Harbor International Airport (PHX) to complete a comprehensive fire alarm system upgrade at its Terminal 4, which houses more than 80 airline gates spanning...
Henkel Adhesive Technologies India is excited to share the launch of its new automotive warehouse in Chakan, strategically located in one of India’s key automotive hubs. This built-to-suit...
The acquisition of Australian company Aerial Fire Control strengthens Vallfirest’s global position in aerial firefighting and accelerates the development of next-generation wildfire suppressio...
Hochiki Europe is proud to announce the successful installation of its ESP Addressable fire detection system as part of the ambitious conversion of the former Scott Harbor office building in Cardiff B...
Pierce Manufacturing Inc., an Oshkosh Corporation business, is pleased to announce Cary Fire Department in North Carolina has introduced into service a Pierce Volterra electric pumper, which is the fi...
Honeywell has acquired from Nexceris its Li-ion Tamer business, a major off-gas detection solution for lithium-ion (Li-ion) batteries that detects thermal runaway events. The acquisition enhances Hon...
Milwaukee® continues its commitment to relentless innovation with the M18™ Backpack Fluid Pump Gen 2, M18™ SWITCH TANK™ 15L Chemical Spray Tank, and M18™ SWITCH TANK™...
The 17th Real Estate Development (RED) Summit – Saudi Arabia | Europe Edition, hosted by GBB Venture, turned the spotlight on Lisbon as it welcomed some of the most influential names from Saudi...
Dräger, an international pioneer in the fields of medical and safety technology, has launched the new FPS-COM Voice mask-integrated unit to improve voice firefighter communication when using brea...
The New Future For Fire Agencies
DownloadThe Eight Key Trends in Fire Detection in 2023
DownloadA Digital Platform to Improve Fire Safety Compliance and Inspections
DownloadOvercoming the Challenges of Fire Safety in the Paper Industry
DownloadCarbon Monoxide: Creeping Killer Caught In The Act
Download